Current trends in MWF microbicides
Dr. Frederick J. Passman | TLT Cover Story May 2010
Despite half a century of industrial usage, many unanswered questions remain about the future of these critically important chemicals.
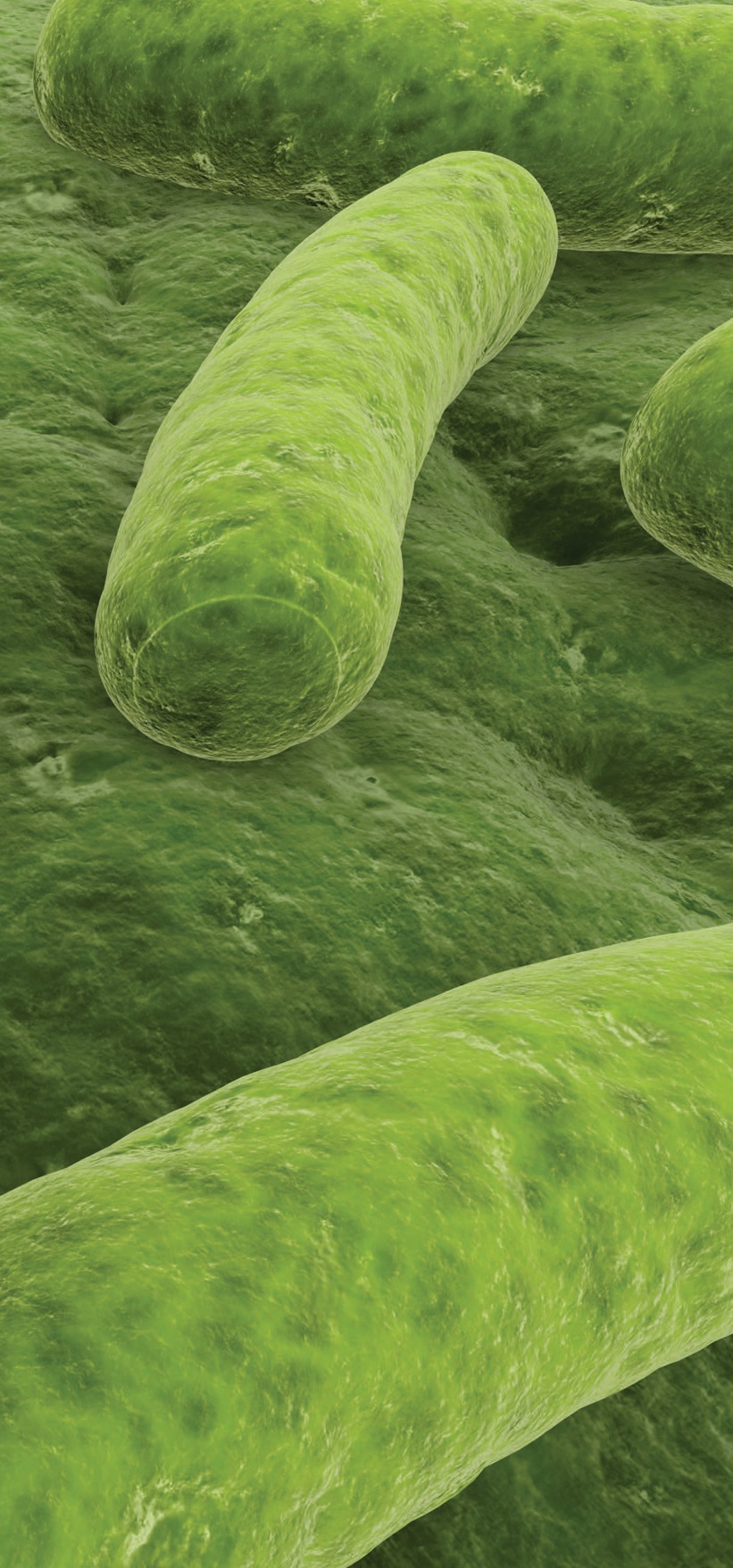
www.canstockphoto.com
KEY CONCEPTS
•
Petroleum companies began researching pathogenic microorganisms in water-miscible MWFs in the 1940s and ’50s.
•
The Clean Water Act was one of two watershed events that transformed the MWF microbicide market in the early 1980s.
•
Although the number of available MWF microbicide products will remain stable or increase slightly over the next several years, the total number of active ingredients will shrink.
Metalworking fluid microbicides (also known as biocides or, in regulatory parlance, antimicrobial pesticides) are chemical substances used to protect MWFs from biodeterioration. As explained in ASTM E-2169 (
1), microbicides can be used to control microbial contamination in fluid-blending systems (tanks, etc.), as preservatives during in-drum storage or as performance chemicals in application. Although the use of organic antimicrobials dates back to the invention of para-chloro-meta-xylenol (PCMX) in 1889, routine use of microbicides began in earnest in the mid-20th Century.
Three trends drove this mid-century growth. First, the use of water-miscible fluids (any MWF in which the concentrated product is diluted in water, either by emulsification, dissolution or a combination of both) increased dramatically during the pre-World War II period, as both the automotive and aviation industries began to blossom. Growth in numbers of manufacturing plants was coupled with the trend toward the construction of large central cooling systems. Greater volumes, production rates and sophistication of fluid formulations provided an impetus to protect those formulations against biodeterioration.
In the 1940s and 1950s, several petroleum companies sponsored studies on the presence of potentially pathogenic microorganisms in water-miscible MWFs. Not surprisingly, opportunistic pathogens were recovered from the most-used MWFs (E.O. Bennett frequently observed that the taxonomic profile of the microbial community in a given MWF reflected the profile of the community in the make-up water used to dilute the MWF concentrate). Despite these trends, microbicides were used sparingly, even begrudgingly, until the late 1970s to early 1980s. They were generally perceived to be non-value added chemicals, used only when foul odors and slime accumulation couldn’t be controlled by other means.
Two watershed events transformed the MWF microbicide market. In the early 1980s, provisions of the 1977 Clean Water Act (
2) began to impact the cost of MWF facility waste management. As plant discharges came under national, state and local regulations derived from the National Pollutant Discharge Elimination System, the cost per gallon of waste treatment approximated and in some localities exceeded that of the original MWF concentrate. This created a strong impetus for increasing fluid performance life.
During the same period, a number of MWF compounders introduced the concept of fluid management. In the pre-fluid management era, typical MWF system draining intervals ranged from two to four months. Companies promoting fluid management programs promised to extend fluid life substantially. Depending on fluid turnover rates, contaminant removal systems, condition monitoring and tankside additions, some systems could operate for years between full draining and system clean out. The effective use of MWF microbicides played a significant role in fluid life extension. Additionally, the period 1965 to 1985 marked the introduction of most of the approximately 80 active ingredients currently approved by the U.S. EPA for use in MWF (
1).
In the United States, microbicide use has been regulated since 1910. Initially, use was regulated under the 1910 Federal Insecticide Act. The 1947 Federal Insecticide, Fungicide and Rodenticide Act (FIFRA) made the process of registering and use reporting more stringent. Since 1947, FIFRA has been revised on a number of occasions. Until the EPA was created in 1970, the U.S. Department of Agriculture had responsibility for managing the registration and use of all pesticides. The EPA’s Office of Pesticide Programs has administered pesticide regulations ever since. Periodic data recalls have had a substantial effect on both the variety of active ingredients and number of microbicide manufacturers in the MWF industry. For example, after the 1986 data recall, approximately half of the active ingredients with MWF end-use sites (a “site” is a permitted use) disappeared from the list, the number of companies with primary registrations for hexahydro-1,3,5-tris(2-hydroxyethyl)-s-triazine (HTHT; CAS No. 4719-04-04) shrank from 16 to four. These are registrations as manufacturers, as opposed to supplemental registrations, which include authorization for companies to repackage and sell the product under their private label.
When faced with a data recall, manufacturers can choose to discontinue production of the product, develop the data as required by EPA or negotiate with EPA to define precisely what EPA needs in order to appropriately satisfy the agency’s risk-assessment requirements. Historically, data recalls have tended to reduce the number of active ingredients approved for use as MWF microbicides and the number of companies manufacturing products for sale into the MWF market. This trend has reflected each manufacturer’s return on investment assessment.
European Union implementation of the Biocidal Products Directive (BPD (
3)) and REACH (
4) have further complicated the regulatory atmosphere for MWF microbicides. The BPD precedes REACH by nearly a decade. It is similar to the U.S. EPA’s FIFRA-based regulations. As with the FIFRA registration process, a battery of environmental fate and persistence, and toxicological tests must be submitted as part of the registration application package. The types of toxicological tests depend on a product’s toxicity and the anticipated exposure risks.
One of the major implications of REACH is that it might require essentially the same environmental persistence and toxicological data as currently required under the BDP for all chemicals sold into or manufactured within the EU. The cost of developing a full environmental fate and persistence; toxicology data set can exceed $2 million U.S. The details regarding the types of toxicological tests to be required under REACH remain in flux; however, from the perspective of the microbicides market, it would level the playing field between registered microbicides and unregistered products whose primary function is MWF preservation.
TODAY’S MWF MICROBICIDES
As noted above, approximately 80 active ingredients are currently approved by EPA for use in MWF (
1). However in practice fewer than a dozen active ingredients account for more than 90% of the total volume of MWF microbicide use.
First introduced in 1924, HTHT remains the most widely used MWF microbicide in the U.S. Seven manufacturers—four of whom are active in the MWF market—hold primary FIFRA registrations. HTHT remains a high-volume product because of its low cost and versatility. It is a water-stable bactericide that can be formulated stably into emulsifiable-oil, semisynthetic and synthetic MWF and can be used as a tankside treatment.
Although it is still used widely, HTHT has several vulnerabilities. It is a member of the formaldehyde-condensate, formaldehyde-release microbicides. It is manufactured by reacting of formaldehyde and methyl ethanolamine. It kills microbes by hydrolyzing to release the formaldehyde, which then reacts with cell proteins. Since the mid-1980s it has been well-known that many common MWF microbes can become resistant to formaldehyde. This translates into reduced HTHT efficacy.
In the early to mid-1990s, and again over the past couple of years, concerns over formaldehyde toxicity have raised the threat of a total ban on the use of formaldehyde-release microbicides in MWF. My comparison of the toxicological profiles of various MWF microbicides (
5) and Howard Cohen’s investigation of formaldehyde in the MWF environment (
6) seemed to have cooled the 1990s hysteria. However, a decade later, the issue has returned.
Figure 1. Three samples from a series of 15; 20 weeks after having been diluted to end-strength (5% v/v). Sample 1 was prepared using tap water, but contained no microbicide. Sample 10 was treated with a microbicide and was filtered periodically. Sample 9 was similar to sample 10 except that it was diluted with high-quality (reverse osmosis) water and its pH was maintained at 9.2. Among the 15 samples only those that contained microbicide retained appearances similar to those of samples 9 and 10. The other 12 samples appeared similar to sample 1 at the end of 20 weeks. (Courtesy of STLE member John Burke)
In response to concerns about the potential cancer risk associated with incidental exposure to formaldehyde released from formaldehyde-condensate microbicides used in MWF, the EPA’s Office of Pesticide Programs is considering imposing a requirement for full carcinogenicity studies for formaldehyde-condensate microbicides. Carcinogenicity studies are lifetime (typically two-year) experiments run on laboratory animals. Post-mortem, the test animals are autopsied to determine the range of effects of exposure to the test substance. These studies can cost more than $2 million.
A pending U.S. EPA registration review for HTHT is likely to require HTHT manufacturers to submit new data for the complete battery of acute, sub-chronic and chronic toxicity tests (estimated cost $4 million). Moreover, EPA is considering lowering the maximum permissible HTHT dosage to 500 ppm; well below the effective dose. These two measures could effectively remove HTHT and other formaldehyde-condensate microbicides from the U.S. MWF market. Several trade organizations are working hard to convince EPA that the existing toxicological data do not support such draconian measures.
Oxizolidines, hydantoins and other formaldehyde-condensate microbicides in addition to HTHT would be affected by this EPA action. It’s likely that the variety of antimicrobial products would shrink if carcinogenicity studies were required.
Speculation that the acid fact bacterium
Mycobacterium immunogenum is the primary agent responsible for the respiratory disease, hypersensitivity pneumonitis (HP), led several major automotive manufacturers to ban or severely limit the use of HTHT in MWF formulations. For reasons explained in my 2008 paper (
7), an untested hypothesis that
M. immunogenum only grew when the so-called
normal population (microbes that formed visible colonies on nutrient media within two-to-three days) was suppressed gained wide acceptance for a period. Since HTHT did a good job of controlling the normal population, there were industry stakeholders who concluded that general microbial control was somehow a bad thing.
It is now generally recognized that
M. immunogenum is one of approximately a dozen microbes that are commonly recovered from MWF and known to cause HP. Also, it has been demonstrated that the prevalence of M. immunogenum is unrelated to the prevalence of other microbes in MWF. Moreover, it has been shown that aldehyde-based microbicides (formaldehyde-release and glutaraldehyde) denature endotoxin, but other antimicrobial chemistries do not. However, the ban on in-formulation use of HTHT persists at some metalworking facilities. This is not an endorsement of HTHT. It’s simply a polemic against letting hysteria guide technical decisions. When considering the risk associated with the use of certain substances, it’s equally important to consider the risks associated with not using those substances.
The second major class of MWF microbicide chemicals in current use is the isothiazolines. The first isothaizolin-3-one to gain acceptance as a MWF microbicide was Rohm & Haas’ (now part of the Dow Chemical Co.) Blend of 5-chloro-2-methyl-4-isothazolin-3-one (CIT; CAS 26172-55-4) plus 2-methyl-3(2H)-isothiazolin-3-one (MIT; CAS: 2682-20-4). The CIT/MIT combination is an effective bactericide at less than 20 ppm active ingredient. However, it hydrolyzes quickly in the presence of primary amines. Consequently, historically CIT/MIT has been used only as a tankside treatment. There are now stabilized formulations of CIT/MIT that can be used in-formulation. Initially, there were a number of patents protecting both the CIT/MIT chemistry and its applications. As these patents have expired, new manufacturers have entered the market. Although CIT/MIT is the best known isothiazoline, a family of isothiazolines has been developed over the past 20 years.
Although products based on 1,2-benzisothizoline-3-one (CAS 2634-33-5) arrived on the scene nearly a decade before the CIT/MIT blend, their use in MWF was negligible until the mid-1990s. Unlike CIT/MIT, BIT is stable in MWF formulations, but 500 to 700 ppm active ingredient is needed in order to achieve effective antimicrobial activity. Moreover, in contrast to either HTHT or CIT/MIT, BIT performance is MWF formulation dependent. Several isothiazolines are used primarily as fungicides (for example: 2-n-octyl-4-isothiazonline-3-one (CAS 26530-20-1) and n-butyl-1,2-benzisothazolin-3-one (CAS 4299-07-4)).
The isothiazoline fungicides are niche products compared to the two primary chemistries used to control fungal contamination in MWF. For years, sodium-2-pyridinethiol-1-oxide (NPT; CAS 3811-73-2) was essentially the only MWF fungicide in general use (there were a few niche products, but none represented a significant market share).
In the late 1980s, a 20% active dispersion of 2-iodo-2-propynylbutyl carbamate (IPBC; CAS 55406-50-6) was approved for use in MWF. The two actives still dominate the emulsifiable-oil and semisynthetic sectors, but NPT remains the dominant product used to protect synthetic MWF from fungal contamination.
In addition to PCMX, two other phenolic products have been used in MWF: sodium para-chloro-meta-cresolate (PCMC; CAS 15733-22-9) and ortho-phenylphenol (OPP; CAS 90-43-7). The popularity of the phenolics has waxed and waned over the years. When chlorinated phenols in water discharges became regulated, all phenolics fell out of favor. Only a few MWF compounders continued to formulate with phenols through the 1980s and 1990s.
However, in the late-1990s, phenolics were regentrified. Their lipophylic properties made them excellent candidates for penetrating the high-lipid content cell-membranes of mycobacteria. Moreover, PCMC has recently received an H-1 certification (approval for incidental food contact) by NSF, so that it can be used legally to protect food-grade lubricants against microbial contamination.
STATE OF PLAY
Over the past 10 to 15 years there has been considerable consolidation among microbicide manufacturers. Arch Chemicals, BASF, Dow Chemical and Troy Chemical have each expanded their biocidal product lines through acquisitions. Given the cost of bringing a microbicide to market, it’s likely that further consolidation will occur. The two other major MWF microbicide suppliers are Buckman Laboratories and LANXESS.
The expansion of product lines reflects a trend toward customer focus. Historically, U.S. microbicide manufacturers only marketed products for which they were the primary producers. Today there is greater emphasis on offering a variety of actives and on developing blends of active ingredients or improved active ingredient delivery systems (for example, using low-volatile organic compound solvents and improving the solubility/dispensability of the active ingredient in different types of MWF).
The BPD is likely to affect the U.S. MWF market bidirectionally. European companies that have invested to develop BPD toxicological data packages are likely to use these data to support U.S. EPA registrations. This could result in the availability of new active ingredients in the U.S. The major U. S. manufacturers are supporting BPD registration of their products. Because BPD registration satisfies the requirements of REACH, MWF compounders will be able to sell products that have been formulated using microbicides purchased from U.S. manufacturers.
Although the major MWF microbicide manufacturers do a good job of supporting their customers, the MWF market is an orphan biocide market. Microbicide sales into this sector are dwarfed by sales into other markets such as household and institutional products, water treatment and coatings. With the cost of introducing a new active ingredient approaching $4 million just for the data needed to support a registration application, it is unlikely that a new active ingredient will be developed principally for use in MWF. New chemistries will be introduced only after they have been proven successful in larger markets. This trend is exacerbated by the virtual disappearance of non-agricultural microbicide research and development. At most companies, R&D departments have shrunk to the point that the remaining technical staff members have little time to do more than technical support. This scenario is not conducive to new product development.
Beyond the regulatory costs and shrinking R&D efforts of microbicide manufacturers, a historical market dynamic continues to have an adverse impact on MWF microbicide innovation. It’s the use of chemicals that are not registered as biocides but whose function is primarily microbicidal. Under FIFRA, pesticide registration is required only for products whose intended use is as a biocide. The logic behind this is not unsound. For example, strong inorganic acids (consider concentrated sulfuric acid) can be extremely toxic. Since they are not normally used to control pests, they do not need to be registered as biocides.
For certain chemicals, the distinction is less clear. Consider dicyclohexylamine (DCHA; CAS 101-83-7). Like other primary amines, DCHA has a high pH (11) and pK
a (10.4). Compounders using DCHA can claim that it is being used solely as a neutralizing amine. However, in reality, DCHA is used primarily to confer biostability on MWF formulations. Phrased less delicately, it’s being used as an unregistered antimicrobial pesticide. Since the cost of toxicological and environmental fate and persistence testing for chemicals other than those registered as pesticides is a fraction of that required for pesticides, unregistered products are typically less expensive.
Recently, several compounders have discussed the risks associated with DCHA use in MWF (
7). Other products, some of which had FIFRA registrations prior to the 1986 data recall but whose manufacturers decided not to support retaining their registrations, continue to be marketed as buffering agents. Less toxicological data, however, does not translate into less risk. It simply reduces the incentive of microbicide manufacturers to bring new active ingredients into the marketplace.
THE FUTURE
More likely than not, although the number of available MWF microbicide products will remain stable or increase slightly over the next several years, the total number of active ingredients will shrink. In particular, with the possible exception of HTHT, formaldehyde-release products approved for tankside application are likely to disappear if manufacturers are required to develop life-cycle toxicity/carcinogenicity data. Unless the trend in research department spending is reversed, the level of technical support provided by microbicide manufacturers will diminish over time.
There’s a running debate on where microbicides should be added to MWF. Some end-users are adamant that microbicides should only be used tankside so that microbes in MWF systems won’t become resistant to the treatment chemicals. Others are equally adamant about not using any microbicides tankside. They object to the inconvenience of tankside additions and to the potential health risks associated with having their workers handle biocide concentrates in the plant. From a performance perspective, those who insist on tankside additions are on firmer footing.
www.canstockphoto.com
The concentration of active ingredient that is present in diluted MWF depends on the concentration at which it was added to the MWF concentrate, its stability in the concentrate, the end-use concentration of the MWF product and the various demands on the microbicide in the MWF system. The concentration of microbicide added to a MWF formulation is limited to the range that has been approved as part of the product’s FIFRA registration. Microbicide stability in concentrate is affected by the MWF’s total chemical composition, storage conditions and time between production and use. The microbicide concentration that’s appropriate for a MWF used at 7% is likely to be insufficient when the same MWF is used at 3%. Conversely, it may exceed the permissible dose level for a MWF used at 3% if the microbicide was formulated for a MWF used at 7%.
Finally, it is impossible to predict all of the demands (all factors that consume biocide molecules) on a microbicide in end-use application. Water-quality, metalworking operations and industrial hygiene practices all affect the rate at which microbicides in MWF are consumed. When handled in accordance with manufacturers’ recommendations, microbicides can be used safely as tankside additives.
Industry stakeholders are becoming more aware of the need to control both biofilm development and bioaerosol generation. Historically, the focus has been on controlling the numbers of microbes in recirculating MWF. Unless the biofilm community is also controlled, microbe numbers drop briefly then increase rapidly after biocide treatment. Moreover, the mechanism of biocidal action is likely to affect both the total amount and composition of bioaerosol in MWF mist. Over the next few years, I anticipate that industry stakeholders will consider the effects of biocides on biofilm and bioaerosols as part of the product selection process.
ACKNOWLEDGEMENTS
Although this article reflects my personal views of the MWF microbicide market, I am grateful to those who shared their perspectives with me and who commented to the thoughts that I shared with them. In particular I would like to thank Mike Pfister, Arch Chemicals; Nannette Hermsen, Dow Chemical Co.; Oliver Kretschick, LANXESS; Phil Miller, Lubrizol; and Adrian Krygsman and Richard Rotherham, Troy Chemical.
REFERENCES
1.
ASTM Standard, E-2169 (2007), “Practice for Selecting Antimicrobial Pesticides for use in Water-Miscible Metalworking Fluids,” ASTM International, West Conshohocken, Pa., 2003, DOI: 10.1520/E2169-01R07,
www.astm.org.
2.
Code of Federal Regulations, 40 CFR 122, EPA Administered Programs: The National Pollutant Discharge Elimination System.
3.
Directive 98/8/EC of the European Parliament and of the Council of 16 February 1998 Concerning the Placing of Biocidal Products on the Market.
4.
(EC) No.
1907/2006 of the European Parliament and of the Council of 18 December 2006 concerning the Registration, Evaluation, Authorization and Restriction of Chemicals (REACh).
5.
Passman, F.J. (1996), “Formaldehyde Risk in Perspective: A Toxicological Comparison of Twelve Biocides,”
Lubrication Engineering,
52 (1), pp. 68-80.
6.
Cohen, H.J. (1995), “A Study of Formaldehyde Exposures from Metalworking Fluid Operations using Hexahydro-1,3,5-Tris (2-hydroxyethyl)-S-Triazine,” In. J.B. D’Arcy, Ed.,
Proceedings of the Industrial Metalworking Environment: Assessment and Control. American Automobile Manufacturer’s Association, Dearborn, Mich., pp. 178-183.
7.
Anonymous (2006), “Controlling Microbial Growth… Safely,” Milacron Marketing Co., Cincinnati, Ohio.
STLE Fellow Fred Passman is president of Biodeterioration Control Associates, Inc., in Princeton N.J. You can reach him at fredp@biodeterioration-control.com.