PdM: Your choices for an effective oil analysis program
Dr. George Staniewski | TLT Cover Story October 2009
A nuclear engineer analyzes four testing options and explains how to best balance machine maintenance and cost factors.
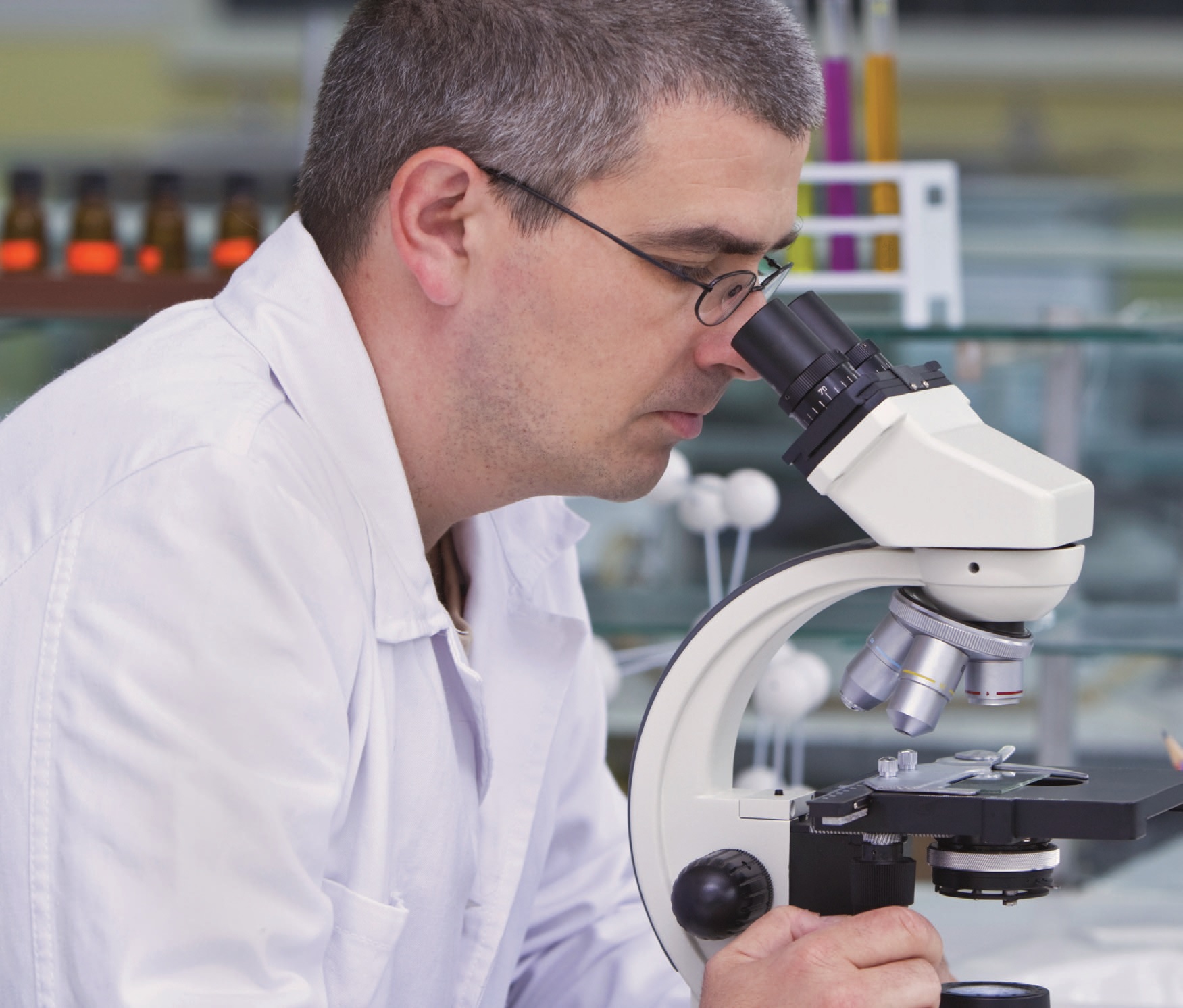
KEY CONCEPTS
•
In the last 30 years, predictive maintenance has slowly replaced preventive maintenance as the preferred machine maintenance strategy.
•
Commercial labs, in-house testing, mobile labs and at-line sensors are the four key oil analysis options and have their individual advantages and disadvantages.
•
For most industrial operations, a condition monitoring program that integrates the four testing options is usually the best approach for protecting machinery and reducing costs.
Dr. George Staniewski
For decades preventive maintenance (PM) has been the preferred maintenance strategy for manufacturers. Unfortunately, this approach is costly due to the need to halt the production process.
In the last 30 years, predictive maintenance (PdM) has been slowly replacing PM, particularly for critical equipment. Regrettably, most corporations did not achieve the expected level of economical benefit, as vibration monitoring was the only employed PdM monitoring technique. End-users slowly realized that their PdM programs could be more efficient if vibration analysis was supplemented by other PdM techniques such as oil analysis, infrared thermography and motor diagnostics.
The experience of successful industrial organizations suggests that an integrated lubrication program can significantly improve equipment reliability and availability, reduce operating costs and improve production and safety. Factors influencing the effectiveness of an integrated lubricant program include lubricant selection, the procurement process and quality assurance, the lubricant station database, storage and handling processes as well as condition monitoring and waste disposal.
While this article concentrates on condition monitoring, please recognize that improvement in only one element of a lubrication program cannot generate a sufficient and sustainable effect on improving equipment reliability and cost control.
GENERAL REQUIREMENTS
An effective oil monitoring program requires a high degree of cleanliness of the lubricating oils to enable the detection of changes in the solid particle distribution (i.e., strong signal-to-noise ratio). Individuals responsible for the condition monitoring program should initiate a design review of seals, filters and air breathers for the equipment selected. In addition, the cleanliness of new oils should be reviewed as well as associated handling and storage processes to ensure initial oil cleanliness is below the generic cleanliness target for a particular piece of machinery.
Since condition monitoring can be time-consuming, only selected equipment can be included in this program. In most cases this includes critical safety-related machines, equipment that may cause environmental hazards, equipment with long replacement lead times and equipment that has a critical impact on production. You also might want to include equipment with a poor operational record and those for which spare parts are not readily available.
Another important step is identifying an appropriate oil sample
location, as non-representative samples can make the testing and analysis meaningless. Equally important is
consistency of sampling methodology. For forced oil circulation systems, the preferable sample port location is on the oil return line. The concentration of wear particles in this line is greater than in other locations. Include a number of secondary sample ports for additional oil sample access if further investigation is necessary.
For splash oil-lubricated equipment, the preferable sampling port location is on the sump wall, usually with a stainless tube extension to the area of high turbulence. A similar option is a drain valve with a tube extension to allow sampling above the sump bottom. Ensure that the stagnant material in the tube is not captured for analysis.
The next steps are determining sampling frequency and the type of oil tests. Typically, sampling is based on the fastest rate of progression of the critical degradation mechanism. Some users, however, simplify this task by increasing the initial sampling frequency to generate a reliable baseline for all test methods. The purpose of a baseline database is to identify the present condition of equipment, determine the rate of change of lubricants and component deterioration and optimize target and alarm limits.
An oil baseline should be taken at the beginning of the condition monitoring program, after equipment overhauls, oil changes, and/or after any major process changes. Baseline, as well as all samples, should be obtained during normal operating conditions.
A typical oil sample volume is approximately 100 to 200 ml depending on oil type, its design function and the test.
Sampling methods should facilitate the procurement of a representative sample from equipment with minimum requirements for flushing the sample line. In addition, the sample should be kept to a minimum and the sampling procedure strictly adhered to.
A typical oil sample volume for most medium-size industrial equipment is approximately 100 to 200 ml depending on oil type, its design function and the performed test. Wherever possible, transparent plastic sample bottles (i.e., polyethylene terephthalate or PETE) should be used. However, end-users should also refer to ASTM D4057 standard.
The information on the oil sample bottle’s label is critical. At a minimum each sample should include:
1.
Equipment ID/description
2.
Sampling point
3.
Lubricant type
4.
Operating times or equivalent value, if possible
5.
Sample date and the name of the person taking the sample.
Extensive knowledge and experience is required from individuals involved in the interpretation of oil test results. Failed components should be inspected by those who performed the oil analyses. Images (obtained through an optical microscope and recorded by a digital camera) should be compared with previously obtained oil test results to establish a comparison between test results and actual wear.
Components considered for visual inspection should have clear orientation marks before their removal. This is necessary in order to identify the direction of acting forces. Carefully select the cutting area to avoid any damage to the wear pattern.
Finally, it must be realized that condition monitoring is an expensive approach; therefore a cost/benefit analysis should be performed on anomalies. Lack of cost benefit or cost avoidance may result in scope reduction or elimination of the condition monitoring program.
Specific industry applications have different requirements and, therefore, a different form and scope of oil monitoring program. In general, they can be divided into four primary forms:
1.
Commercial oil labs
2.
In-house oil screening facilities
3.
Mobile oil labs
4.
Continuous monitoring using sensor technology.
Let’s look at the pros and cons of each.
COMMERCIAL OIL LABS: ADVANTAGES
There are several advantages of an oil analysis program performed at commercial labs. First, this continues to be the most widely used approach for oil analysis. Initiated almost a century ago, its success generated a solid foundation for the concept of oil analysis by highly qualified experts.
Historically, the primary disadvantage that initially existed was inadequate oil testing capabilities, testing procedures and quality control systems. New and specialized instrumentation was yet to be developed, the information on the oil degradation mechanism was not well understood, and testing capabilities were significantly limited. The effect of lubricant on the lubricated components and particularly the testing of failed components were not always performed.
Most of today's commercial laboratories are well equipped with efficient, sophisticated and precision oil testing instruments. Commercial laboratories maintain control of oil standards and associated documentation such as the Certificate of Analysis and perform adequate periodic calibration of their testing instruments as well as frequent data validation activities. Most commercial laboratories regularly participate in different quality programs driven by ISO standards (i.e., 9001, 17025) or specific industry requirements (i.e., Nuclear Utility Procurement Issues Committee).
PdM is more effective when vibration analysis is supplemented by other techniques such as oil analysis, infrared thermography and motor diagnostics.
The personnel involved in oil testing and particularly in the analysis of oil test results are well trained, provide unbiased opinion and possess information not only on the lubricant testing method and oil deterioration but also on generic equipment design. By performing frequent analysis for many different applications, they continuously enrich their interpretation skills and offer excellent input on both the lubricant and equipment conditions. Also, the work undertaken by commercial laboratories provided excellent input for our understanding of oil degradation mechanisms and provided justification for more formal research activities by oil suppliers and/or research institutions.
Another benefit of commercial laboratories is in their advanced computerized lab management system. Typically, the sample is effectively monitored from the time of arrival, through all phases of testing to report formation. Some laboratories allow their customers to have read-only access to their lab management system so that they also can monitor testing progress. Data transfer is done electronically and in some circumstances automatically imbedded into end-user database software. The end-user can not only inspect the current sample test results and developing trends but also be aware of the samples and testing status.
Commercial laboratories commonly deliver critical sample test results within 24-48 hours of sample receipt. More time-consuming tests are reported later, but this is due to test procedures rather than poor process efficiency. The benefit of an efficient and effective oil testing process allows commercial laboratories to offer end-users an affordable price for testing services. The cost per sample is most likely the lowest of any of the discussed options.
Some industries have very specialized requirements for testing. In these cases, specialized commercial laboratories are the best choice for such analysis. An example of such a requirement is the need for thermal aging and/or irradiation resistance of selected lubricants used at nuclear power plants in safety-related systems.
End-users must use proper sampling bottles and techniques when working with a commercial lab.
COMMERCIAL OIL LABS: DISADVANTAGES
There are, however, several disadvantages of commercial laboratories. One of the most important is a poor control over sampling methodology. End-users must use proper sampling bottles with an acceptable internal cleanliness level, employ proper sampling hardware and follow correct sampling procedures.
Additionally, end-users must obtain representative oil samples from appropriate locations, under normal operating conditions at designated intervals. This might require installing new sampling ports.
A further concern is shipping. This task depends on appropriate packaging and shipping procedures, which can be more challenging than it sounds—consider oil samples from marine ships, military armor vehicles or radiation-contaminated equipment from nuclear stations.
End-users also should communicate to the commercial laboratories all factors that could affect the oil analysis such as oil makeup, external filtration or performance of equipment maintenance. In general, commercial laboratories have poor access to the end-user’s operation database. Both parties must implement an efficient two-way communication process. Without this feedback loop, some test results could be misinterpreted. Laboratories deal in high volume and cannot afford to learn about the sample history.
One of the important limitations of an effective oil analysis program is the in-service cleanliness of the lubricating oil or hydraulic fluid systems. End-users must maintain a relatively high cleanliness level in their lubrication and hydraulic systems to allow for early detection of wear particles.
Also, most commercial labs do not always use ASTM test methods, as some are not cost-effective. Most of them implement some modifications of typical ASTM standards. In such situations, the repeatability and reproducibility of their data is an unknown. End-customers have no way of knowing how precise the data is, so the data provided from a commercial lab is likely to have the lowest quality of any of the discussed options. The associated problem with oil test modification is the possibility of being unable to compare test results from one lab to another.
Another disadvantage of commercial laboratories is the potential for relatively poor in-house knowledge on lubricating oils and their deterioration mechanisms. Although there is always a possibility to get input from the commercial lab analyst, it is the end-user’s responsibility to verify the recommended corrective actions and implement them as required. Lack of adequate understanding of the test results and their interpretation could cause a failure of the entire analysis program.
Finally, the need for revenue generation will entice most commercial laboratories to accept and process large numbers of samples. This may negatively impact their ability or willingness to specialize within a specific industry or application and, therefore, limit the interpretation skills of their analysts.
IN-HOUSE OIL SCREENING: ADVANTAGES
During the past two decades, for safety or regulatory requirements, some corporations were forced to perform initial oil testing in-house. Some users, however, implemented in-house oil testing to increase their monitoring capabilities of critical equipment. The same crews involved in the predictive maintenance program enlarged their monitoring scope by performing not only vibration analysis but also in-house oil screening tests, infrared thermography and ultrasound or motor diagnostics. This was implemented to achieve earlier detection of equipment deterioration and widen the margins for scheduling corrective actions.
One of the greatest benefits of this approach is that the personnel directly involved in the monitoring process have a good knowledge of the equipment and its performance. The predictive maintenance crew has the advantage of inspecting the removed failed components and correlating their monitoring parameters with actual component damage. There is also the opportunity to perform correlation analysis with different PdM indicators and optimize the predictive maintenance scope, an invaluable learning opportunity.
By performing in-house oil analysis, corporations may eliminate or significantly reduce the requirements for oil sample shipments and their associated costs. This could be of great benefit in cases of regulatory requirements for additional testing prior to shipment.
One of the benefits of in-house oil testing is the potential for immediate oil analysis in emergency conditions. Although the aforementioned monitoring approach improves the early detection of equipment deterioration, emergency situations will occasionally occur, and the rapid response of an in-house facility is critical for safety. The in-house screening facility also allows an organization to test equipment to declare that it is acceptable for service. This is almost as powerful as stating that a problem exists.
In-house oil testing also improves the quality control process of new lubricants through verification of critical properties against approved specifications. Such commercial grade dedication activities provide another baseline for the trending purposes. The in-house lab is likely to produce the highest quality data in terms of repeatability and reproducibility of the discussed options.
Many end-users begin in-house oil analysis programs to better monitor critical equipment.
IN-HOUSE OIL SCREENING: DISADVANTAGES
In today's economy, justifying a large budget for an extensive in-house monitoring program is difficult. Only some industries can justify such a large budget and relatively high cost per oil sample based on the penalty of lost production or jeopardized public safety.
Some end-users tried to minimize the purchase of expensive instruments by substituting simple testing equipment. In most cases, the precision and detection limits of these apparatuses are significantly lower and do not allow for the detection of early lubricant deterioration.
Another potential disadvantage of in-house oil screening programs is the maintenance personnel's inadequate knowledge of a robust analysis program. Most end-users do not possess adequate knowledge of component degradation mechanisms and the parameters that allow for the monitoring of their progression. They may not have sufficient knowledge of the critical elements of an efficient in-house oil analysis program, the preferable scope and frequencies of oil sampling and the testing.
In addition, the testing is carried out by mechanics who require additional training and may not fully appreciate the need for data validation or periodic instrument calibration. In-house testing is generally understood as a screening tool that does not require extensive data verification. This is a concern as standard maintenance activities such as in situ filtration or oil replacement may be performed based on erroneous interpretation.
In-house oil screening requires a selection of appropriate database software capable of recording and trending all collected data, performing some statistical analysis and providing good access to the maintenance work management system and other predictive maintenance databases. Since maintenance labor is one of the main cost factors of in-house testing, both automated instruments as well as automated data transfer from test instrument into database are preferred. In most cases, neither oil database software nor all lab instrumentation has these capabilities.
Relatively few oil samples make it difficult to justify automated instrumentation, forcing in-house personnel to perform manual testing of each sample. This decreases testing efficiencies, increases the cost per oil sample and diminishes the interest of personnel involved in repetitive oil testing. As a result, frequent personnel rotation may be experienced, thereby increasing the cost of training and negatively impacting the quality of testing and the interpretation of results. The in-house lab produces a higher cost per sample than a commercial lab and has limited flexibility.
Another frequent problem associated with in-house oil screening programs is related to an inadequate lab management process. Usually, only personnel directly involved in oil analysis are aware of the status of the oil sampling process. This leaves management and equipment owners unable to independently monitor the progression of the sampling process.
In most cases, in-house testing concentrates only on the basic properties, which may necessitate periodic testing at external commercial laboratories. This increases the cost of the testing program, sometimes bringing into question the need for in-house testing.
Similar to any sample-based monitoring program, in-house oil screening programs require the installation of proper sampling ports and use of adequate hardware and procedures. Organizations with in-house oil screening programs are responsible for purchasing and storage of oil sampling supplies and any safety procedures related to solvent handling. Safety and fi re protection hardware and procedures also must be implemented to satisfy all local and national requirements. Further modification to the equipment components also might be required to minimize contaminant ingression rate.
Another potential problem is related to the limited number of qualified in-house staff capable of performing oil analysis and possessing extensive interpretation skills. These personnel are not always on-site due to training, sickness or vacation—furthering the potential for problems, particularly during emergency conditions.
MOBILE OIL LABS: ADVANTAGES
To address some of the disadvantages of oil analysis programs performed by commercial laboratories and in-house oil screening, some organizations introduced an oil program based on testing performed in mobile oil laboratories. This concept eliminates an in-house oil screening facility and also reduces shipment costs.
In general, this approach can significantly reduce the overall cost of the oil analysis program, particularly in comparison to a typical in-house oil screening concept. At the same time, mobile oil laboratories provide better access to operating data and knowledge of environmental impact and design limitations of the equipment. Depending upon the particular arrangement, the contractor also could perform oil sampling.
Most mobile oil labs possess automated testing instrumentation with high precision and detection limits that allow for early detection of equipment deterioration and efficient testing. The test results can be automatically downloaded to the local user's database with immediate interpretation and corrective actions. Theoretically there is a greater opportunity to inspect the failed components and adjust oil limits and program scope.
End-users are not responsible for calibration of the oil testing instruments and data validation process. Additionally, end-users are not responsible for upgrades to the oil testing instruments and storage of the clean oil-sample bottles.
This approach for oil sampling allows for a better understanding of particular equipment operating data, working conditions and performed maintenance. If required, analysts immediately can have access to additional design data or operational history. Finally, a good relationship between the mobile and maintenance crews can reduce or even eliminate the need for an on-site resident expert on lubrication.
MOBILE OIL LABS: DISADVANTAGES
The main disadvantage of this approach is a limited number of oil testing instruments in the mobile laboratory. Usually, only tests with a short completion time can be conducted. A long-term test requires a commercial laboratory.
Also, mobile laboratories present difficult working conditions for personnel performing tests and analyzing data. This may result in frequent staff rotation. In addition, the congested space, an inability to control temperature and humidity as well as the potential for vibration impacting instruments during frequent mobile lab movement might affect test results.
Since the oil testing and sampling could be conducted by the contractor, there could be inadequate in-house knowledge and experience on lubrication practices. Lack of a resident lubrication expert may influence the quality of the integrated lubrication and advance PdM programs.
Again, installation of appropriate sampling ports and additional improvements to the equipment hardware to minimize contamination ingression are necessary.
SENSOR TECHNOLOGY: ADVANTAGES
Sensors detecting simple oil parameters and other associated properties have been implemented successfully for several years in industrial applications. The most important advantage of sensor technology is its ability to provide continuous monitoring and data collection during the entire operation cycle. This is an invaluable asset, particularly for equipment in remote or inaccessible locations. Applications such as wind power turbine gearboxes, equipment located in nuclear reactors or in mobile equipment are good examples of systems benefiting from sensor technology.
Sensors are rugged enough to withstand normal industrial environments and can be installed directly in hydraulic systems and lubricated components, providing real-time data collection and retrieval. Typically, sensors monitor such properties as cleanliness, wear debris, water content, dynamic viscosity, presence of some additives, dielectric properties, oxidation and acid/base numbers. Recent developments in multiparameter-based sensors, providing multiple outputs on several properties, further enrich the sensor technology potential.
The introduction of more sophisticated sensors capable of monitoring critical properties of lubricants and contaminants allows end-users to make decisions based on real-time conditions reported continuously. Sensor technology also allows for the implementation of expert systems providing consistent and more accurate interpretation of oil and equipment conditions. Oil results can be immediately correlated with other predictive indicators and performance parameters to enhance the interpretation capabilities. Current developments in telecommunications can allow for continuous monitoring anywhere in the world via the Internet. This provides a comprehensive integrated automatic assessment of stationary and mobile equipment conditions worldwide.
Sensor technology provides an additional advantage to the traditional monitoring programs by helping to identify the optimum time for additional testing. Lubricant samples will be taken only as required, when a definitive need for additional input has been identified.
SENSOR TECHNOLOGY: DISADVANTAGES
One concern is the poor involvement of equipment manufacturers in including sensors in their equipment. Most manufacturers do include a number of sensors for monitoring performance characteristics of equipment or systems; however there is resistance on their part to install oil monitoring sensors. End-users are taking the initiative by retrofitting oil sensors to their equipment and enhancing their monitoring program. This process is more expensive as it includes design approval for the proposed modification and loss of production time.
Another challenge facing sensor technology is the need to improve data collection and storage. Software must be capable of monitoring large volumes of data, including proper data selection, recording, retrieving and reporting. Although there are databases that can handle such demanding requirements, further innovation is needed in this area.
The most important disadvantage of the sensor approach is the limited number of properties that can be measured. This often requires further testing, using standard test methods, conducted in a laboratory environment. However, the one advantage in this scenario is that additional testing would only be conducted as required. It is important to note that sensor technology would not exclude the need for the previously discussed testing options including commercial lab, in-house screening program or mobile laboratories.
Since additional testing in laboratory environments could be needed, the end-user might need to install appropriate sampling ports, maintain sampling containers and packaging and improve equipment hardware to minimize contamination ingression.
One further challenge facing sensor technology is the need for periodic calibration. Also, sensors will eventually have to be replaced in a manner that allows for continuous data collection.
CONCLUSION
None of the discussed options alone can satisfy the requirements of an all-encompassing and sustainable monitoring program. In most cases, end-users implement a combination of options to achieve their cost-control objectives.
A significant interest in the installation of in-line monitoring sensors is likely. Sensor technology will be associated with expert systems for helping end-users to interpret lubricant and equipment conditions.
In the near future, end-users will more readily implement the integrated lubrication programs due to recognition of the benefit and impact on improvements to equipment reliability and production cost-control.
George Staniewski, P.Eng., OMA, CLS, is senior technical engineer with Ontario Power Generation, in Pickering, Ontario, Canada. He is a professional engineer in the Province of Ontario and holds three STLE certifications: Certified Lubrication Specialist, Oil Monitoring Analyst I and II. You can reach him at george.staniewski@opg.com.
George would like to acknowledge Dave Frycki from Herguth Laboratories and Bryan Johnson from Palo Verde Nuclear station for providing comments on this article. A separate acknowledgment is extended to Allison Toms from GasTOPS, Ltd. and Dr. John Duchowski from HYDAC Filtertechnik GmbH, Werk 8 for inspiration to prepare this article.