Selecting the ‘perfect’ metalworking fluid
Jerry P. Byers, CMFS | TLT Best Practices March 2009
In addition to fully understanding the operating conditions, be sure to question all assumptions about MWFs. Many of them are the tribological equivalent of old wives tales.
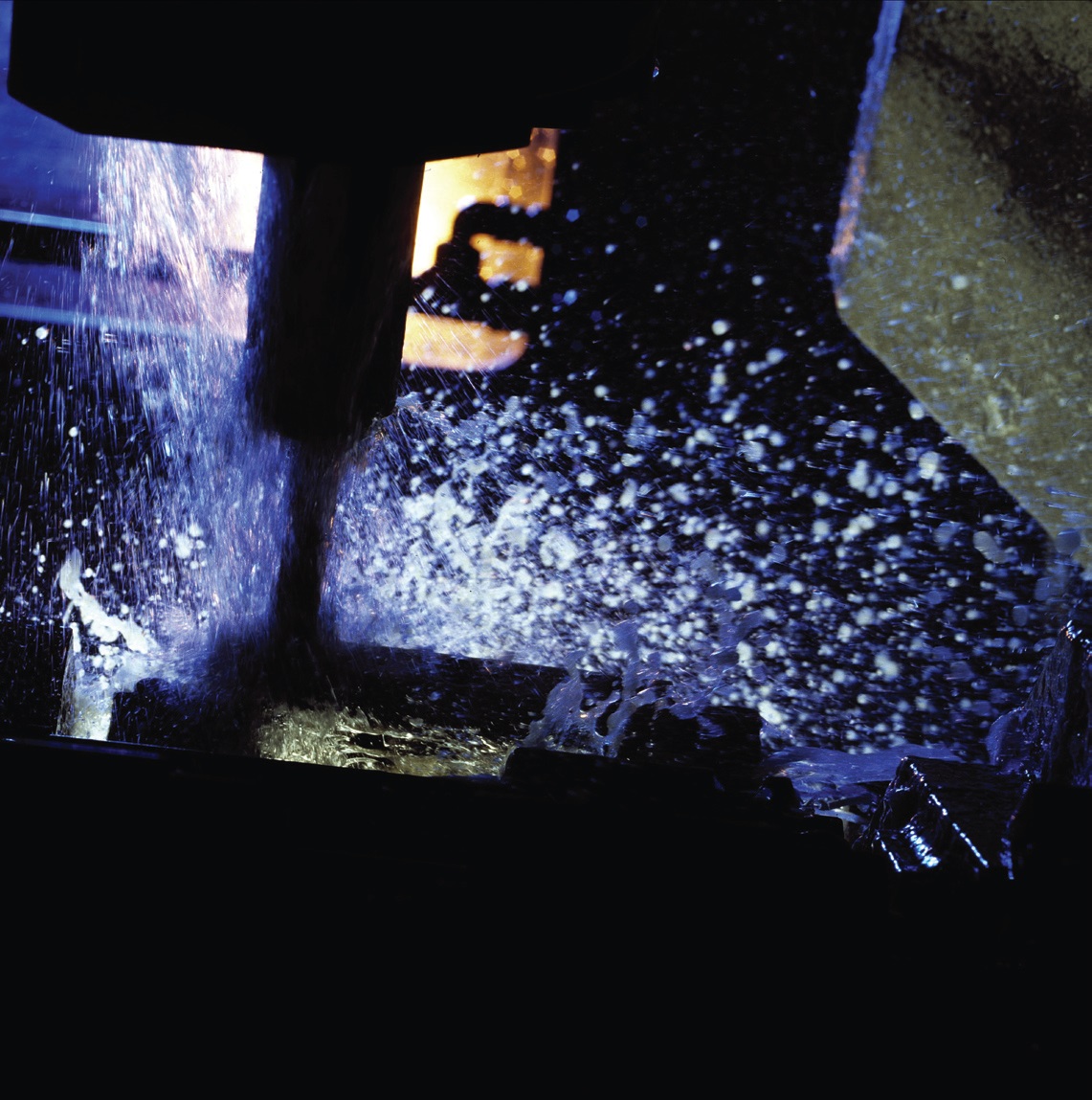
Metalworking fluids are a key production aid in the manufacture of metal parts, from seemingly simple items such as coins and wire, to complex objects such as medical devices and engines for aerospace applications.
www.canstockphoto.com
KEY CONCEPTS
•
Understanding the four basic categories of MWFs is recommended before selecting the best fluid choice for a particular plant or operation.
•
Though many fluids work well with a given application, one may offer slightly better rust control and another slightly better tool life or cost advantages.
•
•
There is no such thing as a single “perfect” MWF that can be used in every plant, under every condition, for every operation.
Metalworking fluids (MWFs) are a key production aid in the manufacture of metal parts, from seemingly simple items such as coins and wire, to complex objects such as medical devices and engines for aerospace applications. These fluids are used because it is more cost effective to run most operations with a fluid than without. The benefits include more high quality finished parts by the end of the shift with lower tool wear, reduced grinding wheel usage and less machine downtime.
MWFs help maintain a constant temperature for the metal part, the tool and the machine—improving dimensional stability of the parts produced. Temperature control is achieved through (1.) lubricants that reduce heat generation and (2.) the cooling action of the fluid that removes heat. The fluid is also used to carry metal particles (chips) away from the cutting zone to an area where they are separated and collected.
The benefit for tool life is shown in Figure 1, a graph of tool wear vs. machining time for a turning operation where 390 aluminum is being machined with polycrystalline diamond tooling under two conditions: either dry or with a semisynthetic MWF being applied. Notice that tool wear is greatly reduced and the time between tool changes is dramatically extended when the fluid is applied.
Figure 1. Graph of tool wear vs. machining time
An additional benefit is that MWFs keep metal fumes and dust out of the air. One study published in
Applied Occupational Environmental Hygiene showed that in many situations where water-based fluids were in use, total particulate in the air was less than when cutting metal dry (
1). STLE-member Lloyd Lazarus of Honeywell FM&T, LLC, in Kansas City, Mo., describes how one plant handles metal dust concerns: “(Stainless steels are) high in nickel and chrome content. When machined, a microscopic amount of dust is generated at the chip-workpiece interface. These microscopic particles are breathable and present a health hazard (based on the ACGIH TLV). When we use cutting tools that are designed to run dry (to obtain better tool life) in an enclosed machine tool, we use the MWF to wash the dust from the part, fixture and table before unlocking the enclosure. We use a similar approach when machining alloys with other hazardous components (
2).”
SELECTION CRITERIA
Obtaining the above benefits starts with fluid selection. There are many companies that offer MWFs, and each typically will have a wide array of fluid options. How does one arrive at the best fluid choice for a particular plant or operation? First, one must understand that there are four basic categories of MWFs:
•
Straight oils are used as received, without dilution.
•
So-called soluble oils have a high petroleum oil content but are designed to be diluted in water to form a milky dispersion.
•
Semisynthetics contain a low to moderate oil content, plus water and performance additives.
•
Synthetics contain only water and water-soluble additives but no mineral oil.
Each of the last three categories are sold as concentrates and then diluted with water at the point of use. These four categories cover most of the MWFs available on the market. However, other products using vegetable or synthetic oils may also be available, but these can generally be expected to perform similar to the above four types relative to the amount of “oil” they contain.
Figure 2 illustrates the differences between these four categories. Each class of products offers certain advantages and disadvantages, which are summarized in Figure 3. This is a broad-brush generalization, and there are certainly exceptions to every statement, but the table gives a glimpse into how compositional differences affect performance.
Figure 2. Metalworking fluid classifications
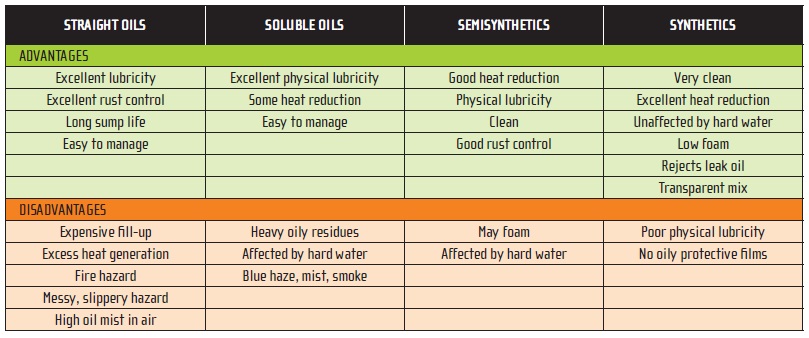
Figure 3. Advantages and disadvantages of the four basic MWF classifications
MATCHING THE FLUID TO THE APPLICATION
The presence of petroleum oil in a product will provide a physical lubricating film under light loads called “hydrodynamic lubrication.”
The lubrication properties of both water and petroleum oil can be enhanced through the use of various additives. Fats, vegetable oils, fatty esters, fatty acids, fatty alcohols, soaps and polymers can be added to improve boundary lubrication. These “boundary lubricants” have a weak affinity for the metal surfaces to help prevent tool wear and protect the machined surface. Products containing only boundary lubricants are typically used in light to moderate duty applications.
Another class of lubricants called “extreme pressure” or “EP” lubricants may be formulated into the heaviest duty MWF. These are typically molecules that contain either phosphorous, chlorine or sulfur and tend to be used in heavy-duty products. Under conditions of high heat or pressure, EP additives chemically react with the metal surfaces to form a strong, protective barrier film. However, if the cutting conditions are not severe enough, EP lubricants will not be activated, and their potential benefits will not be realized. Thus, putting a heavy-duty product in a light-duty operation may offer no measurable improvement over a lighter duty fluid. All of these lubricants are available in relatively more oil-soluble or water-soluble forms and can be used in any of the MWF types.
To help decide whether a light, moderate or heavy-duty MWF is required, many common metal-removal operations have been ranked in Figure 4 for easy reference. Figure 5 shows typical product compositions for water-based fluids designed for these light, moderate and heavier duty applications.
Figure 4. Machining and grinding severity

Figure 5. Fluids for each application
PLANT SURVEY
Once the severity of the operations has been determined, a number of other factors must be considered that will affect the choice of fluid. Consider the following:
•
What metals are involved? Consider the metals being machined, as well as metal components of the machine tool. A fluid that has excellent rust control but is not compatible with aluminum could be used for machining cast iron and steel—as long as there are no aluminum components on the machine itself. However, many fluid manufacturers will typically formulate aluminum and/or copper inhibitors into their products to protect machine tool components. Corrosion testing on the various metals involved is advisable.
•
Do the machines have individual fluid reservoirs, or are they connected to a large central system? Fluids in individual machines need to be able to run without much maintenance or attention.
•
Are individual machines equipped with a system for removing metal chips from the fluid, or do the chips accumulate in the machine sump until it is dumped and cleaned?
•
Are machines new and well sealed, or are they older and leak a lot of oil? How does the MWF being evaluated handle leak oil? Reject it? Emulsify it?
•
Is there any means of oil removal on the sump?
•
What is the water quality? Since water is typically 90% to 95% of the in-use fluid, and is constantly being added to replace evaporation losses, it has a major impact on performance. Water that is too hard will eventually lead to instability of the diluted mix and corrosion problems. Water that is too soft may cause foaming. Softened water is not as good as deionized (DI) or reverse osmosis (RO) water when it comes to corrosion control and emulsion stability. The fluid must be able to tolerate the water conditions, or the water quality needs to be improved.
•
What is the method used for fluid disposal? Test the fluid using that method.
•
How much time do operators’ hands spend in contact with the fluid? For individual machines, the contact time is probably high, requiring a very mild fluid, whereas for automated transfer lines the skin contact will be minimal.
•
Are any preliminary screening tests conducted in the plant (foam, corrosion, isolated machine test, waste treatment, etc.)?
•
Are there any specific chemical restrictions within the plant or municipality (silicones, phenols, chlorinated compounds, secondary amines, etc.)?
•
Are there problems with the fluid currently in use?
•
How will the fluid be monitored and controlled?
•
Is a fluid recycling system being used?
•
Is the fluid diluted via a premix tank, automatic proportioning device or by dumping concentrate and water directly into the sump?
•
What contaminants are expected to enter the system?
CHECK THE MSDS
Review the supplier’s MSDS during the selection process, but be careful about the conclusions drawn from the review. Does the MSDS represent actual data or merely opinions? A health rating of zero (NFPA or HMIS systems) could simply be an opinion. Most any MWF concentrate will be an eye irritant, which requires a health rating of 1. If the health rating is 1 or 2, there should be at least one hazardous ingredient listed. There is no requirement that an MSDS list every ingredient—just the ingredients related to the hazards associated with the product.
HOW NOT TO SELECT A FLUID
Many fluids work well on a given application, although one may offer slightly better rust control and another slightly better tool life or cost advantages. The MWF classifications of synthetic, semisynthetic or soluble oil only indicate oil content, not performance. Selection should be based upon the process requirements and potential benefits from the fluid choice rather than a match for the same type of product that was always used in the past.
Be sure that laboratory screening tests relate to the actual operation. When testing fluid filtration, do not use a membrane filter for the lab test if the plant uses non-woven, pressed-fiber filter media. Similarly, do not use a test method simply because it was published somewhere or is an ASTM standard. ASTM test methods that were developed for one application may give misleading results if used for an entirely different, unrelated application.
For example, copper corrosion tests conducted at elevated temperatures in a “corrosion test bomb” and intended for use with diesel fuels should not be used to evaluate corrosion control with water-based fluids. Many tests appropriate for MWFs have been described in published literature (
3-4).
Selecting one fluid because it has a zero health rating on the MSDS over another that has a 1 rating assumes that both ratings were assigned using the same guidelines and based upon toxicological data, which may not be the case.
Selecting a fluid because its MSDS lists the fewest number of hazardous ingredients assumes that all suppliers use the same criteria for listing ingredients. Again, this is probably not the case.
Don’t play the “no, no” game by selecting products based upon someone else’s list of forbidden chemicals. You should understand why each material is forbidden and the consequences of that decision.
Consider:
Some plants request no surfactants. The term “surfactant” is not a specific chemical and simply means a surface-active material. Surface active ingredients serve many functions in a MWF from corrosion control, lubrication, emulsification, foam control, cleaning and wetting—every important property of the fluid.
Ban the boron? This is a good opportunity to contact the customer and ask about his concerns. Are they based on a waste treatment issue or a health concern? Boron is used in personal care and household products (i.e., boric acid in eye-wash and borax in the laundry) and reportedly has human health benefits such as enhancing the absorption of calcium for bone health. Peanut butter is a rich dietary source of bone-protecting boron (
5-6). In MWFs, the combination of boron and amines gives very good rust control on ferrous metals.
Absolutely no biocides (aka microbicides and antimicrobial pesticides) allowed. Microbicides are some of the most thoroughly tested materials available and must be registered with the EPA for each specific application. Without these ingredients, excessive levels of bacteria and mold could result, leading to high endotoxin content in the used fluid (from Gram-negative bacteria). Fluids that are claimed to control bacteria and mold “without biocides” are generally relying on unregistered materials to achieve the desired result (
7). An unregistered chemical is not inherently safer to use that a registered biocide. In fact, Dr. Arnold Legzdins states: “Unregistered compounds acting as biocides are potentially dangerous to users and the environment (
8).”
EXAMINE ASSUMPTIONS
Anyone with an e-mail address has received e-mails containing stories or warnings that sound reasonable but later prove to be untrue. Several Web sites have sprung up to help the reader determine whether these stories are fact or fiction. Similarly, there are many assumptions within the industry that are not upheld by scientific studies. Here are a few that bear further examination:
Triazine causes the growth of mycobacteria. Mycobacteria have been proposed as a causative agent for hypersensitivity pneumonitis, and triazine is one of the oldest and most widely used bactericides in the industry. It has been proposed that the use of triazine in a MWF system can lead to the development of mycobacteria. A recent unpublished laboratory study of 12 MWFs stated that eight contained triazine, and four used other types of microbicides. All eight triazine-based formulations gave complete control of mycobacteria (no counts), while those without triazine had high growth. (A mixed mycobacteria culture was used in this study.) At STLE’s 2006 Annual Meeting in Calgary, Dr. David Ashworth presented data showing that the use of triazine could indeed control the growth of mycobacteria in MWF (
9). An article by Dr. Jagjit Yadav (
10) reports that mycobacteria are simply more resistant to
all microbicides (not just triazine) than are other bacteria commonly found in MWF.
Some MWFs allow growth of only “good” bacteria. Studies have found repeatedly that the same organisms show up in all types of MWF. Besides, even “good” bacteria will release endotoxins into the fluid. The best approach is to keep
all bacteria counts at low levels.
Just let the Gram-negative bacteria grow, and you won’t have mycobacteria. STLE-member Len Rossmoore of Biosan Laboratories, in Warren, Mich., states that this concept “proved to be untrue (
11).” Further, a study conducted by Koh and Koh, and presented at the 15th International Colloquium on Tribology in Esslingen, Germany, found that “mycobacteria and Gram-negative bacteria coexisted in the coolant system” and the “mycobacteria population increased with the level of Gram-negative bacteria (
12).”
The cost of using MWF represents 16% to 20% of the total manufacturing cost. Tooling companies and others like to quote this ridiculous figure (
13), although no original source for the data can be located. Their conclusion is that machining should be done dry to save money. Studies conducted in two different manufacturing plants in the U.S. refute this assumption:
Lloyd Lazarus of Honeywell FM&T, LLC, conducted an extensive cost review of his company’s operations and concluded that MWF costs for all machining operations averaged less than 3% of the total manufacturing costs. His analysis included MWF purchase price, system cleaning, chemical material handlers, salaried and hourly technical support, waste disposal costs, system maintenance costs, machine operator labor costs and perishable tooling. The cost of the metal being machined was not included, however, which would have further reduced the MWF percentage (
14).
STLE-member Doug Hunsicker and George Egger of Caterpillar, Inc., in Peoria, Ill., report that fluid costs at their plant have remained less than 1% of manufacturing costs for almost 30 years (1974 to 2001). During the same time, perishable tooling costs ranged from five to 12 times the fluid cost. Again, their data did not include the cost of the metal being machined (
15, 16).
CONCLUSIONS
Contrary to what the title of this article implies, there is no single “perfect” MWF that can be used in every plant, under every condition, for every operation. Many fluids could work well on the same job. One might offer better corrosion control, while another might be somewhat better at lubricating the cut. Laboratory test methods may be used to evaluate MWF candidates, but the tests should relate to the actual conditions of the operation.
Examine common industry assumptions about MWF. Contrary to earlier claims, the cost to use MWF represents between 1% and 3% of total manufacturing costs, depending upon the operation and plant conditions. Application of a fluid will improve almost every metalworking/metal-removal operation by lubricating, cooling, improving surface finish and extending tool life in savings on tool purchases and machine downtime. MWF also helps to keep metal dust and fumes out of the air. To obtain these benefits, take care of the MWF, and do not treat the fluid system like a sewer.
REFERENCES
1.
Woskie, S., et al. (1994), “Factors Affecting Worker Exposures to Metalworking Fluids During Automotive Component Manufacturing,”
Applied Occupational and Environmental Hygiene,
9 (9), pp. 612-621.
2.
Lazarus, L. (2006), “Costs Associated with the Use of Metalworking Fluids,”
Metalworking Fluids, Second Edition, CRC (Taylor & Francis) and STLE, pp. 422-423.
3.
Byers, J.P. (2006), “Laboratory Evaluation of Metalworking Fluids,”
Metalworking Fluids, Second Edition, CRC (Taylor & Francis) and STLE, pp. 422-423.
4.
ASTM. (2003),
Metalworking Industry Standards: Environmental Quality and Safety, Fluid Performance and Condition Monitoring Tests, ASTM International, Philadelphia, Pa.
5.
Carper, J., “Eat Smart,”
USA Weekend, Gannett Publication (June 3, 2001).
6.
“Postscripts,”
The Cincinnati Post, Scripps Howard Newspaper (March 15, 2006).
7.
Rossmoore, H. (1993), “Biostatic Fluids, Friendly Bacteria, and Other Myths in Metalworking Microbiology,”
Lubrication Engineering,
49 (4), pp. 253-260.
8.
Legzdins, A., “Biocide-free MWFs: Are They Really a Safer Alternative?” Presented at the MRF 2008 Symposium, Dearborn, Mich. (October 2008).
9.
Ashworth, D., “Triazine in Metalworking Fluids: Its Role in the Control of Micro-Organisms that are Injurious to Health,” Presented at the 61st STLE Annual Meeting & Exhibition in Calgary, AB, Canada (May 9, 2006).
10.
Yadav, J., “Role of Biocides in Establishment of Mycobacterium in Metal Removal Fluids,”
Report to the United States Council for Automotive Research (USCAR) (June 30, 2004).
11.
Rossmoore, L. (2005), “Magnets and Magic Wands: Exploring the Myths of Metalworking Fluid Microbiology,”
Compoundings,
55 (9), pp. 19-21.
12.
Koh, K.W. and Koh, K. (2006), “Biological Activities in Metalworking Fluid Systems,”
Automotive and Industrial Lubrication—Book of Synopses, 15th International Colloquium Tribology in Esslingen, Germany, W. J. Bartz, Ed., Technische Akademie Esslingen, p. 58.
13.
Canter, N., (2003), “The Possibilities and Limitations of Dry Machining,” TLT,
59 (11), pp. 30-35.
14.
Lazarus, L. (2006), “Costs Associated with the Use of Metalworking Fluids,”
Metalworking Fluids, Second Edition, CRC (Taylor & Francis) and STLE, pp. 421-423.
15.
Hunsicker, D. and Egger, G. (2004), “Optimizing Metalworking Fluid Processes,” Presented at the STLE Metalworking Fluids Course in Toronto, ON, Canada.
16.
Canter, N. (2003), “The Possibilities and Limitations of Dry Machining,” TLT,
59 (11), pp. 30-35.
Jerry Byers is a certified metalworking fluid specialist (CMFS) and is the manager of Cimcool Product Research & Development at Milacron, Inc. in Cincinnati. He also serves on the STLE Board of Directors and is the editor of the best-selling book, Metalworking Fluids, Second Edition. You can reach him at jerry_p_byers@milacron.com.