KEY CONCEPTS
•
Electric vehicle (EV) transmission fluids, which multitask as lubricants and coolants, are likely to be formulated as vehicle design elements, with fill-for-life applications in mind.
•
EV fluid formulations may help dissipate stray electrical currents, and they must be compatible with the copper wiring and polymer seals and insulators with which they come into contact.
•
Thermal management fluids for battery and power electronics systems are an active area for development.
Electric vehicles (EVs), because they are fundamentally different from internal combustion vehicles, are presenting multiple challenges—and opportunities—for lubricant formulators. “I’ve been developing lubricants for almost 30 years, and this probably has been the biggest single change that we’ve faced over the years,” says Michael Gahagan, driveline technology manager for The Lubrizol Corp. in Derby, UK.
Changing demands
Sales of EVs are increasing, and these increases are projected to continue, says Gahagan. However, internal combustion engine (ICE) vehicles, including hybrid vehicles, will continue to be used for the foreseeable future, he says. Even ICE vehicles now feature an increasing number of electronic components—sensors, electronic ignition, computerized driver-assist devices and start-stop configurations, to name a few. He refers to the proliferation of vehicle transmission design types as a “Cambrian explosion,” referring to the proliferation of life forms that appeared some 500 million years ago. Some species persisted and thrived, and others went extinct—a fate that could await some of the types of vehicles now on the road or currently under development (
see Figure 1).
Figure 1. Evolution of vehicle designs and components. ICE = internal combustion engine, HEV = hybrid electric vehicle, PHEV = plug-in HEV, REEV = range-extended EV, BEV = battery EV and FCEV = fuel cell EV. Figure courtesy of Gareth Fish, The Lubrizol Corp.
Passenger cars are leading market growth in hybrid and all-electric vehicles today and are expected to continue to outpace two-wheeled and commercial vehicles.
1 Hybrid cars continue to use ICEs, but they also have batteries and their cooling systems, as well as one or more electric motors. Having both systems can increase range, since the vehicle does not rely solely on the battery for stored energy. However, this increased range is at the expense of added weight and less room for passengers and cargo.
EVs differ from ICE vehicles—and from each other—in a variety of ways. Motors, gearboxes and transmission systems vary in design according to the make and model of the vehicle. All-electric vehicles do away with pistons and cylinders, as well as many other components essential to ICE systems, including alternators and fans. EVs may have multiple electric motors, some situated close to the location (e.g., wheels or accessories) where the power is used (
see Figure 2). Stop-start vehicles do away with solenoid-based starters, in favor of permanently engaged starters that also serve as generators that recharge the battery. In vehicles with regenerative braking, the electric motor acts as a brake, with the energy returning to the battery when the brakes are in use.
Figure 2. Electric vehicle layouts and components require different lubricants than for ICE vehicles. Figure courtesy of Michael Gahagan, The Lubrizol Corp.
Anastazi Sarigiannis, business development manager for Klüber Lubrication NA LP in Detroit, Mich., says that the automotive parts industry is scrambling to adapt to the resulting decrease in demand for accessories typically associated with ICEs. “It’s becoming a more competitive situation where everyone’s trying to come up with a solution to those components that are left,” he says.
In addition to changes in vehicle designs, changes in vehicle usage patterns also affect performance requirements. Although some issues are unique to EV lubricant development, others affect lubricant formulation and economics in all types of vehicles. For example, the automotive industry has been slowly but steadily shrinking, Sarigiannis says. Ride sharing is steadily gaining ground over personal vehicle ownership, and autonomous vehicles are just over the horizon. Both of these developments are tipping the balance away from large numbers of privately owned vehicles of any kind that sit idle most of the time and toward much smaller numbers of shared vehicles that are, more or less, constantly in operation.
EVs really are different
New systems running under different operating conditions, loads and temperatures require new lubricants. Synthetic oils already on the market can hold up under the higher temperatures and more demanding operating conditions required by today’s vehicles, but the demand for even better performance is likely to continue to increase. “For increased longevity, you’re going to be looking at purely synthetic lubricants—and ones that typically have fairly high operating temperatures,” says Sarigiannis. He explains that synthetic lubricants resist oxidation much better than mineral oils, and, thus, hold up longer at higher temperatures, an important consideration for hot-running electric motors.
Longer lasting oils and greases also present an opportunity to increase the number of fill-for-life applications in electronic vehicles, including greases for sealed bearings and EV-specific automatic transmission fluids.
2 Unlike ICEs, electric motors do not release combustion byproducts into the lubricant stream. Because there are no combustion byproducts to degrade these oils, regular oil changes for passenger cars may become a thing of the past (or at least less frequent).
Lubricants for EVs serve different functions from their counterparts in ICE vehicles.
3 For example, an ICE needs motor oil to reduce friction in the engine. Transmission fluid circulates separately, and it serves as a lubricant, hydraulic fluid for gear shifting and coolant. Transmission fluids for ICE passenger cars are typically changed less frequently than motor oils (depending on OEM specifications).
Electric motors in an EV can run at 15,000 rpm or more, and the gear ratio reducer in an EV, which converts the motor speed to the speed needed to drive the wheels, functions as its transmission. EV transmission fluid is an oil that also lubricates the gearbox and serves as a coolant for the transmission. Many EV transmission fluids also are specifically formulated for thermal management of the electric motor(s) integrated in the same gearbox.
Efforts are underway to develop unique synthetic oil-based lubricants with rheological and thermal properties that work well for EV propulsion systems.
4 In addition, “A lot of automotive companies that are using oil-flooded electric motor systems are using something similar to automatic transmission fluid,” says Sarigiannis.
Thermal management fluids, in particular, are under continual development. Typically, thermal management fluids for EV batteries are distinct from the EV transmission fluid. Development of a single thermal management fluid suitable for batteries and transmissions is being actively pursued, but these efforts are still in the early stages. However, the efficiency of battery fluids also affects the performance of the electric drives, because these fluids help batteries deliver power on demand. Battery thermal management fluids help keep the battery and power electronics systems within the best temperature range for fast charging and quick acceleration, whether the vehicle is parked or in use.
Lubricants as a design element
Over the past decade, OEMs have increasingly asked for dedicated lubricants, tailored to the specific needs of their hardware designs.
5 The largest OEMs are very demanding in terms of technical requirements for each fluid application, says Thomas Gillet, team leader for driveline and electric fluids for TotalEnergies Lubricants in Paris, France. These companies have in-house tribology and formulation specialists who develop specifications and perform product testing. “One [oil that] fits all, unfortunately, will never happen,” he adds. However, for passenger cars, more and more applications are fill-for-life, so the factory fill fluids will not need to be replaced unless there is a leak or other type of malfunction.
At the consumer level, this specificity means that although an off-the-shelf oil might work in an EV, there is no guarantee that it will perform as well as the recommended oil, and it might not perform well at all. To ensure compliance with the terms of a vehicle warranty, a customer or mechanic would need to order the recommended fluid, citing a part or catalog number in much the same way that they would order a specific sensor or dashboard display component. For some applications, an OEM might provide a listing of approved fluids that are covered under the vehicle warranty.
Smaller OEMs, lacking in-house lubricant formulation and testing capabilities, may have to rely on products already on the market that are not customized to a specific make of vehicle. Likewise, smaller lubricant suppliers may find it challenging to meet the requirements of multiple OEMs, each with their own lubricant specifications. Gillet notes that several association working groups are emerging to establish standardized test methods and performance evaluation standards. These methods could prove useful to evaluate the suitability of various formulations across applications or manufacturers. Earlier this year, the Southwest Research Institute launched a consortium to develop a common approach to evaluating advanced fluids for electrified vehicles.
6 The Society of Automotive Engineers (SAE) has formed a technical committee to draft industry specifications for EV fluids,
7 and German and French automotive industry associations are helping to develop standards for the European Union.
Gahagan notes that there is not a single standard for EV lubricants, but that this is nothing new; ICE vehicle manufacturers also make use of multiple standards for guiding the formulation and testing of the lubricants they use. Over the past decade, Gahagan says, OEMs have increasingly asked for dedicated lubricants, tailored to the specific needs of their hardware designs. “Because the OEMs see [the lubricant] as a design component, they will specify that oil in as much detail with as much rigor, and, in many cases, with as much stringency, as any other components in the transmission.”
Gahagan adds that even though test methods and oil property definitions may be based on existing standards, OEM requirements for finished formulations are often quite advanced, involving a significant investment in research and testing to provide the best lubricant for their hardware design. He stresses that specialized fluids are valued highly, and the investment pays off in terms of increased reliability and better performance, especially in light of the extended lifetimes (up to and including fill-for-life) expected from today’s EV transmission fluids.
Electrical conductivity
Some of the challenges posed by EVs are already familiar to workers in industrial operations. Electrical currents, for example, can leak through a rotating stator and exit through a motor casing if a motor is not properly grounded. From there, the current follows the path of least resistance, and that path often goes through the bearings.
Electrical currents can travel from one bearing raceway, through the rolling elements and out the other raceway. Along the way, electrical arcing causes fluting damage: closely spaced parallel ridges. As the rolling elements pass over these ridged areas, they vibrate, producing noise and accelerating bearing wear. In vehicles that use variable frequency drives (VFD), current leakage is a higher possibility. VFD controllers vary the electrical frequency and voltage supplied to an electric motor to control the motor’s speed—higher frequencies generate higher rpm.
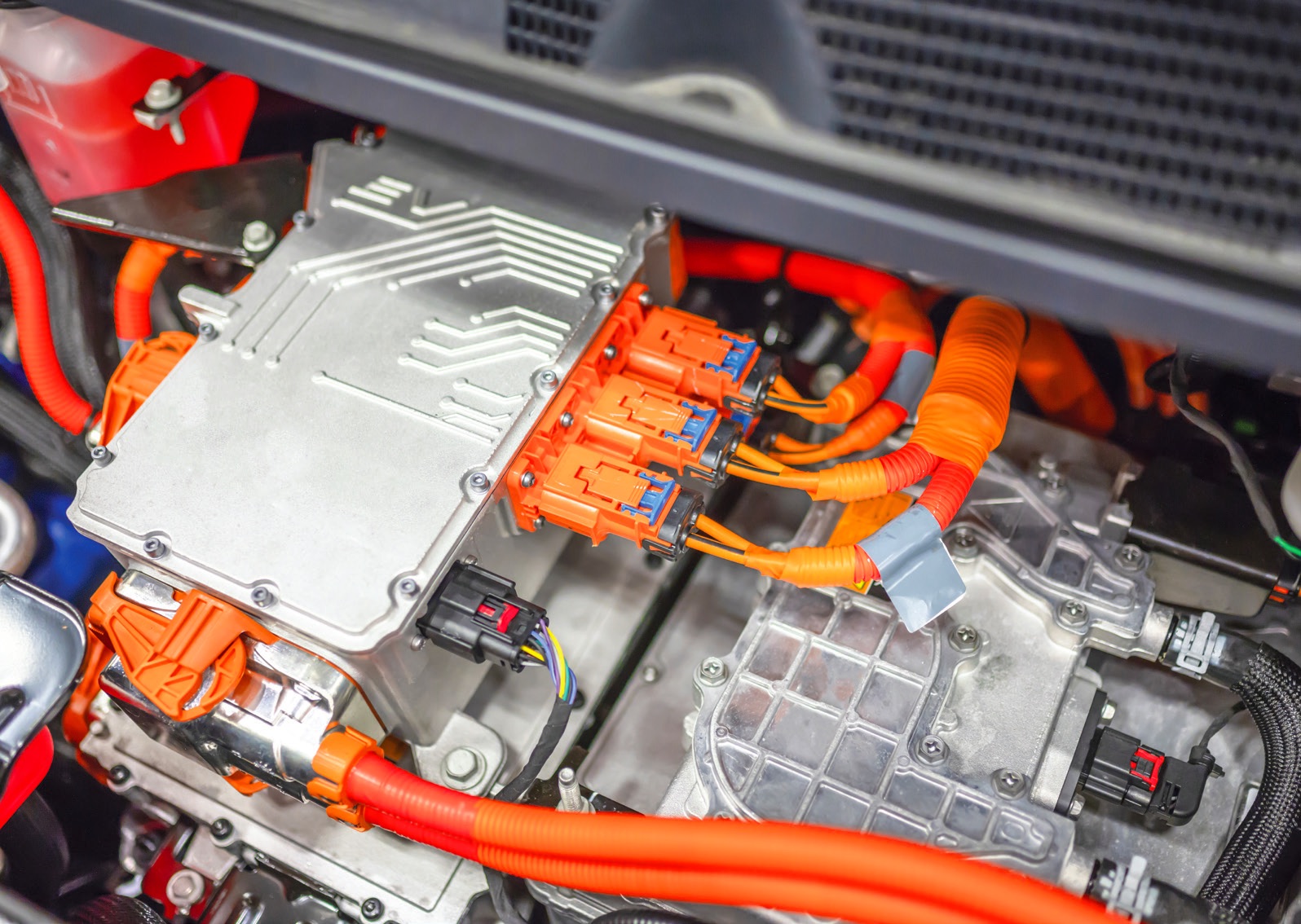
Electrical currents can leak through a rotating stator and exit through a motor casing if a motor is not properly grounded. From there, the current follows the path of least resistance, and that path often goes through the bearings.
STLE member Gareth Fish, technical fellow at the Lubrizol Corp. in Wickliffe, Ohio, explains that liquid lubricants can play a role in protecting bearings because of the flow of fluids where the electric motor feeds into the gearbox. In early EVs, he explains, a seal separated the bearing from the rest of the gearbox. However, in newer EV transmission arrangements, this seal is gone, and the gearbox fluid also lubricates the bearing adjacent to the gear transmission. Using one fluid to lubricate both components solves one problem but may introduce others, he says. For example, the gear fluid might not have the right base oil viscosity or the correct additive combination for electric motor bearing lubrication.
Electrically conductive additives can help optimize the electrical properties of the lubricant, but they also must work well with the rest of the formulation. For example, gold, copper and graphite are highly conductive, but like most solid particulates, they can accelerate wear. Soluble ionic species like metal salts are less conductive, but they don’t promote mechanical wear. However, some metal salts can be highly corrosive. “You can’t just take any old salt and put it in there,” Sarigiannis says. Ionic additives can be expensive, so the initial cost must be balanced against the savings from extending service life and preventing damage.
How big of an issue is lubricant conductivity? “It all depends on the customer,” Sarigiannis says. Some vehicle companies are looking at conductive seals (which can wear down the rotating shaft and drop in conductivity over time). Another option is using brushes that ground the stator to the housing, but these brushes also wear over time, reducing the contact area and the resulting conductivity. “I don’t think there’s going to be one solution that is going to cure everything,” he says. “I think it’s going to have to be a combined solution, looking at conductive seals, improved conductivity, lubricants and then also ways of minimizing this voltage issue that that’s happening with variable speed drives, which has been an issue for years and years.”
Gillet explains that OEMs can adapt motor housing thicknesses and other hardware characteristics to accommodate the resistivity profile of the lubricating fluid. This minimizes the chance of static charge buildup or stray current damage, he says, adding that, in general, EV fluids with higher resistivity should perform better.
Electrically insulating sheaths and housings isolate the components of an electric motor and transmission from the surrounding oil, but electrical contact points and pass-through points are sometimes exposed to the transmission oil, Gahagan says. In addition, insulating materials can become cracked through fatigue, exposing the wires.
Selecting a lubricant formulation for electric motor bearings, Fish says, requires knowing the type of motor being used and whether the motor will be generating stray currents. Transmission oils, being naturally insulating, provide protection against stray currents, but if the resistivity of an oil is too high, static charges can build up and discharge as electrical arcs, damaging or destroying sensitive components.
Different types of motors present different challenges, Fish says. AC induction motors use coils rather than a permanent magnet to create the magnetic field that drives the motor. These motors are very efficient, but they are prone to stray currents building up. Permanent magnet motors vary by features and efficiencies, but some of them can build up charges as well.
“We describe the lubricating oils that we deal with as static-dissipative insulators,” Gahagan says. He notes that acceptable conductivity ranges for EV oils are set by the OEMs. In general, OEMs are either satisfied with the conductivity levels of the oils they are using, or, in some cases, they want the conductivity to be even lower, he says, but still within the static dissipative range.
Chemical compatibility
Because electric motors generate instantaneous torque, they also generate heat rapidly at very low speeds. Lubricants, seals and other nonmetallic components must be able to operate well in these environments, and they must be compatible with each other.
“When you open up an EV gearbox, you will see a lot of insulated metal, but you also will see a surprising amount of plastic,” Gahagan says. Polymer components reduce the weight of the vehicle—they are used in insulators and component housings, but they also are used for support structures, bearing cages and seals. Thus, transmission oils must be compatible with all of the different types of polymer with which it comes into contact, to prevent embrittlement or excessive softening, either of which can cause a part to fail. Many types of chemical reactions contribute to plastic aging, especially at high operating temperatures.
Hydrogen is a major contributor to seal failures. For example, polyalphaolefins (PAOs) can absorb hydrogen out of polymer seals, causing them to harden. Seals, on the other hand, can swell when they pull hydrogen out of ester-based oils. Thus, vehicle manufacturers are looking at hydrogen-free fluorinated elastomer lubricants that work well at high temperatures. Not all fluorinated compounds are appropriate for use as lubricants or seals, however. Some of them pose toxicity and environmental problems. Perfluoroalkyl compounds (PFAs), for example, can bioaccumulate and persist for years in human tissues.
8
One fluorinated compound, perfluoropolyether (PFPE), has been used as an aerospace lubricant for at least 30 years PFPE can operate in the 280-300 C range, but it is very expensive, so it is best used in small amounts and in fill-for-life applications, says Sarigiannis. PFPE is not compatible with fluoropolymer seals (e.g., PTFE), but it can be used with hydrogenated acrylonitrile butadiene rubber (HNBR). HNBR is currently used to make air conditioning seals and hoses; engine seals, grommets and gaskets; fuel system seals and hoses; and various other automotive components.
Copper corrosion
Of all the factors that go into formulating an EV transmission oil, copper compatibility is probably the most critical, Gahagan says. In contrast with metal gears, which can wear gradually over the life of the gearbox, corrosion of copper motor windings or electrical connections can occur rapidly and cause catastrophic failure, he adds, noting that this failure can occur early in the life of the transmission.
Transmission oil compatibility with copper electronic components is “one of the most difficult things to address,” says Gillet. “Fluid additives play a key role in copper compatibility.” Some additive companies have a tendency to rely on proven technologies, he says, but more work is needed to develop EV-specific additives.
Some currently used EV transmission fluids are adaptations of transmission fluids designed for ICE vehicles. Manual transmission fluids, with their higher viscosity and sulfur-containing extreme-pressure (EP) additives, are not suitable for electric vehicles.
9 Adapted versions of automatic transmission fluids (ATF) have been used, but some ATF fluids also contain too much sulfur to work well in an EV. “You really need to work on a dedicated formulation, with new additives and new base oils, to address copper compatibility,” Gillet says.
Standardized tests would help in comparing fluid performance, and more work needs to be done on this as well, Gillet adds. He notes that an ASTM task force is working on copper corrosion testing methods specifically for EV fluids. The current copper strip immersion method, ASTM D130, does not account for the effects of electrical currents passing through copper wires in contact with transmission fluids.
2
Gearbox temperatures can temporarily spike much higher than normal operating temperatures, accelerating corrosion reactions, Gahagan says. Even if copper corrosion does not result in catastrophic failure, the formation of corrosion products (copper oxides, sulfates and other salts) reduces the conductivity of the wire. Heat builds up in these corroded areas, which accelerates the corrosion process still further. Thus, copper compatibility and corrosion inhibition are essential in the formulation of an EV transmission oil (
see Figure 3). An OEM can’t just select an off-the-shelf oil that has worked in the past and expect it to work with a new system, Gahagan says, but the right oil formulation can be very effective at protecting copper components against corrosion.
Figure 3. (a) In-house test setup for wire corrosion testing. (b) Copper strips, half immersed in oil, were left for one week at 80 C. The reference fluid released volatiles that corroded the strip on the left, while the e-fluid protected the strip on the right, even in the vapor space. (c) Printed circuit boards were immersed in oil for 1,000 hours at 150 C, under an applied voltage. The circuit board in the reference fluid corroded, while the e-fluid effectively prevented corrosion on the other circuit board. Figure courtesy of Michael Gahagan, The Lubrizol Corp.
Electrical components don’t have to come into contact with liquid lubricating oils to be affected by them, Gahagan says. Because EV motors run so hot, volatile components of an unsuitable oil lubricant can vaporize and penetrate where the liquid can’t reach. Some corrosion inhibitors are only active in the liquid oil, and not in the vapor phase. Vapor-phase corrosion can be more rapid than in the liquid phase. Thus, lubricant formulators have to guard against vapor-phase corrosion, especially for circuits enclosed in a gearbox where the liquid oil is not able to splash against the circuits and protect them.
Thermal management
The two predominant mechanisms in oil aging are thermal degradation and oxidation, Gahagan says. EV oils must manage heat, which accelerates any type of chemical reaction, including oxidation. For example, a large current draw on an electric motor (during acceleration, for example) can cause the motor coils to heat up to 180 C, which puts added stress on the transmission oil. Using high-quality base oils with good thermal stability, in addition to a good combination of oxidation inhibitors and dispersant additives (which retard sludge formation), can counteract these stresses, he says.
In some EVs, the motor is surrounded by a cooling jacket that uses water or air as a coolant. However, Gillet says, he has seen a trend toward direct cooling designs in which the transmission oil functions both as a lubricant and a coolant for the electric motor (
see Figure 4). This type of direct cooling, which eliminates the need for separate lubricating and thermal management oils,
10 is used on the Tesla and the Chevrolet Bolt (sold as the Opel Ampera-e in Europe until 2020).
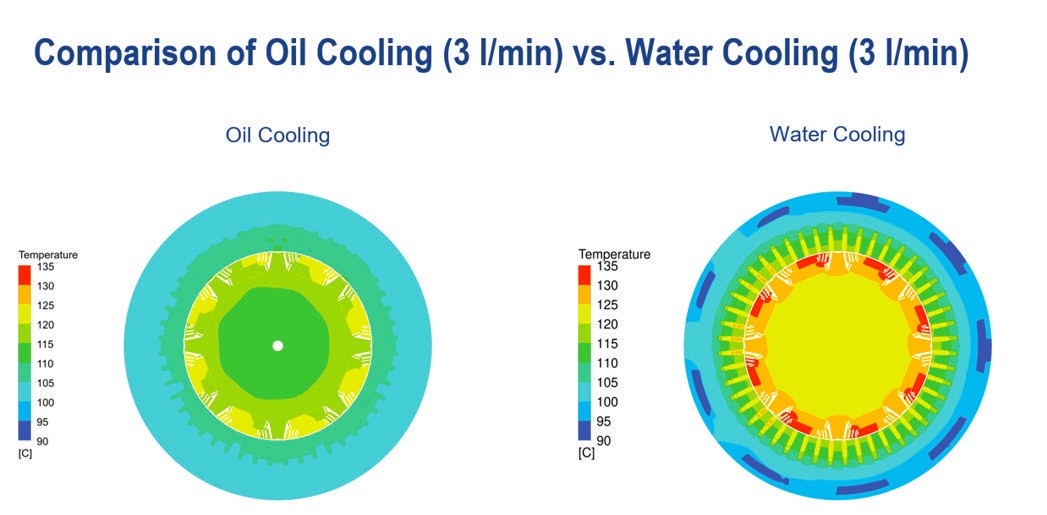
Figure 4. Computer simulation illustrating the cooling capabilities of oil compared with water. Figure courtesy of Thomas Gillet, TotalEnergies.
Gillet notes that thermal management of the battery is emerging as a challenging area for OEMs, and today’s battery cooling fluids require different formulations from motor cooling fluids. One particular challenge is that EV batteries must be maintained within a certain temperature range (warm enough for quick starts but cool enough for optimum performance) in all types of weather, even when the vehicle is not running.
Hot-running systems and reaction with oxygen from the air can cause the oil to gradually become more viscous if the oil is not stable enough. The added drag caused by this increase in viscosity reduces the operating efficiency of the motor, which could reduce the range that a vehicle can be driven between battery charges. High-quality base oils and additives, chosen with thermal stability and corrosion inhibition in mind, help extend the life not only of the oil but of the vehicle itself (
see Water-Based Lubricants).
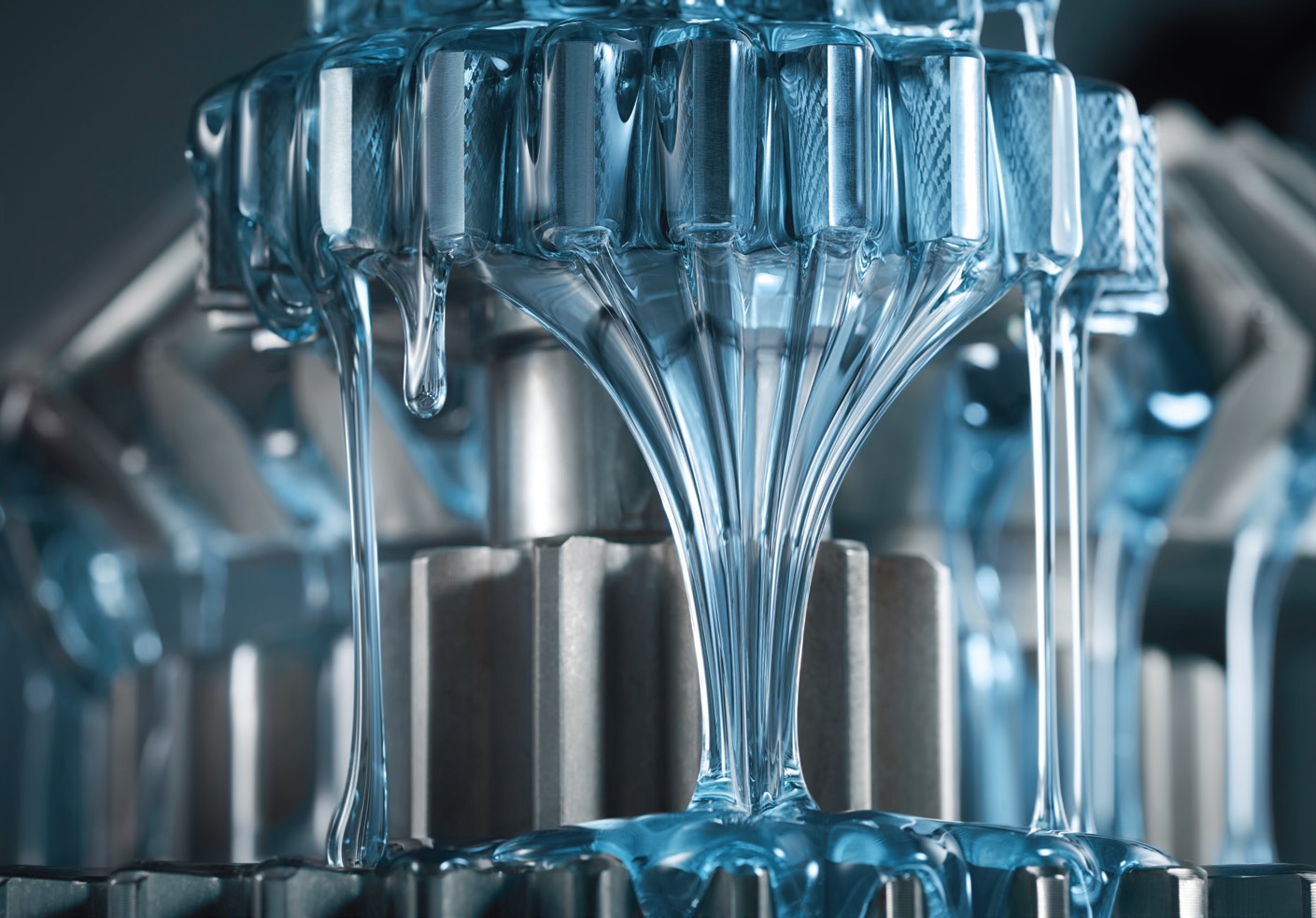
Water, used as a functional constituent of emulsion-based lubricants, is an effective coolant, and it undergoes little to no shear thinning. Photo courtesy of Klüber Lubrication NA LP.
Water-based lubricants
Unlike hydrocarbons, water is a good electrical conductor (unless it’s been highly purified, but that’s another story). Of course, a saltwater lubricant would not only be ineffective at keeping solid surfaces separated, but it also would be highly corrosive to metal parts and could degrade some types of seals and gaskets, says Sarigiannis.
Emulsions of oil and water, however, can be highly effective. Even though emulsion lubricants is an emerging field, some of these lubricants are already on the market for specific applications.
A Water has the added advantage of being a good coolant—an important feature in electric vehicle motors, which can generate large amounts of heat. The ratio of water to base oil in water-based lubricants depends on the viscosity required to produce and maintain elastohydrodynamic (EHD) separation at the loads and speeds of a particular application.
Unlike oils, which consist of long, entangled chain molecules, liquid water is a disordered three-dimensional network of three-atom molecules connected by hydrogen bonds. High load-bearing operations shear oils over time, and this effect is especially pronounced for line-contact bearings (e.g., taper, spherical, needle and cylindrical roller bearings), in which the rolling elements have a greater contact area with the raceways than for ball bearings. In contrast, water experiences little to no shear thinning.
Getting the oil–water balance just right involves not only viscosity, lubricity and shear resistance but also optimized conductivity and cooling properties. This field is still very much in a developmental phase, says Sarigiannis, and companies are reluctant to disclose specific information on their formulations.
A. Klüber Lubrication, “Hydro lubricants – more efficiency with lubricants containing water as a functional component.” Available here.
Just as concerning, Gahagan says, is sludge formation. In an EV gearbox, much like in a conventional gearbox, sludge accumulates in the sump of the vehicle transmission. However, electric motors are more sensitive to sludge that remains in circulation. Sludge deposits on motor components act as an insulator that interferes with heat dissipation, causing the motor to run hotter than is ideal. Some types of sludge also can be corrosive, he adds.
“Anything that consumes energy will reduce the range of the vehicle,” Fish says, adding that the electric motor and cooling circuits represent the most drastic changes from ICE vehicle systems. One energy-consuming necessity is a system to keep the batteries at an optimum temperature—cool enough to avoid failure but hot enough to keep the battery running. The temperature control system operates even when the car is not in use, Fish says—this prevents damage to the battery during hot weather and helps with quick starts during cold weather. Some EV designers use the motor casing as a fluid-cooled jacket, while others immerse the motor in fluid.
Thermal cooling fluids are still being investigated, Fish says. He notes that in one EV, transmission fluid was being used in the differential, but that’s not necessarily recommended for that application. Some vehicle makers don’t have their own standards for fluids, he says. Instead, they rely on the suppliers of the various components to set standards. “But it’s by no means finalized.”
Surviving the EV “Cambrian explosion”
Radical changes in vehicle designs and usage patterns have shaken up the vehicle lubricants and thermal fluids markets. Formulations that survive and thrive will be those that perform well under high temperatures, last for the life of the part and coexist compatibly with the hardware components they assist and protect.
REFERENCES
1.
Singh, A. (April 2020), “Electric vehicle market by type: Global opportunity analysis and industry forecast, 2020–2027,” Allied Market Research report A02073. Available
here.
2.
McCoy, B. (2021), “Next generation driveline lubricants for electrified vehicles,” TLT,
77 (3), pp. 38-40. Available
here.
3.
TotalEnergies Advertorial (Jan. 11, 2019), “Lubricating Electronic Vehicles, CNBC.” Available
here.
4.
European Commission, “Novel coolants for enhanced thermal performance in electric vehicle immersion cooling systems,” CORDIS project H2020-EU.1.2.1. - FET Open. Available
here.
5.
Lubricant World (Nov. 10, 2020), “TOTAL pioneers the electric vehicle fluids market with its EV Fluids product series.” Available
here.
6.
SwRI press release (April 14, 2021), “SwRI launches consortium on advanced fluids for electrified vehicles.” Available
here.
7.
Fuels and Lubes (Nov. 10, 2020), “Electric vehicle fluids: Off-the-shelf or brand new additive chemistries?” Available
here.
8.
Environmental Pollution Centers (Feb. 21, 2018), “What are PFOA and PFOs and how dangerous are they?” Available
here.
9.
Wolf Lubricants, “The basics of lubricants: The guide to understanding transmission fluids/gear oil.” Available
here.
10.
Singh, S. (Sept. 2, 2020), “Future of automotive lubricants, can E-fluids be far behind?” Forbes. Available
here.
Nancy McGuire is a freelance writer based in Silver Spring, Md. You can contact her at nmcguire@wordchemist.com.