Fabricating fertilizers by force
Drs. Wilfred T. Tysoe & Nicholas D. Spencer | TLT Cutting Edge June 2021
Ball-milling nitrogen in the presence of iron powder breaks the strong N2 bond, enabling it to react with hydrogen to make ammonia.
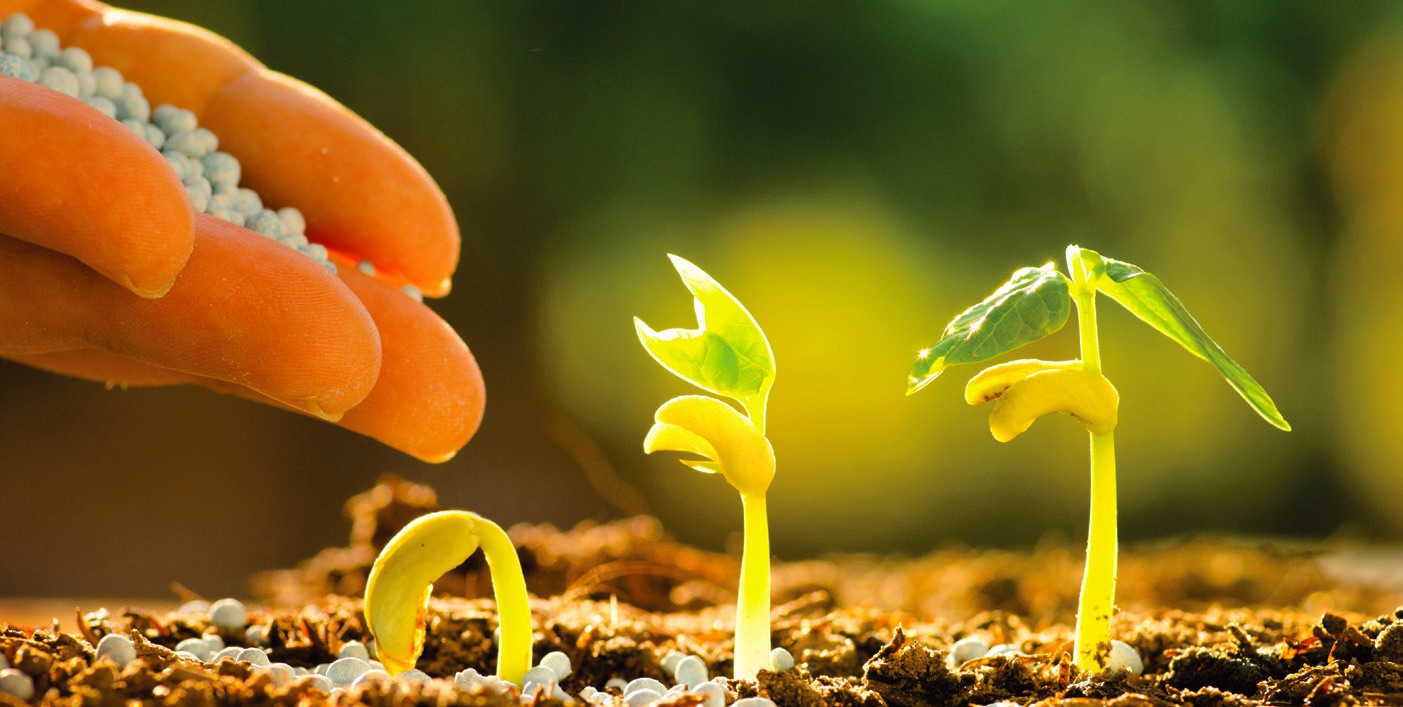
Previous Cutting Edge articles have discussed how the surface region of copper could be restructured by sliding,
1 thereby creating defect sites to accommodate the restructuring and reducing the copper coordination number—the number of other atoms to which each atom is bound in the metal. Some years ago, one of the co-authors of this article demonstrated that the rate of iron-catalyzed ammonia synthesis by a reaction between nitrogen and hydrogen, the Haber-Bosch process, depended on the coordination number of the iron atoms on the surface of the catalyst.
2
The synthesis of ammonia is arguably the most important catalytic reaction ever discovered. It allowed the use of natural fertilizers to be augmented or replaced so that now approximately half of the world’s population depends on fertilizers made using the Haber-Bosch process. Much of the world would starve without it.
However, the conditions needed to break the strong chemical bond in nitrogen are harsh—temperatures from 400 to 500 C and pressures up to 100 atmospheres. When the process was discovered in 1909, there were justifiable concerns that the plant might explode.
Figure 1. The ammonia synthesis cycles can be divided into two steps: nitrogen dissociation and hydrogenation. The active defects on the surface of the activated iron, created by repeated collisions, facilitate nitrogen dissociation. In the hydrogenation step, the impact produces additional energy, which facilitates the reaction of strongly adsorbed NHx (x = 0–2) intermediates. Published with permission from Ref. 3.
In order to overcome these limitations, a large group of experimentalists and theorists consisting of Gao-Feng Han, Feng Li, Seok-Jin Kim, Hyuk-Jun Noh and Jong-Beom Baek from the Ulsan National ORGInstitute of Science and Technology, Korea; with Zhi-Wen Chen and Qing Jiang from Jilin University, China; Claude Coppex and Samira Siahrostami from the University of Calgary, Canada; with Zhengping Fu and Yalin Lu of the University of Science and Technology of China; and Chandra Veer Singh from the University of Toronto, Toronto, Ontario, Canada, collaborated to investigate if the mechanical creation of low-coordination sites on iron, the conventional material used to catalyze the synthesis of ammonia, would enable the reaction to be carried out under milder conditions. The reaction was carried out in a ball mill, in which steel balls were rotated in a container containing iron powder. As illustrated in Figure 1, when the ball mill is pressurized by nitrogen, the large forces generated as the balls collide create sufficient defects to induce nitrogen dissociation. The amount of nitrogen absorbed by the iron initially increases with rotation speed, as expected, but then starts to decrease as the temperature becomes too high (
see Figure 2(a)).
Quite remarkably, ammonia is generated in a second step in which the nitrogen-containing iron is ball-milled in hydrogen, where the total ammonia yield increases with hydrogen pressure (
see Figure 2(b)) and can produce ammonia concentrations that exceed those in the industrial process.
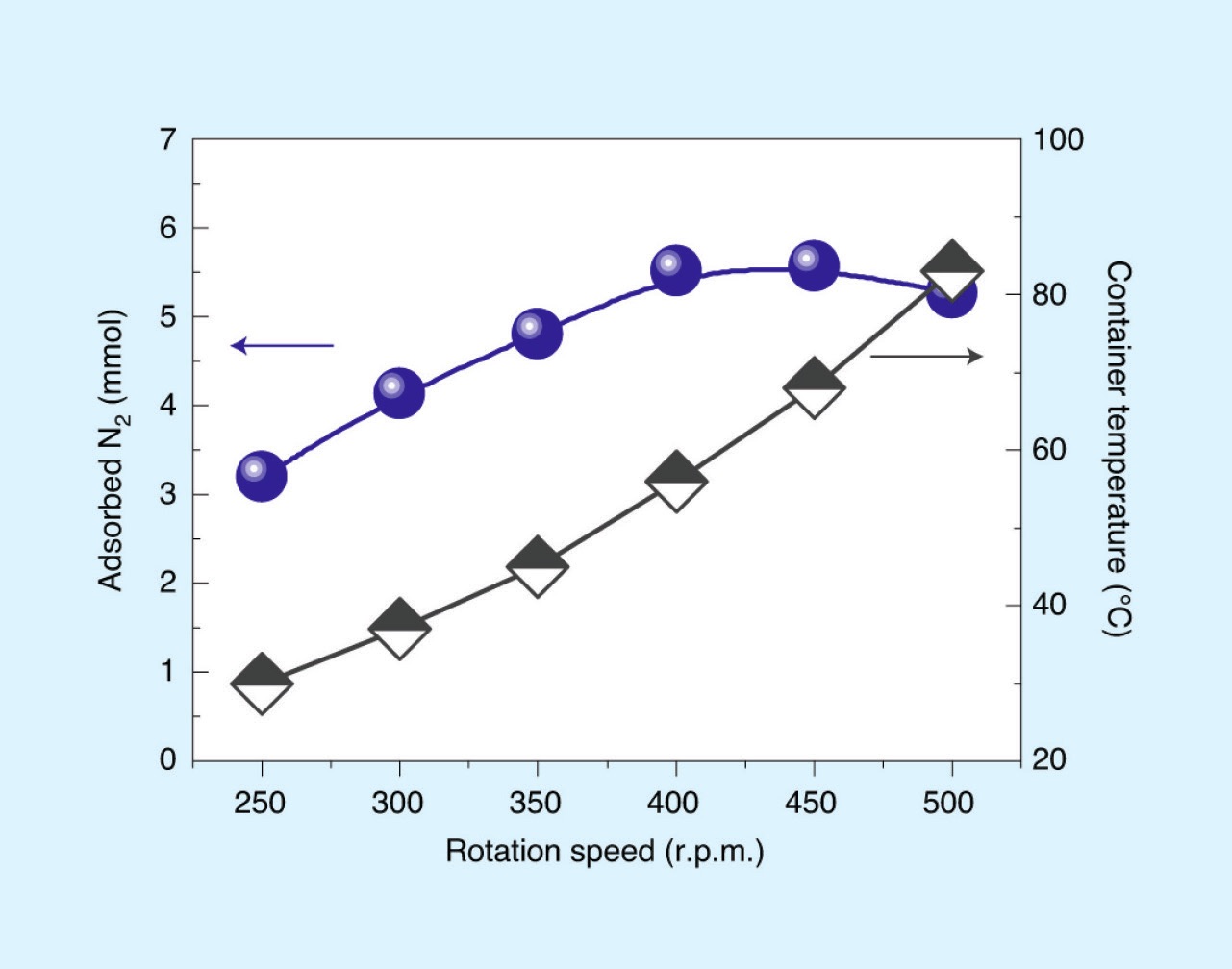
Figure 2. (a.) The amount of adsorbed N2 and the container temperature are functions of the rotation speed. The nitrogen-containing iron powder, Fe(N*), was prepared by ball-milling in N2 (9 bar) at a rotational speed of 400 rpm for 37.5 h. (b.) The ammonia was obtained by hydrogenating the as-prepared Fe(N*) at a rotational speed of 500 rpm for 4 h. The graph shows NH3 concentration and NH3 yield as a function of the initial hydrogen pressure. Published with permission from Ref 3.
The authors comment that the mechanical process is more efficient than the Haber-Bosch process at the laboratory scale. However, perhaps the most important advantage of this tribological approach is that it is much simpler technology than the commercial plants so that it could provide a straightforward and elegant method for making fertilizers in the developing world.
FOR FURTHER READING
1.
Tysoe, W.T. and Spencer, N.D. (2015), “Into the fold,” TLT,
71 (4), pg. 72.
2.
Spencer, N.D., Schoonmaker, R.C. and Somorjai, G.A. (1981), “Structure sensitivity in the iron single-crystal catalysed synthesis of ammonia,”
Nature, 294, pp. 643-644.
3.
Han, G.-F., Li, F., Chen, Z-W., Coppex, C., Kim, S.-J., Noh, H.-J., Fu, Z., Lu, Y., Singh, C.V, Siahrostami, S., Jiang, Q. and Baek, J.-B. (2021), “Mechanochemistry for ammonia synthesis under mild conditions,”
Nature Nanotechnology, 16, pp. 325-330.
Eddy Tysoe is a distinguished professor of physical chemistry at the University of Wisconsin-Milwaukee. You can reach him at wtt@uwm.edu.
Nic Spencer is professor of surface science and technology at the ETH Zurich, Switzerland, and editor-in-chief of STLE-affiliated Tribology Letters journal. You can reach him at nspencer@ethz.ch.