Culture change
Evan Zabawski | TLT From the Editor May 2021
Out with the old, in with the new.
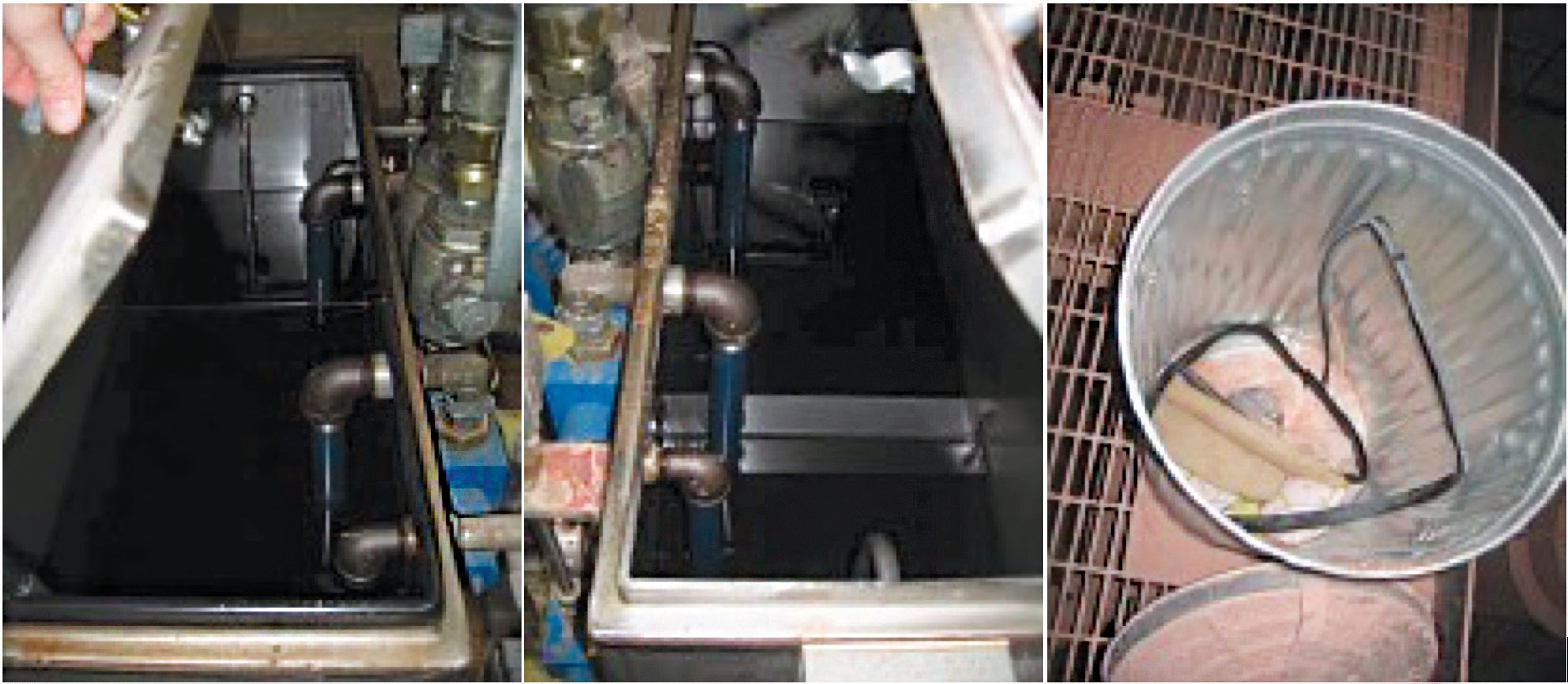
Tank with seal (left), tank without seal (middle) and discarded seal (right).
How can I improve my lubrication program? This is a question I have been asked many times over the years, and one that has an answer that is much more easily said than done.
One of my more memorable occurrences of this question was in relation to a potash mining and milling facility I audited. The presumption was that the audit would review their lubrication practices and make some recommendations for the construction of a new lubricant storage room. It was stipulated that they had a very large budget for this project, so they were eager to ensure my recommendations met the requirements of a “world-class” lube storage room.
Shortly after my arrival, I was ushered toward the existing storage room located in the building where the mined potash was milled—a room they admittedly knew had some obvious shortcomings. The path I walked to get there was absolutely covered in fine potash dust, sometimes deeper than the toes of my boots. When the lube room door was opened, I was pleasantly surprised to see it was relatively dust-free, but my eyes soon spotted some stalactites hanging from the ceiling, directly above the drums of new synthetic oil!
The “salt-cicles,” as I dubbed them, were being formed due to water and potash dust mixing, which then seeped through the floor above. The source of the potash dust was no mystery, but a trip upstairs showed the water came from hoses aimed directly on some overheated bearings and onto the floor.
Other deficiencies were noted in the lube room, including an absence of tank lid seals on the hydraulic return tanks (daylight could be seen between lid and top of tank) and an absence of dust caps on the vertically mounted quick-connects for filling the compactor lube systems. The compactor lube skids revealed a greater, underlying issue though.
One compactor’s reservoir lid had an intact seal, but the other compactor’s seal was missing, yet by a stroke of luck it was spotted in a nearby trash can. Whoever had recently serviced both units had thrown it away, even though it showed no defects once it was reinstalled. Over the next few days, I continued to observe signs of this near-malicious behavior as I shadowed various members of the lubrication team about their daily work.
On the last day of the audit, I sat down with the reliability supervisor for a wrap-up meeting. He asked me what I thought their biggest issue was, and I think he was expecting me to say the lube room, judging by the surprised look when I said it was his lube team. I detailed how I witnessed them perform several oil changes and how they seemed to have next to no regard for oil cleanliness, as it was being transported from the lube room to the machine (in open containers) or when added to the machine (with dirty funnels).
Given that airborne contamination was inherently their biggest concern, I pointed out that though the effort to minimize contamination begins in the lube room, it does not end until the oil is in the machine, and that handling a lubricant exposes it to more opportunities for contamination than storage does. I emphasized that a “world-class” lube room alone would not necessarily result in cleaner oil in their equipment.
The discussion turned toward the attitude of the lube team. If they were willing to discard a perfectly good seal instead of resetting it, or use an obviously dirty transfer container or funnel, what they really needed was a culture change and not a new lube room. This kind of change does not come quickly or easily by way of a mandate from management—it comes from a concerted effort to break old habits and instill new ones using proper tools or techniques by providing training and support.
This facility started using filter carts to handle some of their oil, and they achieved a full payback within one year simply due to extended oil drain intervals—not including all the downtime and labor saved. The shifting of culture became apparent when the lube team asked for more filter carts!
Evan Zabawski, CLS, is the senior technical advisor for TestOil in Calgary, Alberta, Canada. You can reach him at ezabawski@testoil.com.