Blame the lube—that was easy!
Paul Hetherington | TLT President's Report March 2021
Failures are due to hundreds of different reasons—be sure to find the root cause.
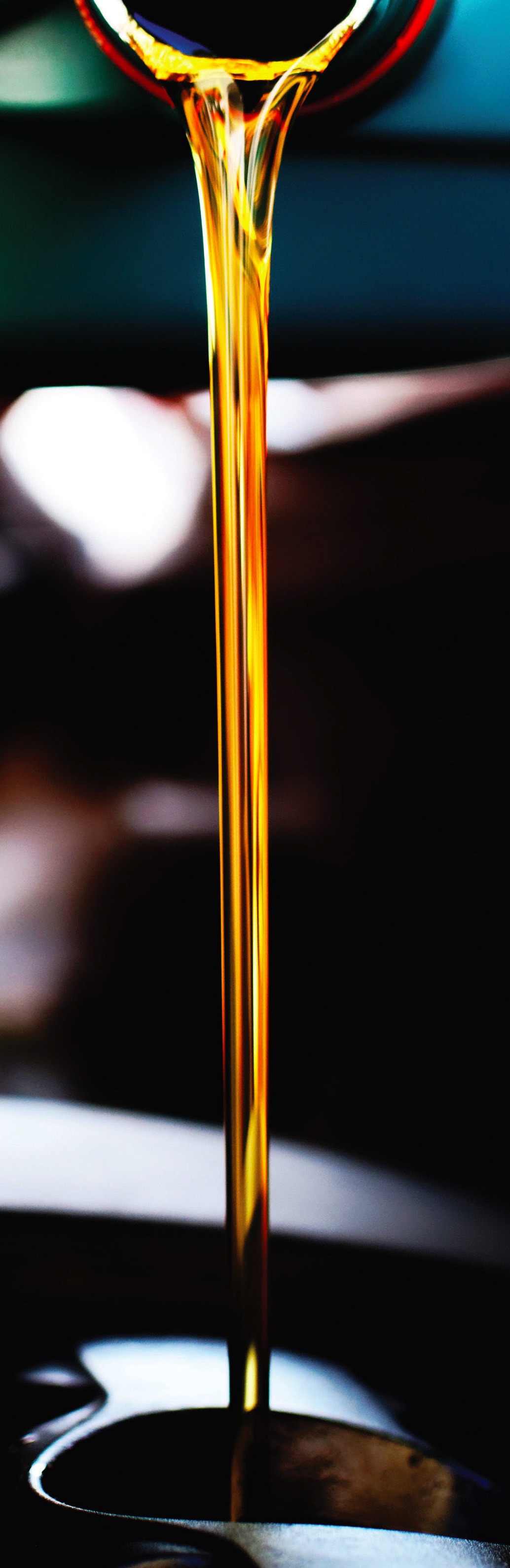
Lubricants don’t make mistakes. Never have. Never will.
I have always been amazed throughout my approximately 40-year career by the number of times I have heard someone say, “It’s the lube’s fault.” Yikes, talk about hitting the easy button and moving on to the next issue. But if there is one thing I have learned—and this truly is no major revelation—it’s that lubricants don’t make mistakes. Near as I can figure, never have and never will.
So why is it that some people are so quick to blame the lubricant? I guess the simplest answer is that it is just easier than trying to determine the true overall root cause of a failure. Unfortunately, I am aware of countless times where the initial reaction to a failure is the immediate change to a different lubricant. Quite often the next lubricant selected is an arbitrary guess by someone in the organization.
The truth is that a failure could be due to hundreds of different reasons ranging from, but definitely not limited to, viscosity (high or low), wrong or insufficient additives, wrong base oil for application, contamination (water, dirt or other foreign matter, or cross contamination of another product), too much or too little lube, inherent design issues, etc. The list could go on for the rest of this article.
The other unusual thing I see quite often in published failure analysis reports is the somewhat helpless statement that the failure was due to “lack of lubrication.” So, what does that mean, and how is that finding supposed to help the equipment owner? Truth is, it doesn’t.
In a simple view, lack of lubrication to me just says there was either no lubricant or not enough lubricant. In an application where the bearings are submerged in an oil bath, there is definitely no lack of lubrication. But, more specifically, it may mean that the existing lubricant is not appropriate for the application and/or its present condition (and the laundry list of possible reasons why) was not providing adequate lubrication to the components.
I realize that in some cases those who evaluate a set of failed parts (i.e., bearings) might be doing so far removed from the actual component and failure location. The failure mechanism on the bearings might clearly indicate the lack of adequate lubrication leading to inappropriate lubricant film (i.e., viscosity) and/or wear protection (EP or AW additives) subsequently leading to excessive overheating and spalling, etc. Remember, the viscosity issue might have nothing to do with it being the right lubricant per se in the system but, rather, some other contamination like water that is disrupting the lubricant film.
The key point is, don’t blame the lubricant. Rather, make sure you determine the true root cause. Once you’ve determined that, make the appropriate adjustments to maximize long-term reliability of the components and system.
Paul Hetherington is manager technical services for Petro-Canada Lubricants in Peachland, British Columbia, Canada. You can reach him at paul.hetherington@hollyfrontier.com.