Worker health and safety
Don Smolenski, Contributing Editor | TLT Machinery October 2020
It’s important to evaluate these issues on a regular basis.
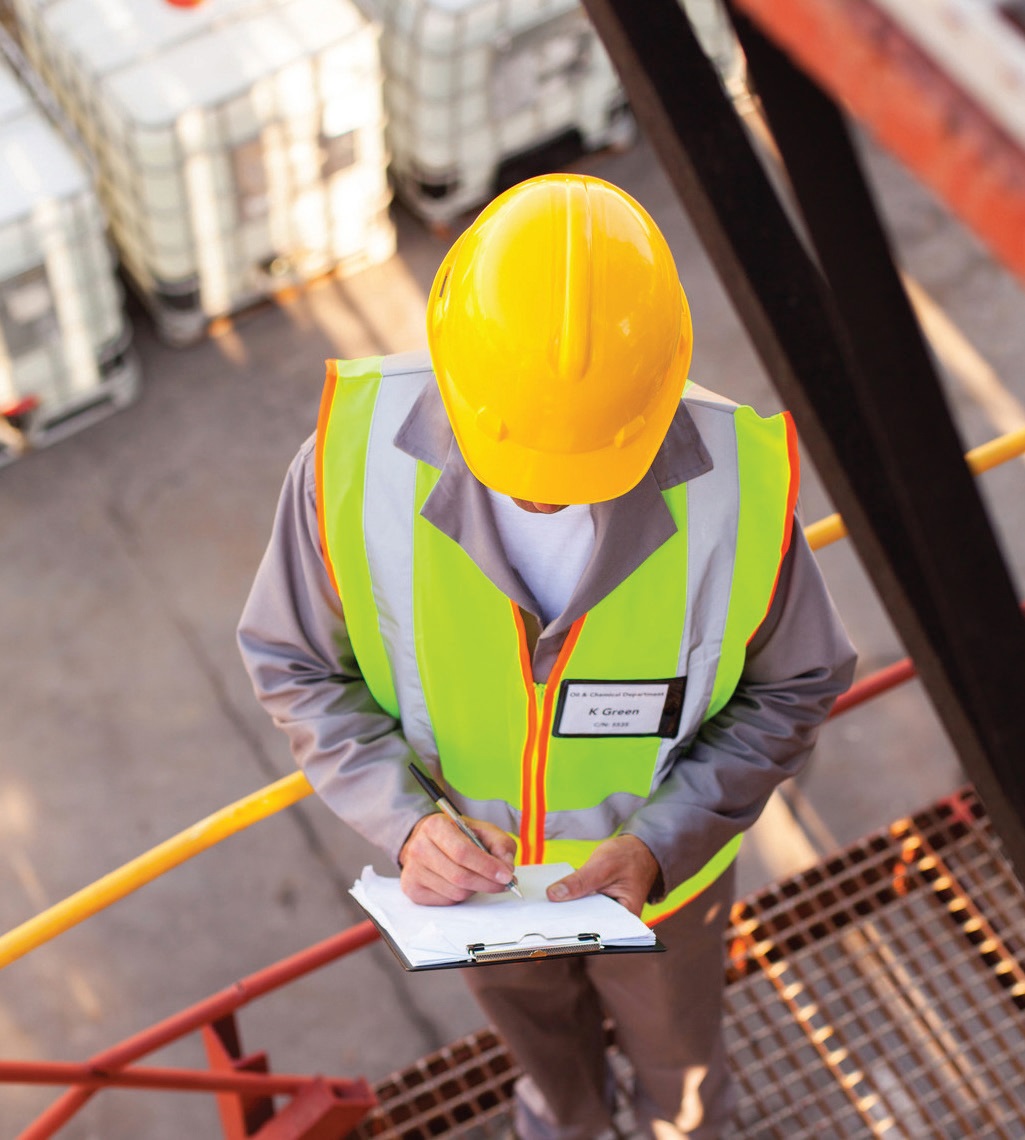
Continuous formulation changes, better fluid maintenance, elimination of stagnant areas and more fresh air all help to reduce the potential for health issues in workers.
With COVID-19 front and center, it seemed like a good time for a column on worker health and safety. Health and safety issues have existed in manufacturing plants for a long time, and there have been continuous efforts to eliminate or minimize them. Many times, fixes for the safety issues are pretty straightforward, such as locking out equipment that poses a crush, electrocution or other hazard before performing maintenance on it, using a harness to reduce the risk of falling, etc. But causes of health issues related to chemical exposure might require detective work.
Many years ago, “mule spinners,” who operated machines that spin cotton or other fibers, were found to have a high incidence of cancer. This was due to exposure of poorly refined oils, likely containing high concentrations of polycyclic aromatic hydrocarbons (PAHs), which are known or suspected carcinogens. This was an early example of health issues in workers caused by exposure to chemicals.
Many types of cancer, including leukemia, lung, skin, digestive, pancreatic, esophageal, stomach, liver and others, have been found in workers exposed to metalworking fluids (MWFs). The data is often equivocal, with white and Black people, for instance, exhibiting different propensities. PAHs are present in crude oil and base oils that are not severely refined, such as acid clay refined base oils. These were common decades ago but were largely phased out by the mid-1970s. Solvent refining and severe hydrotreating have minimized concentrations of these chemicals in base oils.
However, MWF additives, such as long-chain aliphatic hydrocarbons, sulfur-containing compounds, formaldehyde-releasing biocides and nitrites (not themselves carcinogenic but can form nitrosamines during use) can be of concern. Continuous formulation changes, better fluid maintenance (tramp oils, metal fines and dirt can all be problematic), elimination of stagnant areas in the metalworking system, enclosures of machining operations, local exhaust and more fresh air all helped to reduce the potential for cancer.
Several years ago, workers exposed to MWF mist had a relatively high incidence of allergic respiratory issues, subsequently diagnosed as hypersensitivity pneumonitis (HP). HP is caused by a wide range of antigens, including bacteria. Variability in the symptoms exhibited and the similarity of HP to other respiratory diseases sometimes caused missed diagnoses. Mycobacterium immunogenum (MI), a gram-positive bacterium, were likely causative, with endotoxins released by MI specifically implicated. The tendency of MI to form biofilms made treatment with conventional biocides more difficult. Ultimately, both engineering controls and MWF formulation changes to reduce mist concentrations were found to be helpful. In fact, the OSHA limit for oil mist concentration was lowered to a maximum of 5 mg/m
3, and in many plants was 1 mg/m
3 or less.
Skin irritation, ostensibly allergic contact dermatitis, also has been a common complaint of machinists exposed to MWFs and is thought to be due to ingredients such as formaldehyde-releasing biocides, ethanolamines and other biocides. Mineral oils used in MWFs have been known to cause skin irritation as well. The use of gloves, barrier creams and reducing irritants in the fluids were found to bring relief in many cases. It is not surprising that many of the changes implemented to reduce HP also had a beneficial effect on dermatitis.
The lesson in all of this is that we need to have a continued focus on incremental improvements in health and safety—we can never be too safe or too healthy!
FOR FURTHER READING
Li, K., Aghazadeh, F., Hatipkarasulu, S. and Ray, T.G. (2003), “Health risks from exposure to metal-working fluids in machining and grinding operations,”
International Journal of Occupational Safety and Ergonomics, 9 (1), pp. 75-95.
Don Smolenski is president of his own consultancy, Strategic Management of Oil, LLC, in St. Clair Shores, Mich. You can reach him at donald.smolenski@gmail.com.