The additives equation
Mary Beckman, Contributing Editor | TLT Additives September 2020
Biobased oil stocks serve up different chemical qualities than mineral oil base stocks.
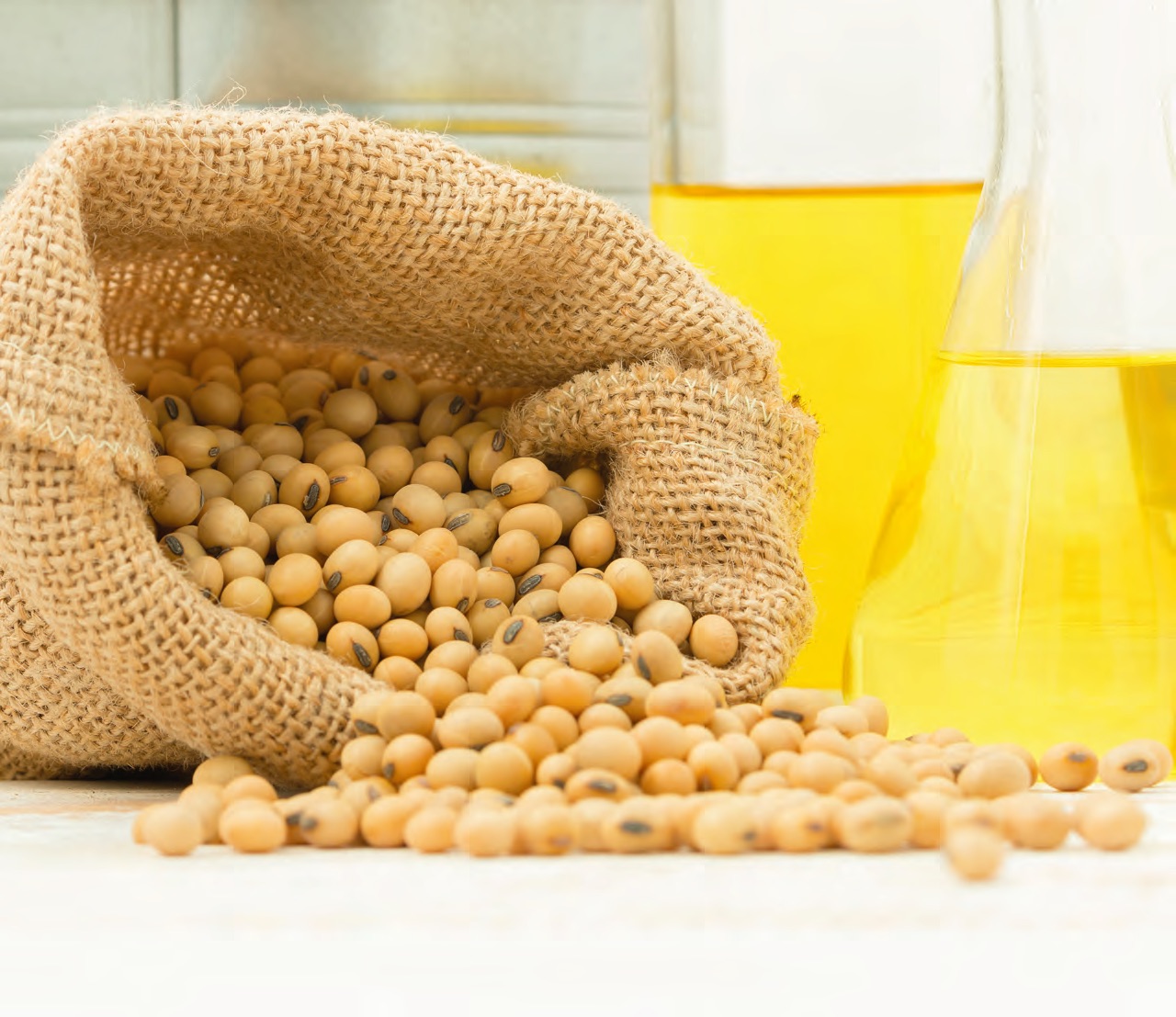
KEY CONCEPTS
•
The polarity of plant-based oils improves their ability to reduce friction on surfaces.
•
The chemical structure of additives affects how they perform in polar and nonpolar base stocks.
•
Heat-treating plant-based oils makes their molecules longer and improves their viscosity.
For the lubricant industry, going renewable means researchers and engineers have to find new sources for base stocks that make up oils and greases. But making something last for the life of your vehicle or farm implement out of something that is inherently biodegradable is a tricky problem.
Part of the issue is characterizing biologically derived base stocks. Lubrication engineers have been working with petroleum products for over a century, but plant-based oils haven’t been given as much attention by modern science.
And then there are additives. Formulating oils and greases requires an understanding of the chemical qualities of everything that goes into the mix and how those chemicals interact.
“It’s something people have to pay attention to,” says STLE-member Ted McClure, technical resources manager, for Sea-Land Chemical Company and SLC Testing Services in Westlake, Ohio. “Even between additives, because it’s usually not just one additive—it’s a coordinated group of additives in a base stock.”
Within the last 15 years or so, more chemists have been testing and characterizing biobased oils, especially soybean oil. One of the hardest problems to overcome is the ease with which biobased oils oxidize, a process that leads to breakdown and becoming thick and rancid. They’ve also explored soybean oil’s structure, how it gets along with additives and even how to modify the oil itself.
Polar express
Because a biobased oil, such as soybean oil, normally functions in a living world of water, its chemical structure is different from mineral oils, which reside inertly in rock. Polar molecules are a little bit positively charged on one end and a little bit negatively charged on the other, which gives them particular characteristics. Soybean oil is polar while mineral oil is not.
Additives have various chemical structures as well, and they might interact with polar and nonpolar base oils differently.
To explore these interactions, STLE-member Girma Biresaw, a research chemist, for the U.S. Department of Agriculture (USDA) in Peoria, Ill., S. J. Asadauskas and McClure examined two base stocks and two additives to see how the mix of chemical structures influences the performance of the modified oil under extreme pressure conditions.
1
The researchers mixed and matched nonpolar paraffinic oil 150N, the more polar soybean oil, and two extreme pressure additives, a commercially available polysulfide or a biobased polyester. Then they subjected the oils to a four-ball friction and wear test and a twist compression test. In the four-ball test, one metal ball sits atop three stationary balls bathed in the lubricant. The test puts force on the top ball and rotates it. The torque of the rotation provides the coefficient of friction, and the scar from the twisting ball provides standard wear information. The twist compression test works similarly except a cylinder sitting atop a flat workpiece replaces the top ball and three lower balls. Comparing test results between oils allows the researchers to see which combinations reduce friction and wear under extreme pressure conditions, when the oils form a very small boundary layer of lubricant.
First, the team compared the base oils themselves. Torque rises and falls over time in the test, and soybean oil had a lower and later peak in torque compared to 150N, showing that the setup with soybean oil exhibited lower friction than the mineral oil. This suggested that soybean oil’s polar molecules can adsorb onto the surface to reduce friction. Mineral oil’s lack of polarity gives it no such advantage.
Five percent polyester added to 150N oil reduced both the amount of peak torque and friction, but it had no effect when added to soybean oil. The soybean oil result was not surprising—since it is already chock full of esters, adding more doesn’t help. But the nonpolar 150N benefitted greatly from the added esters.
When the team added 5% polysulfide to the base stocks, both 150N and soybean oil became much better lubricants—it cut both torque and friction. But adding even more polysulfide didn’t improve matters. The team concluded that once there was enough polysulfide to coat the surfaces, more wouldn’t help.
Finally, the team looked at a measurement called the weld point. In the four-ball test, enough load will eventually weld the top ball to the lower balls. Higher weld points mean better protection by the additives.
Both additives yielded higher weld points in either base stock. Polysulfide resulted in two to four times higher weld point than the polyester additive in 150N oil. In soybean oil, polysulfide had better performance than polyester. The results confirmed previous expectations.
The additives’ overall improvement of the base oils depended on the base oil’s chemical structure. For example, polyester improved performance of mineral oil more than soybean, and polysulfide performed better in soybean oil than mineral oil. This might be because polysulfide is more reactive with steel than polyester and will be more able to improve the performance of polar soybean oil than polyester. Additive interactions with base oils and the surfaces lubricated should be considered as formulators develop biobased oils.
Additives adding up to more
Another USDA study focused on the oxidation problem and found some synergy. STLE-member B.K. Sharma, now at the Illinois Sustainable Technology Center, University of Illinois at Urbana-Champaign, and colleagues tested a variety of antioxidants in soybean oil, alone and in combinations.
2 They used two pressurized differential scanning calorimeter (PDSC) tests. One heats up the oil and additives and takes the temperature of the mixture when oxidation starts, which gives off a burst of additional heat due to oxidation’s exothermic nature. The other test heats up the oil to a set temperature and keeps it there until, again, a burst of exothermic heat indicates oxidation has begun. The “onset of oxidation” temperature from the first test and the “oxidation induction time” from the second can be compared across formulations. Higher is better.
They compared four different antioxidant additives and three different antiwear additives for how well they preserved the oil. The antioxidants can do their jobs in several ways, such as by scavenging free radicals, unstable molecules that bounce around and damage other molecules, or by sacrificing themselves to convert dangerous hydrogen peroxide to water and oxygen, stopping it in its tracks. These different means to the same end might allow antioxidants to work more effectively together than alone.
First the bad news. The researchers found that, when combined with antioxidant butylated hydroxytoluene, two of the antiwear additives were actually making oxidation worse.
Now the good news. The third antiwear additive, antimony dialkyldithiocarbamate (ADDC), reduced oxidation in the soybean oil. All four antioxidants also worked as advertised. But when researchers matched three of the antioxidants with ADDC, the results were synergistic. This meant that when they worked together, the effect was more than the sum of its parts.
The team explored one other aspect of the additives—the base oil stock. When they used the additives in soybean oil that contained larger amounts of oleic acid, the additives provided more antioxidant activity. The onset of oxidation temperature surpassed 250 C, suggesting manipulating the saturation content of base stocks would be another way to increase the oxidation stability of biobased oils.
Heating up for gear oil
Treating the base oil itself before adding modifiers is a method a group used in a publication in 2013. Researchers led by Kenneth Doll at USDA in Peoria developed a soybean oil-based gear oil and compared its performance to commercially available gear oils.
3 They performed a series of tests to determine the final mix of their bio-base stock, which they called bio-GO.
First, since regular soybean oil does not have the viscosity for an application involving gears, they heated up the oil in such a way as to make longer molecular chains within the oil, a process called thermal polymerization.
4 The treatment resulted in a base stock called thermally polymerized soybean oil (TP-SO) that would have qualified as an SAE Viscosity Grade of 190.
Of course, then it wasn’t going to flow well at low temperatures. The first chemicals they tested for their formulation were proprietary pour-point depressants. They chose one that allowed the oil to pour at -15 C rather than its beginning point of -9 C. Because the USDA requires biobased oils to be at least 58% renewable to be certified, the team tested the addition of synthetic oils as well on the pour point. Based on the results, their final formulation would have 30.5% by weight of the Group V synthetic aromatic ester base oil.
One of the biggest problems with vegetable oils is oxidation. To find a suitable additive, they tested TP-SO with nine different antioxidants. They used a PDSC to measure the “onset of oxidation temperature.” Based on the results, they chose two antioxidants to add to their base stock.
“Of course, an industrial lubricant needs to do one thing well, and that is lubricate,” the researchers wrote. “This is an especially important factor in gear oil applications.”
To make sure their formulation would grease the gears, they evaluated several antiwear additives in TP-SO using a fourball friction and wear test.
They found that a boron ester antiwear additive combined with a compound called ZDDP created the smallest wear scar. The scar was so small compared to the base stock TP-SO that the two additives might be working synergistically.
Having come up with a formulation for bio-GO, the team put it up against five commercial gear oils. Bio-GO had the second to highest viscosity index of the oils and created the second-smallest scar in the four-ball wear test. Although it performed admirably in those tests, it began to oxidize at the lowest temperature of the set. The commercial oils hit at least 269 C before oxidizing, whereas bio-GO became unstable at 220 C.
Overall, the researchers were encouraged that thermal polymerization could produce a biobased gear oil that held its own in bench tests.
Just like with the gear oil, exploring ways to balance the biodegradability and renewability of bio-base stocks with the need for a long stable life is a problem for which scientists, increasingly, are holding their own.
REFERENCES
1. Biresaw, G., Asadauskas, S.J. and McClure, T.G. (2012), “Polysulfide and biobased extreme pressure additive performance in vegetable vs paraffinic base oils,”
Industrial and Engineering Chemistry Research, 51 (1), pp. 262-273. Available
here.
2. Sharma, B.K., Perez, J.M. and Erhan, S.Z. (2007), “Soybean Oil-Based Lubricants: A Search for Synergistic Antioxidants,”
Energy Fuels, 21, 4, pp. 2408-2414. Available
here.
3. Arca, M., Sharma, B.K., Perez, J.M. and Doll, K.M. (2013), “Gear oil formulation designed to meet bio-preferred criteria as well as give high performance,”
International Journal of Sustainable Engineering, 6 (4), pp. 326-331. Available
here.
4. Erhan, S.Z. and Bagby, M.O. (1998), “Vegetable oil-based offset printing inks,” 5713990, Feb. 3, 1998. Available
here.
Mary Beckman is a freelance science writer based in Richland, Wash. You can contact her at mbeckman@nasw.org.