Extending the service life of engine oils
Lynne Peskoe-Yang, Contributing Editor | TLT Lubrication Fundamentals July 2020
Developing cost-effective analysis programs can maximize oil life to improve your maintenance operations.
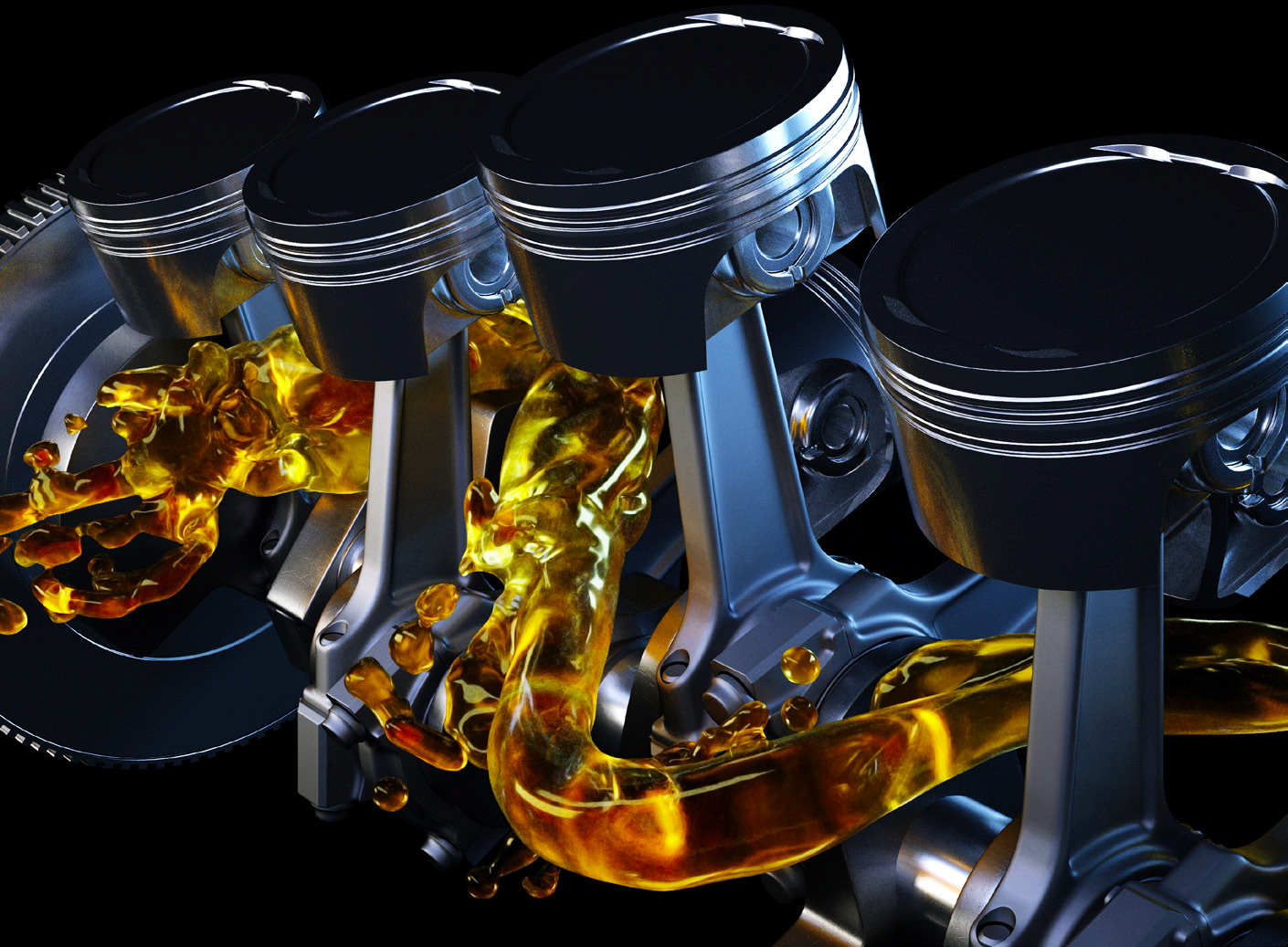
Even in an ideal lubrication scenario, where a well-matched oil runs on a healthy component under normal operating conditions, some amount of breakdown is inevitable. Engine oils are biodegradable fluids with naturally limited service life. Simply using an engine oil according to OEM instructions will eventually result in the degradation of the fluid, and additives can only hold off the process for so long. However, a basic understanding of how oils move through machinery over time reveals several options for extending the life of your oil and engine, even under the most extreme conditions.
End of service life
The chemical breakdown of oils in service starts with oxidation. “In an engine oil, we might start to see oxidation increase over time,” explains Emlyn Eager, a fleet maintenance engineer for BC Transit. As the oil’s natural molecular breakdown progresses, its viscosity drops, resulting in “thin” oil that can no longer form an effective barrier between the moving hardware components in the engine. Eager has seen this occur with great frequency in challenging applications like oil sands mining, where “equipment is often pushed to its limits in some of the most extreme environmental conditions,” such as extreme temperatures, wet terrain and air full of particulate matter. In these environments, measures to conserve oil life are essential to keeping down operational costs and might even save lives due to the extreme risks associated with engine failure.
Even in plant settings, where machines operate with automatic lubrication and where “temperature, duty cycle, speed and other factors that can affect lubrication are all consistent and controlled,” according to Eager, the life cycle of engine oil is limited by use. Adding mechanisms that extend the service life of oil can cut costs, lower environmental impact and reduce the risk of injury to operators by cutting down on the amount of time humans need to spend interacting with the machinery. Since all oil eventually breaks down, early warnings and planned oil maintenance are essential to keeping the degradation from affecting the engine as a whole.
Premature degradation
Intrusions from the external world can precipitate oil breakdown, far in advance of the recommended service life. The introduction of moisture from outside can encourage corrosion of metal components, which are at greater risk of disintegrating and further contaminating the oil with abrasive solids. Detached particles of rust can spread throughout the system, altering its chemical composition and scratching bearings and other hardware.
The most destructive force reducing oil life, however, is excess heat. “Heat basically accelerates the aging process of a lubricant,” says Eager. The purpose of engine oil is not only to lubricate moving parts but to keep the engine cool. Once temperatures rise enough to limit the oil’s effectiveness, the rest of the machine is at risk of overheating as well. This can trigger a cascade of failures within the engine, leading to devastating component damage. High temperatures encourage even more oxidation, which “can expedite the breakdown of the lubricant and eventually lead to reduced viscosity.” As viscosity decreases, the oil is no longer protective, and friction between moving parts is imminent. “Once this metal-to-metal contact starts to take place, it can lead to some very aggressive wear,” Eager warns.
Used oil analysis
To help operators maximize oil life and minimize waste, “education and training is key,” explains STLE-member Roger L. Young, senior field technical advisor for Imperial Oil. Scientific expertise can help operators avoid the mistakes that arise from poor oil health—without having to throw out good oil.
That expertise often comes in the form of used oil analysis, a maintenance operation in which the contents of engine fluids are tested in a laboratory setting. Technicians performing used oil analyses examine the lubricant for signs of contamination, levels of additives and traces of other components that might have degraded since the last servicing. The results of the sample analysis can save costs, either by assuring operators that the planned maintenance intervals are sufficient, or by prompting further investigation into any suspicious contents before the problem can affect other parts of the system and cause further damage.
Samples might be sent to oil analysis laboratories after every oil change, but experts warn that scheduled oil change intervals might be insufficient to keep the fluids in optimal condition. “If [the operators] are not monitoring oil health with used oil analysis trending, and only doing hourly or calendar-based oil changes, there is a very good chance they are not realizing the full potential of the lubricant,” warns Young. Frequent monitoring of indicators like viscosity retention, oxidation and pH level allows the earliest possible intervention, preventing further damage to the system. For this reason, operators might choose to invest in more frequent sample analyses to maximize cost efficiency over the lifetime of the engine.
Delaying oil breakdown
Some end-users avoid adding extra precautions like used oil analysis programs, advanced filtration systems or reduced operational temperatures to their maintenance plans because of the perceived cost of these changes. This and other concerns can be mitigated by “working closely with the supplier of the lubricants and other service providers,” says Young. Service providers can work with consumers to determine the best mechanisms for monitoring oil health in each application and to help plan the most cost-effective analysis programs over the life of the application.
Aside from frequent analysis, the best way to extend the optimum service life of an oil is to clean it before any contaminants have a chance to degrade the oil and set off a chain reaction of engine failures. “If you can keep a lubricant clean and dry, it can achieve very long service life in normal operating conditions,” explains Young. Filtration systems and desiccant breathers should be checked and changed on a regular schedule to ensure that they are efficiently drawing out contaminants and moisture.
Mechanisms like bypass filtration, magnetic filtration and other creative cleaning systems also might be recommended, depending on the needs of their engine model and application. “Some operators are installing centrifugal filtration on all their large engines, allowing them to more than double the OEM recommended oil drains, and sometimes extend their preventative maintenance intervals,” says Young.
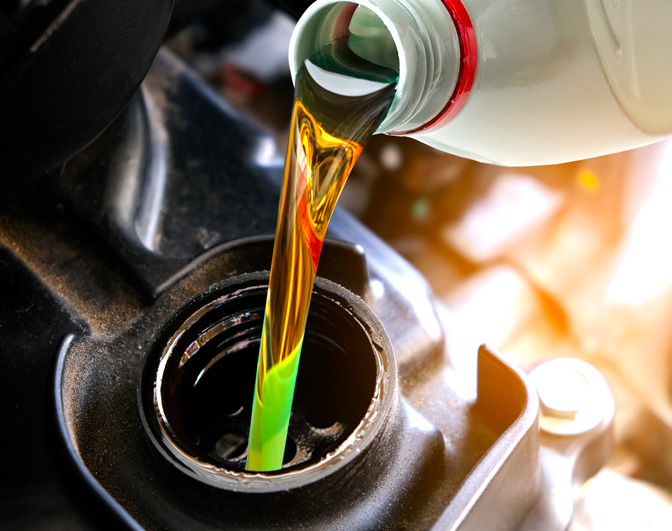
Post-failure recovery
Versions of these technologies are often available to customers as well, both for purchase and as treatments during routine maintenance. Aftermarket magnetic filtration technologies can keep debris from spreading throughout the system. These systems are especially helpful once failure does occur, as they can quickly remove contaminants before they start to travel, minimizing the need for post-failure oil flushing.
Oil end-users also can play an important role in maintaining the health of their lubricants by being engaged and informed consumers. “Changing inline filters on a regular schedule, or by monitoring pressure differential, also is good practice where applicable,” says Young. “Using these technologies can be key to extending oil drains and achieving the full potential of the product in use.”
Eager suggests paying extra attention to the selection of the lubricant and consulting experts to find the right grade, additives and other properties for the job. Common maintenance failures, such as improperly aligned hardware and overheated equipment, might decrease the service life of the oil, so routine maintenance and careful operation are essential in the long term.
Some end-users take advantage of preventative maintenance intervals to use kidney-loop bypass filtration, which “polishes” fluids instead of draining them. This method can add months to the life of gear oils and hydraulic oils. For certain applications, any interval between maintenance sessions is too long, notes Young. In such cases, customers have the option to install “permanent bypass filtration on stationary equipment and some mobile equipment applications to keep the oil clean and extend its service life.”
Investments like these can decrease the amount of product necessary to keep each application running, which is an effective cost-saving measure in the long run. But there is no limit to the advantages of mechanisms that maintain the cleanliness, viscosity and purity of engine oil, says Young. Advanced filtration and desiccant systems have benefits for the whole engine, including extended component life, more equipment uptime potential, softer environmental impacts and safer working conditions for employees.
Lynne Peskoe-Yang is a freelance writer based in Tarrytown, N.Y. You can contact her at lynnepeskoeyang@gmail.com.