3D printing of elastocaloric materials for refrigeration
Dr. Neil Canter, Contributing Editor | TLT Tech Beat April 2020
Researchers developed a nickel-titanium elastocaloric material that exhibits improved performance due to minimization of hysteresis.
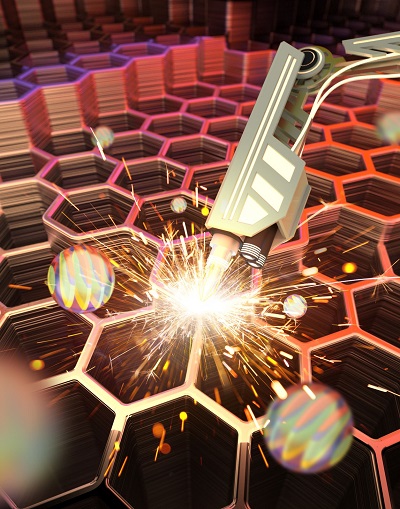
Figure 1. New elastocaloric material with potential as an alternative to liquid refrigerants was produced by 3D printing process known as powder-feed laser-directed-energy deposition. Figure courtesy of the University of Maryland.
KEY CONCEPTS
- An elastocaloric material, based on nickel and titanium, was produced by a 3D printing process and shows potential for use in cooling.
- By inducing eutectic solidification, the elastocaloric material consisted of two nickel-titanium compounds present in different phases.
- The unique structure of this elastocaloric material leads to an extremely narrow energy loss during each superelastic cycle.
Refrigerants used in refrigeration and air conditioning systems have been under regulatory scrutiny for over 30 years starting with the implementation of the Montreal Protocol in 1987. The purpose of this global agreement was to prevent the ozone layer in the earth’s atmosphere from depleting. Since then, liquid refrigerants have come under further scrutiny, leading researchers to evaluate other techniques for cooling.
In a previous TLT article, the preparation of a high-entropy alloy based on iron, cobalt, nickel and chromium, in combination with palladium, was discussed (1). This alloy showed the ability to exhibit the magnetocaloric effect at room temperature. Magnetocaloric materials absorb and release heat in the presence of a magnetic field. In effect, they act as magnetic refrigerators. The significance of this work is that previous magnetocaloric materials required the use of rare earth metals.
Another caloric cooling approach under evaluation is to utilize elastocaloric materials. Ichiro Takeuchi, professor of materials science and engineering at the University of Maryland in College Park, Md., says, “Caloric materials, in general, display highly efficient solid-state cooling that do not require the need for liquid refrigerants or refrigeration lubricants. Elastocaloric materials absorb and release heat through solid-to-solid phase transformations of shape memory alloys. The change in temperature occurring during these transitions is higher than for all other caloric materials, making elastocalorics the best potential alternative to the currently used vapor compression approach that involves the use of liquid refrigerants.”
Elastocaloric materials shift from an austenite to a martensite phase during the solid-to-solid phase transformation.
One limitation for elastocaloric materials is hysteresis. Takeuchi explains, “Hysteresis represents the energy loss occurring during each superelastic cycle when heat is released and absorbed. The elastocaloric material undergoes stress-induced superelastic strain when going through phase transformations. During each cycle, a certain percentage of energy is lost as heat. One goal of research, therefore, is to identify elastocaloric materials that will exhibit minimal hysteresis during use.”
A new approach for identifying and producing an elastocaloric material is needed to advance the potential for commercially using elastocaloric materials. Such an approach has been identified that utilizes 3D printing.
Nickel-titanium materials
Takeuchi and his colleagues have developed a new nickel-titanium elastocaloric material that exhibits improved performance due to minimization of hysteresis. The researchers focused on working with nickel (Ni)-titanium (Ti) materials because commercial versions have demonstrated good elastocaloric characteristics.
Takeuchi says, “We knew that existing nickel-titanium compounds were potentially useful as elastocaloric materials, but a new method for manufacturing them was needed to improve their performance. Fortuitously, we found that preparation of a nickel-titanium material through the use of 3D printing produced a unique metallic solid that displayed strong ability as an efficient refrigerant and a heat exchanger.”
The researchers used a technique known as powder-feed laser-directed-energy deposition (L-DED) to produce the nickel-titanium material (see Figure 1). During this process, a nickel-rich blend of elemental nickel and titanium powders were mixed. Upon treatment with a laser, local melting of the metal powders occurred followed by rapid solidification.
Takeuchi says, “In using L-DED, we were able to induce eutectic solidification. This feature led to the formation of a composite that contains not just NiTi, the main cooling phase, but also a second species, Ni3Ti.”
The researchers found that a significant percentage of the nickel-titanium material formed the Ni3Ti precipitate. In some cases, the precipitate represented about 50% of the overall material.
Takeuchi says, “Past work had demonstrated that the presence of precipitates in nickel-titanium materials resulted in poor performance. But in this case, the precipitate present was a benefit.”
Stress-strain curves and elastocaloric cooling data were generated on the nickel-titanium material formed by L-DED. The cooling efficiency of this new material was found to increase by a factor of four to seven over previously developed elastocaloric species.
Scanning electron microscopy clearly showed the two phases (NiTi and Ni3Ti) by virtue of their different crystal structures. Between these two phases is a strained interphase where dislocations are present.
Takeuchi says, “The unique structure of the L-DED formed nickel-titanium materials results in an extremely narrow hysteresis. Only a fraction of the material is affected during the transformation. The key parameter that we are evaluating is the ratio of hysteresis to input energy.”
Durability testing showed that this material displayed repeatable electrocaloric performance over 1 million cycles. Takeuchi says, “This durability is equivalent to a 10-year operating life for a commercial air conditioner or refrigerator.”
In the future, the researchers will be evaluating different geometries of the L-DED formed nickel-titanium material. Takeuchi says, “The 3D printing process enables us to manufacture different shapes. For example, a honeycomb structure is appealing because it will enhance heat transfer.”
One other objective will be to identify a shape memory alloy that exhibits lower transformation stress. Takeuchi says, “We are very optimistic about the future potential for elastocaloric materials. We are very close to demonstrating fully operational cooling devices using nickel-titanium. In the near future, we will be able to showcase a wine cooler using the nickel-titanium species as the elastocaloric solid refrigerant.”
Additional information can be found in a recent article (2) or by contacting Takeuchi at takeuchi@umd.edu.
REFERENCES
1. Canter, N. (2016), “Magnetocaloric effect using high-entropy alloys,” TLT, 72 (3), pp. 14-15.
2. Hou, H., Simsek, E., Ma, T., Johnson, N., Qian, S., Cisse, C., Stasak, D., Hasan, N., Zhou, L., Hwang, Y., Radermacher, R., Levitas, V., Kramer, M., Zaeem, M., Stebner, A., Ott, R., Cui, J. and Takeuchi, I. (2019), “Fatigue-resistant high-performance elastocaloric materials made by additive manufacturing,” Science, 366 (6469), pp. 1116-1121.
Neil Canter heads his own consulting company, Chemical Solutions, in Willow Grove, Pa. Ideas for Tech Beat can be submitted to him at neilcanter@comcast.net.