Environmentally Acceptable Lubricants
TLT Sounding Board April 2020
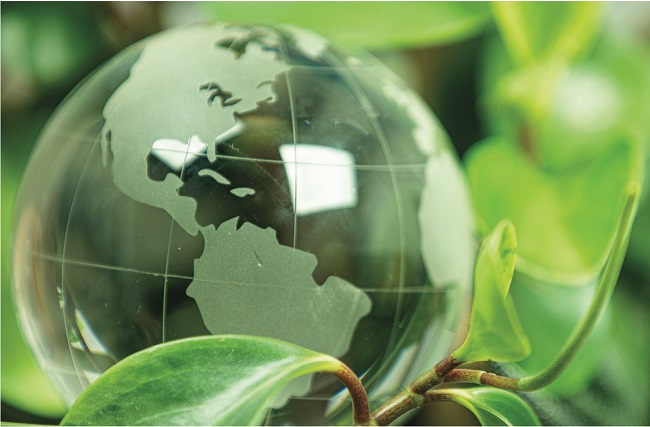
Executive Summary
Cost, stability, oxidation resistance, biodegradability, availability of additives, and regulatory issues were among the most common challenges cited by readers as it relates to formulating environmentally acceptable lubricants (EALs). “Biodegradability versus stability and service life is the biggest challenge for EAL products. Many users want products that have long drain intervals or extended service life, while still meeting the criteria to be classified as EALs,” said one reader. While readers are all for developing more “greener” lubricants, there is some concerns about product quality compared to traditional mineral oil-based lubricants. However, depending on who you ask, some think that with improved service life and technology that EALs could hold their own in performing well in different applications. Said one TLT reader, “A correctly formulated EAL will perform in line, or even better, than a correctly formulated mineral oil-based lubricant. Moving forward, TLT readers expect the use of EALs will become a critical focus in industries such as marine, automotive, power generation, metalworking fluids, among others, as companies become more socially conscious of improving their environmental footprint.
Q.1. What is the single greatest hurdle to overcome in formulating environmentally acceptable lubricants (EALs)?
Testing/proof-of-performance.
Oxidation.
The limited number of acceptable additives.
Secure supply of EAL base fluids.
Cost. In the end, most customers won’t pay more for EALs, although they all claim they will initially.
Too few options and too many regulations.
Finding environmentally acceptable additives.
Price.
The lack of suitable componentry available.
Customer willingness to deal with inherent lower lifetimes. We had EALs 50 years ago. We improved on them. Now we go back.
Preventing premature degradation of the lubricant due to natural processes, such as bacterial or fungal decomposition.
Oxidation resistance at a reasonable cost.
Tradition—that refers more to the usage than the formulation. We have field people who are still relying on what they learned 30 or 40 years ago.
Offering equivalent performance without any surprise interactions—for reasonable cost.
Standardization of performance issue balanced with marketing claims. Anytime the government dictates industry changes, the net benefit to the consumer is questionable.
Availability of accepted environmental impact data for components and formulations (or the cost of obtaining the data).
Biodegradability versus stability and service life is the biggest challenge for EAL products. Many users want products that have long drain intervals or extended service life, while still meeting the criteria to be classified as EALs. This can be a difficult balance to achieve.
Making the product resistant to bacteria and fungus using biodegradable ingredients.
Availability of additives (e.g., antioxidants, corrosion inhibitors).
Providing additives comparable to their mineral-based counterparts that can meet the environmental requirements.
Stability.
End-users like the idea of using EALs, however, they do not want to pay more for them unless it a mandated by regulations.
Biodegradability and non-bioaccumulative.
Not knowing much about the formulation process, my bet would be the formulating and proving of a lubricant that will degrade readily (while not in use) and pose little to no environmental threats.
Cost for the biodegradable esters and the cold temperature problems with the vegetable oils. Customers want to use EALs, but have a hard time justifying the cost.
Formulating materials that have the desired properties but still being EALs. (e.g., need to be water-resistant during use, but must break down in water within a certain number of days).
It can be difficult to replace legacy lubricants because they are familiar and give expected performance. People need to make an effort to adjust to a new product, even if it has better properties.
Cost of product and product quality to compare with life of conventional or other synthetic products.
The higher price level compared to mineral oil-based products.
Meeting all the global standards and having a product that can sustain the environments.
Suitability of base stocks and cost/performance ratio.
Defining what is “environmentally acceptable” in any specific application.
Customer education about modern EAL technology.
Alignment of formulation with customer requirements. With the range of HEPR products now available, together with HEES options, it just leaves formulators to clearly establish the needs of the customer.
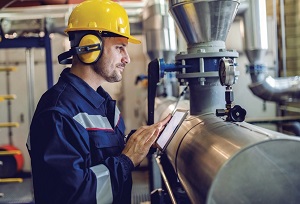
Fear of unpredictable reactions with other substances and equipment walls, and associated liability.
Most EAL oil formulations are based on synthetic esters, which are causing real lubrication problems in the stern tubes during maneuvering in port, or in adverse sea conditions, due to hydrolysis of the esters when contaminated with seawater.
Achieving similar performance for the same cost/value as that provided by non-EALs.
Meeting the key VGP requirements while still securing performance that will provide ROI for the client.
Making them machine compatible while meeting conventional oil performance standards at reasonable cost.
Q2. In terms of longevity in the system, how do you feel EALs compare to traditional mineral oil-based lubricants?
Longevity—oil base products are better.
Low viscosity polyalphaolefin and ester-based fluids are far superior, but biobased lubes still need work.
Great in non-threatening equipment environments, so-so in wet/hot equipment environments.
Less system life.
EALs have much shorter life due to oxidation and bacterial attack.
Slightly inferior.

Depends on formulation of product and the severity of the application.
Shorter life expectancy.
Poorly, but manageable.
They are an improvement.
EALs should, by definition, not last as long as traditional lubricants because they will be subject to decay processes in nature. It may be better to focus on creating or improving decomposition mechanisms for existing mineral oil-based lubricants, to clean up leaks and spills as they happen, and to improve sealing technology to prevent leaks and spills in the first place. If EALs were to fail prematurely in service because of microbial attack, it could cause costly or dangerous equipment failures that may be more environmentally damaging in the long-term than release of small amounts of oil-based lubricant to the environment.
Can be similar, depending on the formulation.
Substandard.
Eventually they will be as good.
EALs compromise performance in order to achieve environmental acceptability.
There seems to be an abundance of imagineering promoting these products. Longevity issues are a concern and the more operational variables faced, the more challenged are these lubricants. Obviously, this is a challenge for all lubricants, but are more so where EALs are concerned.
The oxidation stability of EALs tend to be less than mineral oil-based lubricants, due to the fact that EALs are required to biodegrade by 60 or more in 28 days. The EAL industry is limited in the amount of antioxidants or oxidatively stable components that can be included in the formulation. Mineral oil-based lubricants can be formulated with high levels of antioxidants in order to increase oxidation stability.
Superior.
Just as good in most applications.
They are worse in every way.
It depends on the quality of the formulation and manufacture. Some EALs have very poor life, and are as good as, or better than, mineral oil alternatives.
Depends on the base oil used. But for some it is very good—so long as moisture is kept out of the system.
Getting closer! Technology is available to overcome the original shortcomings.
Historically poor (but getting better).
Less durable.
Those made, not using vegetable oils, certainly hold up much better.
I don’t think EALs last as long as mineral oil-based lubricants. They are designed to break down faster in the environment, which means they will probably break down faster during desired use.
At least as good, if not better.
No good data yet from our customers.
Some will last longer and some not as long as mineral oils, depending upon what type of base oil is used.
A correctly formulated EAL will perform in line, or even better, than a correctly formulated mineral oil-based lubricant.
Nowhere near it yet but comparing apples to oranges because of additives used in traditional oils versus the constraints on the new EAL types.
Generally better and cleaner for hydraulics.
Replacement intervals may be extended.
From experience I can say that, given proper R&D, EALs can perform as well or even better compared to mineral oil-based lubricants.
EALs can be formulated to exceed the performance of Group I and II-based lubes, although there will likely be a cost premium.
They will last as long, or longer, if the correct synthetic EAL is selected.
In theory, EALs should behave better than traditional mineral oils, with up to four times longer life in service, but in reality, their behavior is worse.
They can be comparable, but again the value proposition is difficult to achieve.
In our experience with wire ropes, EALs don’t compare very favorably. Due to their very nature, they do not last very long—if and when—submerged in water; their water spray-off/washout results tend to be inferior. Their longevity tends to be less.
I’m not a user, but I would suspect (and anticipate) shorter service life if I entertained the change.
Q3. To what areas/industries do you feel the use of EALs will become a critical focus in the future and why?
Everywhere! Timing not certain, but I believe that all lubricants will become more environmentally acceptable as a base case.
Food, marine, and farming industries.
Marine, construction, agriculture, and off-road recreation.
Food grade applications.
Mining, due to current and future regulations.
None. The lubricant market will decline, due to use of technologies that do not require lubrication (e.g., electric cars) faster than EALs will be accepted.
As long as oil is at or near the price currently, I don’t think there will be a critical focus for EALs.
Those industries and applications where the chance of spills and leaks onto the environment are a very real possibility.
All areas and industries eventually, but first it will affect those that have a direct effect on the environment like marine applications. It will also affect materials used by industries, as opposed to the public because those areas are easier to regulate and enforce.
Automotive and industrial.
Food processing, agriculture, forestry, aquatics, and any outdoor, exposed application are areas of focus. Any application with the potential for accidental release into the environment will be under increasing scrutiny. The general public’s apprehension about exposure to chemicals will also be a driver for EAL use in the food processing industry.
Metalworking fluids because of the large amount of loss of fluids into the environment and contact with people.
Fluid power. Machine demand and system longevity.
Any application where the lubricant has an opportunity to enter the environment is a candidate for the use of EALs. In particular, the wind power generation industry, which continues to grow, both onshore and offshore, should seriously consider the adoption of EAL products as an industry standard.
Everywhere where the risk of a leak or spill could be too costly to mitigate or clean up.

Mostly in mobile equipment, including watercraft, and more specifically in equipment where a leak or spill could negatively affect soil and water courses, and water tables. This includes mining, dredging, fishing, transportation, agriculture, snow removal and salt spreading, and even (eventually) road construction, particularly when concrete is employed in place of asphalt. Less so in aviation, with the exception of watercraft-like float planes, where engines oils would need an EAL.
Hydraulic fluids (leaks in environment); cutting fluids (increased lubricity), process fluids (disposal).
Industries where the lubricants will have direct exposure to the environment. Areas such as mining, lumber, marine, outdoor recreation, railroad, etc.
Grease.
Remote monitoring and transfer station equipment that is not readily accessible and/or monitored.
Mining, construction and hydroelectric facilities, especially around water and other sensitive areas. The cost now for spilling is growing, and the bad press that can accompany a spill is something users have to be aware of going forward.
Electric vehicles.
Only if government regulation promotes them. Gaining some traction in metalworking fluids without regulation push.
Nearly everything could be seen as a top challenge and potential new and future market.
Focus will be put on off-road equipment in an effort to prevent soil pollution.
Agriculture. Today farmers are using the cheapest lubricants they can get hold of, contaminating fields with mineral oil and additives. The lubricants used should be EAL and food grade.
Transportation, and oil & gas industries. These industries operate and produce byproducts (exhaust, open gearboxes/rack-and-pinion, etc.) that come in direct contact with the marine environment.
All industrial fluids.
Marine applications, agricultural, forestry and mining machinery are the main sectors on which attention will be focused on the use of EALs, being really critical their application on large ships.
Construction, shipbuilding, mining, or any industry where it is difficult to contain the lubricants from the environment. The contamination factor is a much higher risk in these areas than in traditional manufacturing/machine shops where lubricants can be more easily contained.
Maritime will grow for a wider range of applications due to the deserved growing focus on cleaning up our oceans. Forestry for the same reasons. Wind power as they are often situated in environmentally sensitive sites on land and water.
I would suspect that most, if not all, industry will start to move in that direction due to social pressures and public expectation on companies to continue to grow in social and environmental consciousness.
Editor’s Note: Sounding Board is based on an informal poll of 15,000 TLT readers. Views expressed are those of the respondents and do not reflect the opinions of the Society of Tribologists and Lubrication Engineers. STLE does not vouch for the technical accuracy of opinions expressed in Sounding Board, nor does inclusion of a comment represent an endorsement of the technology by STLE.