20 Minutes With Vasu Bala
Rachel Fowler, Managing Editor | TLT 20 Minutes April 2020
Tiarco LLC’s global technology and quality director discusses the challenges of designing and formulating additive systems for lubricants and greases.
Vasu Bala - The Quick File
Dr. Vasu Bala is the Global Director for Technology and Quality at Tiarco LLC. Bala is a graduate of the Pennsylvania State University where he earned his doctorate in chemical engineering in 1988 and completed his postdoctoral studies in 1993. His research interest lies in the fundamentals of lubricant rheology, additive synthesis and lubricant formulation development, mechanics of elastohydrodynamics and boundary lubrication, electrorheology, lubricant and material durability, wear characterization and frictional behavior of ferrous and nonferrous materials.
Bala was previously employed at Afton Chemical Corp., Cognis-Henkel and BASF Corp. (1993-2017), serving in various capacities as technical advisor and global technical director. Now at Tiarco, his responsibilities include developing product marketing strategies, new grease and lubricant technologies for North American, European, Japanese and Chinese automotive and industrial systems. He is an STLE member and also maintains affiliations with Alpha Chi National Honor Society, Tau Beta Phi National Engineering Honor Society, Society of Automotive Engineers (SAE), TAE Germany, Industrial Tribology-UK, National Lubricating Grease Institute (NLGI) and Who’s Who for Outstanding Scientists.
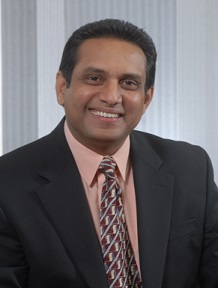
Dr. Vasu Bala
TLT: What are some of the challenges in today’s applications for the development of additive components or systems for use in lubricants, particularly automotive and industrial gear lubricants and greases?
Bala: Some of the key challenges stem from meeting field performance standards that require lubrication for severe applications. End-users, in their continuous pursuit for operational efficiencies and profits, are driving OEM requirements in setting new limits for endurance in gearboxes, gears and bearings. The demands for off-highway performance are also trending towards mainstream. Collectively, these drivers have OEMs promoting higher gearbox efficiencies, operating with higher power densities and temperatures, and extending warranties with longer lubrication intervals (see Figure 1).
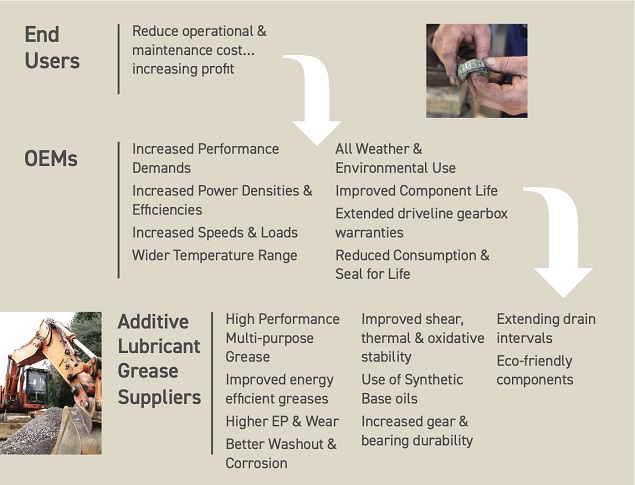
Figure 1. Lubricant grease trends and their consequences. 2019 Annual NLGI Meeting.
These increased OEM requirements are placing higher performance demands on lubrication of power transmission gearboxes. Lubricants and greases must inherently be able to provide lubrication under high loads and low speeds, possess improved thermal and oxidative stability, and be able to operate in wide temperature ranges and harsh environments (see Figure 2). Additional requirements also extend to eco-friendly options for lubricants and greases for electrification (conductivity, material compatibility and corrosion), biodegradation and low toxicity.
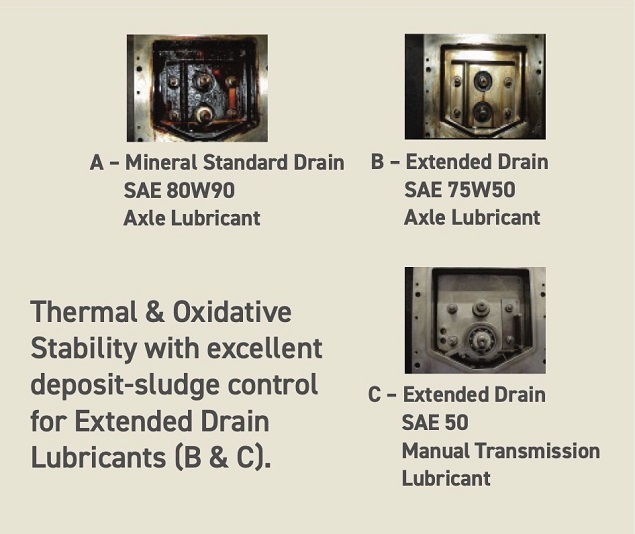
Figure 2. Deposit and sludge control comparison of extended drain synthetic driveline lubricants. 17th International Colloquium Tribology, 2010, Germany.
TLT: When designing and formulating a lubricant additive system, what are some of the considerations, aspects and steps that should be evaluated to assess the development of this additive system?
Bala: It is essential to develop a performance profile that encompasses end-user, OEM and environmental and regulatory requirements, each of which requires careful consideration. A testing matrix is defined based on these requirements for initial screening with additives, thickeners and base oils. The next phase in testing requires lubricant or grease formula optimization to meet performance requirements and treat cost limits. In almost all cases, competitive benchmarking is the final step to capture performance claims that merit lubricant or grease replacement.
One significant challenge to this development phase could be limited field correlation using standard bench or rig tests. Lubricant and grease formulators may have to incorporate testing methodology as part of the overall product development. Several regulatory and toxicological profile and Freedom to Operate (FTO) reviews are also recommended throughout the development phase to ensure a smooth product launch. Another challenge to bear in mind is ensuring the supply chain for additive production is well secured prior to initial field testing or scale-up.
TLT: What global concerns, trends and challenges do you foresee will lead to the development of innovative additive systems?
Bala: There are several hurdles and challenges that hinder the development of new chemistries for innovative additive systems, including new categories for industry and OEM specification, FTO conflicts, intellectual property filing and regulatory considerations. When OEMs are developing performance targets driven by new hardware or design changes, the lubrication requirements are created last. This can sometimes lead to untenable performance targets. Several OEMs have incorporated lubrication requirements early into their design phase to better manage this limitation. It is also common to have OEMs develop new testing protocols that simulate field durability. In most cases, extensive field testing can take several years with prototype power transmission gearboxes.
When an innovative system has passed production scale-up and rigorous field trials and is ready for commercial launch, the tasks to file intellectual property coverage and obtain regulatory approval and registrations can be very costly and time consuming. Sometimes, to mitigate these costs and to meet launch timelines, currently available additives are used and the final mixtures are designated as confidential. As lubricant suppliers are assessing mandates and integrating automotive trends into their lubricant developments, incorporating performance benefits can facilitate defining sustainability benefits for lubricants and greases. This can further delay product launches. Examples in classifying these benefits can range from application types, health, safety, toxicity, biodegradability and labeling. Examples around the world that have adopted ecological labeling requirements for sustainability are shown in Figure 3.
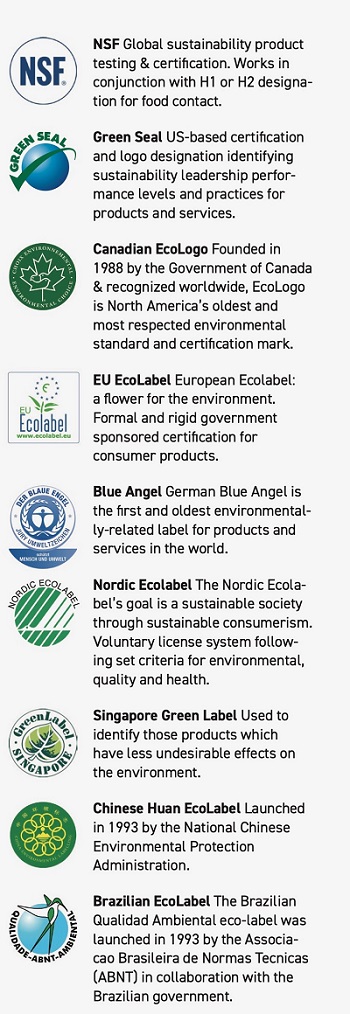
Figure 3. Worldwide labeling for sustainability. 17th International Colloquium Tribology, 2010, Germany.
TLT: What are some of the resources that you use to track industry trends?
Bala: There are several resources that are available to keep up with industry trends. The following are listed not in any order of importance, nor is the list exhaustive:
- Trade publications (Tribology International, Tribology Letters, Wear, Tribology Transactions, Journal of Tribology, Friction, Lubrication Science)
- Patent literature (USPTO, EPO)
- Conferences or symposium plenary lectures (STLE, NLGI, SAE, Gordon Research Conference, World Tribology Congress, F&L Asia, ILMA, International Colloquium Tribology, Japan International Tribology Conference)
- Industry Advisory Panel (Detroit).
The International Tribology Council (ITC) also provides a comprehensive annual list of tribology-related conferences worldwide.
TLT: What types of bench testing do you take into account in the development of an additive system or component?
Bala: Once the base oil or grease type is defined, the additive screening is initially performed on bench tests. These tests are selected based on the initial assessed lubricating regimes and operating conditions. Several bench tests for wear friction, scuffing, load bearing, oxidation, elastomer compatibility and corrosion are widely available for use at sanctioned outside laboratories (see Figure 4).
The challenge is to run several key tests in parallel to cull and optimize additive types in the shortest possible time. Further confirmatory tests are then performed in the next tiered key tests. These sometime include modified bench or rig tests that target new hardware, design or operating conditions. The interpretation of the results from these tests are critical as field testing is the next phase in development. The reliance of field test approvals allows for minimizing risks associated in both OEM equipment rollouts and running changes. The used oil or grease analyses and equipment inspections to assess overall failure modes is a necessary step towards any equipment or lubricant/grease product launch. This last step may be iterative in developing the final optimized additive system that meets the targeted performance claims.
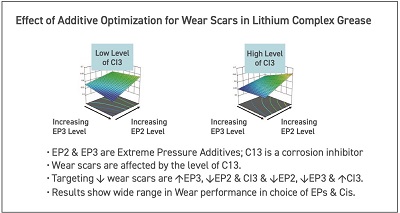
Figure 4. Effect of additive optimization for wear scars in lithium complex grease. 2019 Annual ELGI Meeting.
TLT: How do you take into account possible base oil and/or additive interaction or reactions that may affect the overall performance of a lubricant additive system?
Bala: This is an interesting, yet easily overlooked, criterion for developing an additive system. It is not always initially apparent what base stocks and grease types that are compounded are preferred by the customer. In some instances, the slate of base oils or components used in grease manufacture can vary during the additive system development phase. At best, base oils and grease types should be considered very early on in the additive system’s development phase.
The quality of base oils and unique grease production that are widely prevalent makes it challenging but can be screened with initial bench tests that relate to bulk lubricant or grease properties. Examples of these tests include churning losses, oxidation, corrosion, dropping point, washout, low temperature rheology and oil separation. Additive systems can be optimized specific to base oils or grease types. Figure 5 depicts an example of temperature reduction using an optimized additive system used in a synthetic manual transmission keeping the base oil systems similar.
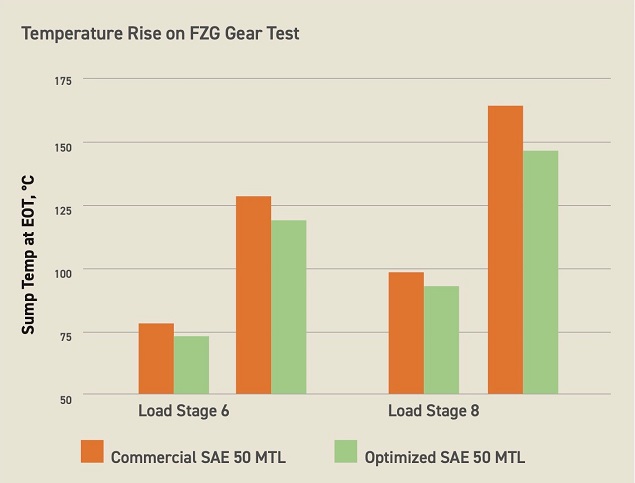
Figure 5. Minimizing gear sump temperature on FZG gear test. 17th International Colloquium Tribology, 2010, Germany.
TLT: When you first started developmental work in the industry, what were some of your initial challenges?
Bala: Some of the initial challenges included developing new chemistries for improved high temperature gear and bearing wear, scuffing, corrosion and oxidation for hardware durability and fuel economy. The bench and rig tests needed to evaluate these improvements were not available, and a great deal of time was also spent on developing test methodologies and real-time depletion of lubricant additive characterization. The gratifying outcome was these chemistries and formulations are still in use today, as shown in Figure 6.
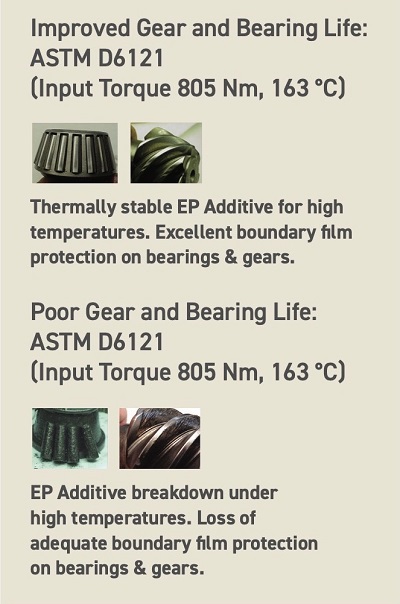
Figure 6 (a.) Improved gear and bearing life: ASTM D6121 (input torque 805 Nm, 163 C), (b.) Poor gear and bearing life: ASTM D6121 (input torque 805 Nm, 163 C). 17th International Colloquium Tribology, 2010, Germany.
Another example is the development of an axle efficiency testing methodology to simulate SAE J2360 fuel economy (see Figure 7).
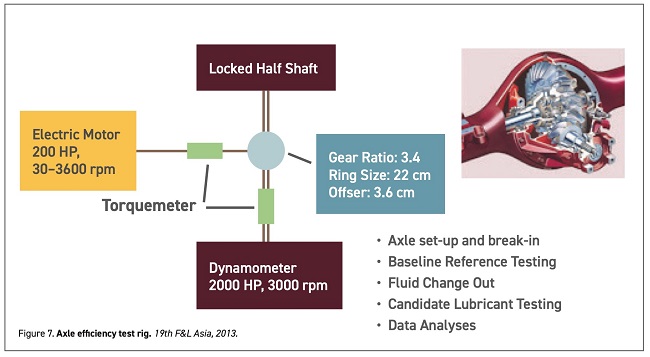
Figure 7. Axle efficiency test rig. 19th F&L Asia, 2013.
TLT: How did these initial challenges help with your skillsets to develop a lubricant additive system?
Bala: The initial challenges helped reinforce the belief that the use of tribology fundamentals is not limited to quantifying lubricating regimes, but also to accounting for additive types and their effects that are far more difficult to quantify. Tribology fundamentals are still limited in developing dynamic models for boundary friction, film formation, reactive pathways for thermal rearrangement in oil/grease bulk phase and eventual decomposition on surface. There is still far more to understand. When we keep our minds open to recognizing the unexpected performance synergies, research and development can always stay current.
You can reach Vasu Bala at vbala@trcc.com.