Filter Selection
Evan Zabawski | TLT From the Editor March 2020
Using the beta ratio in a practical way.
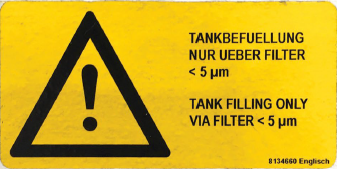
During a lubrication audit of a manufacturing plant with injection molding machines it was noted that the OEM required the lubricant to be prefiltered to <5 µm—which was not being done. The predictive maintenance technician asked how much time prefiltration using suitable 3 µm filters would add to an oil change, and the answer depends on the desired cleanliness, which, in turn, depends on the beta ratio.
Beta ratio is a singular value coupled with micron rating, e.g., ß3=75, where 3 represents the micron rating and 75 represents the number of particles upstream of the filter where one particle would remain downstream of the filter after one pass through the filter; so why is it not written 75:1?
The method used to determine the beta ratio is laid out in ISO 16889:2008, known as the multi-pass method for evaluating the performance of a filter element. Essentially the test is comprised of a miniaturized oil circulation system with particle counters and pressure sensors installed both upstream and downstream of the filter. The fluid is then dosed with ISO medium test dust contaminant and circulated through the filter until terminal pressure is obtained.
The calculation uses the upstream particle count divided by the downstream particle count, then reduces the values so that the denominator is one, after factoring the number of passes. Therefore, the reported value of 75 (“:1” is assumed) indicates an average of 74 out of 75 particles are removed per single pass through the filter being evaluated.
How some people try to make sense of the beta ratio is to convert it to single pass efficiency—a percentage removal rate. For a beta ratio of 75, the efficiency is 98.7%, obtained by taking 74 divided by 75, then multiplied by 100. The problem is that 98.7% sounds very high, yet a beta ratio 1000 is commonly available, and its efficiency is 99.9%, a seemingly small-sounding improvement.
The reality is that the 1.2% difference compounds with each pass through the filter and after just four passes a ß3=75 filter would allow over 30,000 times as many particles through the filter compared to a ß3=1000 filter. From this perspective, there appears to be a significant difference between the two filters, which is why single pass efficiency can be somewhat misleading.
Ultimately it is best to leave beta ratio alone, without conversion, and to simply calculate the number of passes required to obtain the desired cleanliness. This calculation is straightforward: take the existing particle count at the required micron size and divide the beta ratio to obtain the resulting particle count after one pass. Divide this answer by the beta ratio again to obtain the particle count after two passes; repeat until desired cleanliness is reached.
For example, let’s assume 1,000,000 particles larger than 3 µm is the current cleanliness of the fluid and calculate the resulting cleanliness from four passes. Taking 1,000,000 and dividing by 75, then that answer is divided by 75, and then two more iterations would yield 0.031605 particles. Repeating the calculation by dividing the particle count by 1,000 through four iterations yields 0.000001 particles.
Though it is true the former value is over 30,000 times higher than the latter, both filters would eventually reduce 1,000,000 particles to less than one particle. The practical perspective is that transferring oil from a drum using a duplex filter cart equipped with twin ß3=1000 filters could reduce 1,000,000 particles to one particle in one pass, but twin ß3=75 filters would require almost twice as many passes to achieve the same cleanliness.
In the end, I usually say, “What you lack in efficiency is made up in passes.” Filters rated at the same micron value will eventually remove all the same particles, but the beta ratio determines how quickly.
Evan Zabawski, CLS, is the senior technical advisor for TestOil in Calgary, Alberta, Canada. You can reach him at ezabawski@testoil.com.