Pour point
Evan Zabawski | TLT From the Editor November 2019
Misleading, misinterpreted or misnamed?
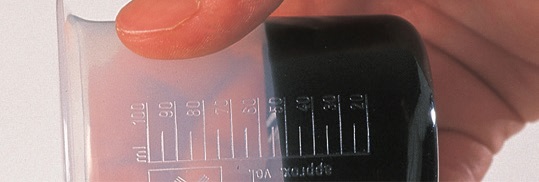
This test should be called the ‘lowest temperature that a sample moves within five seconds’ test, not pour point.
Photo courtesy of Parker Kittiwake.
When researching a lubricant’s physical properties, most data appears to provide intuitive information. Flash point and fire point provide guidance regarding upper operating temperature limits for lubricants used near sources of ignition, though more information would be required for proper flammability assessment. Consequently, it seems to be a common extrapolation to assume pour point provides guidance for the lower operating temperature limit of a lubricant—but does it?
It is helpful to understand the basics of pour point testing. A small volume of sample is placed in a flat-bottomed, cylindrical glass jar that is stoppered using a cork with a thermometer inserted through its center. The sample is then heated to at least 45 C (113 F) before the jar is jacketed and transferred to a liquid bath cooled using dry ice. As the sample cools, the jar is removed from the jacket every 3 C from the starting temperature and tilted enough to discern any movement. If movement is observed the jar is replaced in the jacket and cooled another 3 C.
This step is repeated until such time as tilting the jar completely horizontal and maintaining this orientation for five seconds yields no discernible movement. At this point the temperature is recorded and the test is concluded, but the reported result is determined by adding 3 C to the recorded temperature, essentially reporting the last temperature with observable movement.
Truthfully, this test should be called the “lowest temperature that a sample moves within five seconds” test, and not pour point. The test does not measure pouring ability in any manner, so really it is a poorly named test (pun intended). So, just what does the result imply?
Essentially the test is determining the effect the formation of wax crystals has on the strictest definition of flow (minimal movement), rather than a particular viscosity. Ken Bannister’s book Lubrication for Industry suggests, as a guide, that the maximum pouring viscosity is 22,000 cSt, the maximum viscosity for splash lubrication is 11,000 cSt and the maximum pumpability viscosity for gear and piston pumps is 8,600 cSt. Pour point does not represent any of these limits.
Some documents suggest staying 5 C to 10 C above the pour point to ensure proper operation of lubricated equipment, but this seems dangerously close to the possibility of a loss of flow. I was told of a failure during the commissioning of a splash-lubricated gearbox at -34 C, a full 20 C higher than the lubricant’s reported pour point of -54 C. The Root Cause Analysis later performed by the rebuild shop determined the failure to be due to a lack of lubrication, suggesting the oil likely channeled within the first rotation and most of the gear teeth and bearings ran dry.
Another viewpoint that can lead to failure is using a tool like a viscosity calculator to reverse calculate the temperature where the viscosity reaches one of the aforementioned limits. The problem lies in the fact that viscosity follows a predictable relationship with temperature until waxes begin to solidify, and pour point proves this value varies significantly based on the wax content (purity) of the lubricant and not its initial viscosity. Therefore, the calculation cannot necessarily be relied on at very low temperatures.
Essentially then, the pour point is not revealing relevant viscosity information, there is no reasonable safety margin to supplement pour point, and no other common data like the viscosities at 40 C and 100 C offers the requisite information to safely determine a lower operating temperature limit. One solution could be low-temperature viscosity measurements run at reasonable and expected cold-weather temperatures based on local weather tables. The downside is that the onus for this testing would fall on the end-user or the lubricant distributor.
Perhaps we should just report the first temperature all movement ceases and give the test a more literal name like Plastic Point?
Evan Zabawski, CLS, is the senior technical advisor for TestOil in Calgary, Alberta, Canada. You can reach him at ezabawski@testoil.com.