Solid lubricants
Jane Marie Andrew, Contributing Editor | TLT Lubrication Fundamentals August 2019
These materials are well suited for extreme conditions where liquid lubricants are impractical.
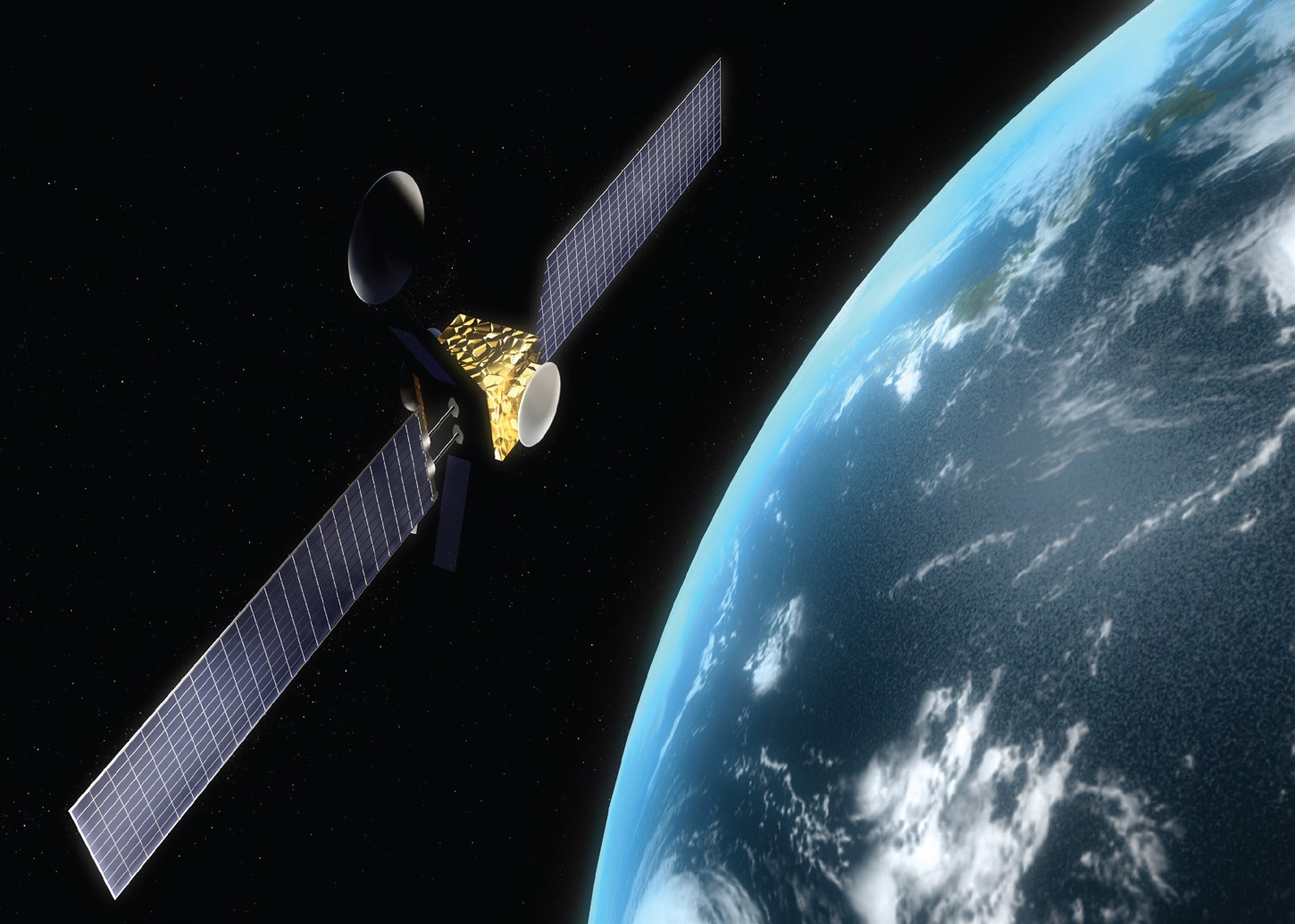
© Can Stock Photo / Eraxion
KEY CONCEPTS
• Solid lubricants are ideal for but not limited to extreme conditions.
• They are usually applied as coatings by a variety of methods.
• Advances are focused on coatings whose properties can change with operating conditions.
Although liquid lubricants are the typical solution for reducing friction, sometimes they are impractical or inadequate, for instance, where there is extreme contact pressure, elevated temperature or a vacuum. Such atypical conditions call for atypical solutions. Fortunately lubrication technology now includes a range of solid lubricants (also called dry or dry-film lubricants) that are well suited for extremes.
Solid lubricants take the form of either a coating applied to a surface or solids added to a composite. Unlike liquids or gases, solid lubricants do not volatilize or decompose in extreme operating conditions. However, they often have specific operation criteria and thus require careful selection or customization to the application.
Most solid lubricants fall into one of four classes:
1. Carbon-based solid lubricants such as graphite, diamondlike carbon (DLC) and nanocrystalline diamond
2. Transition-metal dichalcogenides such as molybdenum disulfide (MoS2) and tungsten disulfide (WS2)
3. Polymers and polymer composites, including polytetrafluoroethylenes (PTFEs, e.g., Teflon) and polyimides
4. Soft metals, such as gold, silver, lead and copper.
First developed for applications in the 1980s, these coating have become more structurally sophisticated as research has advanced. In a review chapter for an ASM handbook (1), Sandia Laboratories scientist and STLE Past President Michael T. Dugger classified solid lubricants according to their chronological development, moving from single-component structures to multicomponent or multilayer structures, then later to nanostructured, superlattice or functional gradient structures. At the forefront today are adaptive or smart structures.
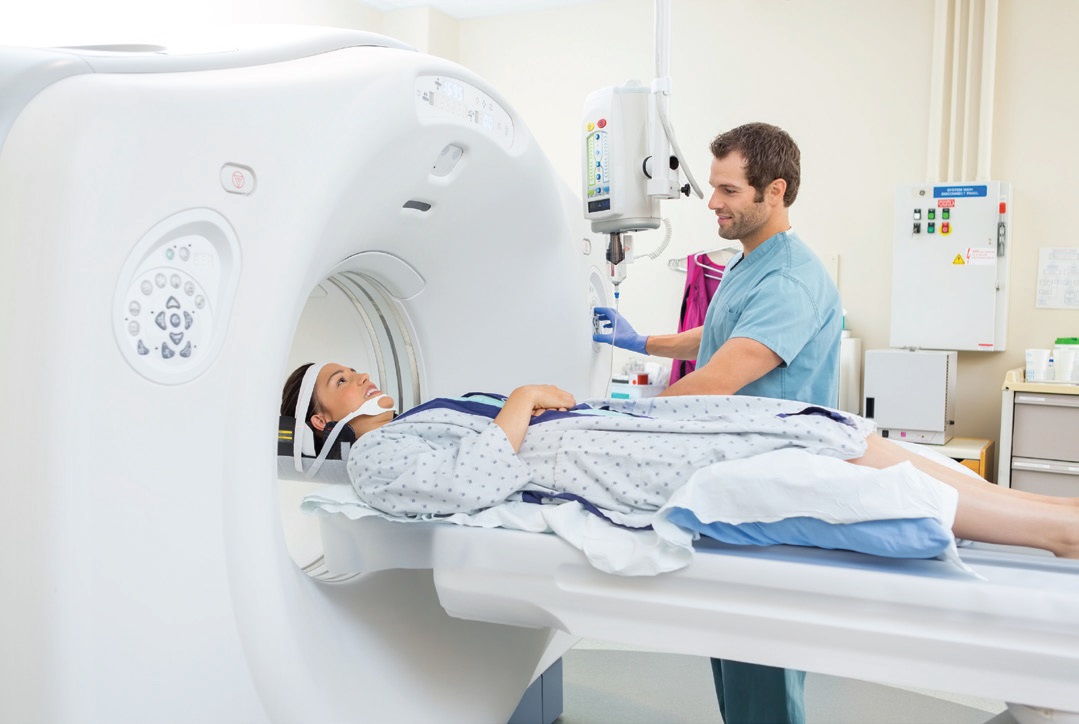
Solid lubricants are a good choice for diagnostic imaging machines because the bearings in these tubes operate at high rotational speeds, at high temperature and in a hard vacuum.
© Can Stock Photo / Leaf
Application or fabrication
Solid lubricants can be either monolithic or applied as a coating or thin film. Most solid lubricants are applied as a powder that is burnished, thermal sprayed or cold sprayed on a part to form a coating or film. Such methods can be inexpensive and are appropriate for coatings that need to be replaced periodically. For coatings used in environments where replacement is not possible, physical and chemical vapor deposition processes may be required. In these processes, atoms or molecules of the solid lubricant are vaporized from a piece of the solid and deposited on a substrate material. For polymer-based solid lubricants and their composites (e.g., PTFE containing nickel), electrochemical processes are used.
Although solid lubrication usually requires an application or fabrication step, under some conditions a similar effect is created during operation. Liquid or gas lubricants can sometimes react with the contacting material during operation to form a thin film of solid lubricant, often called a tribofilm. Such a film can function like a solid lubricant as long as the film remains in the moving contact. For example, tribofilms can form on DLC in the presence of liquid lubricants as a result of friction-induced chemical reactions between the DLC and additives in the lubricant. Thus, DLC can be used to mitigate friction and wear in automotive piston rings and cam followers, for example.
Characterization and evaluation
The composition and structure of solid lubricants are studied with a range of spectroscopic and structural microscopy techniques. Their performance is evaluated initially with standard tribological lab tests such as pin-on-disk sliding and high-frequency reciprocating wear. Once a candidate material is identified, larger-scale bench testing, such as engine tests, are conducted.
Lubrication mechanisms
The fundamental lubrication mechanism for a solid lubricant is interfacial sliding between the wear track that forms on the solid lubricant and the transfer film or tribofilm that adheres to the sliding counter face material. When low interfacial shear can be achieved, friction between the contacting surfaces is often very low, extending wear life.
The wear life can be further increased by using a hard, load-bearing underlayer to minimize the contact area. This soft-on-hard combination is often referred to as the Bowden-Tabor concept (2). The four classes of solid lubricants mentioned previously all provide low interfacial shear at the moving contact.
Properties and operating parameters
In general, the parameters that control friction and wear with solid lubricants are low interfacial shear in the direction of sliding; strong adhesion to the surface; adequate lubricant cohesion; and physical, chemical and mechanical compatibility with the contacting surface. These parameters must be satisfied for the intended operating contact pressure, temperature and chemical environment. Other parameters to be considered include thermal stability, oxidation stability, volatility, chemical reactivity and melting point.
Sliding friction coefficients for solid lubricants are usually <0.1-0.2, and wear rates range between 10-6 and 10-7 mm3/Nm, thus somewhat higher than those of liquid lubricants. (See Scharf and Prasad (3) for a summary of friction coefficients for many common solid lubricants.) The latter wear rate equates to an average removal rate of less than 1 atomic layer per 1 cm pass of a counter body loaded at 5 N. A maximum hardness of 5 on the Mohs scale is the practical limit for solid lubricants.
As to operating parameters, in general, solid lubricants do not volatize or evaporate; they are less sensitive to picking up dust or other contaminants, and they can be stored or dormant for long periods of times without lubricant escaping from the contact. Their general advantages and disadvantages are summarized in Table 1. Solid lubricants are available for a wide range of temperatures (cryogenic to approximately 700 C), environments (humid to dry air, ultrahigh vacuum), and contact pressures (megapascals to gigapascals). General characteristics and operating conditions of the main classes of solid lubricants are summarized in Table 2.
Table 1. Advantages and Disadvantages of Solid Lubricants

Table adapted from Van Rensselar, J. (2009), “Aerospace Lubricants: Solid is essential in every sense,” TLT, 65 (6), p. 44.
Table 2. Operating Parameters of Solid Lubricants
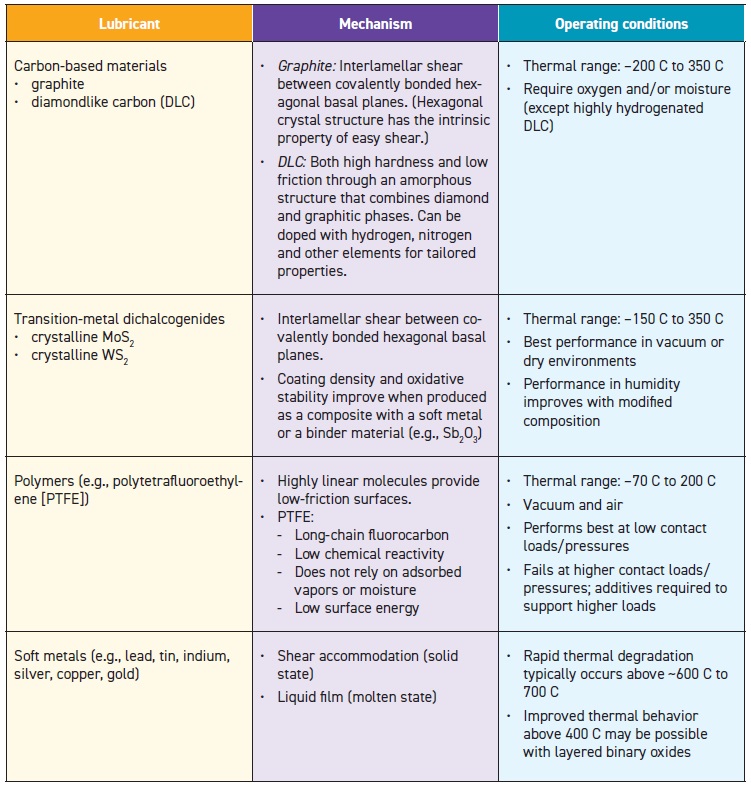
Typically, solid lubricants are used at extremes of temperature and pressure at which liquid lubricants are not feasible (see Figure 1). For example, coatings on satellite components must function in an ultrahigh vacuum atmosphere in low Earth orbit, resist exposure to radiation and atomic oxygen and cycle between extreme temperatures (cryogenic to about 100 C). Such applications usually use an MoS2-based coating. Increasingly, however, designers are choosing solid lubricants even within the traditional liquid lubricant regime. For some cases, solid lubricants are cheaper and easier to implement than liquid or gas-phase lubricants.
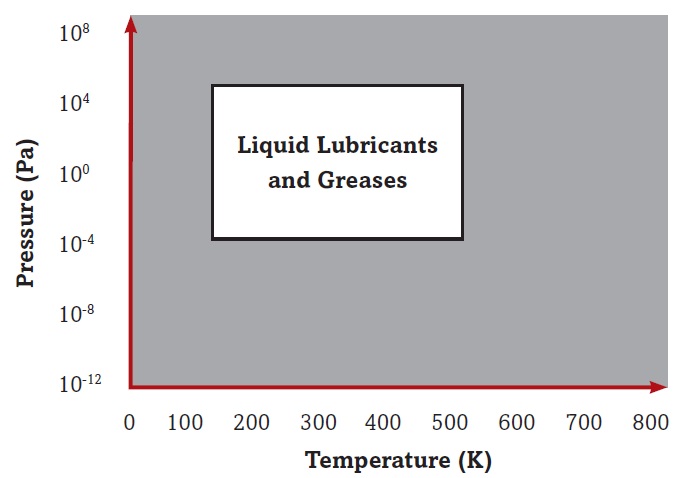
Figure 1. Typical operational and temperature range of liquid lubricants and grease. Traditionally solid lubricants have been used in the region outside the box, but increasingly they are used throughout the entire pressure/temperature space. (Adapted from Doll, G.L., (2017), “Lubricant strategies for challenging environments,” ASM Handbook, Vol. 18: Friction, Lubrication, and Wear Technology, edited by G.E. Totten. Materials Park, Ohio: ASM International, pp. 213-219. Reprinted with permission of ASM International. All rights reserved. www.asminternational.org.)
These operating ranges can be tailored to a degree, but no single solid lubricant material can function over the entire range of extremes. Attention has thus turned to composite solid lubricants in which each phase in the composite can target given operational range(s). For example, a composite coating consisting of CaF2/BaF2 (for high temperatures), silver (for low temperatures) and CrOx (for wear resistance) has been developed for use to ~900 C. Other composites that have been qualified for applications include MoS2/Sb2O3/C for space coatings and WC-doped DLC for rolling elements.
In addition to the main categories listed in Table 2, a variety of other materials can function as solid lubricants under certain conditions. Fluoride coatings (e.g., CaF2 and BaF2) and oxide coatings (e.g., B2O3) are lubricating at high temperatures (i.e., over 500 C) where their shear strengths are small. PbO has good lubricating properties from about 450 C-700 C but is limited by its shear strength at low temperatures and by phase change, reactivity and melting at high temperatures. Other materials that are sometimes desirable for their high-temperature lubricating properties include oxygen-deficient TiO(2-x) materials with mechanically weak shear planes, oxides and double oxides, and Cs-based compounds.
Applications
An application that illustrates the value of solid lubricants is coatings for rolling bearings in rotating anode X-ray tubes used in diagnostic imaging. Bearings in these tubes operate at high rotational speeds, at high temperature and in a hard vacuum. In addition, electrical current must pass from the bearing housing to the shaft, which is connected to the anodic material. Some of the important criteria for solid lubricants used in this application include high electrical and thermal conductivities, low wear rates and high lubricity at operating temperatures. These criteria limit the solid lubricants to materials such as lead, gold and silver. Additional application requirements limit the thickness and deposition processes that can be used to deposit these materials.
In general, solid lubricants are highly valued for mechanical devices that operate in vacuum, high temperatures or inert atmospheres, and they are essential for components operating in space (4). They also are used to mitigate fretting-type wear in mechanical components that experience low-amplitude, oscillating motion. Rolling bearings used in high-speed turbine engines employ silver coatings on steel cages to lubricate the ball/cage and cage/land contacts. Foil bearings used in gas turbines now employ a specially developed solid lubricant coating (5). Diamondlike carbon lubricants are now being used on rolling bearings and gears that are normally oil-lubricated but experience periods of interrupted oil flow (6). During these interruptions, the DLC coatings function as solid lubricants.
Customization
For some applications it is advisable to customize solid lubricant coatings to meet the demands of the contact environment. For example, when the operational lifetime of the component depends entirely upon the durability of the coating, the solid lubricant must have adequate wear resistance and/or a stable tribofilm. In contrast, where the goal is to minimize frictional heating from intermittent contact, a low friction coefficient is more critical than good wear resistance. It is sometimes possible to meet conflicting tribological demands with a composite. Some composites are self-lubricating—that is, the contact surface material incorporates a solid lubricant (such as graphite or MoS2). In other composites, different components provide the necessary properties at different conditions.
Future approaches
The next step beyond composites, in terms of broadening the operating range of solid lubricants, appears to be adaptive lubricants. Adaptive lubricants are materials that react with the environment to form new lubricious phases as temperature increases. Adaptive lubricants have a low-friction surface at room temperature, and as temperature increases, the components react with each other and with oxygen to form a high-temperature lubricious phase. Examples of adaptive lubricants include
• Transition-metal dichalcogenides strengthened with oxides and doped with soft metals
• Nanocomposites with diffusion barriers
• Dichalcogenide composites with phosphates and soft metals
• Fullerene-like nanoclusters of transition-metal dichalcogenides in metal nitride matrices.
Adaptive solid lubricants may enable machine elements to operate more effectively in changing and/or demanding application environments.
About the experts
This article is based in large part on contributions by STLE-member Thomas Scharf, professor, department of materials science and engineering, University of North Texas (scharf@unt.edu), and STLE-member Gary Doll, Timken professor of surface engineering, chemical and biomolecular engineering department, University of Akron (gdoll@uakron.edu).
Further reading
• In addition to a general review, Tribology and Applications of Self-Lubricating Materials (7) (CRC Press, 2017) focuses on composites and self-lubricating materials.
• ASM Handbook, Vol. 18: Friction, Lubrication, and Wear Technology (2017) includes an overview of the history, characteristics, processing methods and qualification of solid lubricants (1) and a discussion of lubrication in challenging conditions (8).
• Scharf and Prasad (3) provide an overview of research on lubrication mechanisms in solid lubricants as well as a detailed listing of 20 solid lubricants with their characteristics and applications.
• A classic resource on the mechanisms of solid lubrication is the 1942 Nature article Mechanism of Metallic Friction by Bowden and Tabor (2).
REFERENCES
1. Dugger, M.T. (2017), “Solid lubricants,” in ASM Handbook, Vol. 18: Friction, Lubrication, and Wear Technology, edited by G.E. Totten. Materials Park, Ohio: ASM International, pp. 191-206.
2. Bowden, F.P. and Tabor, D. (1942), “Mechanism of Metallic Friction,” Nature, August 15, pp. 197-199.
3. Scharf, T.W. and Prasad, S.V. (2013), “Solid Lubricants: A Review,” Journal of Materials Science, 48, pp. 511-531.
4. Van Rensselar, J. (2009), “Aerospace Lubricants: Solid is Essential in Every Sense,” TLT, 65 (6), p. 44.
5. DellaCorte, C. (2000), “The Evaluation of a Modified Chrome Oxide Based High Temperature Solid Lubricant Coating for Foil Gas Bearings,” Tribology Transactions, 43 (2), pp. 257-262.
6. Mutyala, K.C., Singh, H., Evans, R.D. and Doll, G.L. (2016), “Effect of Diamond-Like Carbon Coatings on Ball Bearing Performance in Normal, Oil-Starved, and Debris-Damaged Conditions,” Tribology Transactions, 59 (6), pp. 1039-1047.
7. Omrani, E., Rohatgi, P.K. and Menezes, P.L. (2017), Tribology and Applications of Self-Lubricating Materials, 1st ed., Boca Raton, Fla.: CRC Press.
8. Doll, G.L. (2017), “Lubricant Strategies for Challenging Environments,” ASM Handbook, Vol. 18: Friction, Lubrication, and Wear Technology, edited by G.E. Totten. Materials Park, Ohio: ASM International, pp. 213-219.
Jane Marie Andrew is a free-lance science writer and editor based in the Chicago area. You can contact her at jane@janemarieandrew.com.