Friction welding
R. David Whitby | TLT Worldwide May 2019
This modification could be used in many industrial applications.
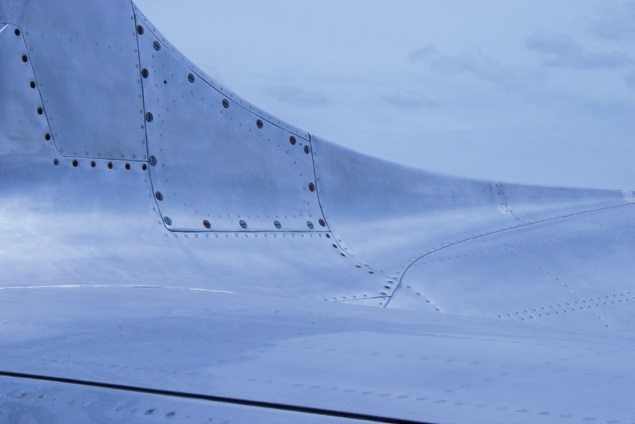
Rivets are still used widely, for example, in making planes and ships.
© Can Stock Photo / sparky2000
All tribologists know that friction can, in some circumstances, generate heat. This has been put to practical use in friction-stir spot welding. Individual spot welds are created by pressing a rotating tool with high force onto the top surface of two sheets that overlap each other where they are to be joined. The frictional heat and high pressure plasticizes the sheets so that the tip of the tool plunges into the joint area until the tool’s shoulder is in contact with the surface of the top sheet. The shoulder applies a high forging pressure which bonds the components metallurgically without melting. After a short dwell time, the tool is pulled out of the workpieces so that a spot weld can be made about every five seconds.
However, friction-stir spot welding has proved less successful in heavy industry because the welds are generally not as strong as either arc-welds or rivets. The rotating tool leaves an indentation in the weld, which, apart from being unsightly, could introduce a weakness. Although riveting is old fashioned as a method of joining two sheets, it produces very strong joints. Rivets are still used widely, for example, in making planes and ships.
A rivet is a mushroom-like stud with a cap and a stem. The stem is pushed through matching holes made in the two materials to be joined so that its end is proud. The proud end is then made into a second cap using a hammer or a rivet gun. Rivets can be made so that the cap on the outer side of the joint is flush with the surface.
An improved method of friction welding, called refill-friction-stir spot welding (RFSSW), is nearing commercialization by TWI (formerly the Welding Institute), an industry-funded laboratory near Cambridge, England, and Kawasaki Heavy Industries. The process uses a non-consumable tool comprised of two rotating components, a probe and a shoulder, assembled concentrically with a static clamp ring. The major improvement to this process, in comparison with the other friction-stir spot processes, is that the rotating elements have independent vertical movement. The RFSSW process has two variants, shoulder-plunge and probe-plunge, which depend on the plunging component.
As the weld cycle begins, the three components move to the surface of the top sheet and dwell for a certain amount of time to produce initial frictional pre-heating. For the shoulder-plunge variant, the shoulder is the plunging component to a set depth into the base material. At the same time, the probe retracts to create a chamber for the displaced material to flow into. During the plunge stage, the friction on the shoulder causes the material to heat and soften. For the probe plunge variant, the principle is similar but the probe is the plunging component. Then the rotating components return to the surface of the top sheet whilst rotating and the previously retracted component consolidates the weld material by offsetting the positions from the previous stage. The weld cycle finishes by extracting the tool from the surface of the material.
RFSSW has been used mainly to join heat treatable aluminium alloys, without and with surface protection, for example, anodized or coated. Dissimilar combinations between aluminium and other engineering materials, such as magnesium, steel, titanium, copper and carbon fiber composites, also have been joined successfully. It also is possible to weld polymers and polymer composites.
As a single-spot welding process, RFSSW is an alternative solution to replace mass-adding fastening processes, such as rivets, and to address challenging material combinations for fusion spot welding processes. Although this technology is only currently being used for research and development applications, possible industrial sectors for this technology include panels for decks, sides, bulkheads and floors in ships and skin/stringer applications and fuselage and wing structures in planes. Applications in rail stock vehicle floor, side and roof panels, particularly for high-speed trains, and railway tankers and engine chassis cradles and car body structures in the automotive sector.
The modification to friction welding could drive refill-friction-stir spot welding into many industrial applications, because the result of the refill is not only stronger but smooth. This is crucial to the aerodynamics of planes, the manufacture of lightweight cars and the hydrodynamics of ships.
David Whitby is chief executive of Pathmaster Marketing Ltd. in Surrey, England. You can reach him at pathmaster.marketing@yahoo.co.uk.