Fundamentals of base oils
Dr. Nancy McGuire, Contributing Editor | TLT Webinars February 2019
A lubricant’s success depends on matching the right base oil to the application.
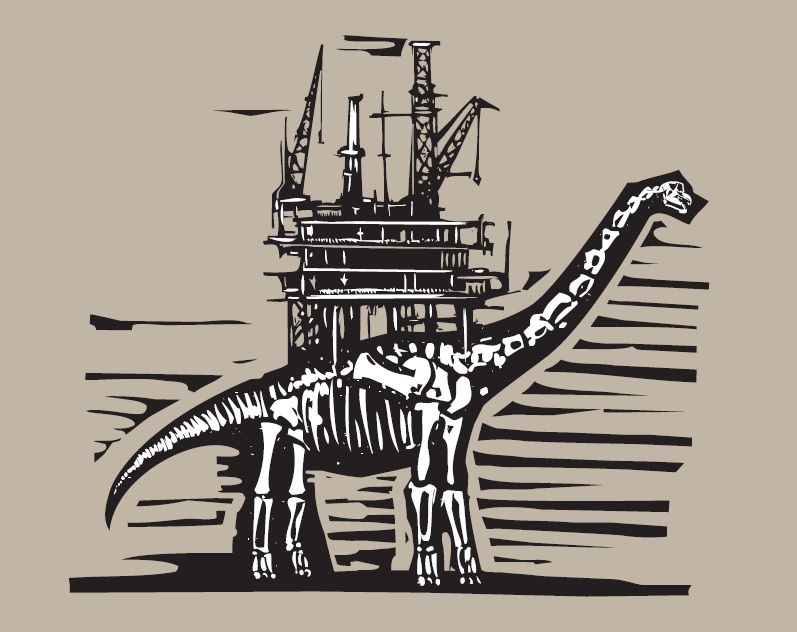
© Can Stock Photo / Xochicalco
KEY CONCEPTS
•
Crude oil compositions vary with their point of origin and history.
•
The ability to keep solid surfaces separated is what provides an oil’s ability to lubricate.
•
While paraffinic base stocks dominate today’s market, naphthenic mineral oils continue to play an important role in lubricant production.
MEET THE PRESENTER
This article is based on a Webinar presented by STLE Education on Feb. 14, 2018.
Fundamentals of Base Oils for the Lubricant Formulator is available at
www.stle.org: $39 to STLE members, $59 for all others.
David Turner is a product specialist with the Lubricants Fluid Technology group of CITGO Petroleum Corp. in Houston. He holds a bachelor’s of science degree in chemical engineering from Lamar University in Beaumont, Texas, and has more than 37 years of experience in the lubricants industry in formulation, manufacturing, selection, application and technical service of lubricants and greases.
Among the awards and honors Turner has received: the NLGI Clarence E. Earl Memorial Award, the ASTM Award of Excellence, the NLGI Meritorious Service Award, the NLGI Fellows Award, the NLGI Chevron Lubricants Award, the NLGI Shell Lubricants Award for Instructor Excellence, the ASTM Eagle Award and the NLGI Award for Achievement. He is an NLGI Certified Lubricating Grease Specialist, an STLE Oil Monitoring Analyst and an STLE Certified Lubrication Specialist.
You can reach Turner at
dturne3@citgo.com.
David Turner
A strong, stable, inert base oil is the platform on which lubricant additives ride—it provides the lubricating film and the minimum viscosity needed for effective lubrication. This article discusses mineral oil base stocks in API Groups I, II and III, and the naphthenic oils (which are in Group V).
A base stock is a lubricant component produced by a single manufacturer to one set of the manufacturer’s specifications, independent of feed source or manufacturer’s location. A specific base stock is identified by a unique formula, product identification number or both. A base stock slate is a product line of base stocks that have different viscosities but are in the same base stock group and from the same manufacturer.
Base stocks, as defined in API 1509 Appendix E: Engine Oils, may be manufactured using various processes. Some of these processes include distillation, solvent refining, hydrogen processing, oligomerization, esterification and re-refining. Re-refined stocks are substantially free from materials introduced through manufacturing, contamination or previous use.
Appendix E defines a base oil as the base stock or blend of base stocks used in an API-licensed engine oil. Oils for use in gasoline engines are 80%-85% base oil, and industrial turbine oils are to 98%-99% base oil (but there may be as many as 10 different additive components in the remaining 1%-2%).
From dinosaurs to distillates
Petroleum (crude oil) forms when heat and pressure transform decayed organic matter buried beneath Earth’s surface over millions of years into a liquid-gas mixture containing primarily hydrogen and carbon, with lesser amounts of oxygen, nitrogen, sulfur and other impurities (including metals). Crude oil compositions vary with their point of origin and history. Refining separates crude oil into its components, from which useful products can be made (
see Figure 1).
Figure 1. Refining separates crude oil into useful products.
In the U.S. market, about 90% of demand is for light products, the most volatile components of crude oil. (Gasoline makes up about half the demand for light products.) However, light fractions make up less than 60% of some crude oils. Heavier fractions are used to make lubricants, but typically a 42-gallon barrel of crude oil will yield only about a half-gallon of lubricant-quality oil (
see Figure 2).
Figure 2. How much lubricant base stock is in a barrel of crude oil?
The first step in the path from crude oil to marketable product is a desalting process to remove corrosive mineral salts from the oil–water mixture that comes from the oil well. This is followed by distillation, which separates the more volatile petroleum gas, gasoline, naphtha, kerosene and light gas oil from the less volatile atmospheric residuum (typically about 40% of crude oil). Crude oils have various distillation curves, depending on their composition (
see Figure 3).
Figure 3. Typical crude oil true boiling point versus yield.
Distillation at atmospheric pressure separates out the most volatile components; that is, the components that vaporize at lower temperatures. Raising the temperature separates out successively less-volatile components, but at temperatures above about 350 C the crude oil components begin to decompose rather than evaporate. To avoid this, the atmospheric residuum oil is distilled under vacuum to further separate the heavier oil fractions without thermally decomposing them.
To make API Group I base oils, distillation products are extracted using solvents to remove aromatic compounds and asphalt. Additional solvents and low temperatures crystallize and remove waxy components before the components go through a finishing process (e.g., hydroprocessing to give neutral base oils).
Types
API has defined several groups of oils according to their composition, properties and refining methods (
see Table 1). API Groups I, II and III are all paraffinic oils—they consist mainly of saturated hydrocarbons. These oils are refined from crude oils that are naturally high in paraffinic compounds (
see Figure 4).
Table 1. API Base Stock Categories
Figure 4. Molecular structures in base oils.
API Group I (conventional) base oils are the largest group of base oils in use worldwide, although their market share is shrinking. These oils are produced using older refining technology that involves vacuum distillation, followed by solvent extraction, dewaxing and finishing. This process is refining by subtraction: solvent extraction removes some 50%-80% of the aromatic species, and the dewaxing step removes high molecular-weight n-paraffins by chilling the oil to solidify them and then filtering them out. The remaining base oil still contains some unsaturated, polar and waxy compounds as impurities. Group I base oils are cost effective for making monograde engine oils, some heavier multigrade engine oils, industrial oils, greases and metalworking fluids.
Group II oils, introduced in the 1970s, became prevalent in the 1980s. Group II processes use no solvents and produce fewer waste byproducts. The refining process is similar to that for Group I oils, but instead of the solvent extraction steps, the vacuum-distillation step is followed by hydrocracking, catalytic dewaxing and hydrofinishing processes. Hydroprocessing reshapes 98%-99.99% of undesirable species into desired molecular structures rather than simply removing them.
Hydroprocessing uses hydrogen at more than 2,000 psi to convert aromatics into cycloparaffins (also called naphthenes) and waxes into high-quality isoparaffins (branched molecules). The process also converts sulfur and nitrogen into species that can be removed from the mixture. Compared with Group I oils, Group II base oils have a higher purity, better stability against oxidation and very low amounts of aromatics, sulfur, nitrogen and oxygen (
see Figure 5). Used lubricants can be re-refined to make high-quality Group II base oils, but the logistical limitations of collecting used oil often confines these products to regional markets.
Figure 5. Group I oils (top) have more impurities than Group II oils (bottom).
Group III base oils are produced using a more severe hydrocracking process. Their performance approaches that of Group IV oils. They are low in sulfur, and they can resist oxidation better than Group II oils. Despite the severe hydrocracking involved, these oils are less expensive to manufacture than the polyalphaolefins (PAOs) (but more expensive than Group II oils). An unofficial subcategory, the Group III+ oils, are made from high-purity wax feedstocks, and their properties are competitive with those of the PAOs. Gas-to-liquid (GTL) and coal-to-liquid (CTL) processes typically produce Group III base oils.
Group IV contains the PAO fluids. These oils are derived from chemical reactions of smaller molecules to produce lubricant-grade fluids. The viscosity indexes of these synthetic oils are similar to those of the Group III base oils.
Group V includes everything else not covered in the other groups. This includes naphthenic base oils and biobased oils that are derived from agricultural products (e.g., soy or canola). Naphthenic oils also are called pale oils because of their typically light color. Light, medium and heavy cuts are produced using atmospheric distillation, followed by vacuum distillation and severe hydrotreating. In some cases, the distillates are solvent extracted before the hydrotreating step to remove carcinogenic polycyclic aromatic species.
Naphthenic oils are made from crude oils that are naturally rich in naphthenic compounds, and they tend to be far less waxy and less viscous than highly paraffinic crude oils. This makes them easier to handle in the refinery.
Naphthenic base oils typically require less processing than paraffinic base oils. Their low wax content gives them naturally low pour points. However, these oils are more prone to oxidation and have poorer viscosity indexes and can be incompatible with elastomers. These oils generally have good solvency, and they can be blended with Group I or II base oils to further improve the solvency properties of those oils. Naphthenic oils are commonly used in greases, metalworking fluids, refrigeration compressor lubricants and low-temperature lubricants.
Base oil properties
Viscosity, an oil’s resistance to flow, is what provides the oil’s ability to lubricate and is the most important oil property. High temperatures reduce oil viscosity and low temperatures increase it.
Viscosity index (VI), a natural characteristic of an oil, is an indicator of how much the viscosity of an oil changes over a range of temperatures. For example, the viscosity of a Group I paraffinic oil with a VI of 90 will change more over a given temperature range than the viscosity of a Group III oil with a VI of 130. In general, heavier Group I oils have slightly lower VI values than lighter oils, Group II oils have directionally higher VI than Group I oils, and Group III oils have higher VI values overall.
Volatility is the tendency of a liquid to form a vapor at a given temperature. Liquids with higher molecular weights tend to be less volatile, and the vapor components must be raised to a higher temperature before they ignite in air (higher flash points). In low-viscosity engine oils, the same low-molecular weight compounds that reduce viscosity also can increase volatility. Because mineral base oils are mixtures of hydrocarbons, molecular weights are determined as an average or a range using nuclear magnetic resonance (NMR) or gas chromatography-mass spectrometry (GC-MS) analysis methods.
An oil’s oxidation and thermal stability—its ability to resist chemical and thermal decomposition—is determined by its hydrocarbon molecular structure. There is some correlation between viscosity and oxidative stability. Paraffins and isoparaffins are more stable than naphthenics, which are more stable than aromatics—that’s one reason aromatic compounds are removed during refining. Heterocyclic compounds, which contain chemical elements other than hydrogen and carbon, can be less stable than pure hydrocarbon compounds.
Group I bright stock has somewhat poorer oxidative stability than a lower-viscosity light or medium solvent-neutral paraffinic base oil. Group II base oils, which have lower aromatic, sulfur, nitrogen and other impurity levels, are more stable against oxidation, and thus tend to have a longer life, than Group I oils (
see Figure 6). Group III base oils have even fewer impurities, but their viscosities are too low for industrial applications like hydraulic fluids and gear oils. Oils in Groups II and III are so highly processed—and thus lower in the more reactive cyclic compounds and unsaturated hydrocarbons—that they are inherently more stable against oxidation.
Figure 6. Fewer impurities increase turbine oil life.
Hydrolytic stability is the ability of a lubricant (base oil and additives) to resist chemical decomposition in the presence of water. Mineral base oils typically resist hydrolytic decomposition well, but some of the additives used with them do not. Some synthetic base fluids (e.g., certain esters) are susceptible to hydrolytic decomposition.
Low-temperature performance is important for startup conditions, refrigeration equipment and cold weather operation. A base oil’s low-temperature properties vary depending on what components are in the mixture. Tests for low-temperature properties include pour point (the temperature below which an oil is no longer fluid), cold cranking simulator (CCS), miniature rotary viscometer (MRV) and Brookfield (rotary) viscometer tests.
Paraffinic base oils, even catalytically dewaxed oils, all contain residual wax. Unbranched paraffins have a high viscosity index, but they also have high melting points; that is, they are more likely to solidify at operating temperatures. Isoparaffins have branched molecular structures, and this impedes crystallization; these oils remain liquid at lower temperatures.
Naphthenic base oils are virtually wax-free, so they have inherently low pour points—a plus for the normally low operating temperatures in refrigeration compressors. However, these oils also have a lower viscosity index, and they become viscous more quickly as the temperature drops.
Solvency, the ability of one material to take another material into solution, is one measure of a lubricant’s compatibility. Lubricants often come into contact with rubber or synthetic polymer seals, gaskets and mechanical parts, so it’s important that these substances not degrade each other.
Some lubricants can extract chemical components from a polymer part. For example, lubricants that are incompatible with nitrile-butadiene rubber (NBR) can cause the plasticizer to migrate out of the rubber, causing the rubber to shrink and harden. Going the other direction, some lubricants can migrate into a polymer such as polychloroprene rubber (CR), causing the rubber to swell and soften.
The aniline point of a base oil is an indicator of its solvency. The aniline point is the lowest temperature at which equal volumes of oil and aniline (an aromatic amine compound) are miscible, using the ASTM D611 aniline point test method. More polar oils are more compatible with the polar aniline molecules, so the two components remain miscible at lower temperatures: these oils have greater solvency. Paraffinic base oils and PAOs have higher aniline points and correspondingly poorer solvency (
see Figure 7).
Figure 7. Highly polar oils have lower aniline point temperatures and greater solvency than less polar oils.
An oil’s viscosity gravity constant (VGC) is a dimensionless quantity based on mathematical processing of the oil’s viscosity and density values (ASTM D2501). This constant provides a weighted value that takes into account the viscosity effect on solvency and the chemical nature of the oil, which affects the density (
see Figure 8).
Figure 8. The viscosity gravity constant (VGC) takes into account an oil’s chemical nature and the effect of viscosity on its solvency.
High-solvency base oils provide several desirable properties in greases. Combining naphthenic and paraffinic oils can optimize the solvency to the desired level while keeping the cost down. High-solvency base oils require less thickener to produce the desired grease consistency, which improves the manufacturing yield. The grease soap fibers are more uniform in shape and size, producing a more homogeneous soap structure. Greases made with high-solvency base oils have a smooth texture, a glossy surface and a translucent appearance (
see Figure 9).
Figure 9. Higher-solvency base oils produce a more translucent grease (left).
Markets and trends
Base stocks provide an oil’s lubricating film and are the largest component of a lubricant formulation, so selecting the right base stock for a given application is important (
see Table 2). Paraffinic base stocks still dominate today’s market, and mineral oils continue to play an important role in lubricant production. While re-refined stocks are more available than they once were, their impact is still small.
Table 2. Base Oil Comparison
Hydroprocessing is the leading technology for producing oils in Groups II and III, and the markets for these base stocks are growing (most Group III oils are produced in Korea and the Far East). The market for PAOs (Group IV) and naphthenics (Group V) are holding their own, but the market for Group I oils is shrinking.