Salesman: The self-made super sleuth?
Dr. Robert M. Gresham, Contributing Editor | TLT Lubrication Fundamentals February 2019
The latex-glove manufacturer insisted his plant was OK and our product was the culprit.
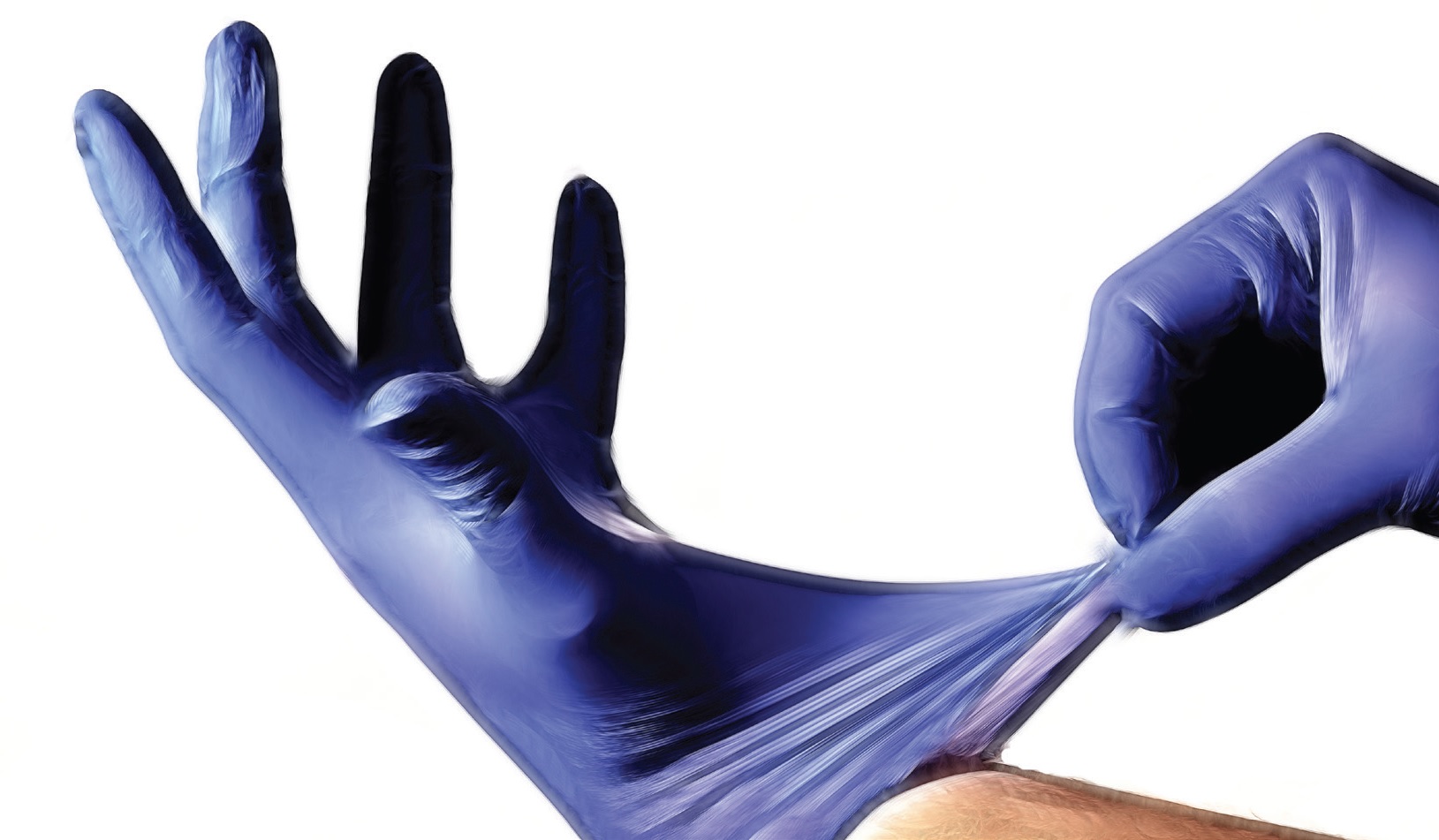
© Can Stock Photo / TheNikon
In our industry we are always talking about how multidisciplinary tribology is, requiring all of us to learn many new things on the job beyond what we learned in school. This is true whether you have a doctorate, master’s or bachelor’s degree or maybe no college degree at all. In fact, aside from schooling, sometimes our respective backgrounds and experiences need to be multidisciplinary as well.
When we confront problems in our industry we, hopefully one way or another, see the various real or potential facets of the problem. One obvious example is the way our auto folks look at the problem of maximizing fuel efficiency: engine and drivetrain, road-tire interface, aerodynamics, braking losses, driving habits (autonomous vehicles), etc. The list is pretty long, yet all need to be addressed as each one has a contribution. So it is with most of the problems we confront, especially when diagnosing problems with existing products and processes, especially in a customer’s operation.
In these circumstances, most often our first line of defense is the self-made super sleuth: the salesman. The salesman is usually the first to hear there is a problem and the first in the door to see the problem. I’m often impressed with the skills of experienced salesmen who become quite adept at sleuthing and equally can recognize when it is time to call in reinforcements.
As an example, back in my Dupont days I was technically responsible for our neoprene latex products. A senior salesman called me in, naturally on a Friday, to help with a customer who made neoprene latex gloves in high volume. When we got there the customer brought us into the conference room and spent about an hour taking the hide off our backs. They hadn’t been able to make decent gloves for almost two weeks. The customer guaranteed that everything was OK in their plant, processes and materials checked and double checked, all the operators had been questioned relentlessly, no one had made mistakes, etc. Therefore, of course, our latex had to be the culprit.
The salesman deftly managed to tie up the irate bosses in the conference room and get me free to walk around the plant, checking on things and talking to the people. Making latex gloves is a delicate controlled precipitation process where pH control is critical. Turns out they had only one operator who always calibrated the pH meter, partly because she was very good at it. About two weeks previously she went on vacation. I wasn’t entirely clear if anyone calibrated the meter, or did it incorrectly because the folks weren’t talking much, but one thing was clear—pH control was way off (I had brought my hand-held meter).
After calibrating the meter, like magic, the process started running normally. The point is that while checking the raw materials, equipment, operation of the equipment including running pH regularly as per the process, the culprit was not obvious, and it took a little sleuthing beyond the obvious to find the problem. Since people were in jeopardy of losing their jobs, I more or less kept to myself. The process ran well through the weekend, the calibration lady returned on Monday, and senior management was convinced that some mystical, magical, unexplainable chemistry had invaded their plant, but now all was well.
So when it comes to diagnosing friction and wear problems, especially with existing designs, our super sleuth salesman has to look at all aspects of the problem, not just the obvious. He has to think of it as a tribosystem and look to all aspects of what might affect this system. Usually the first step is to examine the worn parts and try to identify the type of wear. The problem is that we are not particularly consistent in our lexicon. Gear folks and bearing folks tend to use slightly different words for the same or nearly the same thing, which can lead to confusion.
It might be better to think in terms of causative forces even though these too can overlap or one cause can, over time, create a secondary cause. For example, is the wear the result of thermal damage, which can lead to oxidation or softening or deformation of the metal? Is the wear the result of mechanical damage? Is the wear the result of chemical damage? Or even the result of something like radiation? Then you might ask, do conditions exist in the tribosystem that might promote one of these degradation processes? If so, are there secondary degradation processes taking place? Then see if there are outward visible signs: scratching, cracking, discoloration, deformation, material transfer, etc. What are the inward signs identifiable by various lab analyses? Finally, be sure the equipment is operated as designed, measurements are accurate (yes and calibrated), etc. What about human error?
This is a lot to ask of our first line of defense, the often-self-made super sleuth salesman. This also is why STLE’s certifications are important—they document that our super sleuth has a better-than-average chance of winning the day.
Bob Gresham is STLE’s director of professional development. You can reach him at rgresham@stle.org.