The tribology of music
R. David Whitby | TLT Worldwide January 2019
Oil and grease play an instrumental role in perfecting each note.
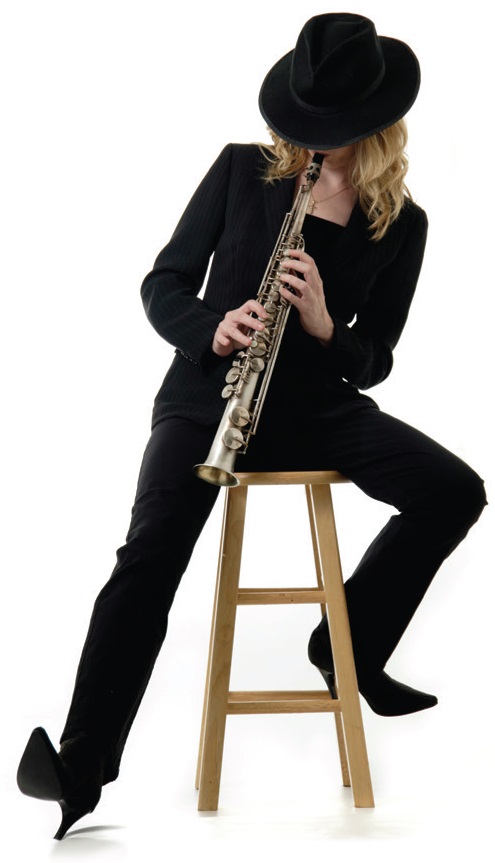
© Can Stock Photo / geotrac
The places and activities in which the science of moving surfaces appear never ceases to amaze me. The latest revelation is with musical instruments and musicians.
With stringed instruments, such as violins and cellos, drawing a bow across the strings causes them to vibrate. The vibration is transmitted through the bridge and sound post to the body of the instrument, allowing the sound to effectively radiate into the surrounding air. The tension and type of strings, placement and tension of the sound post, quality of the bow and construction of the body all contribute to the loudness and tonal quality of the sound.
The strings are stretched across the bridge and nut of the instrument so that the ends are essentially stationary. The vibration creates standing waves and the fundamental frequency and harmonic overtones of the resulting sound depend on the material properties of the string such as tension, length, mass, elasticity and damping factor.
Increasing the tension on a string results in a higher frequency note. The strings are wrapped around adjustable tuning pegs, so each string may be loosened or tightened until it produces the desired pitch, which may be described in terms of frequency. The length of the string also influences its pitch. Musicians stop a string with a left-hand fingertip, shortening its playing length and thereby increasing its pitch. The string is usually stopped against the instrument’s fingerboard, but in some cases fingertip contact alone is enough to stop the string at the desired sounding length.
A vibrating string does not produce a single frequency. The sound may be described as a combination of a fundamental frequency and overtones, which form the sound’s timbre. Strings were originally made from catgut, but modern strings are made of steel, stranded steel or a variety of synthetic materials. Strings are generally helically wound or “overspun” with metal to keep their thickness within comfortable limits as well as to control their surface friction properties.
String vibration is generally provided by a bow consisting of a flat ribbon of parallel horse hairs stretched between the ends of a wooden, fiberglass or carbon-fiber composite stick. The hair is coated with rosin to provide controlled stick-slip as it moves transversely to the string. Different types of rosin are available, providing varying amounts of grip or static friction.
Contrary to the controlled stick-slip friction required for stringed instruments is the smooth sliding friction required for brass and woodwind instruments.
Trumpets, saxophones, tubas, flutes, clarinets and similar instruments use valve oils and key oils to ensure effortless action as their mechanisms are pressed and released frequently. Trombone slides are lubricated with either slide oil or slide cream. French horns have a rotary valve that requires oil. Most brass instruments have a turning slide that is maintained in position once it has been adjusted. This requires a grease. Many woodwind instruments require a “cork grease” for their assembly and disassembly and to keep cork linings moist and provide long life. These oils and greases must, of course, have no odors, stains, residues or toxicity. More important, they must provide the low friction that musicians expect.
Modern brass and woodwind instruments have very tight tolerances, usually around microns. Consequently, valve oils are low viscosity, white oil based with kinematic viscosities at 40 C between 2 and 4 centistokes (cSt). Ball joints, key levers and other mechanisms require oils with kinematic viscosities of up to 70 cSt. The oils and greases must be compatible with brasses, Monel and/or stainless steel, as well as glues, plastic and rubber parts and seals. Many of the latest oils and greases use polyalphaolefin base oils.
Each musician selects the oil or grease that most suits the instrument they play and the way in which they play it. Some musicians fine tune the oils or greases they use by mixing components such as commercial valve oil, anhydrous lanolin and kerosene to meet their individual preferences. Some use oils derived from plants.
Of course, some older brass instruments do not have valves or slides that require lubrication, although they are more difficult to play.
David Whitby is chief executive of Pathmaster Marketing Ltd. in Surrey, England. You can reach him at pathmaster.marketing@yahoo.co.uk.