Effective use of organomolybdenum additives in lubricants
Dr. Nancy McGuire, Contributing Editor | TLT Webinars November 2018
These versatile and non-toxic chemistries solve difficult friction problems and enhance the performance of other additives.
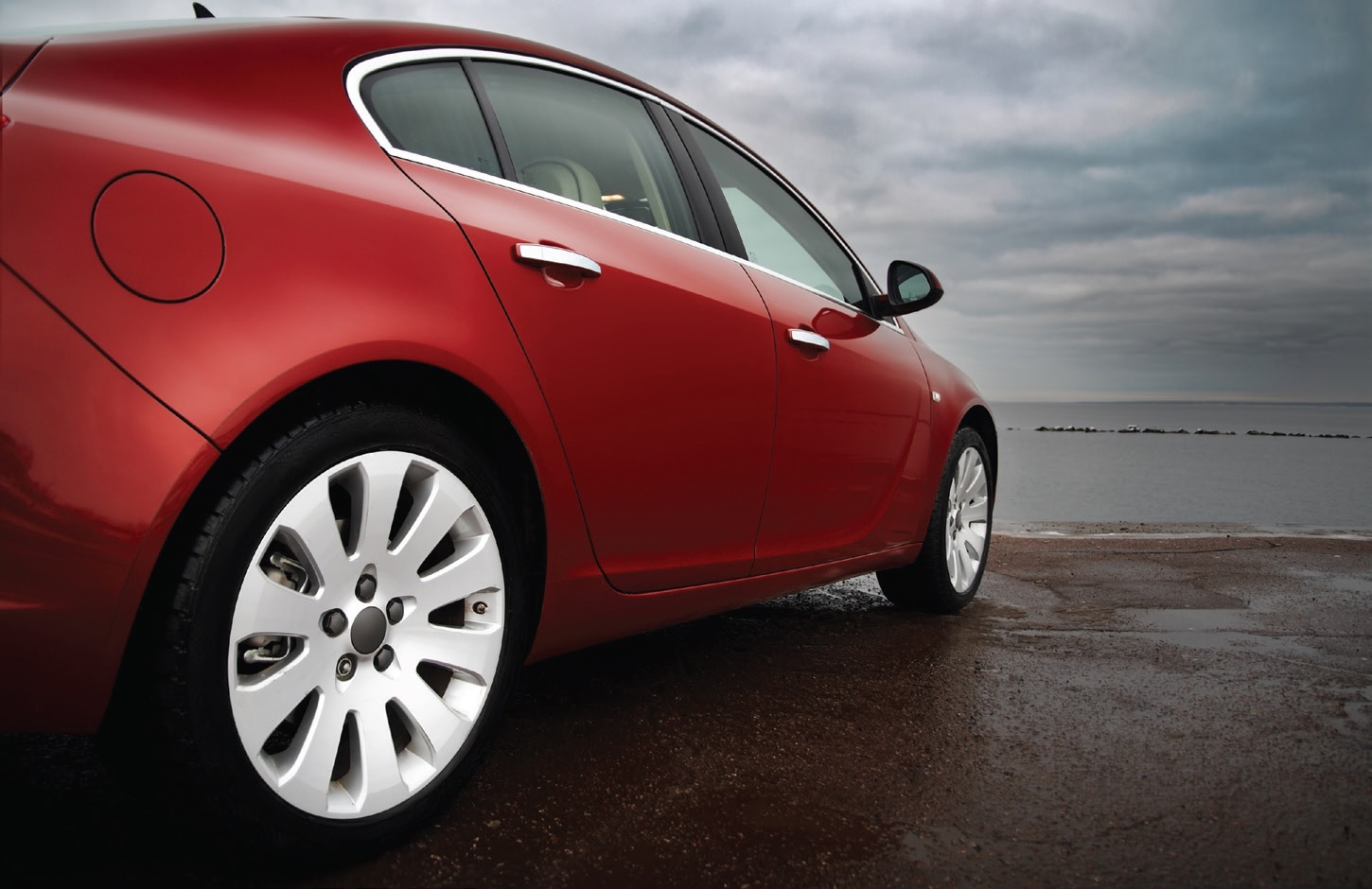
© Can Stock Photo / mtoome
KEY CONCEPTS
•
Molybdenum’s versatile chemistry lets it serve a variety of functions and helps make molybdenum compounds more soluble in lubricant formulations.
•
Molybdenum compounds can produce beneficial synergistic effects in properly formulated additive packages and lubricants.
•
Molybdenum and its compounds do not poison or leave deposits on automotive exhaust catalysts.
MEET THE PRESENTER
This article is based on a Webinar presented by STLE Education on June 28, 2017. Effective Use of Organomolybdenum Additives in Lubricants is available at www.stle.org: $39 to STLE members, $59 for all others.
Dr. Vincent Gatto has worked for 32 years as a research, applications, technical service and product-development scientist in lubricant, fuel and polymer additives. He is research director for Vanderbilt Chemicals, LLC (Norwalk, Conn.), where he is responsible for the management and strategic direction of a team of synthetic organic chemists. His team works on the discovery and development of new chemicals for use as additives in the lubricant, rubber and plastics industries. He also directs and prioritizes projects in the petroleum applications laboratory.
Gatto received his doctorate in chemistry from the University of Maryland and held a postdoctoral position at the University of Miami. He joined the staff at Ethyl Corp. (now Afton Chemical Co.), where he worked for 16 years as a technical service advisor and additive scientist. He then worked for 11 years as an R&D technical service manager at Albemarle Corp. before starting work at Vanderbilt.
Gatto holds 125 U.S. patents, patent applications and technical publications in the areas of chelation additives and additives for polymers, lubricants and fuels. He has delivered numerous presentations on the applications of additives in industrial fluids and engine oils.
You can reach Gatto at VGatto@vanderbiltchemicals.com.
Vincent Gatto
Organomolybdenum lubricant additives solve a wide range of lubrication challenges. In greases and engine oils, these additives have a track record of reducing friction and improving fuel economy, but there are many more applications. Their multifunctional and synergistic nature delivers true value. They are cost-effective when used properly, and they are effective even at low treat rates. Molybdenum technology is sustainable: this transition metal is not only non-toxic, it serves as a micronutrient in living organisms. Molybdenum additives also are compatible with passenger car catalyst systems.
All about molybdenum
Molybdenum is a very versatile element. Its abundance in the Earth’s crust is similar to that of tin, tungsten and lead. This transition metal forms ions and compounds with an oxidation state ranging from -2 to +6 and it bonds with 4-6 other atoms in coordination compounds. Molybdenum compounds have a wide variety of stereochemistries and reactivities, and molybdenum can form compounds with most organic and inorganic ligands. This is useful for overcoming solubility challenges associated with incorporating Mo effectively into a lubrication system.
Molybdenum has an extensive sulfur chemistry. Sulfur is an important lubricant component in its own right, and molybdenum compounds that include sulfur often exhibit beneficial properties from both elements.
Molybdenite (MoS
2), the principle ore form of molybdenum, is readily available as an important industrial catalyst as well as a lubricant additive. Molybdenite can be roasted in air to form molybdenum trioxide. This oxide can be reacted with an aqueous solution of either sodium hydroxide or ammonia to form Na
2MoO
4, (NH
4)
2Mo
2O
7 or (NH
4)
6Mo
7O
24, which can react more easily with organic ligands and solubilize more easily in a lubricant system. These compounds serve as the basis for further reactions to form organomolybdenum compounds.
Molybdenum in lubricants
Molybdenum provides effective solutions to a variety of difficult lubricant formulation problems. Small amounts can produce large benefits without detrimental side effects. Organomolybdenum additives can serve several functions at once: antioxidancy and deposit control; antiwear and extreme pressure performance; and friction reduction, which improves fuel economy (
see Figure 1). Further, these compounds can work synergistically with other additives, including antioxidant and antiwear additives, to provide more effective lubricant and machinery protection. Organomolybdenum additives can deliver significant improvements in performance at low treatment levels, and they are compatible with automotive catalyst and emission control systems.
Figure 1. Applications of organomolybdenum in lubricants. (Figure courtesy of Vanderbilt Chemicals, LLC.)
In the late 1960s, the Vanderbilt Co. became the first to patent many of the molybdenum lubricant additive technologies still in use today, and other companies have gotten into the field since then. A recent patent search shows that 67% of patents for molybdenum oils and fluids are for grease applications, 15% are for engine oil applications, and the remainder are for hydraulic, gear, transmission, transformer, turbine, metalworking and compressor fluid applications.
Engine oil applications commonly use liquid molybdenum dithiocarbamate (MoDTC) or liquid molybdenum ester compounds. The choice of organic ligands used to make the MoDTC determines whether the product is liquid or solid; compounds with longer and branched organic chains are more likely to be liquid at ambient temperatures. MoDTC is phosphorus-free, and it contains alkylamine groups that give it excellent solubility in oils. Molybdenum esters contain neither phosphorus nor sulfur; these compounds also serve as antioxidants, antiwear agents and friction modifiers. Molybdenum esters have low toxicity, are biodegradable and are a relatively low-cost source of molybdenum (
see Figure 2).
Figure 2. Molybdenum products for engine oils. (Figure courtesy of Vanderbilt Chemicals, LLC.)
Solid MoDTC has a low solubility in oil, but it is commonly used in greases because it can be dispersed relatively easily. Because the solid MoDTC compounds use smaller organic ligands, molybdenum forms a higher percentage in these compounds, and less additive can be used to provide the same benefits. Both solid and liquid MoDTC serve as antioxidants, antiwear agents and friction modifiers, but the solid form also is an extreme pressure agent. Solid MoDTC is superior to inorganic molybdenum compounds (e.g., MoS
2) for antioxidant and antiwear performance.
Liquid molybdenum dithiophosphate (MoDTP) compounds are dark green to brown liquids that have excellent oil solubility. These compounds are used in greases, and their molybdenum, sulfur and phosphorus components all provide benefits. MoDTP compounds have antioxidant, antiwear, extreme pressure and friction modifier properties (
see Figure 3).
Figure 3. Molybdenum products for grease. (Figure courtesy of Vanderbilt Chemicals, LLC.)
Improving performance
Antioxidant additives, including molybdenum compounds, are used to reduce the rate of lubricant oxidation and, thus, delay or prevent lubricant degradation that leads to wear, sludge and deposits (
see Figure 4).
Figure 4. How sludge, varnish and deposits form. (Figure courtesy of Vanderbilt Chemicals, LLC.)
Organomolybdenum additives can be used to control oxidation and deposits in engine oils, and their effectiveness is based on their synergistic effects with other additives, including alkylated diphenylamines or sulfur compounds. Organomolybdenum additives can be effective at fairly low levels (50-150 ppm delivered Mo), but their ability to control deposits is very system dependent; at very high temperatures they can actually promote deposit formation. The mechanism of action of these additives as antioxidants is not well understood.
High levels of molybdenum additives like MoDTC and molybdenum esters can sometimes induce corrosion in engine oils, but combining these additives with novel triazole corrosion inhibitors (a relatively new technology) can almost eliminate the corrosion problems caused by high levels of Mo additives (
see Figure 5).
Figure 5. Triazole corrosion inhibitors (new triazole CI) can almost eliminate copper and lead corrosion products caused by high levels of Mo additives in engine oils. DMTD = dimercaptothiadiazole. (Figure courtesy of Vanderbilt Chemicals, LLC.)
Molybdenum compounds are primarily used as antiwear (AW), friction modification (FM) and extreme pressure (EP) additives in engine oils and greases. These compounds act synergistically with other additives, including zinc dialkyldithiophosphates (ZDDP) and sulfurized EP additives. Compounds that have both molybdenum and sulfur in their chemical makeup can function in all three modes: AW, FM and EP. Organomolybdenum compounds can be effective in this capacity at 25-1,200 ppm Mo in engine oils and 400-5,000 ppm Mo in greases.
Fuel economy, which comes from friction reduction, is one key driver encouraging the use of molybdenum additives in engine oils. These additives are especially effective at reducing friction in the boundary and mixed lubrication regimes (
see Figure 6).
Figure 6. Molybdenum-based additives in engine oils reduce friction in the boundary and mixed lubrication regimes. (Figure courtesy of Vanderbilt Chemicals, LLC.)
Various organomolybdenum additives reduce friction using different mechanisms. For example, MoDTC, which is more effective in fresh oils, decomposes to the layered inorganic solid MoS
2. Under high temperatures and loads, MoS
2 forms stacked sheets in the tribofilm, which can easily slide past each other under shear. Oxidation of the MoS
2 sheets causes them to fragment, resulting in a loss of friction-reduction properties. The oxidation product, MoO
3, is not an effective friction modifier. Molybdenum esters act through an adsorption and decomposition mechanism, and these compounds are more effective in aged oils. Organomolybdenum friction-reducing additives are generally effective at 300-1,200 ppm delivered Mo, which is a higher level than is used for antiwear and antioxidant properties.
Molybdenum compounds can be used in combination with a variety of other compounds to produce synergistic effects; that is, the total measured effect is greater than the sum of effects for each compound independently. The performance of these additives is highly dependent on the composition of the finished fluid, however. They can have antagonistic effects when they are combined with other surface additives like ZDDPs or organic friction modifiers if the fluids are not formulated properly. Proper formulation also is essential to preventing compatibility problems with other additives, including organic friction modifiers and for preventing corrosion at high additive levels.
Some molybdenum-based additives have limited solubility, especially in high quality base fluids (
see Figure 7). Newer technologies, which use highly branched alkylamines, can improve solubility across a wide range of additive levels and base oils (
see Figure 8).
Figure 7. Newer fluid technologies, including highly branched amine additives (left), can improve the solubility of molybdenum-based additives over older amine technologies (right) across a wide range of base oils and additive levels. (Figure courtesy of Vanderbilt Chemicals, LLC.)
Figure 8. Symmetrical, branched amine compounds keep molybdenum-based additives in solution in engine oil, even after 90 days. (Figure courtesy of Vanderbilt Chemicals, LLC.)
Grease additives
Molybdenum-based additives, when added at levels of a few percent, increase EP performance in greases, as well as reduce friction and wear (
see Figure 9). Friction measurements using a mini-traction machine (MTM) for a lithium complex grease with 2% of a liquid MoDTC additive containing 10% molybdenum showed that the additive reduced friction best at higher temperatures (120 C versus 60 C).
Figure 9. MoDTP grease additives improve EP performance. (Figure courtesy of Vanderbilt Chemicals, LLC.)
Well-designed formulations that combine molybdenum additives with other additives, including ZDDP and dimercaptothiadiazole (DMTD) dimer complexes, can significantly improve overall results with respect to friction reduction and load-carrying capability (
see Figure 10). Tests using constant velocity joints have demonstrated the benefits of using additive combinations to improve grease performance (
see Figure 11).
Figure 10. Combinations of additives can reduce the coefficient of friction (CoF) and increase the load-carrying capability (higher weld point) of grease formulations. (Figure courtesy of Vanderbilt Chemicals, LLC.)
Figure 11. The right additive combinations can significantly improve the friction-reducing capability of a grease formulation. (Ca salt of ox. wax is a soap used in grease formulations.) (Figure courtesy of Vanderbilt Chemicals, LLC.)
Engine oil additives
As versatile as molybdenum is for grease applications, it has even more applications in engine oils. Molybdenum-based engine oil additives are used for controlling oxidation and deposit formation, reducing friction and wear and improving fuel economy.
Molybdenum ester compounds can act synergistically with antioxidants like alkylated diphenylamines (
see Figure 12). Combining these additives postpones the onset of oil oxidation, and it helps keep aged oils from becoming more viscous (a sign of oxidation). Figure 13 shows the benefits of organomolybdenum additives for controlling deposits that can form when oils oxidize.
Figure 12. Measurements of oxidation induction time (OIT) by pressurized differential scanning calorimetry (left), and increase in viscosity (right) show that a combination of molybdenum ester and alkylated diphenylamine (ADPA) additives works better than either additive alone. (Figure courtesy of Vanderbilt Chemicals, LLC.)
Figure 13. The TEOST® MHT test is a specification test for engine oils that measures deposit formation on a standardized rod. (NDPA and ODPA are alkylated diphenylamines.) (Figure courtesy of Vanderbilt Chemicals, LLC.)
Molybdenum additives also act synergistically with other AW additives, including various phosphate compounds. Additive combinations, without ZDDP, can significantly reduce scuffing and wear (
see Figure 14).
Figure 14. MoDTC and an ashless thiophosphate (ASP) act synergistically to reduce camshaft wear and tappet scuffing (high figure of merit indicates less scuffing). (Figure courtesy of Vanderbilt Chemicals, LLC.)
Timing chain elongation, an indicator of wear, is one test for compliance with the GF-6 specifications for passenger car motor oils. The presence of zinc actually increases chain elongation, but molybdenum significantly reduces elongation. Combining zinc and molybdenum additives produces an even greater reduction as molybdenum cancels out negative effects of zinc (
see Figure 15).
Figure 15. Effects of high (H) and low (L) levels of molybdenum ester- and zinc-based additives on timing chain wear shows that a combination of additives produces a synergistic effect. (Figure courtesy of Vanderbilt Chemicals, LLC.)
Molybdenum additives also act, alone or in combination with other additives, to reduce friction. The proper formulation is key to achieving the greatest reduction in the coefficient of friction, and different additives can be more effective for fresh or aged oils.
Additive combinations can be better than single additives at reducing friction across a range of conditions. For example, liquid MoDTC keeps friction low in fresh oils and oils at elevated temperatures. Most commercially available MoDTC types lose their effectiveness in aged oils, but molybdenum ester additives excel in aged oils and at elevated temperatures. Glycerol mono-oleate, an organic compound with no metal, sulfur or phosphorus, functions best in fresh oils at low temperatures but loses its effectiveness rapidly as the oil begins to age (
see Figure 16).
Figure 16. Liquid MoDTC (green line) keeps friction low in fresh oils, while a molybdenum ester additive (purple line) excels in aged oils. (Figure courtesy of Vanderbilt Chemicals, LLC.)
Oxidation prevention, maintaining the proper viscosity and reducing friction all contribute to improving vehicle fuel economy. Here again, getting the formulation right is key. For example, molybdenum and phosphorus can be antagonistic, but using low levels of phosphorus for a given molybdenum concentration can improve the reduction in fuel consumption by enhancing the performance of molybdenum. Low-phosphorus, high-molybdenum (LPHM) formulations are being developed to push the envelope for fuel economy contributions from next generation oil formulations (
see Figure 17).
Figure 17. LPHM lubricant formulations are being developed to increase fuel economy. (Figure courtesy of Vanderbilt Chemicals, LLC.)
More recently, molybdenum additives have been shown to reduce low-speed pre-ignition (LSPI), a problem that occurs in newer engines using turbochargers and direct injection, in which the fuel ignites before the spark plug is triggered. Reducing LSPI is of particular interest in light of GF-6 specifications and is likely to gain importance in future specifications. Both phosphorus (ZDDP) and molybdenum (MoDTC) have been shown to reduce LSPI frequency while calcium increases it.
Unavoidably, a small amount of engine oil finds its way into a vehicle’s exhaust system. Fortunately molybdenum additives in passenger car engine oils do not poison catalytic converters. In one study, several Las Vegas taxi cabs using either a GF-5 oil formulation or a newer LPHM formulation were put through field trials. At the end of the test, the exhaust catalysts contained deposits of phosphorus, calcium and zinc. Molybdenum levels were essentially zero for both formulations even though both oils contained a relatively high level of molybdenum. Phosphorus deposits on catalysts exposed to the LPHM formulation (42 g/cubic foot) were less than one-third of the level for the GF-5 formulation (158 g/cubic foot), probably because the phosphorus level in the LPHM oil was lower to begin with. Calcium deposits were about one-third higher for the LPHM formulation (46 g/cubic foot) than for the GF-5 formulation (36 g/cubic foot).
In addition, tests show that molybdenum allows the catalyst to “light off” (oxidize exhaust emissions like diesel soot) at a lower temperature than for the untreated base oil or other fuel-soluble metals including strontium and manganese. This effect would allow the catalyst to operate more efficiently.
A versatile, effective element
In summary, molybdenum additives can solve a wide range of lubrication challenges because of their multifunctional nature and their synergistic behavior with other additives. In a properly formulated lubricant, these additives are cost effective, and they can be extremely effective even at low treat rates. Molybdenum-based additives are nontoxic and compatible with automotive catalytic converters.