Maintaining lubricant quality throughout the supply chain
Dr. Nancy McGuire, Contributing Editor | TLT Webinars October 2018
How to avoid potholes in the long, complex road from raw materials to customer delivery.
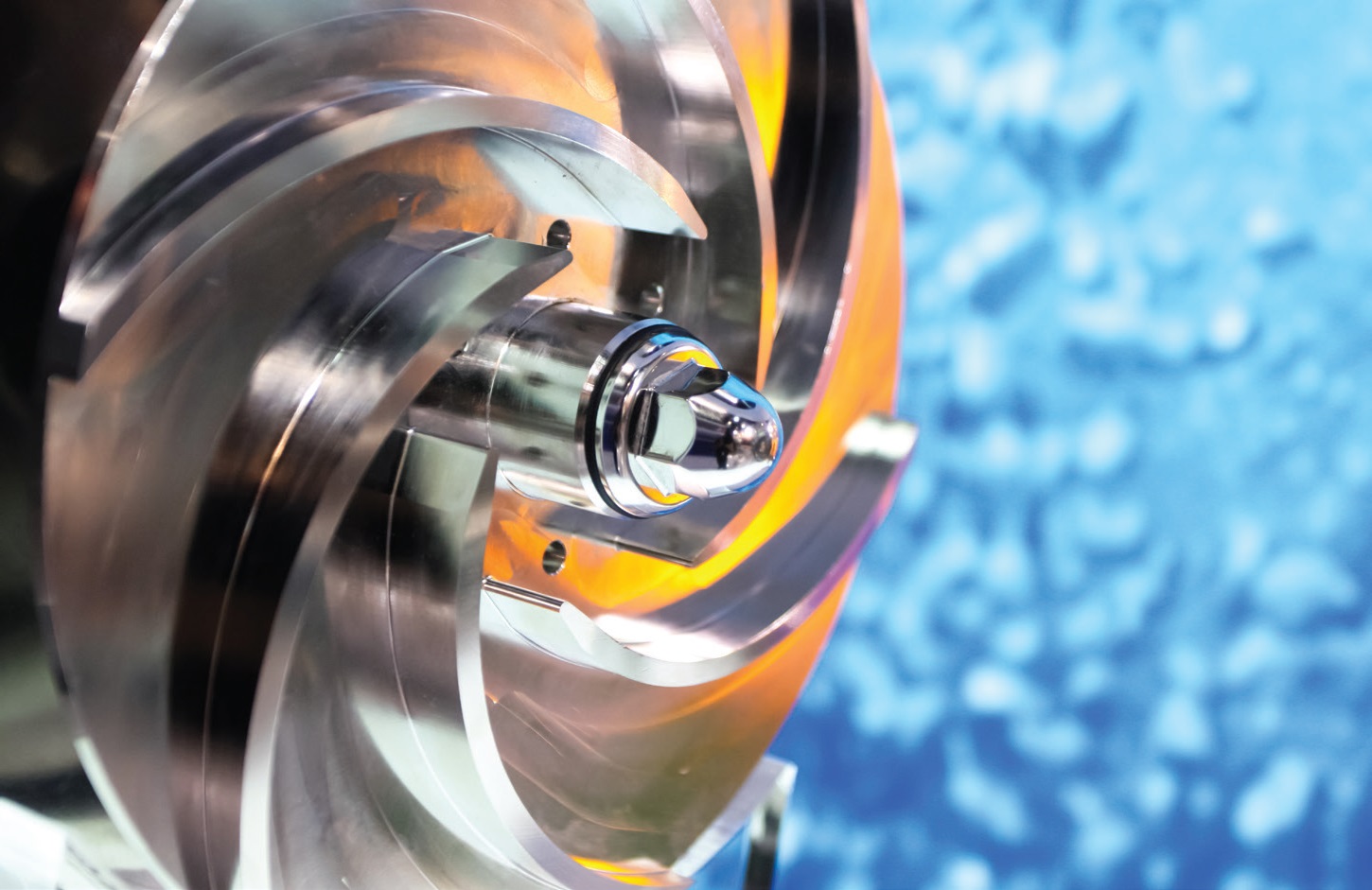
© Can Stock Photo / onizu3d
KEY CONCEPTS
•
Delivering the right lubricant up to standards requires following documented procedures and paying attention at every step of the process.
•
Clean, well-maintained containers and handling equipment prevent cross-contamination and introduction of substandard products.
•
Engaged managers and trained, motivated employees are critical to maintaining high quality standards.
MEET THE PRESENTER
This article is based on a Webinar originally presented by STLE Education on Oct. 26, 2016.
Maintaining Lubricant Quality throughout the Supply Chain is available at
www.stle.org: $39 to STLE members, $59 for all others.
Michael Roe has a bachelor’s of science degree in chemistry from Creighton University in Omaha, Neb., and a master’s of business administration from the University of Nebraska Omaha. He has worked in the lubricants industry for more than 40 years. His experience includes working as a lab technician and lab manager for Witco and its predecessor companies; an automotive product engineer, additive supply coordinator and industrial product engineer for Texaco and its subsequent Equilon Enterprises alliance with Shell Oil; and a technical help desk engineer, products technical advisor and distributor quality advisor for ExxonMobil, where he worked until 2015. He is currently working as a consultant. Roe is a member of STLE (and the current chair of the STLE Houston Section) and is a past member of ASTM and SAE.
Roe thanks J.A.M. Distributing of Houston for the use of photos and feedback on the Webinar content. You can reach Roe at
mjroe2@gmail.com.
Michael Roe
Delivering lubricants is not like delivering bread. If a bakery delivers the wrong kind of bread to a customer, the consequences are less drastic and more easily fixed than if a lubricant distributor puts extended-drain engine oil into a customer’s turbine oil tank.
Lubricant handling is challenging; each lubricant on the market is a complex mixture that has been formulated for a specific application. In addition to getting the type of lubricant right, a supplier must handle each lubricant properly. Handling multiple lubricants using common systems increases the risk of commingling and contamination. The supplier must have systems and processes in place to avoid commingling various kinds of lubricant products or contaminating a lubricant with non-lubricant products in the supply chain.
A lubricant supply chain consists of customers, lubricant manufacturers, raw materials and component suppliers, intermediaries and various types of equipment, processes and activities. The quality of lubricant handling is only as good as the training, knowledge and experience of each of the persons involved in every step of this chain.
Quality is the only way to do business; it’s a key element in maintaining a supplier’s reputation and brand image. Maintaining quality leads to reduced cycle times and costs, and it eliminates errors and rework. But it’s up to the customer to define what constitutes quality—a delivery is only successful if the customer is satisfied.
Quality objectives are documented and measurable. These objectives should be communicated to and implemented on all organizational levels. They should be reviewed on a timely basis, reinforced at periodic meetings and, where appropriate, these objectives should be communicated to the customer.
The lubricant supply chain
The process starts when a customer needs a lubricant for a specific purpose, and it ends when the customer is satisfied with the performance of the lubricant over its service life. So what happens in between?
Manufacturers often obtain product raw materials and packaging components from other suppliers, from which they make bulk or packaged products. In the simplest supply chain, a manufacturer makes a product and ships it directly to the customer. Often, however, multiple manufacturers send multiple products to multiple customers, with or without multiple intermediaries (
see Figure 1).
Figure 1. The supply chain process. (Figure courtesy of Michael Roe.)
Customers must accurately define their specific needs and quality expectations. Meeting customer expectations requires providing a lubricant that passes laboratory tests, bench tests and testing in relevant end-use equipment. It also requires the lubricant to be certified, qualified or licensed to meet the necessary requirements according to standards set by the API, SAE, DIN or OEM.
Manufacturing issues
Manufacturing is the first step in the supply chain. Manufacturers must have a set of specifications for raw materials and finished products and an accurate way to ensure that these specifications are met consistently. Quality assurance measuring equipment (scales, meters, thermometers, pressure and torque gauges and laboratory test equipment) must be accurate, calibrated, monitored and maintained. Manufacturing processes must stay within the appropriate temperature ranges, particularly for solubilizing oil additives and for manufacturing greases.
Adverse incidents are especially likely during a change of assignment—that is, switching from one product to a different one at any stage of the supply chain. Products must be manufactured either in dedicated vessels or using suitable change-of-assignment procedures to reduce or eliminate carryover between batches.
The best manufacturing processes are of limited use if the lines, pumps, meters and valves used to transfer the products are not held to the same high standards. Transfer equipment comes into play at every stage: bulk receiving, storage, packaging, loading and delivery.
Keeping products segregated
Lubricant products must be designed to resist—and avoid causing—adverse effects from commingling and contamination. Compatibility is a measure of a lubricant’s ability to resist these effects. It’s not possible to make every lubricant compatible with every other lubricant, so sorting products into groups and identifying them using a numbering system or bar coding is necessary to keep compatible lubricants together (and segregated from non-lubricant products) (
see Figure 2a-f).
Figure 2. A typical supply chain contains numerous kinds of lubricant and non-lubricant products, which must be kept segregated from each other. (Figure courtesy of Michael Roe.)
Making a lubricant that is completely impervious to commingling and contamination effects while still performing effectively in its intended application is difficult. Complicating factors include environmental claims (low aquatic toxicity, biodegradability); food grade claims (NSF H1); ashless, zinc-free or active sulfur chemistry; use of emulsifiers or demulsifiers; and dyes.
Using commercial product names to identify products for ordering or use in specific applications can be tricky since some lubricants have very similar names. Some product names don’t reveal much relevant information about the lubricant, and sometimes lubricants are commonly referred to using uninformative abbreviations and acronyms.
All lubricant handling equipment should be labeled with the exact name of the product (XYZ Brand ILSAC GF-5/API SN SAE 0W-30) or product group (passenger car engine oils) rather than abbreviations, acronyms or other informal references (30-weight) to avoid confusion. Using an accurate, informative naming system helps to ensure that the product a customer orders completely matches the name on the customer order, transport compartment or package identification; the product that is actually delivered; and the product name that the customer uses for storage.
Batch/lot traceability
A key factor in maintaining quality throughout the supply chain is the ability to trace a lubricant from its source to its final destination. This is done by assigning batch, lot or fill codes to bulk receipts, packaging or loading and delivery. Equally important is a user’s ability to interpret the supplier’s codes to determine the age of the product and spot any shelf-life issues.
In addition to tracking the materials themselves, supply chain managers must create and maintain detailed, documented procedures for activities including manufacturing the products, loading them at the supplier end, receiving them at the customer end, storing, packaging of bulk products and product transfers that occur during each of these activities.
Tracking procedures must take into account all activities at various steps in the supply chain. For example, when suppliers combine more than one lot or batch number of a lubricant into a single bulk container, this creates a new batch or lot. It’s essential to keep track of all the products that went into the container by taking samples before and after mixing and keeping records on those samples.
Packaging issues
Product identity must be maintained when a product is repackaged (transferred, e.g., from a drum to a pail, intermediate bulk container (IBC)/tote or transport compartment). Repackaging should be done in a controlled environment, preferably indoors, to prevent contamination (
see Figure 3). Batch, lot or fill codes should be recorded from the original container. Special precautions must be followed if the product has special environmental, food grade or other claims.
Figure 3. Tank and drums for repackaging, which is a common practice. (Figure courtesy of J.A.M. Distributing.)
Products can be packaged onsite or received in a packaged form. Standards must be in place for package condition (e.g., no excessive or deep container dents) and label information (legibility). First-in/first-out stock rotation requires information on the age of the product. This information can include the batch number, fill code and “use by” date, and the supplier can provide information on how to determine a product’s age. Shelf lives should be determined using a documented testing protocol. This is especially important for products like cutting oils that have a limited shelf life.
Containers in stacks should have uniform heights, and pallets should be suitable for the type of container. Workers should use the right handling equipment (e.g., drum grabbers) for the type of package. If case goods are shrink wrapped, care must be used to not damage the containers; for example, applying excess pressure can crush containers.
Storage areas should minimize exposure to contaminants, and special precautions must be taken for outdoor storage areas. Temperatures in the storage area must be maintained in the proper range to prevent freezing or drop out at low temperatures or product degradation at high temperatures.
If a customer returns packaged products, the distributor’s employees must make sure that the packages meet set standards before returning them to stock. Substandard products must be segregated from the main stock.
Making the delivery
Packaged products must be inspected before they are loaded onto the delivery vehicle to ensure that they are in good condition. The delivery vehicle itself also must be in good condition, especially the roof (no leaks) and shock absorbers. The load must be suitably and adequately secured to prevent load shifting or damage to the product during delivery. This is particularly important for loads that do not fill the entire vehicle.
Load restraint equipment must be inspected periodically and replaced if damaged. If a customer is taking delivery of a partial load, personnel must ensure that the remaining packages in the vehicle remain properly secured.
Loading and delivery equipment for bulk products may be assigned by product group, or change of assignment procedures may be followed to flush and clean the equipment between batches, but dedicated equipment is preferred. For truck or tank wagon transport, the compartments and outlets must be labeled and identified by product or product group.
Pumps, hoses, meters and spouts for transferring a product from a drum should be dedicated by product or product group. Equipment must be adequately flushed between groups, especially if two product groups are incompatible or if the products are especially expensive. If a pump cannot be flushed adequately, it should not be used for more than one product group.
Equipment must be periodically inspected to ensure that it is in good working order, and batch numbers/fill codes on the drums must be recorded to ensure traceability. Representative samples should be taken from the drum and retained, especially if the drums were packaged outside the control of the company delivering the product. At a minimum, drums should be checked to ensure that they meet appearance standards.
Employees at the customer site must have knowledge and experience in handling lubricants, identify the lubricants properly and keep lubricants for various applications separated. Lubricants must be transferred from the storage area to the application using clean, dedicated transfer equipment to avoid contamination.
Compatibility and contamination
A lubricant’s compatibility with other lubricants and products is perhaps the single greatest factor in maintaining lubricant quality in the supply chain. Incompatibility and contamination both present problems, but incompatibility presents a higher risk; you can have a well-maintained system and still ruin a batch by mixing in an incompatible product.
Lubricant compatibility is determined by product technical experts, usually during the product-development process. Compatibility can depend on product claims and specifications, oil analysis, base oils and process oils, environmental considerations, food grade product requirements and products not based on mineral oils (
see Figure 4).
Figure 4. Lubricant compatibility issues. (Figure courtesy of Michael Roe.)
Laboratory studies, bench testing and equipment testing can determine whether fluids are compatible. Formulators report the results of these studies using “compatible, borderline or incompatible” designations on compatibility charts (
see Figure 5). The compatibility chart also can indicate the appropriate change of assignment procedure required when switching from one product group to another. Compatibility charts are most useful for fluid lubricants (oils); compatibility between greases should be tested and confirmed independently.
Figure 5. Lubricant compatibility chart for oils. (Figure courtesy of Michael Roe.)
Product contamination can occur any time a product is transferred during manufacturing, packaging, loading, delivery, receiving or storage. Products can be misidentified, workers can connect to the wrong supply source or they can deliver to the wrong delivery target. Missing or inadequate procedures, lack of training or workers not following procedures also can lead to contamination.
Other causes of contamination include inadequate purging or flushing of vessels and transfer lines before switching to another product or incompatible prior cargoes that have not been effectively purged from transport compartments. At the customer site, suppliers can deliver a bulk lubricant to the wrong tank, or the customer can put the wrong lubricant into their application.
Contamination can occur from a failure to segregate non-conforming products or packages; incorrect or missing identification on transfer equipment, storage tanks or transport compartments; improper storage conditions that allow water or dirt to enter; product tampering or sabotage; distractions, especially during transfer; or inadequate filtration.
Maintaining quality
It’s important for managers on the vendor/distributor side to oversee and review the quality of the supply chain on a periodic basis and record the results of the review. Any changes triggered by new or revised products or their packaging, new employees, new equipment, audit results, customer feedback, quality incidents and benchmarking should be identified, managed and communicated to the relevant employees.
Managers must confirm that the job is being done correctly by actively involving themselves in the work processes, making periodic observations and conducting interviews with employees. Effective communication helps employees recognize the importance of their part in maintaining the quality of the supply chain.
Employee training can include computer modules, class participation, on-the-job training and job shadowing. However, training can’t just be a one-time exercise. Verifying and sustaining employee competency involves documenting completed training sessions, verbal or written testing or other certification, job observations by a supervisor or manager, employee meetings and refresher training as needed.
Documented procedures are a key factor in preventing adverse incidents (
see Figure 6). These procedures should be readily available as printed or electronic documents rather than verbal or handwritten instructions. Responsible individuals should conduct periodic maintenance of documented procedures to ensure that only the current version of each procedure is being used. Lists of procedures should include current references to related documents (work instructions, equipment manuals, process flows, charts, pictures and video presentations). Revisions and documentation updates are needed for new equipment, products or package styles; employee safety issues; customer feedback; or quality incidents.
Figure 6. Bulk loading and delivery elements. (Figure courtesy of Michael Roe.)
Quality controls
Preventive practices keep commingling or contamination from occurring in the first place (
see Figure 7). These practices include using dedicated or segregated storage and transfer equipment, desiccant breathers, particle filtration systems and mistake-proofing equipment (e.g., sensors that detect product defects and warning systems that alert operators). Valves must function properly and be maintained in the correct open or closed positions. Internal and external site security systems also are preventive measures.
Figure 7. Lubricant segregation/change of assignment. (Figure courtesy of Michael Roe.)
Well-maintained and calibrated temperature and pressure gauges ensure that lubricants are stored under the proper conditions. Sampling, testing and retaining practices can help detect any foreign material (including a different lubricant) that might cause a problem.
Employees must be well trained in how to take samples and evaluate the results. Many lubricants in the supply chain have similar viscosities, colors and other properties, so it may be difficult to distinguish between products using just one property.
Samples must be representative of the material in the container, and sample appearance should be recorded. Retained samples should be archived for future reference in a suitable cabinet, using labels with sufficient information on where the product came from and where it went.
Quality incidents
Accidents happen, and quality incidents must be addressed immediately to contain their effects. If an incident does occur, the first response should be to take care of the customer. After that, a root cause analysis and preventive actions will help ensure that the incident does not recur, and follow-ups confirm whether the actions taken were effective and sustained.
Two common causes of quality incidents are a lack of documented procedures and a failure to follow all or part of these procedures. Effective management oversight can ensure that all employees are up to speed on company procedures and that they follow these procedures rigorously.
Managers should be open to suggestions from their employees, and they should do periodic walk arounds. Compatibility charts and checklists serve as references so that employees can verify that they are using the proper procedures. Reviewing what-if scenarios (risk management) with employees can help employees prevent adverse incidents and know what to do if an incident happens.
End-to-end quality assurance
“Label, label, label” is good advice for delivering the right lubricants to the right customer, along with “Check, recheck, check again and have someone else check.” This advice is even more effective when employees are focused on their work, and distractions are minimized or controlled.
Management must take an active role in observing processes and in training and motivating employees. Standard procedures and employee training must be documented and monitored for effectiveness, especially for changes of assignment. Employees and management alike must participate in determining what could go wrong in any process and in establishing and implementing preventive practices.