20 Minutes With Samarth Desai
Rachel Fowler, Managing Editor | TLT 20 Minutes July 2018
This PEER Bearing group leader analyzes the critical factors when specifying lubricants for specific bearing applications.
Samarth Desai - The Quick File
Samarth Desai is an application engineer group leader for industrial applications at PEER Bearing Co., an SKF Group company. He has eight years of experience working as an application engineer in the bearings industry and is a representative for PEER at the American Gear Manufacturers Association. He obtained his bachelor’s of science degree in mechatronics from GCET, Sardar Patel University, in 2008, and his master’s of engineering degree in mechanical engineering from Lehigh University in 2012.
After his undergraduate studies in 2008, Desai worked with FAG Bearings (Schaeffler Group) handling heavy-industry and machine-tool applications. Upon completion of his master’s degree, he joined PEER Bearing Co. While working at PEER, he has managed and supported various projects related to new product development which includes seal and bearing design for radial ball and tapered roller bearings. During his tenure at PEER, his team has implemented many customized product solutions in the PEER portfolio to work in specific applications.
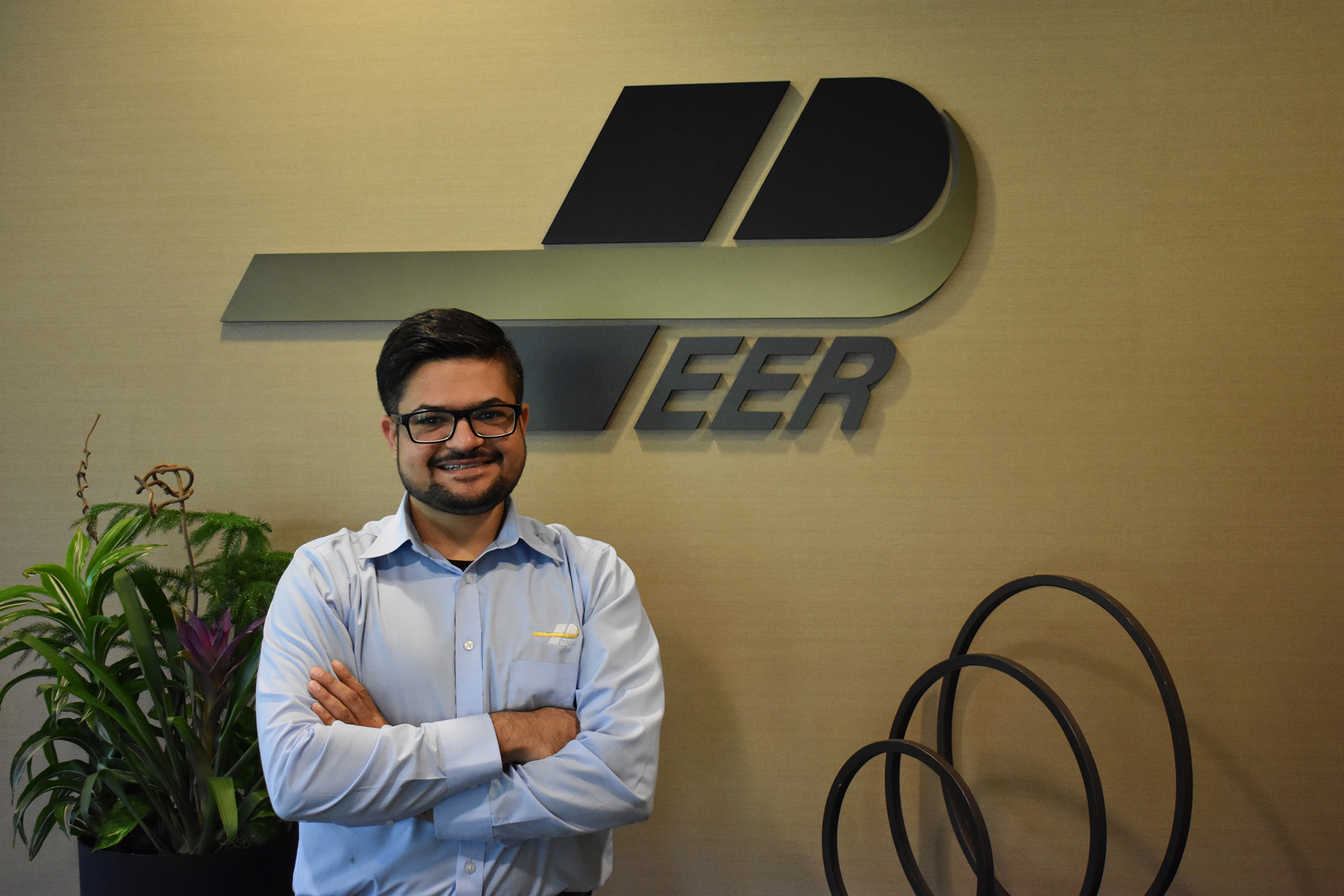
Samarth Desai
TLT: What inspired you to work in the bearings industry?
Desai: With my background in engineering, this industry is an ideal fit to apply my skills and work closely in the field with various applications. Specifically my role in application engineering at PEER is very dynamic, as every bearing application is unique whether it’s in the off-highway, agriculture, fluids or industrial transmission industry, and each has its own challenges that motivates me to evolve and develop new design solutions for specific applications.
TLT: What do you consider to be the most challenging issue when designing a bearing seal?
Desai: Bearing seals have two main functions: to retain lubricant inside the bearing and prevent external contamination from penetrating the bearing. Depending on the application, there are various factors that come into play when designing a bearing seal—speed/torque, operating temperature, chemical compatibility, misalignment and bearing envelope.
The most challenging part with seal design is to meet the life expectancy of the application by providing an appropriate seal with the size and speed constraint. A large amount of data is collected from the field, and various lab tests are conducted to design and benchmark a seal that can perform well in a specific application.
When we design a bearing seal for use in an electric motor or a high-speed application, low seal torque is a key requirement. Using a contact seal with high interference between lips and bearing rings will make it inefficient for the application. Although this motor could be used in a condenser, submersible pump, lawn and garden equipment or near a high-temperature environment, it still needs to prevent water/contaminants from getting in or prevent grease from leaking out. So appropriate grease fill, grease type and seal material are required to meet the application requirements.
In contrast, when considering an agriculture application such as tillage equipment, preventing contamination is the main goal, so much more robust special sealing with multiple lips is required (
see Figure 1). The challenge in this case is to provide an extended bearing life by reducing the equipment downtime.
Figure 1. Tillage application and sealing solution. (Figure courtesy of PEER Bearing Co.)
TLT: How does seal design, speed and lubrication affect bearing life in applications?
Desai: More than 40%-60% of bearings returned from the field have damaged modes associated with contamination, insufficient lubricant, unsuitable lubricant and aged lubricant. Bearing life is very sensitive to these factors.
All these factors relate to each other and affect bearing performance in different applications. Speed is a very critical parameter when it comes to selecting the right seal and lubricant. As per the Stribeck curve (
see Figure 2), at low speeds lubrication film is minimized and leads to boundary friction, whereas hydrodynamic or full-film lubrication—which is the optimum lubrication condition characterized by the separation of two surfaces—is achieved at comparatively higher speeds. To maintain this lubrication film, appropriate minimum base oil viscosity needs to be selected for specific applications based on speeds and temperature. A general rule of thumb is film thickness increases by a factor of 1.6 when speed is doubled.
Figure 2. Stribeck curve—lubrication regimes. (Figure courtesy of PEER Bearing Co.)
The seal is one of the most critical components in a bearing when used in a contaminated environment. Depending on the type of contamination, it could lead to premature damage conditions like corrosion, abrasive wear and surface fatigue/spalling (
see Figures 3 and 4). Any hard debris leads to particle indentation, which progresses toward a surface fatigue or spall.
Figure 3. Bearing damage from corrosion and contamination. (Figure courtesy of PEER Bearing Co.)
Figure 4. Bearing damage from contamination—surface-initiated fatigue. (Figure courtesy of PEER Bearing Co.)
With higher speeds, seal lips tend to wear faster and reduce the sealing efficiency, so proper seal selection is necessary for each application. Precision ground surfaces for seal lips have been used to reduce seal wear.
TLT: What is the optimum quantity of grease fill required for sealed bearings?
Desai: Too much or too little grease and/or inappropriately high- or low-oil viscosity causes viscous drag, surface damage and affects lubricant life. Pre-greased and sealed bearings by manufacturers will have initial grease fill of 20%-30% of the free space in the bearing.
Lower speed and heavily contaminated applications could have grease fill in the range of 40%-80%. Likewise, a higher speed application (N⋅dm > 40,000 to 50,000) will need to have a low-viscosity grease with fill volume of ~15%-25%. Any overfilling will lead to shearing and produce high heat.
For open bearings mounted in housings, housing space is packed partially with grease so there is adequate space in the housing to compensate for grease purged from a running-in period.
TLT: What types of new designs have been implemented for seals in bearing technology?
Desai: There are various kinds of seal designs available for use with specific applications. Seal designs can vary from non-contact type to light contact and contact type depending on the degrees of drag and contaminant exclusion (
see Figure 5). PEER Bearing also offers these seals in different materials like nitrile, polyacrylate and fluorocarbon depending on operating temperatures and chemical compatibility.
Figure 5. PEER Bearing sealing performance in contaminated environment. (Figure courtesy of PEER Bearing Co.)
In the agriculture industry where multiple bearings are used on farm implements such as disc harrows and planters, end-users and OEMs are trying to reduce downtime, maintenance and environmental impact. For this, PEER offers the TILLXTREME™ patented (U.S. 9,157,475) maintenance-free solution with 6 or 7 lip seals (
see Figure 6).
Figure 6. PEER Bearing maintenance-free seals for agriculture application. (Figure courtesy of PEER Bearing Co.)
Additionally, for wheel hubs, PEER Bearing has triple-sealed tapered roller bearings options that can help provide protection and replace traditional shaft seals. It helps reduce cost by compact assembly, helps ease of maintenance and prevents shaft wear from direct contact of seal lips (
see Figure 7).
Figure 7. Sealed purgeable tapered roller bearing. (Figure courtesy of PEER Bearing Co.)
TLT: How have these new seal designs led to improvement in bearing life?
Desai: These new seal designs offer significant improvement in bearing life by preventing contamination and channeling the grease flow. Precision ground surfaces for minimizing lip wear, premium seal materials and design optimization have extended the seal life. The use of mud slurry testing, collaborating with customers for field testing and benchmarking our seals against other industry offerings led us to make continuous improvements in bearing performance under extreme conditions.
As an example, PEER’s TILLXTREME™ solution was validated in a trencher application for an industry leading OEM improving the bearing life by 50%-100% when tested against a conventional relubricatable bearing.
TLT: What tools are utilized to identify the proper lubricant for specific applications or bearing type?
Desai: The basis for selection of a proper lubricant starts with the right base oil viscosity required for the application. Oil viscosity is the main tool to adjust lubricant film thickness. Required minimum base oil viscosity (v1) is selected using the charts in Figure 8 based on bearing size and operating speed. v1 is then converted into required viscosity (v) at operating temperature. The required base oil viscosity should be v1 x (1…4). Viscosity ratio (κ = v/v1) is used to relate with the lubricant film condition observed in the application. The value should at least be ≥ 1 for achieving minimum basic rating life of the bearing.
Figure 8. Lubrication selection. (Figure courtesy of PEER Bearing Co.)
The next step is determining whether a grease or oil is needed for the specific application. Individual lubricants should be examined to determine their suitability based on type of load, compatibility, viscosity index, grease consistency (NLGI), oxidation resistance, rust protection ability and minimum-maximum operating temperature.
Lubrication film thickness and its effect on advance bearing life (ISO/TS 16281) can also be analyzed by application engineers at PEER Bearing using simulation tools such as MESYS and ROMAX.
TLT: What criteria is used to specify the proper lubricant in bearing applications?
Desai: The lubricant should be capable of providing supporting film at operating loads, speeds and temperatures. The basic criteria to specify proper lubricant in bearing applications include temperature, compatibility, load or pressure and operating environment.
1.
Temperature. The maximum operating temperature should be 20 C or less than the upper limiting value of the lubricant, and the minimum operating temperature should be 20 C above the lower limiting value.
2.
Compatibility. This is an important criterion when a bearing is used in a greased housing, typically when they are relubricatable. Grease compatibility depends on base oil type, thickeners, base oil viscosity and NLGI class. Grease compatibility can be further evaluated using an industry standard test defined under ASTM D6185 and thickener compatibility charts from lubricant manufacturers.
3.
Pressure properties. Viscosity should be sufficiently high at operating temperatures to support the load. At high loads, greases with extreme pressure additives should be used. For example, silicone lubricants do not have the film strength of petroleum types and other synthetics. These are recommended for light load applications only.
4.
Environment. If the bearing is operating in dust or high humidity/moisture conditions or a chemical environment, proper lubricant selection also should be considered.
TLT: What issues arise from inadequate lubrication?
Desai: Inadequate lubrication condition is caused due to insufficient lubricant quantity or viscosity, excess heat generation, contamination, oxidation/aging, incorrect lubricant or excess lubricant. As previously stated, most of the bearings returned from the field have damage modes associated with inadequate lubrication. This condition causes metal-to-metal contact between rolling elements, raceways and retainers, so proper elastohydrodynamic lubrication film needs to be maintained under all conditions. Additionally, it protects the bearing against corrosion and wear, reduces bearing noise and prevents contaminants from entering the load path.
The common issue seen due to inadequate lubrication is surface-initiated fatigue on bearing raceways. Metal-to-metal contact causes surface asperities to shear, which leads to micro-cracks at the asperities followed by micro-spalls, and eventually leads to surface fatigue (
see Figure 4).
Another common issue is abrasive wear, which occurs when abrasive contaminants like dust ingress the lubricant and reduces its effectiveness. This damages the microgeometry of the bearing and quickly wears down the raceways of rings and cage pockets (
see Figure 9).
Figure 9. Abrasive wear from inadequate lubrication. (Figure courtesy of PEER Bearing Co.)
Note: TILLXTREME™ is a registered trademark of PEER Bearing Co.
You can reach Samarth Desai at sdesai@peerbearing.com.