Q.1: Describe the most difficult sealing application you faced and how you solved it.
TLT Sounding Board April 2018
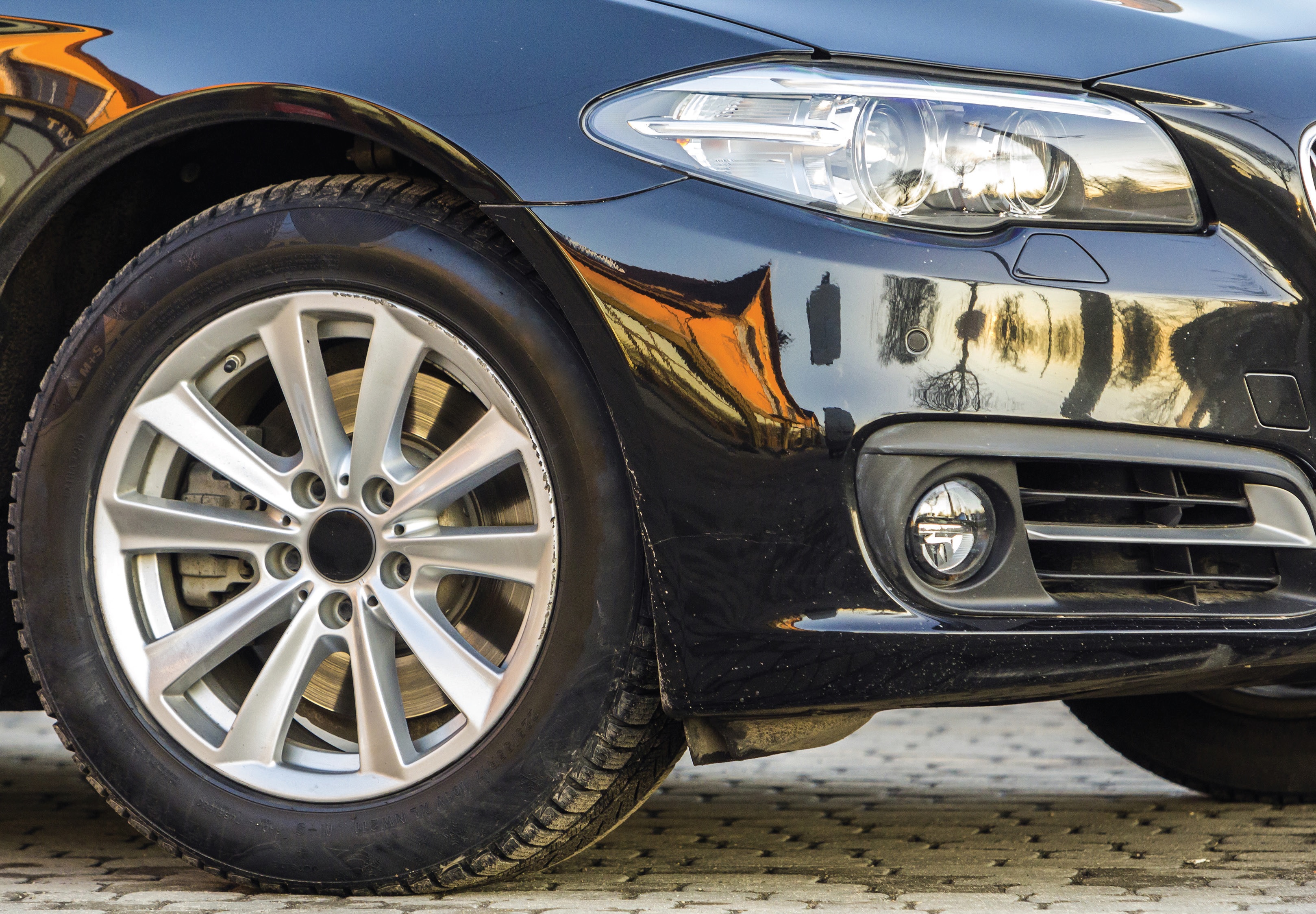
© Can Stock Photo / Bilanol
From industrial machinery to heavy construction equipment to the family commode, TLT readers have seen it all when it comes to seal failures. Two threads that ran through reader comments were (1.) many seal failures are easily avoidable and (2.) gearboxes and other components are frequently blamed for problems that originated with a seal. Readers also noted that despite continual admonitions to check compatibility, many end-users still experience seal failures due to choosing the wrong lubricant. Seal problems can be costly, too. Forty-five percent of survey respondents said seal failures have caused their or their customer’s company more than $10,000 in the last 12 months. “While not necessarily devastating, it is frustrating because it is preventable,” notes one reader.
Dry seal application.
Radial shafts seal at 30,000 rpm.
A screw compressor had a spring-loaded face seal that broke, and leakage was occurring. We increased the surface roughness of the seating so the seal does not slide out due to vacuum.
Mechanical seal failure in PD lobe pump that was pumping liquid sorbitol. Solved problem by changing to a pump that used a labyrinth seal.
Mining suspension strut seal failures are costly and time consuming to repair. Working with the manufacturer’s expertise and supporting test parts with different surface finishes and materials has improved life dramatically, but there is still more life to gain. The biggest hurdle is understanding that improvement is incremental, and every bit makes a difference. It’s not an overnight change in many cases.
Idler from conveyor belts used for iron ore transportation. The problem is not solved yet. Different labyrinth seals with and without grease were tested along with rolling bearings with seals and shields. Results were not satisfying.
The family toilet. The plumber was called.
The bearing of continuous casting in steel industry. We use calcium sulfonate grease.
RON95 (premium gasoline equivalent) down to -29 C in a marine environment for both static and dynamic sealing in commercial off-the-shelf components. Required custom-made specialty gaskets made for replacing key areas and components.
Rapid acceleration and deceleration. Unsolved.
The seal on a high-temperature bearing was failing on test at 150 C. The urea grease was breaking down, and the active nitrogen attacked the fluoroelastomer. We changed to a higher quality fluoroelastomer and to a more thermally stable urea thickener and the problem went away.
Pump seals.
Seal pot on catalytic cracker process. We used a very abrasive material.
Valve cover on my BMW motorcycle.
Roller bearing shielding in mower spindle application.
Leaking high (1,800 psi) steam past a heat exchanger gasket face that we knew was as flat as we could measure. We roughened the surface finish of the mating faces and were very careful on retorquing fasteners.
Labyrinth seal. Replaced it.
The mechanical seal of a ballast pump (capacity 3,000 m3/hrs) started leaking in the engine room, and we had to overhaul the pump to change the mechanical seal. On further analysis, we found the graphite part of the seal had broken.
CIPG. The sealant leaked into the device causing fluid problems.
Pump leakage. We changed the seal for better compatibility.
As a lubricant formulator, the greatest issues we see are typically either with wide cyclic temperature variation or with regular wash downs. In some cases, we have to accept that the lubricant will slowly leak/become contaminated and select/formulate accordingly.
How many seal failures has your company (or your customer’s company) experienced in the last 12 months?
Fewer than 10
63%
10-100
27%
More than 100
10%
Based on responses sent to 13,000 TLT readers.
Q.2: Describe the most devastating seal failure you have experienced or witnessed.
A compressor with a dry seal backed fluid in during a power failure and wrecked the compressor twice.
Overheated seal.
Abrasive wear on rolling bearing caused by dust ingestion and leading to machine shutdown.
I saw the spring-loaded face seal on the compressor shaft break.
Mechanical water flush seals that failed, letting water get into the product being pumped, which contaminated the end product.
Suspension strut seal failures tend to be the costliest on a per-failure basis.
It is not worth describing. Suffice to say the smell was very bad.
Grease coking in the bearing.
Standard mechanical seal on a gearbox application that was bypassing the elastomer around the shaft. Caused significant down time of a passenger ferry after a replacement failed within an hour.
Lots of gearbox failures we have witnessed can be traced back to seal failure. The seals are usually the weakest point in the system. But when the seal “fails,” the gearbox will keep running until something more catastrophic fails. This is then noted as the failure.
A material was chosen that had a weakness against ozone. In areas of high urban ozone, the seals failed. The equipment maker had very high warranty costs to replace failed component assemblies.
Pump failed to feed in raw material in time and ruined an entire batch of valuable material.
Fire and explosion in a Cat unit in 1982.
Sulphur acid pump. Lost 5,000 gallons of concentrated acid to containment.
Premature spindle failure.
I was walking past a boiler feed water pump, and the main shaft packing blew out.
Ballast pump leaking from the mechanical seal while ballasting operation.
2006 Pontiac Solstice rear axle seal/fluid combination incompatible, resulting in axle oil on garage floor and a recall from GM.
We’ve seen several sealing failures at customers, despite repeated warnings to check compatibility with the lubricant before use. While not necessarily devastating, it is frustrating because it is preventable.
How much have seal failures cost your company (or your customer’s company) in the last 12 months?
Less than $100 15%
$100-$1,000 35%
$1,000-$10,000 5%
More than $10,000 45%
Based on responses sent to 13,000 TLT readers.
Editor’s Note: Sounding Board is based on an email survey of 13,000 TLT readers. Views expressed are those of the respondents and do not reflect the opinions of the Society of Tribologists and Lubrication Engineers. STLE does not vouch for the technical accuracy of opinions expressed in Sounding Board, nor does inclusion of a comment represent an endorsement of the technology by STLE.