Are pour point depressants depressing?
Dr. Robert M. Gresham, Contributing Editor | TLT Lubrication Fundamentals March 2018
In reality, they are one more tool formulators have to enhance fluid performance.
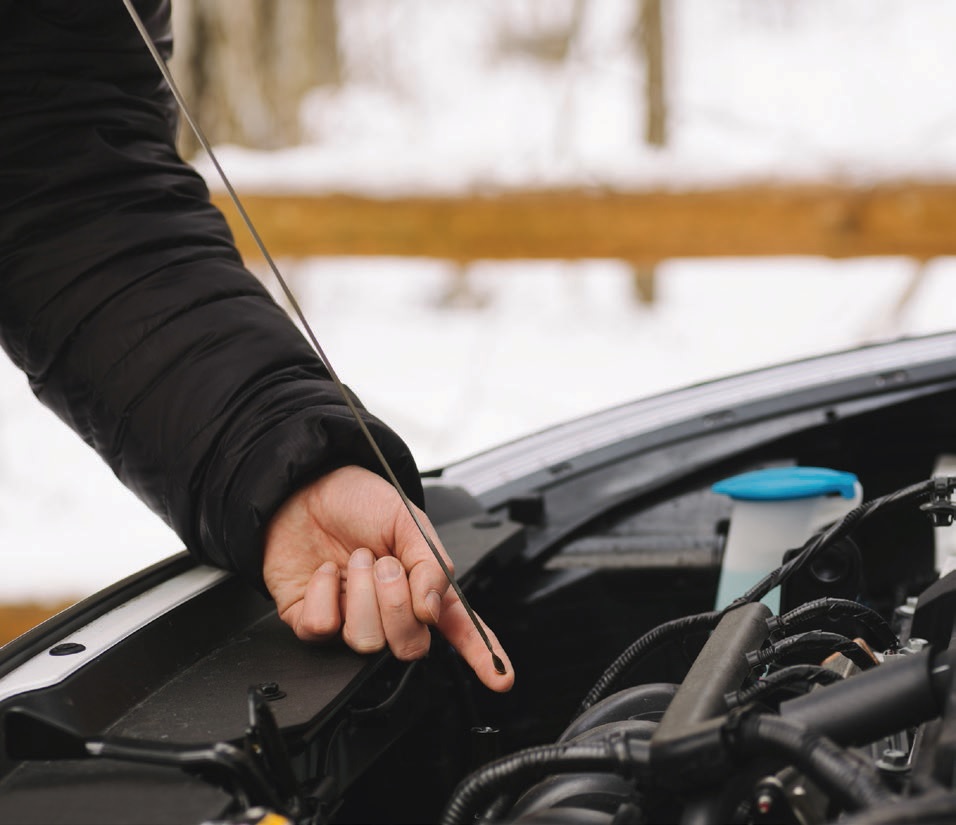
Pour point depressants can be made from many different polymer chemistries.
© Can Stock Photo / WWstockphoto
Pour point depressants (PPDs) are another one of those additives that seem to perform a somewhat mystical and obscure function in lubricants. And the depressing thing is most education courses and books don’t really say much about them. Usually what you hear is, “Pour point depressants are low-temperature flow improvers and wax crystal modifiers, next slide.” So let’s take a closer look.
PPDs are polymeric molecules that are added to mineral-oil based lubricants that are exposed to low temperatures. Their job is to prevent a viscosity increase such that the oil will not flow sufficiently and starve the system of needed lubricant, especially on start up. Indeed, the viscosity can increase such that the oil is said to actually gel or become semi-solid. Some key applications where this can be critical are engine, transmission and gear oils and hydraulic fluids. Additionally, these products are often made with a predominance of paraffinic base stocks, which by their nature contain significant concentrations of 14 carbon chains or higher. These chains are said to be waxy and can cause pumpability problems at low temperatures. Additionally, waxy components also can be added to a formulation as components of the detergent/inhibitor or in some viscosity index improver packages.
These waxy molecules, at low temperature (below the cloud point), cause the oil viscosity to increase rapidly, and the waxy molecules begin to crystallize. The oil becomes cloudy, and ultimately these wax crystals can precipitate from the lubricant. The PPD allows the oil to slowly increase in viscosity with decreasing temperature, as it does above the cloud point, but prevents the rapid increase in viscosity associated with waxy crystal formation.
PPDs, as I stated, are polymeric materials. They can be made from many different polymer chemistries such as acrylates, styrenes, alpha olefins and vinyl acetates, to name a few. These chemistries, when polymerized, form a linear back bone that can have side chains with varying long (waxy) and short (non-waxy) hydrocarbons. Thus, you can imagine the polymers look a little like a hair comb but with long and short teeth. It is this structure that has been found to inhibit the formation of three-dimensional wax crystals by virtue of the long chain portions of the PPD partially co-crystallizing with the wax and the short chains aiding in solubilizing the complex in the lubricant.
One of the dominant chemistries used for PPDs are the polymethylmethacrylates (PMAs). By their nature and structure, PMAs allow for easy manipulation of the side chains. A single methyl (CH3) methacrylate monomer with R1, 2, which can be any of the long- or short-side chains, is shown below. The polymerization takes place when the various monomers are treated with a free-radical initiator such as peroxides, which act on the double bond to form a free-radical, which reacts rapidly with another monomer. Thus, by controlling the mix of monomers with varying R chain lengths during polymerization, you get a polymer of the desired molecular weight (usually about 200-300) and random distribution of long- and short-side chains. Typically, the longer-side chains are in excess of 14 carbons and the shorter chains from 1-14. These side chains can vary in length and distribution within the polymer to optimize performance.
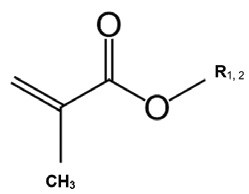
The final polymer might look similar (to keep the diagram small) to the structure below, where in one R group is methyl (CH3) and the other is butyl (
CH3).
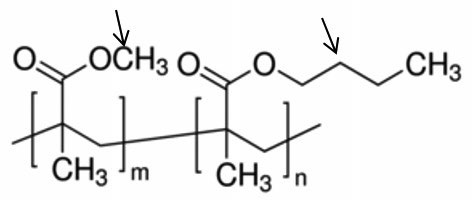
One of the key properties of these PMAs is their inherent oxidative and thermal stability, which makes them ideal for engine oils. This is especially so as automotive OEMs now require low-temperature pumpability of used engine oils as well. Here, in addition to concern about wax crystal formation, there are the effects of oxidation on the oil forming polar molecular species that also can form gels and raise the viscosity of the used oil.
Thus, PPDs are hardly depressing but, rather, one more tool formulators have to enhance the performance of engine, transmission and gear oils as well as hydraulic fluids.
Bob Gresham is STLE’s director of professional development. You can reach him at rgresham@stle.org.