The effect of coating thickness and substrate roughness on tool wear during turning
M. Bar-Hen (1), I .Etsion (2) | TLT 2016 TFC Abstract Highlights February 2018
1. R&D Tool Division, Turning Department, Iscar LTD, Tefen 2495900, Israel
2. Department of Mechanical Engineering, Technion, Haifa 32000, Israel
For the benefit of our readers involved in tribology research, TLT is publishing abstracts of the best papers presented at the 2016 Tribology Frontiers Conference. Registration for the 2018 TFC opens in May. Until then, you can find 2018 updates and program information at www.stle.org.
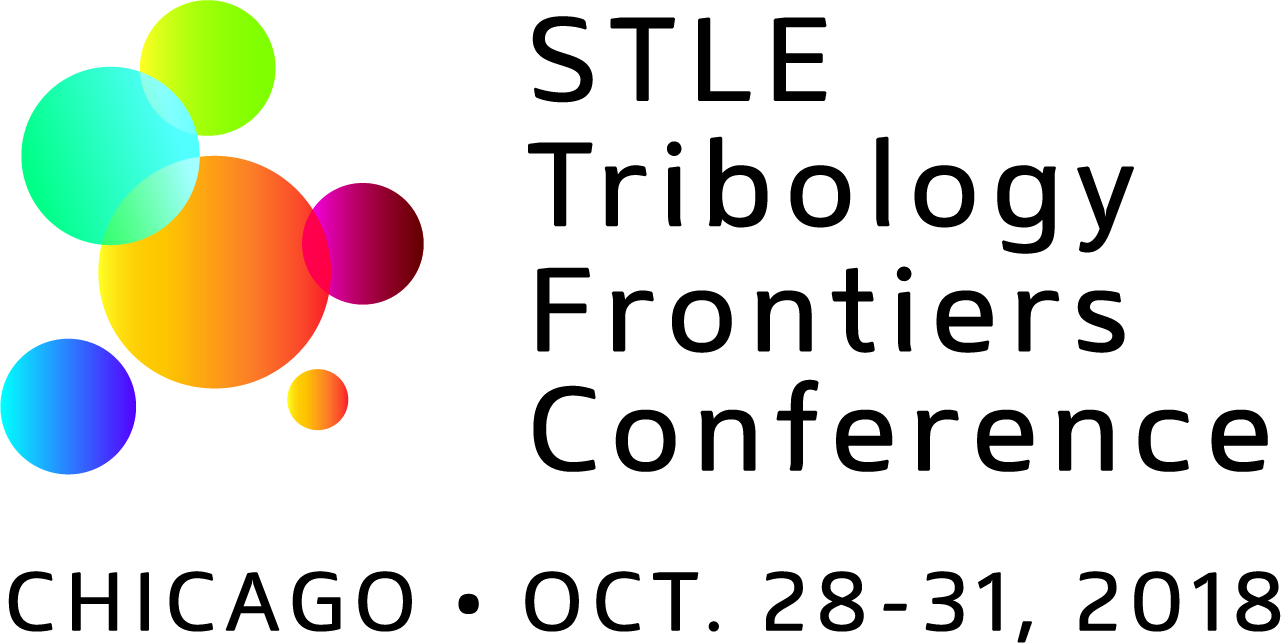
Co-sponsored by ASME Tribology Division.
The effect of coating thickness and substrate roughness on the tool wear in turning was studied experimentally. TiAlN coating of various thicknesses was applied on tungsten carbide (WC) tool substrate having various surface roughnesses. The tool wear was measured following fixed cutting distance and speed tests. In general, when plotting the wear vs. coating thickness alone or vs. substrate roughness alone, a trend of decreasing wear with either increasing coating thickness or substrate roughness was observed. However, the scatter of the results was very large. On the other hand, excellent fit was obtained when the wear results were plotted vs. the dimensionless ratio t/R
su where t is the coating thickness and R
su is the average radius of curvature of the rough substrate asperities. An interesting correlation was shown between the experimental results and some theoretical models for yield inception of a coated spherical asperity.
Cutting tool flank wear.