Implementing an oil analysis program
Jeanna Van Rensselar, Senior Feature Writer | TLT Feature Article February 2018
Vibration analysis, thermography, ultrasound—the best results come when you combine technologies.
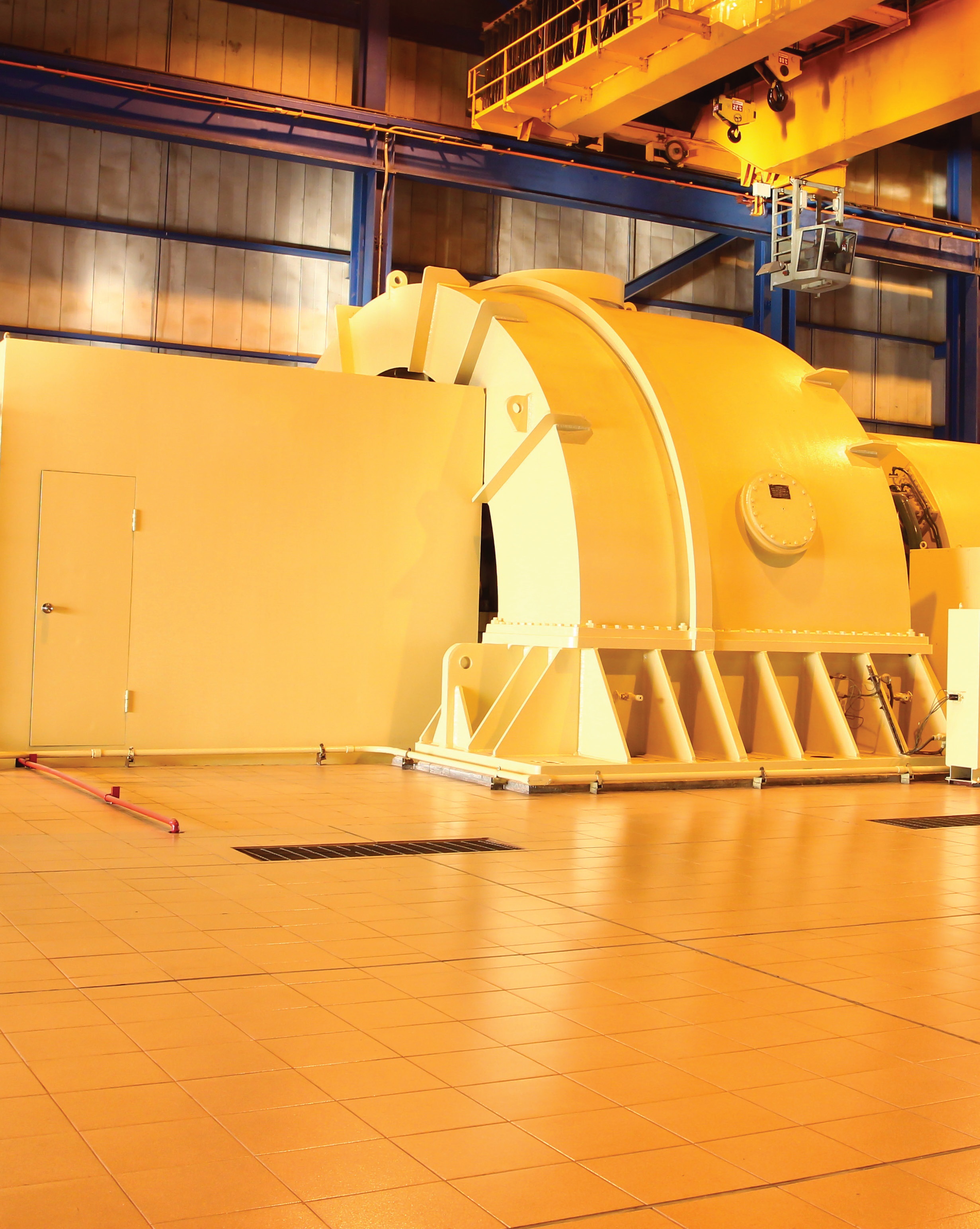
© Can Stock Photo / bajita1111
KEY CONCEPTS
•
For most machinery, there is no more cost-effective way to determine the health of both the equipment and the fluid than oil analysis.
•
Organizations that don’t already have an oil analysis program in place can set one up with a few simple steps.
•
The success of your oil analysis program depends on oversight and follow through.
COST-EFFECTIVE, COMPREHENSIVE AND PROVEN, oil analysis is an extremely powerful condition monitoring tool. Those skeptical of its benefits are likely not fully or correctly leveraging its awesome range of capabilities.
Getting the most from oil analysis starts with setting up the program correctly and continues with thorough follow up. For some organizations, it makes sense to bring in expert help in the form of reliability consultants who will initiate and manage the program.
David B. Doyle, CLS, OMA I, OMA II, general manager of ALS Tribology, says, “Acquiring data without having a process to organize and follow up with the information can lead to confusion and frustration for users. The challenge today is taking the data that historically has been generated and report it in such a way that it provides more value for the user. Reporting data without a process for follow up and ownership limits the value that is available from using these condition monitoring tools.”
OA BENEFITS
According to RCL platform leader for Allied Reliability Matt Spurlock, oil analysis is the one technology that can actually monitor equipment health proactively—before damage occurs. This includes the ability to monitor the presence of solid contaminants, moisture and lubricant health. “In addition to working in the proactive zone, oil analysis is an excellent tool to use within the predictive zone,” he explains. “When sampled from the correct location, following best practice sampling procedures and utilizing a comprehensive approach to sample testing, oil analysis can determine the presence of wear debris very high on the P-F curve (
1).”
One of the benefits that oil analysis has over most other condition monitoring tools is it detects problems in both the fluid and the machine. In addition, it may detect defects earlier than other technologies such as thermography and ultrasound. For this reason, oil analysis is usually the first line of defense.
Among the many benefits of oil analysis are:
Longer equipment life. Oil analysis ensures machinery is being optimally lubricated while also monitoring issues such as wear and contamination. Wear particle analysis—the cornerstone of oil analysis—is amazingly effective at flagging and predicting problems before they start to negatively affect equipment life.
Extend lubricant life. Oil analysis yields a clear picture of the condition of the lubricant so that it never has to be changed prematurely. This can, in some cases, more than double the filter change and drain intervals. Eliminating even one oil change a year saves money in material and labor time.
Reduce equipment downtime. Oil analysis gives maintenance personnel the opportunity to detect and correct issues before they cause equipment shutdown. On-the-road breakdowns, in particular, are expensive. The cost of oil analysis pales in comparison.
Monitor viscosity and acidity. Knowing the oil’s viscosity means knowing if it is adequately lubricating the parts. The Base Number (BN) and Acid Number (AN) on the oil analysis report will indicate if the oil is still protecting the machinery.
Boost resale value. Nothing says the equipment has been taken care of better than a series of reports demonstrating regular oil analysis.
Oil analysis is not just about saving money, it’s also about reducing headaches and having the assurance there will not be any serious disruptions in operations due to equipment failure.
“Analysis of in-service lubricants detects a wide variety of failure modes,” Doyle says. “This can include damaged components, severe operating conditions, lack of proper maintenance, lack of proper lubrication or lubricant degradation and contamination. Different types of equipment have specific failure modes that reflect equipment design and metallurgy that oil analysis diagnostics staff are trained to recognize. Test parameters can give indications as to the root cause. Other times the test data will pick up the symptom of the failure mode, which requires further inspection. Many times the value of the test data can be increased 10 fold after discussion between the end-user or asset manager and the testing laboratory.”
INSTITUTING AN OA PROGRAM
Most people don’t need convincing that oil analysis is beneficial. However, the prospect of setting up a comprehensive oil analysis program can seem daunting. Following are a few steps that, if sequentially adhered to, will ensure the program is set up and then functioning correctly.
1. Select an oil analysis lab. This is a good first step because the lab can provide advice on setting up the rest of the program (
see How to Select a Lab). Look for an established lab with a demonstrable quality assurance program and industry accreditations such as ISO 17025 or 10CFR50. If possible, it’s always a good idea to visit the lab before committing. In fact, the laboratory’s proximity can itself be an advantage since it allows more timely delivery of samples—especially important in emergency situations—which the new oil analysis program will hopefully eliminate.
HOW TO SELECT A LAB (2)
Assuming that an in-house testing facility is not an option (most small to mid-sized companies won’t find this feasible), customers need to select the best lab to test their samples. Here are a few considerations:
•
Is the lab ISO 17025 accredited?
•
Do tests conform to ASTM standards?
•
Are lab employees appropriately educated and/or certified?
•
During what days and hours is the lab available?
•
How many locations does the lab have?
•
Can the lab handle your sample volume?
•
What are the report delivery and format options?
•
What kind of guidance/technical support can you expect?
•
Does the lab have the latest equipment and technology?
•
How many test methods are available—a full menu or just a few?
•
How well does the lab interpret data (ask to see a sample report)?
•
What is the turnaround time for results?
•
What kind of training programs does the lab offer?
•
What are the costs per test, and what is/is not included?
•
What guarantees does the lab offer?
•
Is test selection pre-set (per industry and component type) but also flexible?
© Can Stock Photo / morenosoppelsa
2. Articulate goals. The program’s structure and foundation should be based on sound reliability engineering goals that create a roadmap for designing and implementing the program. The oil analysis lab can help here, but it is ultimately up to the end-user to align the program with the organization’s reliability needs. Following are a few suggestions for goals:
•
Improve reliability by avoiding breakdowns and extending life (both the machinery and its parts)
•
Flag and eliminate recurring problems
•
Eliminate most unscheduled maintenance
•
Maximize lubricant life and performance
•
Support comprehensive proactive and predictive maintenance.
Once these goals are established, it’s time to choose a program champion/key contact.
3. Create an equipment list. Establish a list of equipment to be sampled. Prioritize based on equipment criticality and allow for adjustment as the program continues (
see The Criticality Index—Choosing Machinery to Monitor). This list should include at least the following:
•
Equipment identification (a generic description along with serial number)
•
Component type, make and model
•
Required lubricant brand and grade often designated by the OEM
•
Oil reservoir capacity
•
Filter type and rating
•
Sampling frequency.
Equipment critical to plant operations should be identified first. Appropriate oil analysis for critical equipment includes wear metal analysis, moisture content, viscosity, acid number, particle count and analytical ferrography.
THE CRITICALITY INDEX (3)—CHOOSING MACHINERY TO MONITOR
The Criticality Index determines the logical extent of condition monitoring required for a piece of equipment. It takes into account such factors as:
•
Importance of the machine’s function
•
Whether or not there is another piece of equipment that can take over the function if that piece of machinery fails
•
The overall impact of downtime
•
The projected repair cost.
This index assigns all machines to one of the following three categories:
1. Critical machinery. These machines are so important that the rest of the operating environment cannot function without them, (i.e., power plant turbines). Equipment in this category requires complete online and (where possible) inline condition monitoring—regardless of cost. The specifics of monitoring are often included in insurance policies and warranties. This equipment is a prime candidate for predictive maintenance.
2. Essential machinery. This equipment is key to the operating environment, but its failure does not cripple operations. Sometimes equipment that falls into this category would be considered critical if not for the fact that a backup piece of equipment is readily available. While testing is not as important as it is with critical machinery, it is recommended in order to prevent costly repairs and inconvenience.
3. General purpose machinery. The balance of operations equipment falls into this category. These machines are usually monitored informally and periodically.
4. Devise the sampling strategy. While the oil analysis lab can advise, the end-user is the ultimate decider. This strategy will include sampling locations, method and procedure.
The procedure component of the strategy is where most programs fall apart. Oil analysis labs receive the vast majority of samples with information that is incomplete—making it very difficult for end-users to get the most from the report. This is where the program champion comes in. It is this person’s job to ensure that each sample is correctly labeled when it arrives at the laboratory.
“A key to achieving maximum ROI from oil analysis is to ensure the laboratory has all the required information regarding the equipment being sampled,” Spurlock says. “When going to the doctor for a blood test, we are asked questions such as age and health history in order to assure the correct test state. Just as in misdiagnosing a human, failure to provide the needed information for a machine also will result in a misdiagnosis.”
5. Establish performance metrics. Metrics always lead to accountability, so create metrics tied to the program’s original goals. For example, are there fewer breakdowns? Is there a reduction in recurring problems? Is there less unscheduled maintenance? Are drain intervals being extended? Be sure to account for anomalies and other factors that will affect the accuracy of the metrics.
If all of this seems a little overwhelming, there are reliability service providers that are more than qualified to set up and administer the program. More about this later. The bottom line is that setting up an oil analysis program requires careful consideration, planning and—perhaps most important—consistency and thorough follow through in order to be successful.
INTEGRATING OIL ANALYSIS WITH OTHER TECHNOLOGIES
Adding other condition monitoring technologies to oil analysis has a synergistic affect when it comes to diagnosing machinery. These technologies range from high-tech ultrasound to decidedly low-tech visual inspection by an expert.
Spurlock explains, “The days of suggesting one technology is ‘better’ than the other are long passed. A reliability-centered approach to predictive and proactive technologies that includes the optimized utilization of each technology will always yield higher ROI than relying just on a single technology. Vibration, infrared, oil analysis, etc., each focus on specific failure modes for each component type. While some of these failure modes are repeated across technologies, the degree in which detection can occur and be pinpointed will always vary. The best approach is to incorporate failure mode mapping against each technology.”
VIBRATION ANALYSIS
Vibration analysis is a key condition monitoring tool for rotating equipment. It excels at precisely detecting impending failures in high-speed bearing systems. As components reach the end of their life, they begin to vibrate more dramatically and distinctly. Ongoing vibration analysis flags these signs before significant damage occurs. Common failure modes that vibration analysis detects include:
•
Imbalance
•
Misalignment
•
Cavitation
•
Cracked/broken gear teeth
•
Looseness—both in chains and structural
•
Gear wear
•
Rolling element bearing defects
•
Resonance
•
Bent shafts
•
Multiple bearing issues
•
Sheave run-out
•
Electrical issues
•
Fluid and airflow issues.
Oil analysis and vibration analysis complement each other almost perfectly: oil analysis monitors and controls lubricant quality and contamination; vibration analysis monitors and controls balance, looseness and alignment.
In fleet industries, oil analysis is the primary technology because diesel engines predominate. In industrial applications, especially power generation and petrochemical, vibration analysis is the technology of choice. In general, industrial applications such as primary metals, pulp and paper, etc., use both methods together.
THERMOGRAPHY
The idea behind thermography is that an increase in heat indicates failing components. Thermography detects heat patterns and measures the temperature of electrical and mechanical components. The areas it identifies can indicate electrical resistance or excess friction. It also is ideal for identifying heat loss. Additionally, thermography can uncover problems with moisture, thickness, bonding, capacitance and friction. Thermography will pick up anomalies in motors, couplings, bearings, belts and sheaves, steam traps, heat exchangers and electrical systems/components.
Thermography detects issues that oil analysis can’t, such as the condition of rollers, the level of deposit build-up in storage tanks and the condition of high-speed bearings and couplings.
ULTRASOUND
Ultrasound is defined by high-frequency sound waves above 20 kilohertz (kHz) and up to 300 kHz and is one of the more flexible condition monitoring technologies. It is commonly used for leak detection (compressed gas) and mechanical and electrical inspections. For the latter, ultrasound can be used as a safety tool to identify arcing, tracking and corona.
Ultrasound relies on digital meters that measure high frequency signals and display the results in decibels per microvolt. Trending values point to potential defects caused by contact such as rubbing and friction. Ultrasound complements vibration analysis (which complements oil analysis) well.
SENSORS
Embedding condition monitoring sensors in machinery is becoming commonplace. “The growth in the Industrial Internet of Things (IIoT) as it relates to online real data monitoring is expected to be huge in the coming years,” Spurlock says. “Sensors have been around for over a decade but have been cost prohibitive until just recently. Imagine a suite of sensors that monitors vibration data, oil health, contamination and wear debris. These sensors constantly send data to the cloud where machine learning algorithms allow for dynamic alarms to be in place in order to immediately identify when a condition is changed along with a relevant corrective action recommendation. That day is here.”
He continues, “Oil analysis technology has been severely commoditized over the years. There is fierce competition within the laboratory world for end-user sampling dollars. In addition, oil analysis seems to be one of the most misunderstood tools of condition monitoring. The idea of inline monitoring should help to alleviate both of these issues and bring to light the true benefits of comprehensive condition monitoring and multi-technology integration.”
PERFORMANCE ANALYSIS
This is a basic but often neglected step. It involves comparing actual operating statistics with the manufacturer’s original parameters—usually posted on the machine’s nameplate. These statistics also are available in the equipment manual, online or via the manufacturer’s rep.
Combined with oil analysis, supplemental condition monitoring methods will be able to detect the vast majority of equipment issues—hopefully before they affect operations. If one method detects an anomaly, experts recommend employing a second technology for confirmation.
CASE STUDY: KAPSTONE PAPER
Industry leader KapStone Paper, located in Longview, Wash., produces a wide spectrum of kraft and recycled products ranging from containerboard, including liner and medium, to kraft papers, saturating kraft and folding carton board. It is a shining example of a company that makes full and effective use of integrated condition monitoring technologies. KapStone leverages oil analysis, microscopic analysis, vibration analysis, ultrasonic and thermal imaging.
Jeffrey H. DesArmo, KapStone’s lubrication manager, says, “At KapStone Paper, we have integrated several different technologies into our predictive maintenance program to help increase our uptime and reduce the number of failures we have.
“The benefits of oil analysis are many, and the ability to integrate other predictive maintenance technologies throughout our mill benefits us a great deal and provides for a more thorough and accurate diagnosis of equipment issues,” DesArmo adds. “We work with our vibration department on a daily basis sharing equipment related concerns as they are identified (
4).”
Out-of-spec oil reports are shared between the two crews, which review the historical oil and vibration data. The equipment may be re-sampled as needed and closely monitored for change. When the vibration group reports a motor that is noisy or has a high frequency event on a bearing and asks for lubrication, a lubrication specialist uses the UE systems ultrasonic meter to ensure that the right amount of grease is inserted to the bearing. Thermal imaging helps find hot spots and allows for the location of potential problems in larger, more complex systems.
DesArmo says, “Microscopic analysis is an effective method of identifying wear debris, as it allows us to see what type of particles are being generated in the oil, accurately count the particle numbers and examine their size and shape, which allows us to more accurately assess the machinery and the condition of the oil. We can have results as quickly as an hour after a sample is brought in.”
A good example of the benefits of integrated analysis at KapStone was an oil sample that came back OK—but the vibration department subsequently picked up a high gear mesh on a roll-mounted gearbox. Temperatures were up on the gearbox, and the motor was drawing high amps to keep running. “After performing a microscopic analysis of the oil, I noticed there was wear material in the oil going to the gearbox,” DesArmo says. “The wear material was coming from the pump that was feeding the gearbox from a larger oil reservoir and was not pumping properly. The pump was failing, and with the finding we were able to switch over to a backup pump and replace the failing pump on our time. The cost of the possible failure of a gearbox and downtime associated would have been in excess of $300,000.”
In situations where an oil sample cannot be taken during normal operating conditions, thermography and vibration analysis provide data without requiring downtime or interruption to operations. They also provide a picture of what is happening during actual operating conditions.
According to Doyle, in situations where an oil sample cannot be taken during normal operating conditions, thermography and vibration analysis provide data without requiring downtime or interruption to operations. They also provide a picture of what is happening during actual operating conditions. In addition to thermography and vibration analysis, ultrasonic analysis provides information on structural deficiencies before larger problems occur, which would not necessarily be picked up by oil analysis. The composition of gases generated in emission and effluent processing also can provide unique information regarding asset operating health.
Allied Reliability’s Spurlock has been working with KapStone. He explains that in addition to sending samples to an outside laboratory on a regular basis, KapStone purchased equipment to make patches and view them through a microscope onsite.
“This gives KapStone a very early indication of any potential severe condition,” Spurlock says. “Through this process, the lubrication supervisor prepares patches from oiled and greased components for review. On more than one occasion, they noted abnormal wear particles on the patch and were able to notify the vibration group for further review. In each instance, the vibration group confirmed the presence of a problem, although the vibration data had yet to reach a level of alarm. This allows the facility ample time to plan and schedule needed corrective action or overall component replacement.”
DesArmo explains that KapStone chooses to integrate predictive technologies for several reasons but primarily because of the amount of uptime and reliability they gain.
“Then there is the understanding of other disciplines and how they work,” he says. “Tying all of the technologies together, we find that we work better together than if each department is on its own trying to increase reliability, not knowing what the other is up to.”
CMaaS
Monitoring the health of critical machinery is an important component of an operational excellence strategy. Reliability services providers offer a menu of options that can include maintenance, reliability and operational consulting and services, training and staffing. They also implement and integrate oil analysis programs.
Condition monitoring as a service (dubbed CMaaS) includes a collection of components, solutions and support designed to extend equipment life and increase profitability. CMaaS reduces the effort to collect inspection data and integrate it into a single analyzable format. With inspection data stored in a central system, the integration of reliability engineering, condition-based maintenance, reporting, etc., enables an environment where vendors, contractors and internal personnel can collaborate. This improves the competitiveness of production facilities, raises product quality, increases uptime and production capacity and ultimately lowers costs.
The following is some of what to expect from a CMaaS provider:
Maintenance strategy review. This process ensures the customer is performing the correct maintenance on the right equipment at the optimal time and with the best resources. Ultimate goals include:
•
Aligning maintenance efforts to business needs
•
Reducing equipment damage and losses
•
Increasing availability and reliability
•
Reducing overall maintenance costs in a sustainable manner.
Planned maintenance routines. The reliability services provider will configure, support and deploy a planned maintenance routine. Benefits include increased resource productivity, greater reliability and uptime improvement, and a greater likelihood of meeting production targets and business goals. Effective planning and scheduling result in an efficient planned maintenance routine.
Work planning and scheduling. Planning and scheduling daily maintenance is a vital part of every industrial manufacturing operation. Well-structured, up-to-date planning will reduce costs and have a positive impact on safety and environmental programs by forestalling unexpected events.
Reliability, availability and maintainability. This provides an integrated analysis of expected system performance based on system design, operations and maintenance. It is a key component of lifecycle cost and asset management programs.
Risk-based inspection. This involves defining appropriate inspection techniques, and frequency is based on damage consequences and probability of failure. Examining risks enables optimum inspection programs.
Root cause analysis. This identifies the root cause of failure and identifies actions that will prevent recurrence. The process investigates three failure causes: (1.) physical or technical, (2.) human errors and (3.) organizational systems—operating procedures and decision making.
So for most equipment, oil analysis will be the most cost-effective method of determining the health of the equipment and the fluid. Oil analysis becomes exponentially more effective when teamed with complementary technology such as thermography or vibration analysis. Organizations that don’t already have an oil analysis program in place can either set one up with a few simple steps or opt for a reliability services provider that will design and administer the program for them.
“Oil analysis, thermography and vibration analysis are each condition monitoring tools that, when used in combination, can provide a fuller picture of an asset’s current health,” Doyle says. “The challenge in applying these various tools is to be able to combine the information in such a way that one data complements the others and is easily understood by the end-user and asset manager.”
REFERENCES
1.
The P-F curve represents the gradual loss of function. For a complete explanation of the term, see the video
PF Curve 101 – Keeping it simple here.
2.
Van Rensselar, J. (2012), “Maximizing the benefits of fluid analysis,” TLT,
68 (7), pp. 30-39.
3.
Van Rensselar, J. (2011), “Vibration analysis: The other half of the equation,” TLT,
67 (8), pp. 38-48.
4.
Kyle Newton, maintenance supervisor vibration department, KapStone Paper, collaborated with Jeffrey H. DesArmo on information presented in this article.
Jeanna Van Rensselar heads her own communication/public relations firm, Smart PR Communications, in Naperville, Ill. You can reach her at jeanna@smartprcommunications.com.