Food-grade lubricant additives: Growing safety demands require higher performance.
Dr. Neil Canter, Contributing Editor | TLT Feature Article December 2017
More demanding applications and safety concerns are requiring the use of better performing lubricants.
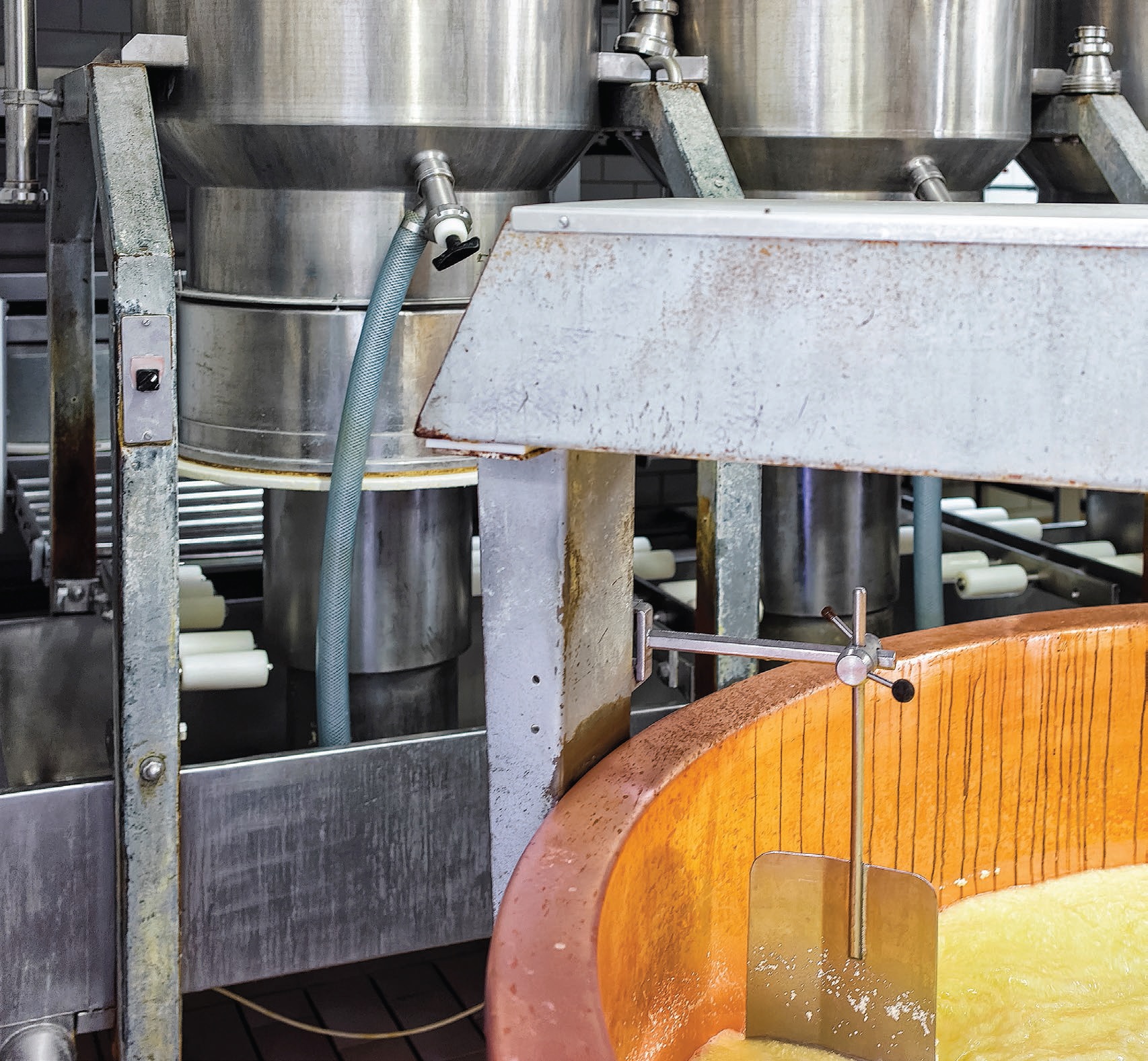
© Can Stock Photo / erix2005
KEY CONCEPTS
•
Growing demands placed on the planet’s food supply require better-performing food-grade lubricants and, as a consequence, additives that contribute better performance.
•
Concentration limits placed on HX-1 additives reduce their individual effectiveness, making it necessary for lubricant manufacturers to develop synergistic mixtures.
•
The use of higher-performing base stocks has enabled end-users to use H1 lubricants in all plant applications, even those not requiring a food-grade lubricant.
MUCH ATTENTION HAS BEEN PAID to the composition of non-food compounds needed to assist with the preparation, processing and packaging of food products. The reason is growing concern about food safety due to problems that have occurred periodically. One category of non-food compounds is lubricants.
An example is a past incident where 490,000 pounds of boneless hams were recalled after consumers reported a bad taste and burning in the throat for up to three hours after eating (
1).
Gear oil contamination was determined to be the cause.
Food safety concerns and the potential for product contamination during processing led to the establishment of regulations by the U.S. Food and Drug Administration (FDA) defining ingredients acceptable for use in formulating non-food compounds. Of particular interest are those non-food compounds that might have incidental food contact.
Sarah Krol, global managing director for NSF International in Ann Arbor, Mich., explains how U.S. regulations define a lubricant with incidental food contact, “A lubricant used in close proximity to food processing, preparation or handling operations where there is potential exposure of the lubricated part with the food being produced.”
Lubricants used in food applications were reviewed and approved in the past by the U.S. Department of Agriculture (USDA). In the late 1990s the USDA discontinued its review and approval program for non-food compounds, including incidental contact lubricants. Since 1998 NSF International has administered a voluntary review and registration program, modeled after the former USDA program to meet industry needs and identify products that have been reviewed and deemed acceptable by an independent, third-party organization. Lubricants acceptable for use where incidental food contact is possible are included in the H1 category. Additives and other ingredients that can be used in H1 lubricants are designated under the HX-1 category.
Krol says, “Chemicals or mixtures are reviewed by NSF for use as additives in lubricants. Due to the chemical nature of some additives, they may not be acceptable for use in some lubricant products or in specific types of applications. The limitations associated with any HX-1 additive can be found within the NSF Registration letter.”
STLE Past President Robert Baker, technical sales & marketing advisor for King Industries in Norwalk, Conn., says, “The FDA is responsible for approving new ingredients that can be used as HX-1 additives. Approved ingredients are listed by FDA in the Code of Federal Regulations under 21 CFR 178.3570 (
2).”
Krol indicates that the NSF Registration Guidelines for H1 lubricants, which are modeled after the FDA regulation in 21 CFR 178.3570 provide requirements for HX-1 additives.
One other potential option for ingredients used in formulating H1 lubricants are those ingredients defined as GRAS, which is an acronym for the phrase Generally Recognized As Safe. This criterion is regulated by FDA, which acknowledges a substance as GRAS if it is generally recognized among qualified experts to be safe for use under the conditions of its intended application (
3). The final rule on GRAS was issued by FDA in 2016 and can be found at 81 FR 54960.
Baker points out that historically H1 lubricants displayed inferior performance compared to lubricants used in non-food related applications. He says, “Formulating with the best HX-1 additives did not overcome this deficiency. Instead, H1 lubricant quality has improved over the past 20 years more through the availability of new base stock options (such as Group II, III and synthetics) than from the development of new additives. These new base stocks have distinguished themselves compared to the traditional H1 lubricant base stocks, vegetable oils and white mineral oils.”
This article discusses current food-grade lubricant additive trends and determines what additive types need to be upgraded to improve performance. Key industry experts were contacted to gain their perspective on food-grade lubricant additives.
The following experts were interviewed.
1.
Dr. Philip Ma, BASF Corp.
2.
Daniel Vargo, Functional Products Inc.
3.
Robert Baker, King Industries
4.
Dr. Thomas Klein, LANXESS Deutschland
5.
Sib Hamid, Lubriplate Lubricants Co.
6.
Sarah Krol, NSF International
7.
Philip Levy, Novitas Chem Solutions
8.
Darren Lesinski, Total Specialties U.S., Inc.
9.
Tyler Housel, Zschimmer & Schwarz, Inc.
KEY FOOD-GRADE LUBRICANT ADDITIVES
Dr. Thomas Klein, technical manager for LANXESS Deutschland GmbH in Mannheim, Germany, provides a list of the eight main additive types used in formulating food-grade lubricants.
•
Antioxidants. Incidental food lubricants are exposed to oxidative stress in a similar manner to conventional lubricants due to the exposure to heat (up to 180 C). Furthermore, approved hydrocarbon base oils have no aromatic content, which limits solubility and high saturation that leads to low required treat rates. There are many antioxidants available for incidental food lubricants.
•
Antiwear (AW) additives. One additive available is a salt of an alkylammonium phosphate ester that also provides some rust prevention. The maximum treat rate for this additive is 0.5%.
•
Extreme pressure (EP) additives. The commonly used member of this additive class is triphenylphosphorothionate (TPPT) that contains only “inactive” sulfur. The lubricant industry can cope with these constraints because heavy-duty lubricants are rarely required in food industry applications.
•
Corrosion inhibitors. Rust and corrosion inhibitors or metal passivators are needed to cope with high-moisture conditions. Additives available are the salts of alkylammonium phosphate esters and oleyl sarcosine. Both types are compliant with food contact requirements up to a content of 0.5%.
•
Thickeners. This additive class is needed to enable food-grade lubricants with varying viscosity grades to be prepared. Typical thickeners are polyisobutylenes (PIBs) for mineral oil-based lubricants.
•
Tackifiers. In food-grade lubricant applications such as chain oils, tackifiers are needed to improve the adherence of lubricants to surfaces. High molecular weight polybutene tackifiers are the only HX-1 additives available.
•
Pour point depressants. Copolymers prepared from maleic anhydride and styrene are highly effective in lowering the pour point of technical white mineral oils. They are needed for applications where food manufacturing occurs at low, controlled temperatures.
•
Defoamers. Foam can be an issue in food manufacturing, which means that defoamers are needed to suppress it. Silicon defoamers such as polydimethylsiloxanes are approved for incidental food contact because of their low surface tension, water insolubility, thermal stability and chemical inertness. Defoamer molecular weights must be more than 2,000 grams per mole, and they are highly effective in all types of approved base stocks.
Daniel Vargo, senior research chemist for Functional Products, Inc., in Macedonia, Ohio, gives a few additional examples of food-grade lubricant additives. He says, “The main categories of antioxidants used are alkylated diphenylamines, high molecular weight hindered phenolics and certain phosphites. Alkylated tolyltriazoles are used as yellow metal deactivators, and corrosion inhibitors such as amine phosphates are used for antiwear and rust inhibition. For aqueous additives, water-soluble disodium sebacate is used as a corrosion inhibitor.”
STLE-member Phil Levy, vice president, sales and marketing for Novitas Chem Solutions, LLC, in Houston, says, “Food-grade lubricant suppliers will select the key additives needed for formulating their products based on the ultimate end-use of the fluid or grease and the type of base stock or base grease used. As different base stocks and base greases have differing inherent properties, this dictates the levels and types of additives used.”
STLE-member Dr. Philip Ma, scientist at BASF Corp. in Tarrytown, N.Y., indicates that a listing for all HX-1 additives is readily available. He says, “Food-grade additives are listed in the NSF White Book™ - Nonfood Compounds Listing Directory under HX-1. Users of these additives should follow the guidelines established in Code of Federal Regulations under 21 CFR 178.3570 (
2).”
TRADITIONAL CHEMISTRIES NOT ALLOWED
Not all of the known additives available to lubricant manufacturers can be used in H1 lubricants. Levy says, “There are quite a number of chemistries that cannot be used such as chlorinated paraffins, graphite, molybdenum-based additives and zinc dialkyldithiophosphates (ZDDPs). Many are popular and very effective in specific applications but not items individuals would want to accidentally drip into their dinner.”
Vargo adds, “Active sulfurized extreme pressure additives such as sulfurized olefins are not used in H1 lubricants. Neither are zinc or heavy metal dithiophosphates or chlorine containing additives.”
Baker reveals that no traditional metal salt corrosion inhibitors were approved until 2010. He says, “A synthetic calcium sulfonate was approved at that time. I believe there are no other sulfonates that meet the HX-1 requirements.”
MOST CHALLENGING H1 LUBRICANTS
Since not every additive used in lubricant applications can be used in H1 lubricants, there are certain food-grade lubricants that are more challenging to prepare than others. Ma says, “Food-grade gear lubricants experiencing high-load, high-EP pressure are generally the most challenging to formulate because only some less-active EP/AW additives can be used, and the amount allowed is limited. However, food processing lubricants do not experience EP wear in a similar manner to lubricants used in mining and wind turbine applications, so the challenge is relative.”
Klein focuses on H1 lubricant applications where oxidation reduction is not the only requirement. “Any lubricant that is used in applications beyond good oxidation inhibited base stocks will be challenging to prepare,” he says. “High-temperature applications where gear oils and oven chain oils are used are two examples.”
Baker agrees that oven chain oils are difficult to formulate. He says, “Oven chain lubricants require appropriate base stocks to start with followed by the use of approved antioxidant chemistries that can be blended synergistically to extend the life of the lubricant.”
Levy believes the demanding requirements for HX-1 additives will in general limit the options for H1 lubricant suppliers. He says, “The industry restriction that allows only the use of registered additives/components from the suppliers and the ever more demanding and stringent quality requirements from customers and users alike.”
The perspective of two representatives from food-grade lubricant suppliers also was requested. STLE-member Sib Hamid, vice president, general manager of Lubriplate Lubricants Co., in Toledo, Ohio, says, “Gear lubricant formulations with high EP requirements are the most challenging product developments where FDA additive limitation does not allow formulators to meet EP requirements with the additive allowable limit of 0.5% maximum.”
STLE-member Darren Lesinski, technical director, Total Specialties USA, Inc., in Linden, N.J., says, “Any application that requires improved performance attributes at higher (or lower) running temperatures and/or involves high pressure where EP additives are required presents a challenge for the lubricant supplier.” Examples include baking chains, can seamers, pharmaceutical centrifuges, air compressor (full duty-high load) and freezer trolleys.”
If wash-down is involved, then this also can present durability problems for the lubricant supplier. Lesinski says, “Any application that has a high frequency of sanitation via wash-down would also require a robust formulary chemistry if the mechanical component cannot be relubricated on a regular basis.”
CONCENTRATION LIMITS
One of the challenging aspects of formulating H1 lubricants is the concentration limits placed on HX-1 additives when they are approved by FDA. Vargo says, “Typically the maximum concentration for most HX-1 additives is 0.5% by weight. This additive level might not be sufficient to provide the performance level required. Therefore, additional HX-1 additives would be required to boost performance. This can significantly increase the cost of the formulated lubricant.”
Levy indicates that some HX-1 additives cannot be used at levels above 0.1%. “Depending upon the performance level requirements of the fluid or grease, the maximum treat rate can make it difficult to pass the necessary testing criteria of various applications,” he says. “In those circumstances, formulators need to ‘load up’ on other additives within the same performance class, but care must be taken to use additives that have sufficiently different chemistries not to be viewed as equivalent and causing the total treat rate to exceed the maximum limit allowed. Some additives are synergistic while others have secondary properties offering added benefits allowing the finished H1 lubricant to meet the specifications for its intended use.”
Baker says, “The biggest challenge is to formulate H1 lubricants to meet the requirements of AW and EP tests, especially the latter.”
Klein presents an example of how to work with EP and AW additives to overcome the 0.5% concentration limit. He says, “It is possible to make use of synergistic mixtures of, for example, TPPT and amine phosphates, which may raise the performance depending upon the base stock used.”
Lesinski and Hamid are in agreement that combining different chemistries is the one strategy to use to overcome the concentration limit issue. Lesinski says, “Some basic fundamentals such as optimizing the phenolic to aminic antioxidant ratio in specific base stocks, or certain synergies between antioxidants and yellow metal deactivators are typical pathways. Additive purity also must be considered when additives are produced by different manufacturers particularly in the case of antioxidants.”
Levy demonstrates differences that can exist in the purity of an HX-1 additive. He says, “Figure 1 shows an image of an additive on the left that is approved for HX-1 but exhibits a noticeable color and offensive odor due to the presence of byproduct for this chemistry. To the right of this additive is an image of a second additive that contains the same chemistry but further purification has improved the quality. The white color of the additive on the right is one obvious aspect of the improvement in quality, but the removal of byproducts is another, although that cannot be seen visually.”
Figure 1. HX-1 additives can exhibit different levels of purity. The image on the left represents an additive with a noticeable color and offensive odor. Purification produces an additive with higher purity, which is noted by the white. (Figure courtesy of Novitas Chem Solutions, LLC.)
ADDITIVE TYPES: IMPROVEMENT NEEDED
Two factors need to be considered from the formulation standpoint in addressing the question of improving the performance of specific additive types. What additive types offer the least available options to the formulator and where is there a need to improve the performance of specific additive types?
Lesinski says, “The additive type with the least available options is EP additives that can deliver pure EP performance as tested in either the four-ball EP or pin and vee block test.”
Hamid also believes that the additive type with the fewest HX-1 options is EP additives. He adds, “The EP and AW additives available in the marketplace exhibit adequate performance but there is need for improvement in both additive categories.”
DEVELOPING HX-1 ADDITIVES
The limitations placed on the types of additives that can be approved for incidental food contact and the restrictions placed on their treat rates makes it very difficult to develop new options. Klein says, “The information required for a rigorous food safety assessment for lubricants is difficult to compile because of the quantity of lubricant, which (a.) could possibly be incorporated into the food (under varying situations!) and (b.) would not affect its safety, and quality is difficult to determine. The assessment underlying HX-1 approval is based on 21 CFR 178.3570 requirements, which are not specific about the measurement and testing protocols. This means that an additive candidate for HX-1 approval must undergo a comprehensive set of toxicological studies.”
Klein continues by indicating one of the key pieces of information that needs to be determined on a new additive candidate to establish a maximum treat rate in H1 lubricants. He says, “For new, and in some cases established additives, toxicological data have to be created and a hazard risk assessment has to be performed to determine what is the Acceptable Daily Intake in milligrams per kilogram of body weight, which is costly and time consuming. There is some risk that the maximum treat rate for an additive used in an H1 lubricant will not be satisfactory from the performance standpoint.”
Klein points out that the addition of mineral oil to food must not exceed 10 ppm (see 21 CFR 178.3570).
Levy agrees. “Food Contact Substance Notification applications are required to register new HX-1 additives,” he says. “The pathway to approval is typically quite expensive due to the need for extensive analytical and toxicological testing to assure that the specific substance is safe for use in H1 lubricants. While this step is necessary to ensure public health and safety, it adds costs that may prevent effective additives from being used in food-grade lubricants.”
Baker feels that this cost for approving HX-1 additives is in addition to the time and expense additive suppliers face in commercializing new products for all applications. He says, “Additive suppliers cannot lose sight of the initial costs for chemical inventory registrations that span all of the major world markets where lubricant companies have to compete.”
UPGRADING THE BASE STOCK
One way to improve the performance of H1 lubricants is to upgrade the base stock used. STLE-member Tyler Housel, CLS, head of Lexolube Division of Zschimmer & Schwarz in Milledgeville, Ga., says, “Years ago, vegetable oils, mineral oils, some polyalkylene glycols and silicones were the only base stocks that could be used in H1 lubricants. Even the best additives could not produce all of the required lubricants with this limited slate of base stocks. Therefore, food processors often used unregistered lubricants for some applications.”
But now, with the availability of more HX-1 registered base stocks such as polyalphaolefins (PAOs), synthetic esters and alkylated naphthalene (AN), HX-1, additives can help the formulator meet all performance targets. Many food plants today operate successfully using only H1 lubricants.”
Housel feels that the current HX-1 base stocks and additives are generally compatible with each other. He says, “There are some examples of incompatibilities, but the lubricant industry has successfully used those ingredients where some additive-base stock compatibilities exist.”
Housel indicates that some base stocks such as PAOs and perfluoropolyethers can be difficult to use with certain additives, and solid lubricants such as boron nitride and polytetrafluoroethylene can be difficult to disperse.
To overcome the concentration limits encountered with some HX-1 additives, Housel proposes upgrading the base stock as an alternative strategy to meet the performance requirements for H1 lubricants in specific applications. He says, “Mineral oil or PAO-based formulations will see improvements in additive solubility, cleanliness and drain interval with the addition of as little as 10% of a more polar base oil such as an HX-1 synthetic ester or alkylated naphthalene. While this will not match the performance of an H1 lubricant formulated with 100% ester as the base stock, it can be a cost-effective way to get around additive concentration limits and build a good quality H1 lubricant.”
Vargo says, “Synthetic esters and ANs are recent products that can serve as base stocks, and improvements in performance such as film strength and high-temperature stability can be seen. Unfortunately it comes at a cost as these base stocks are two to three times more expensive than traditional base oils.”
An upgrade in high-temperature stability can be seen in Figure 2, which shows an example of how the addition of a synthetic ester in small increments can boost the performance of PAO in a thermal stability test conducted at 260 C for 20 hours. The base material is “PAO-100,” which contains 100% ISO VG 68 PAO. Addition of 5% and 10% of a synthetic ester to this PAO produces mixtures designated as “E-5” and “E-10,” respectively. As a positive control, 100% ISO VG 68 synthetic ester is designated as “E-100.” All of the jars in Figure 2 are shown after the completion of the thermal stability test.
Figure 2. Jars showing results from the thermal stability testing of PAO (PAO-100), a synthetic ester with the same viscosity (E-100) and blends of 5% (E-5) and 10% (E-10) of the ester in PAO at 260 C for 20 hours are shown. E-100 shows superior thermal stability as compared to PAO-100, but introduction of small percentages of ester (E-5 and E-10) to PAO leads to an improvement in thermal stability. (Figure courtesy of Zschimmer & Schwarz, Inc.)
Housel says, “‘E-100’ exhibits superior thermal stability compared to ‘PAO-100’ as shown by the reduction of insoluble additives. Use of the synthetic ester at 5% and 10% produces much less residue (in ‘E-5’ and ‘E-10’). This indicates that upgrading the PAO base stock with incremental additions of a synthetic ester with a comparable viscosity leads to an improvement in thermal stability.”
Baker adds, “The new base stocks recently introduced have demonstrated the ability to enable formulators to develop better H1 lubricants while not having any effect on the HX-1 additives already in use. ANs have been found to improve the oxidative and thermo-oxidative properties of common base stocks such as API Group II, III and IV when used at treat rates between 10%-15%.”
As an example, a thermo-oxidative stability study using the Pressure Differential Scanning Calorimetry test (ASTM D6186) shows how the performance of an H1 lubricant with a PAO 4 (4 cSt at 100 C) base stock can be improved through the introduction of AN. In Figure 3, pure HX-1 AN 6 (6 cSt at 100 C) shows no response to an isothermal PDSC at 170 C after two hours. The oxidation induction time (OIT) for PAO 4 is less than 10 minutes under the same conditions. When 10% AN 6 is added to the PAO base stock, the OIT improved to 30 minutes and reduced the maximum heat flow to about half.
Figure 3. A Pressure Differential Scanning Calorimetry test demonstrated that introduction of 10% alkylated naphthalene to PAO containing an alkylated diphenylamine antioxidant leads to an improvement in performance. (Figure courtesy of King Industries.)
Further testing was done by adding an HX-1 approved antioxidant from the alkylated diphenylamine class at a treat rate of 0.2%. Baker says, “Both of the curves are shifted to a higher OIT as shown in Figure 3, and the PAO modified with AN 6 continues to show a reduced exotherm.”
For comparison purposes, the same study was conducted with white mineral oil in place of PAO. Baker says, “The 10% AN 6 modification of the white oil base stock shows improvement in OIT comparable to the PAO study; however, when the antioxidant is added, the OIT is not significantly increased, although the exotherm is reduced. This study demonstrated that adding AN 6 to white mineral oil does not have the same impact seen with PAO and that the use of ANs in general is typically reserved for premium base stocks and/or high temperature applications.”
Baker indicates that blends of PAO 4 with AN 6 are particularly suitable for H1 oven chain lubricants.
Ma stated that use of more thermo-oxidatively stable base stocks also can lead to use of fewer HX-1 additives. He says, “Synthetic esters and ANs are more thermo-oxidatively and hydrolytically stable than castor oils enabling the resulting H1 lubricants to operate in harsher environments for longer time intervals. This means that a lower treat rate of antioxidants will be needed.”
Levy believes that the availability of new base stocks has improved the options available to the food-grade lubricant supplier and led to increasing use of HX-1 additives. He says, “The new base stocks offer enhanced stability and other performance benefits that have been previously unattainable in traditional food-grade base stocks. The result has led to a broader use of food-grade lubricants and HX-1 additives in general.”
Levy cautions that there are challenges in working with the new base stocks. He says, “Due to specific and inherent physical properties in synthetic esters and ANs, these new base stocks often require specific, narrow or even a new set of additives to be used. These new base stocks have different responses to different additives leading to a wider variety of additive and formulation recommendations from suppliers and an increased number of options for the formulator.”
Housel also sees an improvement in the availability of HX-1 additives that occurred when the new base stocks became eligible for use in H1 lubricants. He says, “When the first HX-1 synthetic ester base stocks were introduced, most of the familiar additives for esters were not HX-1 registered. Additive suppliers were persuaded to pursue HX-1 registrations for the most important additives used in synthetic ester fluids, which has led to formulators having additional HX-1 additives to select for use in their applications. This process was a win for both additive and base stock manufacturers as the newly formulated H1 lubricants helped expand the market by satisfying customer demand for higher performance.”
FUTURE DEVELOPMENT OF HX-1 ADDITIVES
Levy considers product quality to be one of the issues that the lubricant industry will be looking to improve in the future. “The emphasis placed on improving product purity will lead to minimizing minor byproducts that can be present in currently used HX-1 additives,” he says. “Some of these byproducts can be toxic, but the additive in question still qualifies for HX-1 status, as often the presence of the byproduct(s) is not addressed specifically in the FDA regulations.”
While purity is a priority, Levy still feels that better-performing additives are required. “The additives that will be developed in the future cover the spectrum of properties needed today,” he notes. “Fluids and greases are being used in tougher and more demanding environments, which means that better antioxidants, AW, EP and corrosion inhibitors, to name four additive types, will be needed to assure adequate performance.”
Baker is concerned that additive options for the future may be limited because of the high barrier for approval. He says, “Additives are just not being developed exclusively for food-grade applications. If they do not offer a benefit for non-food-grade applications, then there will not be justification for the cost of testing for FDA approval.”
As the global food supply expands with the aim of feeding 10 billion people worldwide by the year 2050, demand for food-grade lubricants will continue to increase globally, leading to the demand for better performance and, as a consequence, for additives that will provide better functionality. Krol says, “Food safety regulations are evolving all over the world and are now engrained into the minds of food processors. Processing facilities must establish and implement a food safety system that includes an analysis of hazards and risk-based preventive controls. As today’s food manufacturers realize the importance of identifying contamination risks the correct use of third-party registered products for different applications in facilities provides a reliable prerequisite.”
Baker adds, “Besides improvement in food-grade lubricant quality for required H1 applications, the end-user can choose to use the H1 lubricant in all applications in the same plant, eliminating the risk and cost of inadvertently using a non-food-grade product in error.”
HX-1 additive use will continue to increase as food-grade lubricant suppliers demand better components for use in their products. The challenges faced by H1 lubricant suppliers in only being able to use certain additives in specific concentration limits can be overcome through the use of new base stocks, whether individually or in blends.
REFERENCES
1.
Please click
here.
2.
Please click
here.
3.
Please click
here.
Neil Canter heads his own consulting company, Chemical Solutions, in Willow Grove, Pa. You can reach him at neilcanter@comcast.net.