Complexity in ISFA (in-service fluid analysis): Part XXXV
Jack Poley | TLT On Condition Monitoring November 2017
Holistic condition monitoring in the 21st Century: Part VII
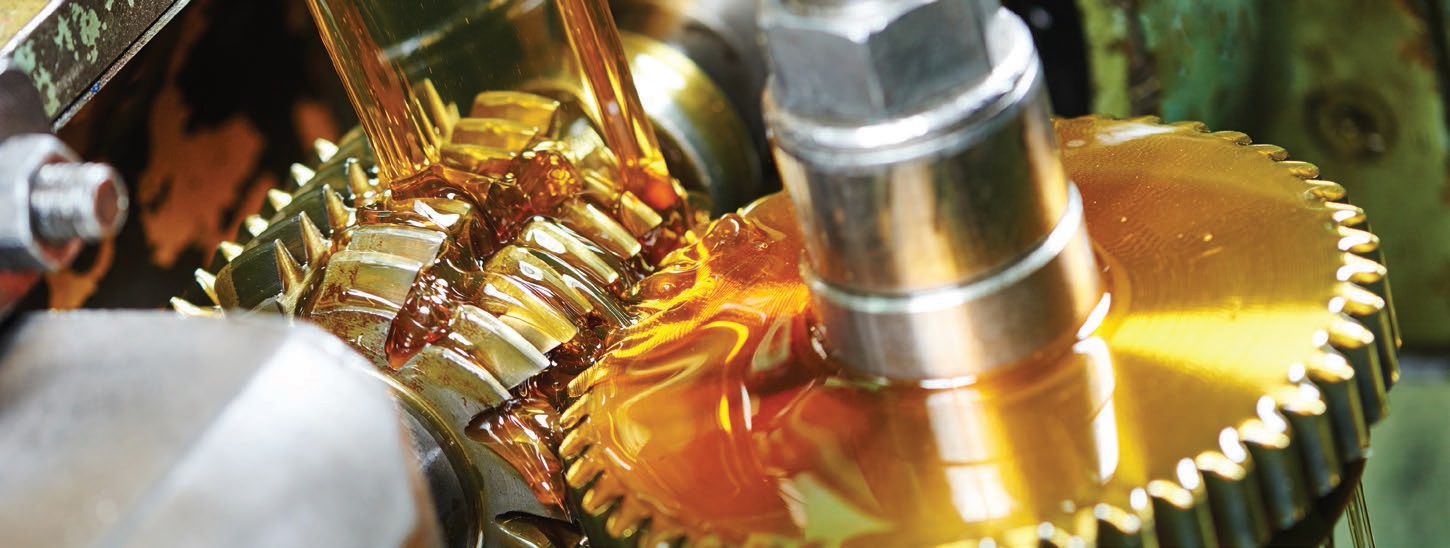
© Can Stock Photo / kadmy
WITH RARE EXCEPTION, IRON (Fe) is the most essential wear element for which to analyze and quantify because it is almost always the dominant element in lubricated machinery. Not having Cu, Al, Pb and let alone Si—the next most important elements—would be extremely limiting, but not having Fe would be fatal in most any case with respect to having a plausible chance of detecting trauma with any dependability.
Last column I mentioned the recent arrival of ISFA instruments using magnetometric methodology for measurement of Fe concentration. Not to be equated with PQ or quasi-scalar direct-reading ferrography that has been supplanted by PQ for the most part, these instruments producing a scalar result representative of an undisclosed Fe content at a relative magnitude. The newer instruments provide a much more precise indication of Fe in units those of us in ISFA are quite familiar with, namely parts-per-million (ppm).
Most methods for Fe detection, whether in relative scalar representation like PQ or ppm precision, cannot supply particle size distribution, but some instruments do address size. Table 1 is a partial list of available instrumentation for Fe detection. The variety is great.
Table 1. Ferrous Wear Metal Detection Methodology
Further comments on the methods:
A.
AA. AA is obsolete for purposes of wear metals analysis, if for no other reason that only one element can be analyzed per pass. Typical elemental analysis involves inspecting for at least 10 wear metals or metal-like elements and maybe another 10-15 supporting elements for additives and contamination dependent on the component type.
B.
RDE. RDE is the first automated, direct-reading spectrometer to perform multi-elemental analyses in one pass, serving numbers of commercial labs well in the 1960s and forward. Its greatest advantage over competing technology was the absence of sample preparation, i.e., samples are analyzed neat. All that was involved was shaking well and pouring a small sample.
C.
ICP. ICP may now be the most popular in commercial labs, or at least at parity with RDE. While a solvent dilution is necessary to conduct this analysis, it has the advantage of being easiest to automate, an advantage many labs covet.
D.
FWM. The Ferrous Wear Meter—a very simple but elegant, lowest-cost instrument to provide Fe in ppm units.
E.
LNF 230. Laser Net Fines was invented in the late 20th Century, but new capability involving magnetometry was recently added for this model by SSI (Spectro Scientific, Inc., which acquired the technology from Lockheed Martin), adding tremendous value to this instrument’s varied output:
•
Particle counter
•
Fe ppm + some size binning
•
Water
•
Particle morphology at 20µ and greater.
No instrument other than an infrared spectrometer has offered such an array of useful data; that the LNF addresses wear rather than only fluid condition, however, makes it especially impressive.
F.
Q5800. Designed for military readiness, the Q5800 incorporates four distinct instruments:
•
X-ray fluorescence for metals analysis
•
VIS
•
Particle count
•
IR (infrared, not FTIR).
G.
Sensors. It was a remarkable achievement, also at the turn of the last century, to get sensors to survive continuous contact with hot, contaminated lubes, yet still be able to provide highly useful real-time Fe indication, including a ferrous particle count. The problem with sensors, however, aside from their expense that confines them mostly to military, oceangoing vessels and other highest-value machinery, is that their detection limit on the small side of particle size is a rather limited 40-100µ,* dependent on the manufacturer. Wear particles of these sizes are, of course, usually indicative of fatigue-oriented events. Accordingly, once particles begin to be detected, one must give heightened attention to rates of increase.
SUMMARY TAKEAWAYS
•
RDE and ICP have for years done a great job in a lot of situations involving hundreds of millions of samples in terms of detecting meaningful wear occurrences and patterns, but there is a growing demand for large-particle information, large particles being the harbingers of catastrophic failure.
•
New and newer technology has come along to bridge that gap of small versus large so that much more can be inferred and understood in the wear of lubricated machinery.
•
ISFA purveyors find themselves with options not available in yesteryear, and, dependent on their clientele’s machinery types, should be looking to integrate some of this new, particle-based technology in their test packages.
•
Despite all the advances, each method has its strengths and limitations. One-instrument-does-all does not yet exist (and I’m done predicting the when…).
*That much difference, frankly, might bias many buyers, all other specifications near equal. 40µ is already considered a “large rock” in the wear particle world. 100µ is a large “boulder.” While any qualified sensor will prove capable of detecting catastrophic wear particles, the timeline in the progressive development of detectable amounts of 40µ versus 100µ particles could easily be fatal in a data evaluation sequence. A sensor with that much difference in its instrument’s lower-size sensitivity would seem to have an enormous advantage over the other in most situations.
Jack Poley is managing partner of Condition Monitoring International (CMI), Miami, consultants in fluid analysis. You can reach him at jpoley@conditionmonitoringintl.com.
For more information about CMI, visit www.conditionmonitoringintl.com.