Functional Products Inc.
Pushing Tackifiers to Higher Temperature
By Erik Willett, Daniel Vargo, David DeVore | TLT CMF Plus November 2017
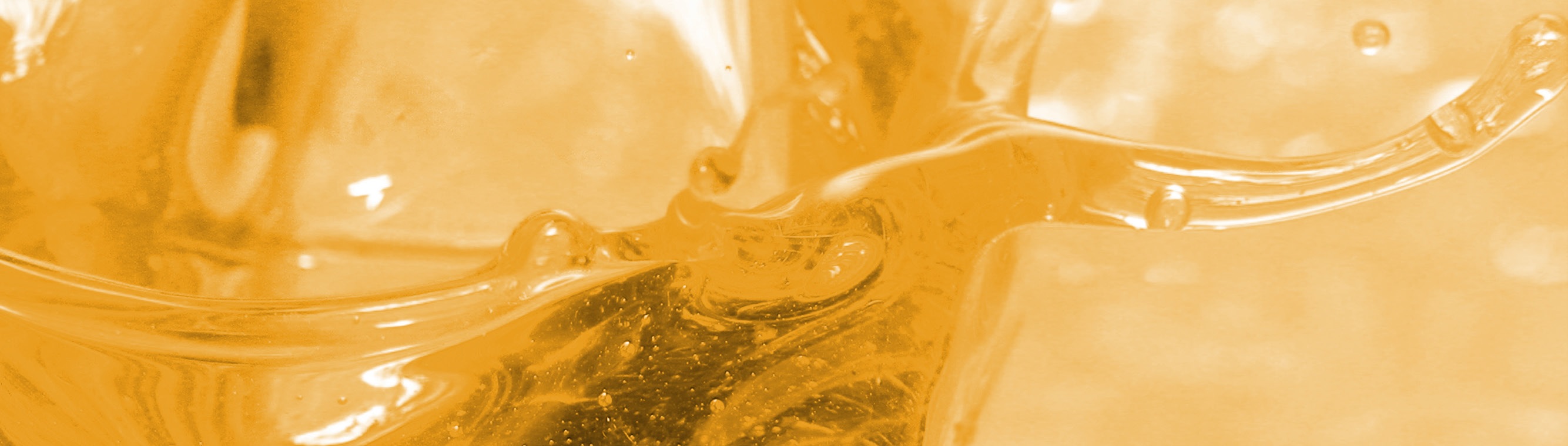
WHAT IS A TACKIFIER?
In lubricant oil applications a tackifier is a solution of ultra-high molecular weight (M
v from 500k to >1M) polymers in oil which contribute cohesive tack or stringiness to the oil (
1). This non-Newtonian behavior improves the adherence of oil to moving surfaces to reduce fling-off or drip, and improve the feed of oil through a mechanical system. Tackifiers also modify the surface tension of oil to reduce misting by coalescing fine oil mist into larger droplets to improve fire safety and promote the wetting of oil across metals to ensure uniform surface coverage.
HOW TO USE TACKIFIERS.
The suggested treat rate for a tackifier depends on the degree of tack desired. Tack at Functional Products Inc. is quantified as “string length” via the ductless siphon technique and correlates to the longest string of oil obtained by evacuating a column of treated oil by vacuum through a narrow capillary tube (
2, 3). Concentrated and exceptionally high molecular weight products can produce oil strings up to a foot in length at 0.5wt% treat in ductless siphon. Due to the highly effective nature of the dissolved polymers, tackifiers are applied at up to 1wt% until light duty applications and several percent under extreme conditions. The exact treat rate required will depend on application, operating conditions, viscosity grade, and service interval of the final product.
Applying a tackifier to an existing formulation is quite simple since the product will impart stringiness, anti-misting, and wetting behavior to oil at <1wt% without a significant change to viscometrics. If needed, tackifiers can be tailored to an application according to the polymer selection, concentration, and required viscosity.
Figure 1. Starting treat levels for tackifier by application. *The actual treat level is best determined by the formulator.
THE SCIENCE OF TACK.
It is important to distinguish between two categories of “tackifiers” in the additive market: lubricant oil tackifiers which use high molecular weight polymers to contribute cohesive tack to lubricants, and adhesive tackifiers that employ low molecular weight polymers to add adhesive tack to coatings. Cohesive tack – an internal property of the treated oil that imparts non-Newtonian behavior as stringiness – is measured through the ductless siphon or modified probe tack methods while adhesive tack – an external property that adheres two different surfaces – is quantified by methods such as pull-off force from a metal surface (
2, 3, 4).
The two predominant polymer chemistries for tackifiers are polyisobutylene (PIB) and olefin copolymers (OCP). Each chemistry presents its own advantages and limitations according to its molecular structure; this trade-off between properties and structure is the core of material science. The chemical scheme for PIB and OCP are shown below along with a simulated polymer coil to demonstrate the difference in size of the structures with equal chain length (100 repeat units, n=100; hydrogen atoms excluded for clarity).
Cohesive stringiness occurs through the entanglement of very long polymer chains in oil to form an entangled network. This entanglement provides internal cohesion between the oil molecules and greatly reduces the responsiveness of the oil as the oil begins to acts as a non-Newtonian fluid. The difference in structure between PIB and OCP affects the ability to form this network and produce tack. PIB remains the premier polymer for tackifiers due to the unique dialkyl structure of the isobutylene monomer. In a monosubstituted (one alkyl branch per unit) OCP, the single branch hinders the free rotation of the polymer chain and prevents the polymer chains from entangling as readily. The dialkyl substitution (two methyl units on one carbon chain) of PIB eliminates the hindrance and promotes the flexibility of PIB (
5). For a given chain length (Mv), PIB will outperform an OCP in string length. PIB tackifiers also benefit from higher commercially available molecular weights than most OCP.
Figure 2. Schematic of PIB and OCP monomer structure and representative polymer coils (n=100)
THE PROBLEM OF HEAT.
Current trends in oil are leading to hotter, higher power density applications which has been enabled by PAO and synthetic ester technologies (
6). Hydrocarbon-based tackifiers remain rooted in 20th century technology which continues to provide cost-effective options for all applications but is ill-suited for a high temperature future (
7). While PIB-based products provide greater tack than OCP the PIB chemistry is more thermally sensitive. At temperatures over 80˚C PIB reaches a thermodynamic tipping point known as the “ceiling temperature.” Here the thermodynamic balance between a polymer chain and free monomers shifts toward depolymerization. PIB’s unique dialkyl structure provides high flexibility at the expense of carbon-carbon bond strength along the backbone. All polymers have this ceiling temperature but it is usually in excess of 200˚C and instead oxidative degradation becomes the dominant thermal degradation mechanism such as with OCP (
8). Degradation from ceiling temperature or oxidative damage will steadily reduce polymer size and result in an eventual loss of tack.
Figure 3. Degradation of an example 1wt% PIB in 4cSt Gr. III oil over time at various storage conditions (9)
Previous work by Functional Products Inc. in 2004 and again in 2017 has identified that oil impurities found in Group I and II oils could accelerate the loss of tack above the ceiling temperature in PIB-treated oils (
9, 10). The original work concluded that diluent oil from a Group I-based tackifier was sufficient to compromise a Group III formulation. This lead to faster loss of tack than even shown in Figure 3, above. The later work reapproached this issue by adding controlled amounts of singular impurities to Group III oil formulation to pinpoint which species were most responsible. It was found that nitrogen was the most likely bad actor while aromatics could actually extend the useful lifetime for tack at elevated temperature. The exact relationships between PIB and impurities were complex. For example, monocyclic aromatics selectively protected higher MW tackifiers and polycyclic aromatics only helped lower MW tackifiers. Sulfur was beneficial for both sizes of PIB.
NEW CHEMISTRY TO ADDRESS HEAT.
Further investigation of beneficial ‘impurities’ in the 2017 study lead to the identification of a novel “tack preservative” for PIB tackifiers effective to 100 ppm. This synergistic additive exhibited excellent performance in a sample formulations using a Group III base stock and Group I/II VI improver and PIB tackifier. No reduction in string length was observed after 2hrs at 200˚C in a sample treated with 0.2% of the preservative while the control group (no tack preservative) lost 30%. A separate comparison at 0.1wt% versus 0.1wt% BHT demonstrated 75% loss of tack in 1hr at 150˚C for the control, 75% loss in 3.5hr for BHT, and only 20% loss after 8hrs for the tack preservative. It was also demonstrated that PIB tackifier treated with the preservative occurred much lower string length loss than an equivalent OCP tackifier (
9). This work was concluded with the postulation that the preservative acts by ‘mending’ the radical chain ends where PIB has thermally broken. Further work is underway to develop this finding.
PIB and OCP polymers are only a small part of the commercial polymer sector. There are roughly thirty polymers common in industrial applications and these are separated into four tiers (
11). PIB and OCP are generally considered ‘commodity polymers’, the lowest tier of pricing and performance. ‘Engineering polymers’ encompass polymers with higher operating temperatures such as polyesters and acrylates. ‘High performance polymers’ include aromatic polymers such as polysulfones, fluoropolymers, and aromatic nylons. These high polymers possess operating temperatures up to 300˚C which would enable sustained use in a high-temperature application (
11).
FUTURE WORK.
Functional Products Inc. is currently at work in developing strategies to find and deliver high temperature polymers to overcome the thermal sensitivity of conventional PIB and OCP tackifiers. These products will likely capitalize on the unique polarity and solvating power of the latest base fluid technologies: bio-based/synthetic esters, polyalkyl glycol (PAG) fluids, and ionic liquids. This effort will rely heavily on lessons learned in established a strong portfolio of VI improvers and additive packages for alternative base fluids like vegetable oil and ester.
Functional Products Inc. has spent over 30 years developing a diverse portfolio of tackifiers and other lubricant additives. 1-330-963-3060 |
www.functionalproducts.com | Functional Products Inc., 8282 Bavaria Road, Macedonia OH, 44056
References:
1.
Rudnick, L. in Lubricant Additives: Chemistry and Applications, Second Edition 357–375 (CRC Press, 2009).
2.
Chao, K. K. K. & Williams, M. C. The Ductless Siphon: A Useful Test for Evaluating Dilute Polymer Solution Elongational Behavior. Consistency with Molecular Theory and Parameters. J. Rheol. (N. Y. N. Y). 27, (1983).
3.
Devore, D. A., Vargo, D. M., Serra, O. R. & Lipowski, B. M. Quantitative evaluation of tackiness in polymer-oil solutions using modified probe tack method. Functional Products Inc. (2013).
4.
Levin, V. J., Stepan, R. J. & Leonov, A. I. Evaluating Tackiness of Polymer Containing Lubricants by Open-Siphon Method: Experiments, Theory and Observations. (2007).
5.
Kunal, K. et al. Polyisobutylene: A most unusual polymer. J. Polym. Sci. Part B Polym. Phys. 46, 1390–1399 (2008).
6.
Rensselar, J. Van. Trends in Industrial Gear Oils. TLT 26–33
7.
Rizvi, S. Q. A. Lubricant Chemistry, Technology, Selection, and Design. ASTM Int. Conshohocken (2009).
8.
Odian, G. G. Principles of polymerization. (Wiley, 1981).
9.
Erik Willett, Daniel Vargo, D. D. Tackifiers for High Temperature Lubricants. Functional Products Inc. (2017).
10.
Levin, V. & Litt, F. Tackifiers for high temperature lubricants. Functional Products Inc. (2004).
11.
Fox, M. & Academy, R. Polymer Tribology. Lube-Tech 32–37 (2016).