ExxonMobil Chemical
Why sacrifice wear protection for energy efficiency?
By Michael P. Sheehan, Senior Staff Chemist, Marketing Technical Services, ExxonMobil Chemical Company | TLT CMF Plus November 2017
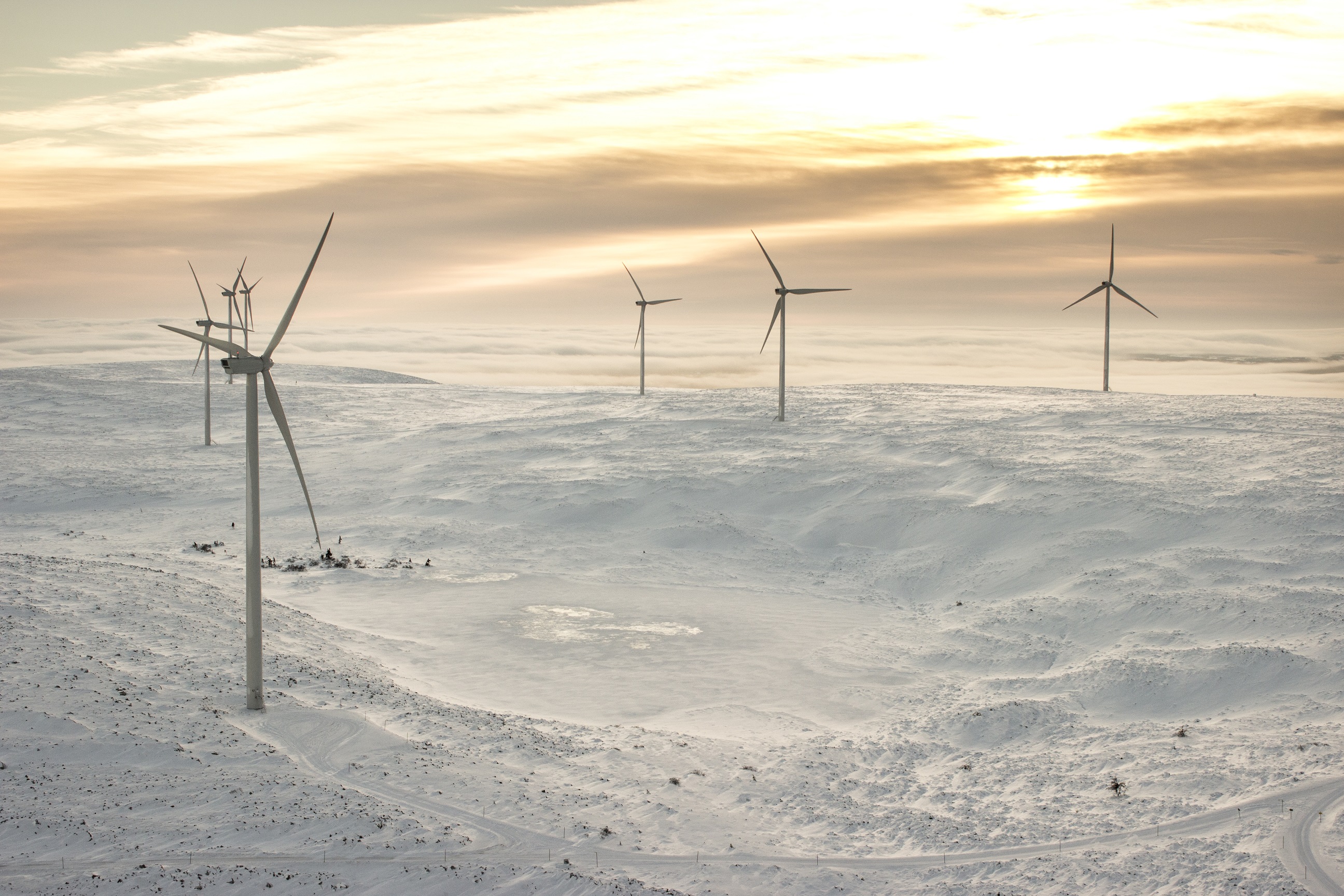
Today’s industrial sector accounts for nearly half of the world’s energy consumption. Improved energy efficiency in this sector obviously can have a major impact on the world’s energy use, which is predicted to grow as much as 25 percent by 2040.*
To help lower industrial energy consumption, lubricant formulators have increased their use of synthetic base stocks, which have been known to improve energy efficiency. But limited test data existed to measure this improvement.
That’s why ExxonMobil commissioned a series of tests at the Institute of Energy of the University of Porto (INEGI). Our goals:
•
Verify and quantify the energy efficiency gained by using synthetic base stocks.
•
Assess the concern of some equipment builders and owners that low-viscosity, synthetic-based lubricants may result in lower wear protection.
– Our SpectraSyn™ polyalphaolefin (cPAO) and SpectraSyn Elite™ metallocene polyalphaolefin (mPAO) synthetic base stocks have demonstrated excellent wear protection capabilities, but we wanted specific rig data.
•
Compare the performance of SpectraSyn Elite mPAO base stocks with conventional PAO, measuring energy efficiency and wear protection.
With this data, we could better guide formulators with solutions that help them innovate energy-efficient industrial lubricants for today’s changing marketplace.
mPAO makes a difference
Created using a proprietary metallocene catalyst process, SpectraSyn Elite mPAO offers much higher viscosity index (VI), better low-temperature fluidity, enhanced film thickness and much lower foaming than conventional high- viscosity cPAO.
The differences between mPAO and cPAO can be seen at the molecular level (
Figure 1). Metallocene PAO has a uniform, comb-like structure and lacks random short side chains, while conventional PAO has short and long side chains in a random orientation on either side of the main backbone. These differences help explain the enhanced performance properties of mPAO.
Through the INEGI test program, we wanted to answer a key question: Does the higher VI and enhanced film thickness properties in SpectraSyn Elite mPAO enable formulators to reduce lubricant viscosity to improve energy efficiency without impacting wear protection?
How did we prove it?
We compared formulations using mineral and synthetic base stocks (cPAO and mPAO) by measuring EHL film thickness, traction curves, energy efficiency and wear protection performance.
The rig test program evaluated roller thrust bearing and FZG gear tests. The program tests measured:
•
EHL film thickness at 40°C, 80°C and 120°C, calculating viscosity using ASTM D341
•
Traction coefficient at 80°C
•
Roller bearing temperature and friction torque at rotational speeds of 75.0, 150.0, 300.0, 600.0, 900.0 and 1,200.0
•
FZG power loss at 500 rpm, 1,000 rpm and 1,750 rpm
•
FZG gear set wear (mass loss, mg)
Mineral vs. cPAO synthetic
The first set of tests compared an ISO VG 460 mineral oil formulation with an ISO VG 320 (58.90 percent cPAO) conventional synthetic PAO reference oil formulation. The synthetic oil demonstrated equivalent film thickness at higher temperatures (80 and 120°C) typical of industrial equipment in operation (
Figure 2), along with lower traction properties, which can enable energy efficiency.
In the roller bearing test, the synthetic showed 14 percent less power loss and operated at a 21 percent lower temperature. In the FZG test, the synthetic demonstrated lower power consumption while maintaining equivalent wear protection.
Overall, the synthetic formulation provided the same level of wear protection as the mineral-based lubricant, even as it delivered substantial energy savings through reduced power consumption.
cPAO vs. 7 percent mPAO
The second set of tests compared the ISO VG 320 reference oil with a similar formulation that substituted 7 percent of the high viscosity cPAO with SpectraSyn Elite™ 300 mPAO.
The oil formulated with mPAO demonstrated enhanced film thickness at 80 and 120°C and equivalent traction properties. The oils were roughly the same in terms of power consumption and wear protection.
The differences were much clearer in the roller thrust bearing test (
Figure 3). Without sacrificing wear protection, the oil with mPAO reduced power loss by 11 percent, proving energy efficiency, and lowered operating temperature by 10 percent.
cPAO vs. mPAO formulations
The final study compared the ISO VG 320 reference oil with two lower viscosity oils that included roughly 50 percent mPAO — an ISO VG 270 (53.40 percent mPAO) and an ISO VG 220 (49.34 percent mPAO).
The mPAO oils demonstrated lower traction properties, which translate to greater energy efficiency. Despite their lower viscosity, these oils maintained roughly equivalent film thickness with the reference oil at 80°C and 120°C (
Figure 4).
In the roller thrust bearing test, the ISO VG 220 operated at a 9 percent lower temperature, while all three demonstrated the same level of power loss, as they did in the FZG test. They also showed no significant difference in wear protection.
Breaking barriers
We now have more specific data to measure how SpectraSyn Elite™ mPAO base stocks can offer enhanced film thickness and energy efficiency while also maintaining wear protection. Lubricants formulated with mPAO base stocks also can operate at lower temperatures, delaying oxidation degradation to help oil stay in grade longer.
The tests confirm:
SpectraSyn Elite mPAO base stocks give formulators the flexibility to create innovative lubricants that meet the changing demands of their customers.
*Source for energy statistics: ExxonMobil’s Outlook for Energy.
© 2017 ExxonMobil. All trademarks used herein are trademarks or registered trademarks of Exxon Mobil Corporation or one of its subsidiaries.
Source of test results/product information: ExxonMobil data