Selecting lubricating greases: What you should know
Dr. Nancy McGuire, Contributing Editor | TLT Webinars October 2017
To get optimal performance and long operating life, pay close attention to specifications and monitor your operations closely.
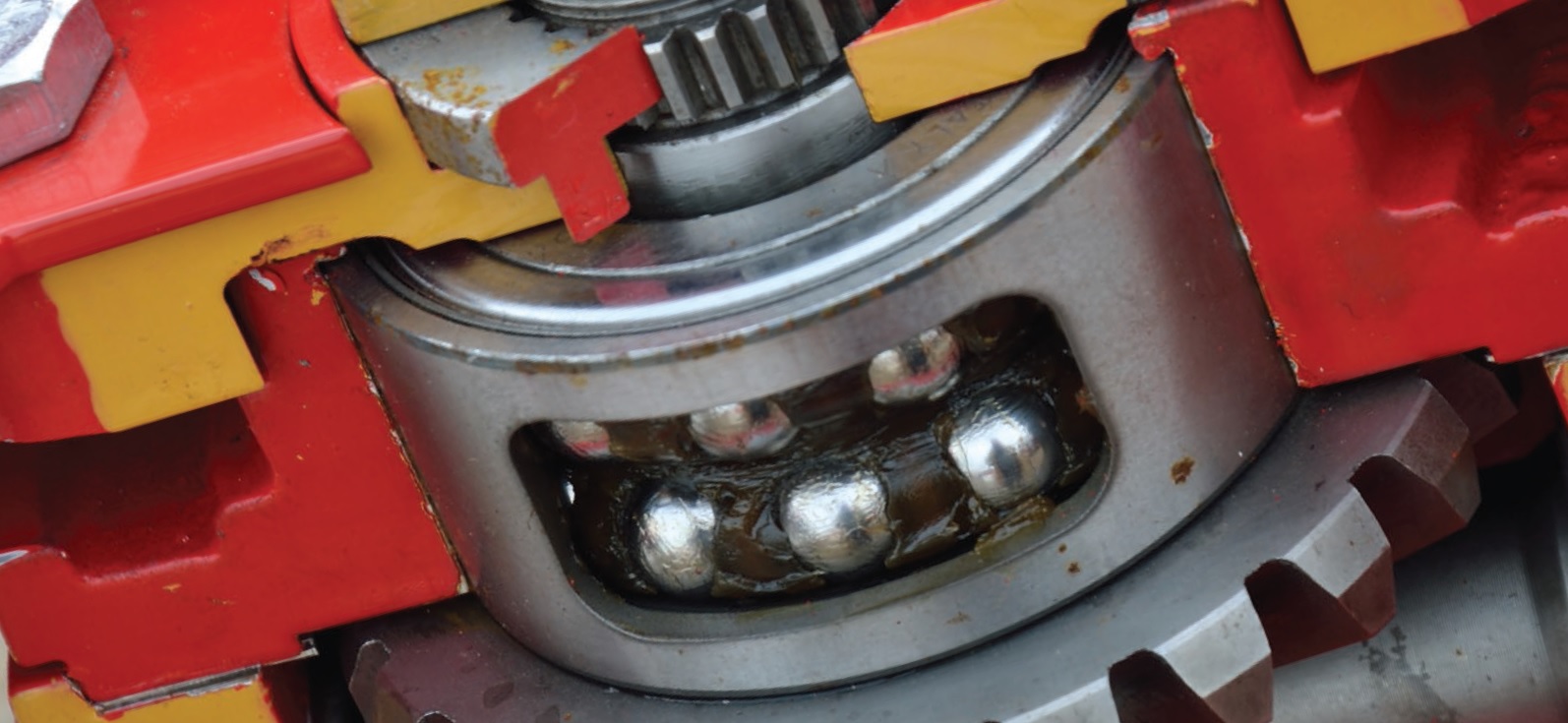
© Can Stock Photo / Pauws99
KEY CONCEPTS
•
Grease formulation is a complex process that takes into account the multiple interactions among base oils, thickeners and additives.
•
Solid lubricants physically or chemically adhere to metal surfaces, forming a protective film in the absence of a hydrodynamic lubricant layer.
•
Selecting a replacement grease can be a simple matter of matching specifications, but other factors include color, smell and feel or tack.
MEET THE PRESENTER
This article is based on a Webinar originally presented by STLE Education on Nov. 3, 2016. Selecting Lubricating Greases is available at
www.stle.org: $39 to STLE members, $59 for all others.
Dr. Anoop Kumar is the director for R&D and business development at Royal Mfg Co LP, a company that makes high-performance oils and greases. He has a doctorate in chemistry from the Indian Institute of Technology and more than 25 years of experience in lubricating greases and industrial oils. Dr. Kumar is the inventor of titanium complex grease. He has published more than 80 technical papers and holds more than 20 worldwide joint patents on lubricating greases. Dr. Kumar serves as treasurer and executive committee member of NLGI and will serve as a TLT technical editor in 2018. In 2013 he received the Chevron Lubricant Award and in 2010 he received the Long Service Award from NLGI India. He is a three-time recipient of the PPC Gonsalves Award and has twice received the ISFL Best Paper Award. In 1992 he received the Khosla Research Award. You can reach Kumar at
anoopk@royalmfg.com.
Dr. Anoop Kumar
PEOPLE HAVE BEEN USING LUBRICANTS since ancient times, possibly since the invention of the wheel, to reduce friction and wear between two mating surfaces. A wagon dating back to 1450 BC recovered from the tomb of the Egyptian pharaoh Tutankhamun was found to have lubricant material (probably made from fat and lime) in its wheel hubs (
1).
Lubricants of various sorts have been used continuously since then, but tribology was not defined as a science until British scientist H. Peter Jost published a groundbreaking report in 1966 that quantified the potential economic benefits of systematic efforts to reduce friction and wear. He coined the term
tribology to mean the study of friction, wear and lubrication. Jost estimated that friction was responsible for energy losses—including heat production and greater fuel costs—costing some £2 billion (£20 billion in today’s currency) within the UK alone. He also estimated that proper tribological practices and maintenance procedures could save some 25% of this cost (
2).
OIL OR GREASE?
Lubricants can be divided into oils (liquid) and greases (semi-solid). Although greases represent only about 2% by weight of this category (2.48 billion pounds per year worldwide), they provide lubrication in high-pressure, high-load situations where oils are not effective (
3). Worldwide, the demand for lubricating greases has risen from 1.64 billion pounds in 2002 to 2.48 billion pounds in 2015. Much of this rise in demand comes from rapidly developing countries like China, whose grease demand rose from 199 million pounds in 2002 to 884 million pounds in 2015. More mature markets like North America have remained fairly steady in total demand (484 million pounds in 2002 versus 481 million pounds in 2015), but these markets are showing a stronger trend toward high-performance greases than the rest of the world (
4, 5).
Greases are commonly used for bearings, gears, bushings, chain drives and wire ropes (
see Figure 1). Between 80%-90% of roller bearings are lubricated with greases because grease provides better sealing and load-carrying properties, and it shows a higher resistance to dirt, dust and temperature extremes than oil lubricants can provide. The tradeoff comes in grease’s poorer cooling properties (in part because the grease remains in place rather than circulating through the system) and in its viscous resistance (the drag that a grease layer exerts on moving parts).
Figure 1. Grease on bearings and a gear. (Figure courtesy of Royal Mfg Co LP.)
The dm⋅N factor (sometimes called the DmN factor) is a useful metric for choosing a bearing lubricant that will perform well under a given set of conditions. This factor is obtained by multiplying the bearing speed in rpms by the average of the outer diameter and bore diameter of the bearing in millimeters.
For a given lubricant viscosity (measured at 40 C, 104 F), a value of dm⋅N exceeding the corresponding critical viscosity rating indicates that oil, rather than grease, should be used as the lubricant (although some specialty greases can be used for dm⋅N factors as high as 1 million). Table 1 shows some typical limiting values of dm⋅N, above which oil is the preferred lubricant. Typical limiting values of dm⋅N for various types of bearings are shown in Table 2 (
6).
Table 1. (Courtesy of Royal Mfg Co LP.)
Table 2. (Courtesy of Royal Mfg Co LP.)
WHAT IS A LUBRICATING GREASE?
Lubricating greases consist of at least 80% base oils, some 10%-15% thickener, with the remainder being additives. However, making a grease is not simply a matter of mixing a set of ingredients together. Grease formulation is a complex process that takes into account the multiple interactions among base oils, thickeners, extreme pressure (EP) additives, anti-wear additives, solid lubricants, antioxidants, tackifiers and friction modifiers. The properties of the final product depend not only on the formulation but also the manufacturing process (including homogenization procedures) and the conditions under which the grease is stored.
Thickeners provide a fibrous matrix that contains the base oil. Under pressure, some of this oil is released into the space between the mating surfaces of the machine parts where it provides lubrication. When the pressure is released, the oil is drawn back into the thickener matrix. At a molecular level, the thickener is attracted to the polar component of the base oil (generally the oxygen atoms in a triglyceride or other oxygenated oil molecule). These attractions take the form of hydrogen bonding, capillary action and van der Waals forces, and they entrap about 75% of oil within the thickener. About a third of the oil in this 75% can be extracted from the thickener matrix by gravity alone. The remaining 20%-25% of the oil is bound within the thickener matrix by mechanical entrapment and can only be extracted using solvents or extreme conditions (
see Figure 2).
Figure 2. Grease matrix micrograph. (Figure courtesy of Royal Mfg Co LP.)
Most thickeners are soap based (i.e., they are metal salts or metal complexes with organic fat [glyceride] compounds). Worldwide, about 55% of thickeners are simple lithium soaps, and about 19% are lithium complex soaps. For North America, these figures are 26% and 39%, respectively, and for China they are 63% and 17%, respectively (
5). Other grease thickeners include simple soaps based on calcium, sodium or aluminum; complex soaps based on calcium, aluminum, barium or various sulfonates; and non-soap thickeners based on polyurea compounds and clays. Overall there is a trend toward more high-performing grease thickeners, including complexes and non-soap thickeners.
In recent years, concerns about the long-term availability of lithium, the most commonly used grease thickener, has driven a search for alternatives. The lithium battery industry increasingly competes for the world’s supply of lithium, and this has already manifested itself in price increases across the board (see Table 3).
Table 3. (Courtesy of Royal Mfg Co LP.)
The choice of a thickener has a strong influence on the overall properties of grease. Sulfonates, polyureas and clays are good for high-temperature applications. Aluminum and sulfonate greases are especially water resistant. Barium greases and sulfonates operate well under extreme pressure. Greases thickened with aluminum complexes, clays or soaps made with lithium or calcium are easier to pump than calcium sulfonate or polyurea greases, and they flow more easily through the lines and nozzles of a grease dispenser. They also have better slumpability properties (i.e., they are more easily drawn out of a drum and into a pump). Aluminum complex greases are especially sprayable.
Base oils can be mineral oils (Group I or II paraffins or naphthenic oils), synthetic oils (polyalphaolefins, esters, polyalkaline glycols, silicones and others) or bio-based oils (soybean, rapeseed/canola, castor oil and others). Most greases (some 90%) use mineral oils as the base oil, 6% use synthetic base oils, 3% use semi-synthetics (mixtures of mineral and synthetic oils) and less than 1% use biobased base oils.
The choice of a base oil influences a grease’s viscosity and lubricating properties, its susceptibility to oxidation and thermal degradation, its performance at high and low temperatures and how well it flows at low temperatures. In addition, vegetable oils and synthetic esters are biodegradable, which is desirable after the grease has been disposed of but not during operations. Synthetic oils have excellent flow properties at low temperatures.
Additives provide any number of additional properties, depending on the desired performance characteristics. Various additives help a grease perform better under extreme pressures, protect parts from wear, guard against oxidation of the grease, guard against rust and corrosion in the parts it protects and modify friction characteristics. Solid lubricants can be used under extreme conditions. Even though less than 10% of grease consists of additives, they represent a significant part of a formulation’s cost.
WHAT DO SOLID LUBRICANTS DO?
Under hydrodynamic conditions, the moving parts are fully separated by a liquid lubricating oil film, which minimizes friction between those parts. However, under boundary/elastohydrodynamic lubrication conditions typical of heavy loads and high pressures (for example, in mining or off-highway applications), asperities on the mating surfaces will break through an oil lubricant film and come into direct contact. These asperities can cold weld together under pressure—causing pitting and wear—and creating sites where corrosion can occur. In these situations, solid or semi-solid (grease) lubricants with antiwear additives are required.
Solid lubricants physically or chemically adhere to metal surfaces, forming a protective film in the absence of a hydrodynamic lubricant layer. This protective film reduces friction and prevents welding. Solid lubricants can be layered materials like graphite or molybdenum disulfide (MoS
2). Each layer of these crystalline materials is one atom thick with layers stacked like a deck of playing cards. Individual layers slide past each other easily, providing a lubricant action, but the layers resist compression when force is applied perpendicular to the layers.
HIGH-PERFORMANCE REQUIREMENTS
General-purpose greases, including lithium 12 based (containing Li-12-hydroxystearate, a common grease thickener), calcium based and sodium based, are suitable for application temperatures below 250 F (121 C) and parts under mild loads. The presence and effectiveness of EP additives are rated using standard tests, which produce ratings like a Timken OK load or weld load. General-purpose greases generally have a 40-45-pound Timken rating and about a 250-kilogram weld load.
A high-performance grease may be required when operating conditions include very high or very low temperatures, heavy loads or shock loading, very high or very low motor speeds or environments in which the grease is exposed to water, dust or dirt. High-performance greases include lithium or aluminum complexes, calcium sulfonates, polyureas and clay-based greases.
High-performance greases can operate at temperatures as low as -54 F (-48 C) or as high as 450 F (232 C), and they contain EP additives that stand up under heavy loads or shock loading. These greases exhibit less than 5% washout and less than 30% spray off when exposed to water. They continue to provide lubrication at speeds exceeding 1,400 rpm.
SELECTING A GREASE
Users can follow one or more approaches to selecting the best grease for a particular operation. Often, OEMs will provide specifications. Industry organizations like the National Lubricating Grease Institute (NLGI) also provide guidance. For example, the NLGI certifies automotive chassis greases (LA and LB) and wheel bearing greases (GA, GB and GC), with a GC-LB designation representing the highest performance classification.
If a grease currently in use is working well, selecting a replacement grease can be a simple matter of matching specifications. New products can be evaluated and analyzed for suitability before putting them to use in the field, or new greases can be used in field trials and tested in actual applications.
Other factors influencing grease selection include color (greases come in a wide range of colors, some of them very bright), smell and feel or tack. In a survey of customer complaints in 2015, only 14% dealt with failure in actual test properties. Of the total number of complaints, 42% were in connection with grease color, 20% dealt with consistency, 16% with tack or texture and 8% with smell (
7).
Of course, a grease with the right color and smell is of very little help if it doesn’t also hold up well in its intended application. Thus, selecting a lubricating grease will depend on the size of a bearing or gear, the operating temperature range, motor speeds, maximum loads (steady or shock), the amount of water or moisture ingress expected and the amount of dust and dirt in the environment. Merely selecting a grease with the maximum rating in each category can be cost prohibitive and may not give you your desired results; it’s better to aim for the optimum set of properties.
Grease suppliers provide technical data sheets (TDS) to help in matching a grease formulation with specific parts and operating conditions (
see Table 4 for an example). Ratings include mechanical and shear stability: the resistance of the grease to dripping out from between the mating surfaces. Water resistance is given as ratings for water washout, water spray off and mechanical roll stability. Weld load and Timken OK load ratings indicate EP additive presence and effectiveness. Drop point and high-temperature life indicate a grease’s performance at high temperatures. Low-temperature characteristics include low-temperature torque (LTT), pumpability, shear rate and flow (measured using a Lincoln ventmeter) and U.S. Steel mobility test ratings. Tables 5-7 illustrate the wide variety of grease properties and how they relate to various applications.
Table 4. (Courtesy of Royal Mfg Co LP.)
Table 5. (Courtesy of Royal Mfg Co LP.)
Table 6. (Courtesy of Royal Mfg Co LP.)
Table 7. (Courtesy of Royal Mfg Co LP.)
DIFFERENT INDUSTRIES, DIFFERENT GREASES
Various industries show preferences for different types of greases. For example, the mining and construction industries used calcium and calcium complex greases in the past, but they are now moving toward calcium sulfonate complex greases. Lithium and lithium complex multipurpose (MP) greases and aluminum complex greases also are commonly used. Because much of the work in these applications occurs outdoors, these industries are showing greater interest in biodegradable and environmentally friendly products.
Marine applications use a variety of calcium or lithium MP greases. Calcium sulfonate greases also are used because they hold up better under salt spray. Marine industries also are moving toward greases that are biodegradable and that comply with Vessel General Permit regulations. The agriculture and forestry industries use lithium MP greases, and they are moving toward vegetable-sourced (ester) base oils for their biodegradability properties. Food industry applications must comply with their own set of strict regulations, and they tend toward calcium, clay and silica greases. They also may use aluminum complex and calcium sulfonate greases.
Open-gear applications relied on asphaltic-based products in the past. Now aluminum complex-based greases are preferred over other types. Constant-velocity joints may use lithium and lithium complex greases with molybdenum sulfide or graphite EP additives, or, preferably, they may use polyurea greases.
USEFUL TIPS
Getting the best performance and longest operating life out of a grease requires careful attention to the specifications and monitoring your operations to make sure you stay within those specifications. For instance, the life of your grease decreases by half for every 10 degrees that you exceed the recommended operating temperature. For general-purpose greases, the application temperature should be kept below 250 F (121 C). For high-performance greases, mineral-type base oils can go up to about 350 F (177 C), and synthetic base oils can go as high as 450 F (232 C).
Oil bleed (the amount of oil that comes out of a grease during storage) should not exceed 5%, and keeping this to about 1%-2% is preferable for good lubrication. You don’t have to fill the whole housing to get good lubrication: for medium to high speeds, about 50% is optimum, with more than 50% required for higher speeds.
If the grease will be in contact with other types of lubricants, check for compatibility issues. This is especially important for synthetics.
ACKNOWLEDGMENTS
Dr. Kumar thanks Todd Corner, Debbie Rowland, Ryan Fields and Aaron Hlusko for help in preparing this presentation.
REFERENCES
1.
Lorenzi, R. (Aug. 3, 2010), “King Tut’s chariots were like Formula One cars,”
Discovery News. Available
here.
2.
Wood, R. J.K and Harrison, K. (June 9, 2016), “Dr. Peter Jost CBE 1921-2016,
UK Tribology Network. Available
here.
3.
Lubes’N’Greases 2015 Lube Report. Available
here, subscription required.
4.
NLGI 2002 Grease Production Survey Report.
5.
NLGI 2015 Grease Production Survey Report. Available at
www.nlgi.org, subscription required.
6.
Prasar, R.K. (2004), “Lubrication Simplified,” p. 108. ASIN: B00LTU109K.
7.
Kumar, A., Bhatnagar, N. and Mallory, B. (May/June 2017),
NLGI Spokesman,
81 (2), pp. 12-17. Available
here.
Nancy McGuire is a free-lance writer based in Silver Spring, Md. You can contact her at nmcguire@wordchemist.com.