Words mean things
Dr. Robert M. Gresham, Contributing Editor | TLT Lubrication Fundamentals August 2017
Especially when it comes to 3D printing, which could be on the verge of ushering in a third Industrial Revolution.
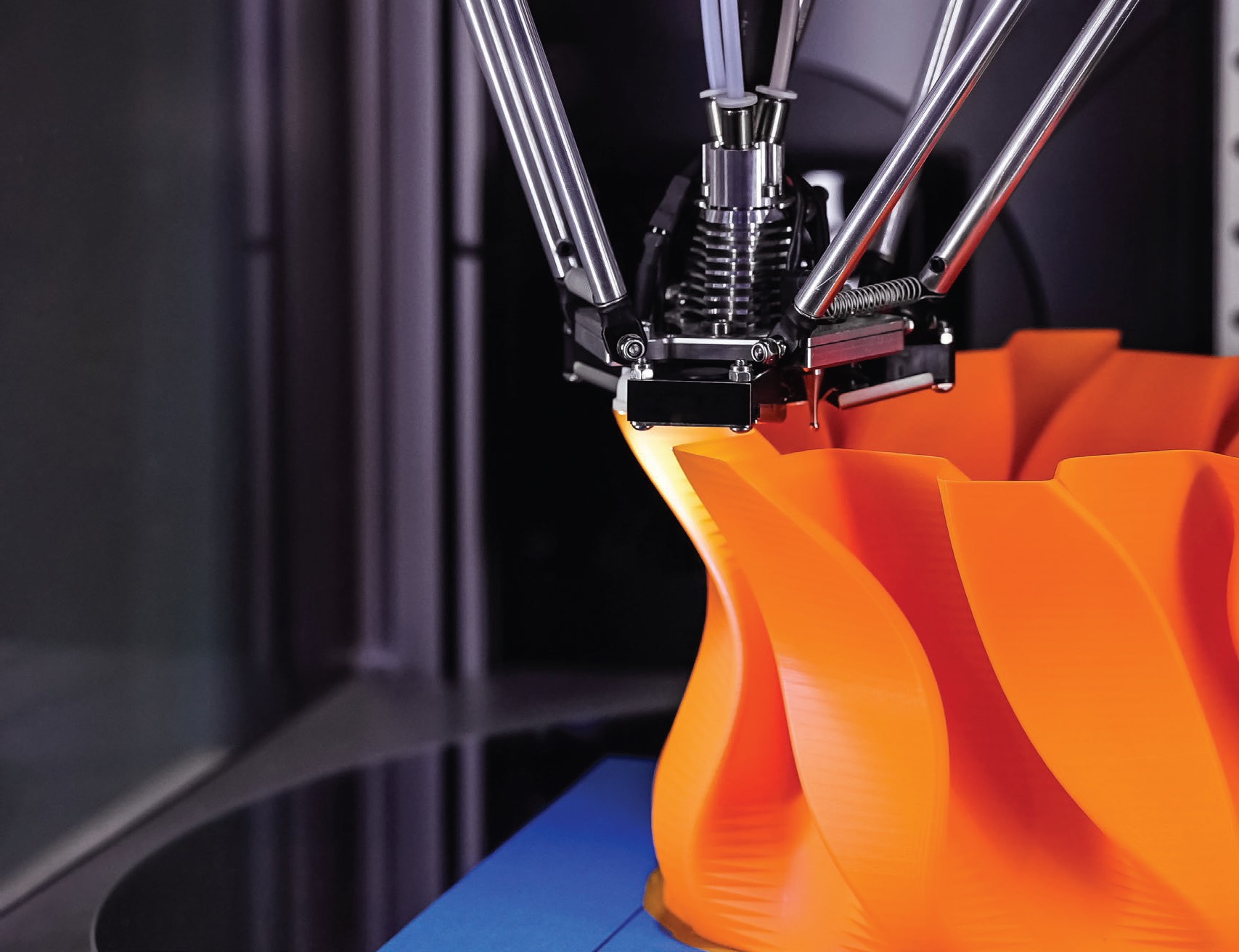
© Can Stock Photo / prescott09
KEY CONCEPTS
•
Additive manufacturing is a process that builds 3D objects by adding layer upon layer of material.
•
The applications for additive manufacturing are virtually limitless.
•
GE Aircraft Engine Group is now printing blades for the low-pressure turbine of the GE9X jet engine, the largest jet engine ever built.
WE HAVE ALL ENDURED SITUATIONS where we thought we had said things quite clearly and later found that we were completely misunderstood. This can be quite unsettling, especially if the audience for what we said was quite large. This happened to us in working on the second iteration of the STLE Emerging Trends Report survey. With careful re-analysis of the results, we should be able to correct the error, so not to worry. However, this is an example of “words mean things,” but not necessarily the same thing to different people.
In our survey, we asked about the importance of additive manufacturing. As you might guess, most folks thought it was pretty important. One group thought it would be more and more important to manufacture both old and newly developed additives for lubricants with better quality and lower cost. Yet another group thought that additive manufacturing, based on 3D printing, would be the wave of the future.
Yup, words mean things!
Let’s take a closer look. Additive manufacture (AM) in this second context is to differentiate between additive and subtractive manufacturing. In subtractive manufacturing material is removed or subtracted from the work piece. Examples are most machining operations: sawing, milling, drilling, grinding, etc. This, of course, results in a lot of wasted material, which may or may not be recyclable.
AM is an appropriate name to describe the technologies that build 3D objects by adding layer upon layer of material, whether the material is plastic, metal, concrete or, one day, perhaps even human tissue. Futurologist Jeremy Rifkin has claimed that 3D printing signals the beginning of a third industrial revolution succeeding the assembly production line that dominated manufacturing starting in the late 19th Century and was popularized by Henry Ford for building cars.
Common to AM technologies is the use of a computer 3D modeling software (computer-aided design or CAD), 3D machine equipment and layering material. Once a CAD sketch is produced, the AM equipment reads in data from the CAD file and lays downs or adds successive layers of liquid, powder, sheet material or other materials, in a layer-upon-layer fashion to fabricate a 3D object. The term AM encompasses many technologies including subsets like 3D printing, rapid prototyping (RP), direct digital manufacturing (DDM), layered manufacturing and additive fabrication.
AM application is limitless. Early use of AM in the form of rapid prototyping focused on preproduction visualization models. More recently, AM is being used to fabricate end-use products in aircraft, dental restorations, medical implants, automobiles and even fashion products. It also is a visualization tool in the design process. Thus, it is a means to create highly customized products for consumers and professionals alike. It can be used for industrial tooling, producing small lots of production parts and, more and more, large lots of production parts.
One most notable example is the use of AM by the General Electric (GE) Aircraft Engine Group. GE’s centerpiece plant is located on the flat and fertile plains that stretch seemingly forever between Italy’s industrial dynamos of Milan and Turin, in tiny Cameri, Italy. In 2013 GE Aviation acquired Avio Aero, one of the most advanced European additive manufacturing companies. They also have bought operations in Sweden, Germany and now several locations in the U.S.
The typical palette of materials used for 3D printing can range in complexity from simple plastics to advanced superalloys. For example, the GE Auburn, Ala., factory’s direct metal laser melting (DMLM) machines create jet engine fuel nozzles by fusing layers of fine metal powder with a powerful laser. Each layer is between 20 and 80 microns thick, thinner than a human hair, and an inch of printed material can contain up to 1,250 layers. Planes powered by jet engines that use these fuel nozzles already are ferrying passengers across Europe and Asia.
The Cameri plant uses 3D printing machines that use an electron beam to fuse together layers of a wonder material called titanium aluminide (TiAl), which is 50% lighter than the previously used nickel-based alloys (
see Figure 1). The electron gun accelerates the beam until it’s several times more powerful than lasers currently used for printing metal parts. GE can build blades from layers that are more than four times thicker than those used by laser-powered 3D printers. They say the method is so fast that it’s competitive with casting, the standard way to make parts from TiAl. There is still final surface finishing, but the material lost is negligible versus standard subtractive manufacture for the whole part.
Figure 1. TiAl powder and finished components inside an Arcam 3D printer in Cameri, Italy. (Figure courtesy of Avio Aero.)
GE is now printing blades for the low-pressure turbine of the GE9X jet engine, the largest jet engine ever built (
see Figure 2). This engine is a mix of both evolutionary and revolutionary technologies. The GE9X is the most fuel-efficient, on a per-pounds-of-thrust basis, that GE has ever built. It delivers 10% improved fuel burn versus the current GE90-115B powered Boeing 777-300R and a 5% improved specific fuel consumption versus any twin-aisle engine available plus achieve an approximate 10:1 bypass ratio, a 60:1 pressure ration and margin to Stage 5 noise limits.
Figure 2. Blades are being printed by GE for the low-pressure turbine of the GE9X jet engine.
This is merely one example of what can be done with this exciting new technology that clearly will be an emerging trend in many, many industries for years to come. There will still be tribology issues with the mechanics of the 3D printer and associated equipment but of a different nature than encountered in subtractive manufacture. It also is an example that “words mean things,” but not necessarily the same thing to different people, especially those who manufacture additives for lubricants.
Bob Gresham is STLE’s director of professional development. You can reach him at rgresham@stle.org.