The future of flying is near
Dr. Edward P. Becker | TLT Automotive Tribology August 2017
Materials engineering and tribology are two big factors when considering flying cars.
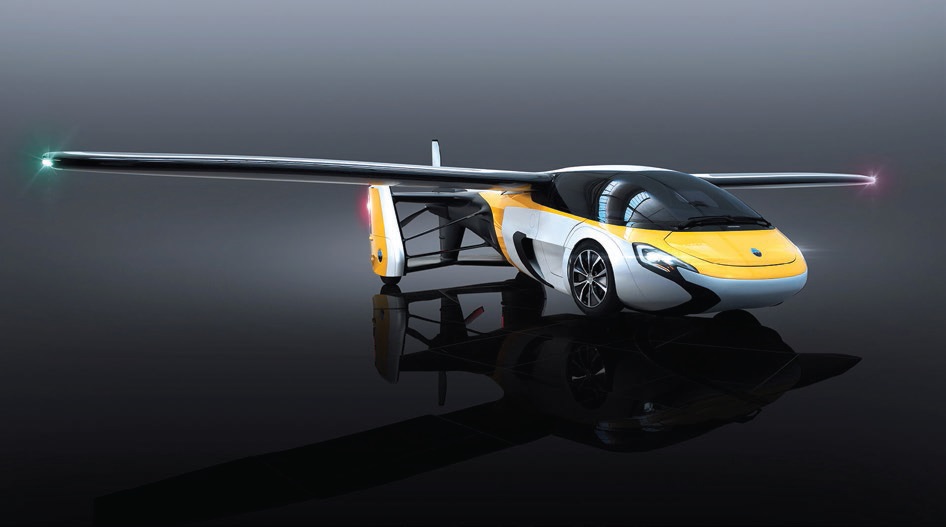
Materials and tribology are among the biggest challenges in achieving an acceptable power-to-weight ratio in a flying car.
FLYING CARS ARE BACK IN THE NEWS. AeroMobil (
1) is exhibiting a production model and claims it will soon begin taking pre-orders for the vehicle. Before you place a deposit, though, consider a couple of other recent statements from AeroMobil:
“The vehicle is expected to go into full production in the upcoming years with the first deliveries being made to customers by 2020” and “The production of AeroMobil’s first vehicle will be limited to a maximum of 500 units and is priced between 1.2 million—1.5 million Euro depending on final customer specifications.”
Now consider some performance specifications for the AeroMobil: top ground speed of 99.4 mph (160 kph), cruising air speed of 161 mph (259 kph), maximum aero range of 466 miles (750 km), carrying capacity of two passengers and maximum useable load of 529 pounds (240 kg). While those numbers might be acceptable to most customers for a small car or a small propeller-driven aircraft, some would note that one can purchase both a higher-performance car and aircraft for less money.
To be fair, a practical flying car is quite an engineering feat. Two major players in achieving an acceptable power-to-weight ratio are materials engineering and tribology. Lightweight, high-strength materials for vehicle structures are necessary to maximize payload. Carbon fiber composites are used extensively for body and interior assemblies. High strength-to-weight ratio metal alloys (aluminum, magnesium and titanium) are used for critically stressed components in the suspension and powertrain where possible.
The power plant for the AeroMobil is a conventional two liter, turbocharged four-cylinder, horizontally opposed, internal combustion engine paired with twin electric front-wheel motors. This hybrid configuration is increasingly popular in automotive applications. However, the AeroMobil does not appear to incorporate a large battery pack, probably because of weight restrictions. The engine directly powers a generator that provides electricity to the wheel motors.
One measure of specific output of an internal combustion engine is the power-to-displacement ratio. In 2015 the average automobile engine in the U.S. produced 64.1 kW/l (
2). The AeroMobil engine produces 112 kW/l, nearly twice the specific output of the typical automobile.
Turbocharging provides the additional oxygen to the cylinders to burn sufficient gasoline to generate such high power, but also important are the use of wear-resistant, low-friction materials in the engine components and the use of advanced, low-friction lubricants in the engine and transmission. Even today, as much as 13% of fuel burned goes to overcome mechanical friction in the engine, with the piston and piston rings to the cylinder bore interface contributing over 50% of that amount (
3). There is still plenty of opportunity for the engine tribologist!
REFERENCES
1.
From
www.aeromobil.com.
2.
U.S. Environmental Protection Agency Report EPA-420-R-16-010,
Light Duty Automotive Technology, Carbon Dioxide Emissions, and Fuel Economy Trends: 1975-2016, November, 2016.
3.
Kenneth Holmberg, K., Andersson, P. and Erdemir, A. (2012), “Global energy consumption due to friction in passenger cars,”
Tribology International,
47, pp. 221-234. DOI: 10.1016/j.triboint.2011.11.022.
Ed Becker is an STLE Fellow and past president. He is president of Friction & Wear Solutions, LLC, in Brighton, Mich., and can be reached through his website at www.frictionandwearsolutions.com.