Spectrometric disconnect
Evan Zabawski | TLT From the Editor June 2017
Misunderstanding abounds with a popular and prominent fluid analysis test.
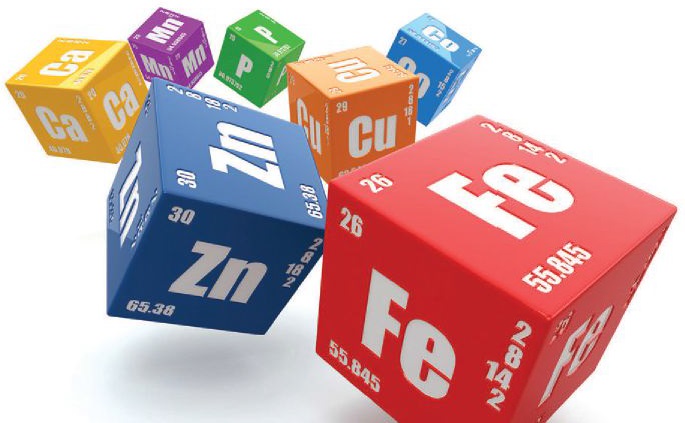
The results are an elemental concentration, not a quantity of a compound, alloy or chemical.
© Can Stock Photo / maxxyustas
THE LARGEST SINGLE SECTION OF A FLUID ANALYSIS REPORT is typically taken up by the elemental spectroscopy, which quantifies 20-25 metallic elements. End-users focus on these results when seeking information about machine wear. However, the results are not as easily interpreted as one supposes.
Two fundamental principles of the test method that must be understood deal with the reported parameters and the ability of the instrument. The test is called elemental spectroscopy because it reports a concentration of an element, not of a compound, alloy or chemical.
As an example, babbit bearing wear appears as lead and tin, but so would leaching of solder. If copper also was present then solder would likely be eliminated as a possibility, but now brass and bronze alloys become suspects. Knowledge of the lubricated components within the machine becomes paramount to proper interpretation. However, the ability of the instrument adds a layer of complexity.
The most popular instrument for performing elemental spectroscopy is the inductively coupled plasma (ICP), which performs atomic emission spectroscopy (AES). Technically, ICP-AES atomizes a small sample diluted with solvent into the plasma and then uses optical detection to measure the intensity of the various elements’ spectra within a narrow portion of the plasma. In layman’s terms, it means a very small sample is essentially burned with a portion of the flame analyzed for brightness of certain colors.
The fundamental aspect of this principle is that only the smallest wear metal and contaminant particles will be quantified accurately, as the particles must ionize completely within the narrow range being measured. This range is generally accepted as 0-5 microns, with the accuracy declining sharply for particles larger than five microns, up to 8-12 microns (sources vary in agreement) where the measurement becomes inaccurate. Regardless of a person’s visual acuity, which declines with age, ICP-AES only measures particles smaller than those visible to the naked eye; this explains why visible debris in the sample does not always produce an alarmed report.
While this may appear to be a significant limitation to the test, it should be understood that particles from normal modes of wear and most airborne particulate falls within this range. Impending failures are still detected, as most machines will see an increase in normal wear while progressing toward severe wear; but rapid failures, such as breakage, could go undetected even without the particle size limit.
The most difficult part of intuiting the results is understanding that they are a concentration, not a quantity, which is highly dependent on the volume of lubricant within the machine. Whether a five-gallon system contains about two fingernail clipping’s worth of material, or a 50-gallon system contains almost here-quarters of an ounce of material, or a 500-gallon system contains nearly a half a pound of material, samples from all three would report the same concentration of 100 ppm of material suspended in the lubricant.
Therein lies the principle difficulty in trying to establish a static alarm limit to universally apply to a machine type. Without a consistent lubricant volume, a limit is practically meaningless. Even so, there is a direct relationship between time and the quantity of wear and contaminant particles, so any limit should progress with time, otherwise any limit would eventually be exceeded given enough time (service). Conversely, low service life samples would only exceed alarm values in the most extreme cases, which would likely come too late to be useful.
The best way to interpret elemental spectroscopy is to trend the data from samples taken at consistent intervals, noting deviations within the individual machine. With true predictive maintenance, it is not really a question of how much is in the sample, nor in the system, but how much the values are increasing.
Evan Zabawski, CLS, is the senior technical advisor for TestOil in Calgary, Alberta, Canada. You can reach him at ezabawski@testoil.com.