VGP 2013: Propelling marine lubricants
Debbie Sniderman, Contributing Editor | TLT Feature Article May 2017
Creating safe, environmentally friendly and high-performing lubes required cooperation between lube manufacturers, OEMs and the U.S. government.
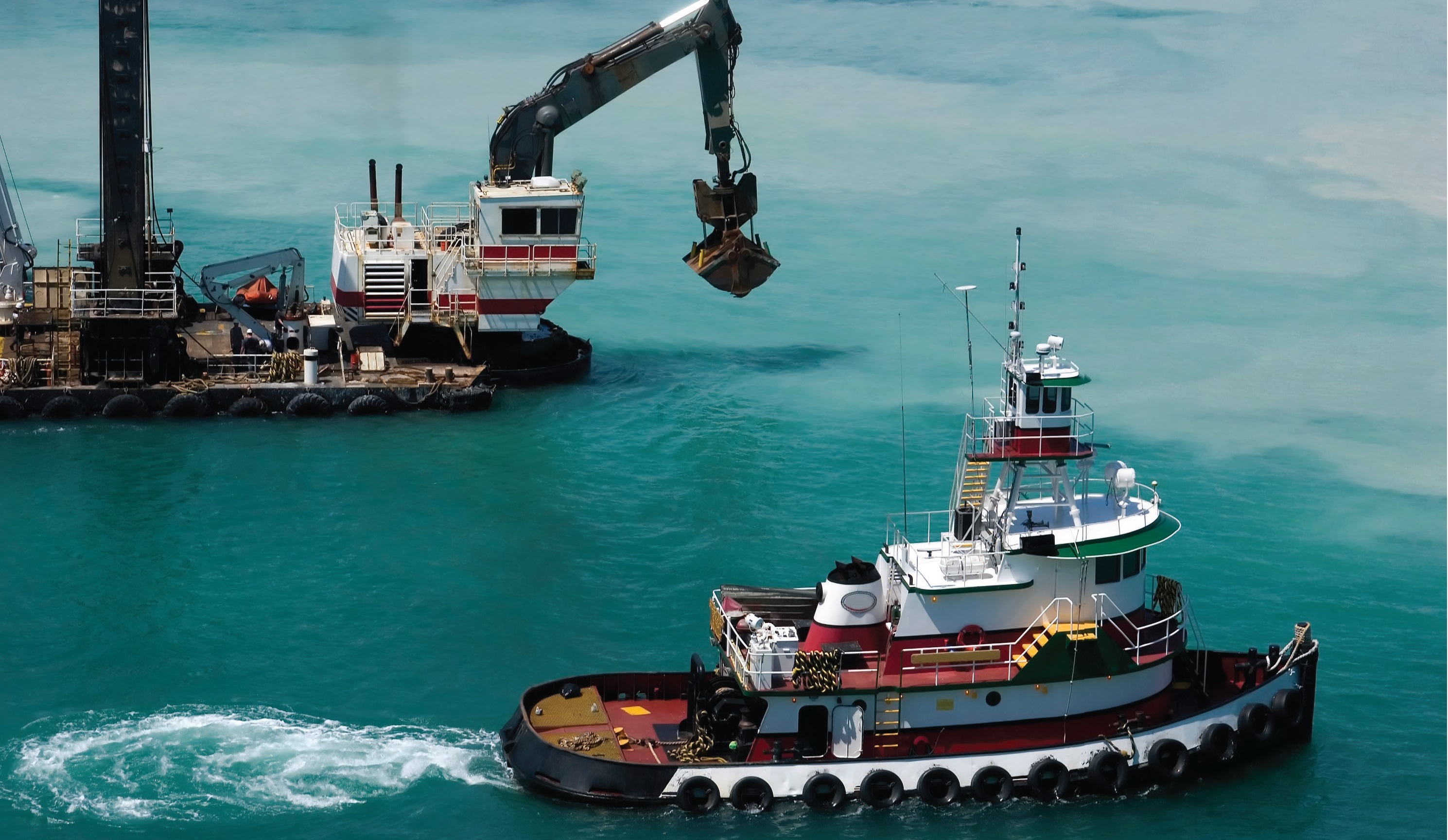
Image courtesy of RSC Bio Solutions.
KEY CONCEPTS
•
VGP 2013 is the world’s first government regulation requiring environmentally friendly acceptable lubricants (EALs) for marine use.
•
New lubricant formulations that meet technical and environmental requirements are still heavily reliant on OEM approval.
•
With ships docking infrequently, the widely accepted VGP 2013 is slowly but strongly impacting the marine industry, cleaning our waters and growing the EAL market.
ON DEC. 19, 2013, the U.S. Environmental Protection Agency’s (EPA) Vessel General Permit (VGP) became effective stipulating that commercial vessels greater than 79 feet must use environmentally acceptable lubricants (EALs) in all systems that interface with the sea. VGP 2013, the first U.S. government regulation that requires the use of EALs in the field, has become a significant force in the marine lubricant industry. Typical mineral oil lubricants do not meet the requirements for EALs, so new formulations are entering the market that meet both the technical and environmental performance needed.
DEFINING EAL
The VGP 2013 defines an EAL as being biodegradable, minimally toxic and not bioaccumulative, but it doesn’t provide technical specifications about its chemical makeup. Biodegradability definitions include the amount of dissolved organic carbon the substance must remove or the amount of theoretical carbon dioxide it must produce, or the amount of theoretical oxygen demand it must consume, plus acceptable test methods for lubricant and grease formulations. It presents similar effects and test methods for the definitions of
not bioaccumulative and
minimally toxic.
VGP 2013 specifies all lubricants used in an oil-sea interface must either be EALs or compliant with an approved international eco-labeling scheme, unless technically infeasible (
see Figure 1). The expression
technically infeasible means either no products are approved for use that meet manufacturers specifications, there are no alternatives for products that come pre-lubricated—such as wire ropes—and there are no products available at any port where the vessel calls or the changeover must wait until the vessel’s next dry docking. According to the International Convention for the Safety of Life at Sea (SOLAS) known as SOLAS 1974, all merchant and passenger vessels must complete a hull inspection in a dry dock twice within a five-year period, with no more than 36 months between inspections.
Figure 1. Despite different criteria in each, all international eco-labeling schemes are valid for products to be considered an EAL by the VGP 2013. (Figure courtesy of Croda.)
There are many other voluntary labeling programs that a lubricant could comply with to meet the definition of an EAL, despite their using different criteria (
see Figure 2). For example, Europe’s Ecolabel program is quite different from the mandatory VGP 2013, dividing lubricants into five categories instead of the two in the VGP 2013, and containing basic requirements for toxicity and bioaccumulation (
see Figures 3 and 4). Ecolabel specifies renewable carbon content levels for various products such as >50% for hydraulic fluids. It also restricts the use of certain compounds in formulations, including most metals and some organic compounds. Its certification allows products to display the Ecolabel logo on a drum for branding or marketing purposes and applies to land-based applications as well as marine.
Figure 2. Comparison of labeling requirements for the VGP with other worldwide standards. (Figure courtesy of RSC Bio Solutions.)
Figure 3. Comparison of relative bioaccumulation levels of various lubricant base oils. (Figure courtesy of RSC Bio Solutions.)
Figure 4. Toxicity comparison of lubricant base oils. (Figure courtesy of RSC Bio Solutions.)
MARINE LUBRICANTS IMPACTED
The VGP 2013 covers all lubricant applications that have an oil-sea interface (
see Figure 5). Most required applications are below the water line and include paddle-wheel propulsion, stern tubes, thruster bearings, stabilizers, rudder bearings, azimuth thrusters, propulsion pods and other mechanical equipment subject to immersion. EALs are strongly encouraged but not required on all above-deck equipment, but they are required on cables and wire ropes that are lowered into the water, although most technically infeasible exclusions occur in this category.
Figure 5. VGP 2013 affected all lubricants with oil-sea interfaces. (Figure courtesy of Croda Lubricants.)
The most commonly impacted lubricants are stern tube lubricants used on bearings that support vessel propeller shafts in the stern tube. The earliest work in the industry with EALs was done in this area, and in 2011 the EPA estimated the size of the problem to be in the millions of gallons of stern tube lubricant lost to the environment annually by vessels in the U.S., or around 0.7 gallons lost per day per vessel. Hydraulic fluids, gear oils, greases and compressor oils are the next most commonly impacted and where more industry attention is going now.
APPROPRIATE TECHNOLOGIES
There are four classifications of EALs recognized by the EPA and ISO, and all are appropriate for marine lubrication:
1.
Hydraulic Environmental Triglycerides (HETG), known as vegetable oils.
2.
Hydraulic Environmental Polyalkylene Glycols (HEPG), known as PAGs.
3.
Hydraulic Environmental Synthetic Esters (HEES).
4.
Hydraulic Environmental PAO (polyalphaolefins) and related hydrocarbon products (HEPR).
HETGs, natural esters based on glycerin with limited thermal oxidation stability, are minimally used as marine lubricants. If used at all, they are only suitable in low-temperature, low-pressure, less-rigorous applications.
A split between HEES, PAG and HEPR technology exists for marine applications. HEES base stocks offer a host of benefits for many applications. PAGs, synthetic polymers produced from the petrochemical base stocks ethylene and propylene, are used in stern tube applications offering benefits of their own.
Traditional PAOs from crude oil sources also are used, and the newest entrants into the suitable EALs are hydrocarbons produced from renewable sources. High-performing renewable HEPR products are gaining a foothold in the renewable marine lubricant industry.
Each category has positive and negative attributes for different applications. While there is no one formulation that is the solution for all products, Chris Donaghy, lube and polymer sales director at Croda in New Castle, Del., says, “The good thing for the environment is that environmental considerations are no longer the lowest priority in this matrix but are now a minimum performance criterion. There is a place for each of the different base oil technologies in this market (
see Figure 6).”
Figure 6. There is more attention now on the different base oil technologies in the industry. (Figure courtesy of RSC Bio Solutions.)
OEM APPROVAL
Unlike other industries, the marine lubrication industry has no industry-wide performance specifications to which equipment vendors adhere, so each manufacturer has its own lubrication specification.
With so many equipment models and designs in the marine industry, each with its own quirks, features and proprietary seals, uniform performance specifications are unworkable. This high degree of complexity puts the onus on equipment manufacturers to assess whether their equipment can use or could be modified to be used with EALs.
Ship owners must comply with the VGP regulation, but the standard doesn’t require them to use EALs if there is no product for a piece of equipment that meets its OEM spec. According to Jeff Brown, CEO and president at Novvi in Emeryville, Calif., “Ship owners look at lists of approved materials to make sure they don’t violate equipment warranties. Many won’t use a new EAL if an OEM hasn’t approved it for use.” The only way for new marine EALs to be approved for use is to be listed on OEM equipment specs, so lubricant manufacturers rely heavily on equipment OEMs for approval.
“OEM approval is key, but it is difficult to obtain,” Brown continues. “Many OEMs feel like they are stuck in the middle in today’s industry. A single thruster manufacturer could be inundated with 100 requests from lubricant companies that want to get their products certified. The VGP has been a burden on the OEMs and lubricant blenders serving this industry, and they have a lot of new work to do. This is not a situation that they were used to. Many don’t have people or processes in place and often pass the cost burden back to the lubricant manufacturer. We’ve witnessed them getting tired of the process and finding it difficult to manage.”
Peter Vickers, chairman and managing director at Vickers Oils in the UK, says it is possible for formulators that want to introduce a new lubricant to get EAL labels and self-certification on their own, but final approvals come from the equipment manufacturers, which involves working closely with them. “The major OEMs carry out physical tests, either directly or indirectly using accredited third party labs. Vickers Oils began working closely with manufacturers early on and developed close technical relationships. Now, the market has grown and there is a larger demand for testing at equipment OEMs,” he says.
Bernie Roell, vice president of technology at RSC Bio Solutions in Indian Trail, N.C., says since the regulations don’t spell out clear performance requirements, OEMs test EALs with their own stringent testing protocols before signing off that a new lubricant is fit for use. “Some OEM tests are more difficult than others, and some rely on the approval of other parties as well,” he says. “Over the past 20 years we have worked with OEMs and supplied the data they request, performed outside testing they needed and assisted with in-house testing. The proof is when products are used in real systems. Until then, most testing is bench testing that takes place on small-scale lab rigs.”
Scott Kovanda, Marine Division product manager at American Chemical Technologies in Fowlerville, Mich., says, “OEMs are the gatekeepers of the recommended lists issued to their customers. The multiple-year OEM-approval process also involves approvals from a long list of sub-suppliers, such as seal, paint and clutch manufacturers, before getting the final approval letter to be used in a system.”
Seal manufacturers are one of the outside parties involved in the long approval process. There are a wide range of seals, and each reacts differently to different materials. John Sherman, Marine Division technical service and development manager at American Chemical Technologies, says, “In some cases stern tube seals have failed at a faster rate when EALs were used when compared to mineral oils. Seal manufacturers have developed new elastomer formulations compatible with all standard EAL types providing the necessary seal life and performance to meet the dry dock intervals of their customers.”
IMPACT
Brown says, “The best impact the VGP is having is that it is actually making the environment cleaner and safer, which was the goal of the legislation. The program is beneficial because it’s accomplishing its goals and protecting our water. There is an unusual adoption curve and a long delay in activating this in all the ships because switching to an EAL only happens while in dry dock; so the industry has seen an incremental change with long periods of time between switching out to the new technologies.”
Ship owners are complying with the new rule, as virtually any major global shipping company, cruise line or ferry company is used to doing. “Learning how to implement it properly took some time. But now the VGP is just one of the pieces of environmental regulations ship owners operate under, and we don’t see a lot of trouble with adoption,” says Brown.
Roell agrees: “Unless customers have an infeasibility letter from an OEM, meaning they are still evaluating the use of an EAL, they comply. A significant amount of vessels out there use EALs in oil-water interface applications—more than 25% and approaching 50% of all vessels, according to some vessel management fleets.”
Donaghy says the VGP was a positive step for the U.S. marine industry. It has met the intent of the Clean Water Act to protect the waters of the U.S. Now VGP-compliant lubricants are widely available in the marketplace, so he believes fewer ship owners will claim technical infeasibility. “When the rule first appeared, the large users stocked up on mineral oils. Now we’re at the resupply point of many of the largest users,” he says.
Supply chains also have improved. “For the first few years it was easy to say that EALs were not available in port, but there are many in the market now. There’s a supply chain, and large producers have built a lot of products,” says Donaghy.
Being the first regulation to mandate EALs has had its growing pains. “EALs have been around and used in other industries for a long time. Much of this information isn’t new but it is to the marine industry in North America. Many ship owners and operators are still making decisions on EALs today and larger OEMs are in the process of updating their equipment specs. There are many trials still going on and equipment manufacturers that have not approved EALs yet. It has been a transition of an entire industry to using EALs that doesn’t know what they are,” says Sherman.
From Peter Vickers’ perspective, the industry has already adopted it. “The time of great emphasis for vessel managers to learn about these products, decide how to implement them, set up recordkeeping systems and gain certifications was three or four years ago,” he says. “There are now a lot more equipment manufacturers that have given approvals for EALs to be used in their equipment, sometime with modifications. More materials are available to formulators.
“Acceptance is worldwide, and the VGP has become a global standard,” Vickers adds. “Vessel operators need the flexibility to deploy vessels at short notice from one trading route to another. In our experience, most operators have taken the chance to introduce EALs into the fleet while at dry dock even if they’re not yet operating in U.S. waters. They want the freedom and can’t avoid the possibility that the vessel might do so in the next five years. A great many more vessels have adopted EALs than have called in U.S. waters.”
ENVIRONMENTAL PERFORMANCE
Lubricant formulators have gone to great lengths to develop high-performing products that meet the technical requirements for the vast majority of marine applications, so end-users shouldn’t have to give up environmental performance to meet their needs (
see Helping End-Users Choose). “With vegetable oils, there were tradeoffs, and users had to decide what they would give up. Some less thermally demanding applications still use them—for example, if they don’t carry heavy loads. But with PAGs and esters, there is nothing to give up,” Donaghy says.
HELPING END-USERS CHOOSE
“Most users in the marine industry are used to using mineral oil and have little knowledge about EALs and how they’re similar, different and what they can and can’t do,” says Sherman. He is creating an ASTM working group to develop a guide for VGP-compliant EALs for use in marine applications. This project is a joint cooperation between ASTM Technical Committee F25 on Ships and Marine Technology and ASTM Technical Committee D02 on Petroleum Products, Liquid Fuels, and Lubricants. Its goal is to be a first step in educating and helping end-users select EALs for use in marine applications that are compliant with the VGP 2013, and it will provide information on the different types of commercially available EALs and recommended test methods. The first draft of the guide is expected to go to ballot this month.
Sherman agrees, saying there is no longer a tradeoff. “EALs on the market today from American Chemical Technologies perform at a level that the industry is used to, comparable to or improving over mineral oil-based lubricants. They are compatible with new seals on the market and in OEM equipment, so there is no sacrifice to make.”
“It’s important to understand the environmental profile of base stocks and additives,” Kovanda adds. “Many base stock suppliers don’t have complete profiles for their customers to know whether it meets the VGP. If formulators have a reasonable expectation it would meet the requirements, they may need to do testing to know what subset of all base stocks and additives can be used at what concentration.
“Know what’s in the toolbox, then meet performance for a specific application,” Kovanda advises. “Products have to be equivalent or better than what ship owners and operators use today or what they’re used to. It’s challenging to meet performance requirements and all environmental regulations. But when operators use an OEM product, they have to trust it for the entire cycle between dry docking. They need it to work whenever it’s needed.”
Brown says most initial products suffered technically and didn’t meet performance specifications. “It was not acceptable for the industry to provide products like that. Initially, major shippers with global contracts were hit hard with regulations, forcing a difficult reconciliation,” he says. “But I’ve been surprised and pleased that most want to do what’s right. If we can’t deliver something that meets performance needs, we can’t expect end-users to adopt them or be happy. Novvi’s technology has unlocked so much that it has taken this decision off the table, making it easier to adopt not only on the end-user’s side but on the lubricant maker’s as well.”
Peter Vickers’ view is that it’s not possible to optimize both technical and environmental performance. “Additive technologies for EALs are not yet available that allow formulators to maximize both, so a balance must be struck. At sea a simple mechanical failure may pose a threat to life or impact safety of operations on an order of magnitude greater than for many land-based applications, so actual operating technical performance requirements for lubrications used there are greater. In formulating our own range of products, we deliberately set out to meet the highest standards of performance. Exceeding equipment performance requirements has to come before exceeding environmental requirements. It is doable, and it is balanced,” he says.
Roell says, “Not having a restriction on the renewability content in the VGP 2013 allows us more flexibility toward obtaining performance. We do use renewable content in both our current brands. However, our next generation brand will contain higher renewable content, carry both Ecolabel and VGP certifications and have the enhanced performance profile. So from a user’s standpoint there is no tradeoff. HEPR technology costs less than synthetic esters, but EALs are still between one and two times more expensive than mineral oil technologies due to the economy of scale and because mineral-based technology is derived from the lowest cost available base oil. I don’t think the cost will ever become as inexpensive. But end-users are looking for the best of the best.”
HOW MANUFACTURERS FORMULATE
American Chemical Technologies Inc., a formulator blender, incorporates any type of EAL into a marine offering without ties to a specific base stock. “We approach formulating marine EALs as many do, with a customer focus on not only the performance but the environmental profile of the base stocks and additives,” says Kovanda. “We have provided PAG fluids to customers for 35 years and also have solutions in the bio-sourced PAO realms. If a customer is used to a mineral oil and feels more comfortable with that product, we have solutions for them as well.”
Novvi LLC, a base oil producer, co-formulates with other base oils and additive companies that meet toxicity requirements to obtain desired properties. Brown says they co-blend PAO alternative renewable hydrocarbon base oils with synthetic esters and other materials to form their product with unique performance attributes that do well environmentally. “Novvi changed the game. Our lubricants gave better performance, could be dropped in and were more cost competitive than synthetic esters. Our approach has been to bring the best performance, environmental protection and economics to make it work,” he says.
RSC Bio Solutions does use renewable content in two product lines, and the next generation of one will contain higher renewable content. “We’ve had to overcome a barrier for the last decade because of a setback 20 years ago when vegetable oil products found their way into marine applications—it was disastrous. It cast a black cloud over EALs that they don’t work, fall apart and fail in systems. Over the years it has been slow going, but the VGP helped speed up adoption. We’ve learned how to use biodegradable, non-toxic, non-bioaccumulative base oils in the hydrocarbon category to offer advantages over esters and triglycerides,” says Roell.
Peter Vickers says all Vickers Oils products are based on esters. “As a class, they’ve been used for decades in various applications,” he says. “We chose a subset of the esters with the best environmental performance that didn’t have limitations seen in other classes, making them most suitable.”
Croda manufactures PAG and synthetic ester base oils and works with lubricant formulators and additive partners to demonstrate how their base fluid technologies can assist them in meeting the requirements of VGP and other Ecolabel programs. “We are trying to enable more environmentally friendly lubrication products and see this industry as in its infancy in terms of switching over,” says Donaghy.
DRIVING TECHNOLOGIES
The VGP created products that not only meet environmental regulations but also perform better. Past marine products were entirely mineral oil based. The VGP forced a transition in the marine industry to synthetic, as was seen in the automotive and other industrial segments.
“For years the perception among ship owners and operators was that environmentally friendly lubrications were not as good, and they were wary. Breaking down on a ship is scary and costs a lot of money,” Donaghy says. “Now, with HEPR, esters and PAGs, the attitude is better. The performance is there. The question is how environmentally friendly the legislators want these lubrications to be. At this stage, the industry is in its infancy. There are a high percentage of ships that haven’t yet come in, and the industry is conservative and slow to start making these changes. There was inertia to overcome the perception in the beginning, but the legislation helped.”
Donaghy continues: “We’d like to see more along the lines of the European legislation, specifying levels of bio-based or renewable content, because that’s what Croda produces. It would also be good for the market to have a consistent set of criteria that is easily understood, adopted and implemented. But the legislators need to be careful to assure tightened criteria can be met by commercially available technologies in order to meet their desired goal of protecting the environment. They have done the right thing in making the VGP incremental, and we expect future legislation to be more of the same with tighter specs on biodegradability and toxicology side. As more products become prevalent in the marketplace, eventually it will become the norm.”
Sherman says improvements in EALs might be slow in coming. “One source of improvements to formulations over what’s available now will come from looking at additives that hadn’t been considered or testing suppliers that hadn’t been available before, to determine if they can be used,” he says. “Using resources to develop additives for EALs doesn’t yet and might never make business sense for additive producers who are making new products primarily for the lubricant mineral oil industry, which has their biggest customers and account for more than 95% of the lubricants used in the world. Right now the best we can anticipate is that additive suppliers may review products in their portfolio, including those that might not be commercial at this time as to their suitability for EAL formulations, recognizing they could be used for this new application without the need of any development work. As new regulations force a greater volume of EALs to be used, more raw material suppliers may see it as a source of income in a new market and directly work toward improving products.”
Permits issued under the VGP 2013 are active for five years. The EPA Website will have the next proposed permit available for public review in the fall of 2017, so comments can be formally made to the EPA before the 2018 revision.
FOR MORE INFORMATION
American Chemical Technologies:
www.americanchemtech.com
Croda:
www.croda.com
EPA VGP 2013:
www.epa.gov/npdes/vessels-vgp
Novvi LLC:
www.novvi.com
RSC Bio Solutions:
www.rscbio.com
Vickers Oils:
www.vickers-oil.com
Debbie Sniderman is an engineer and CEO of VI Ventures, LLC, an engineering consulting company. You can reach her at info@vivllc.com.