Please describe a problem you solved through tribology testing using bench top rigs.
TLT Sounding Board April 2017
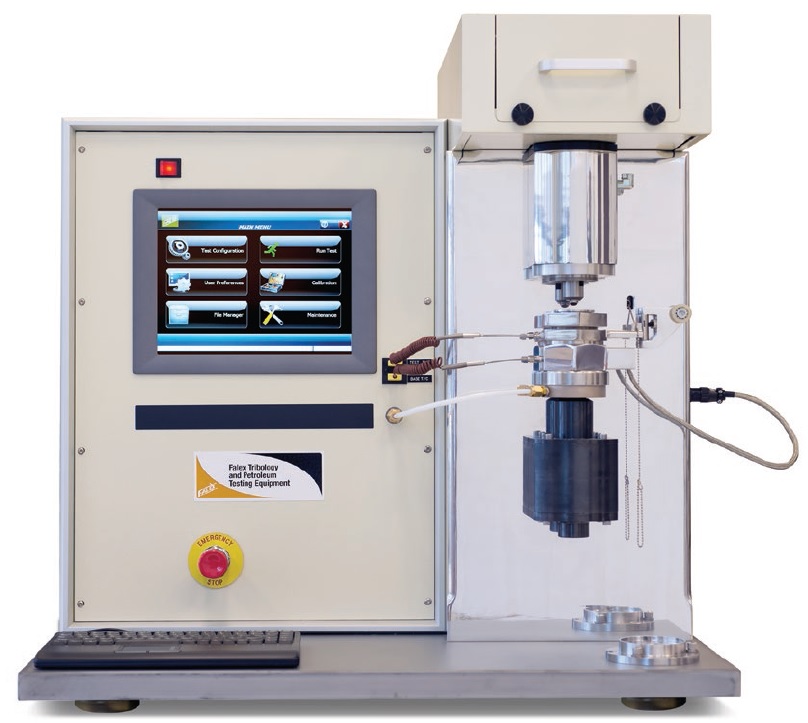
Bench tests for lubricants can be extremely helpful but only if you can properly replicate field conditions, which is far from an easy task. That was the consensus from TLT readers answering this month’s questions, 90% of whom say bench testing saves them both time and money. “These tests afford an opportunity to test technology on a smaller, safer and more cost-effective scale instead of running risky, potentially expensive field tests that could result in failure,” reported one reader. But readers also warned of the “great in the lab, failed in the field” syndrome, noting the difficulty in accurately duplicating such factors as load, speed, materials, temperature, HZ and the human interaction that invariably accompanies real-life work situations. Several readers say they successfully develop their own bench test procedures. “In the cases where we solved application issues with bench tests, it has never been with standard tests,” said one reader. Bottom line? “The pros outweigh the cons,” as one reader noted.
A customer had an issue with the rolls for their sheeting machines. Their challenge was shortened bearing life due to cement and silica dust as well as caustic water getting into the bearings. They had been using lithium complex thickened grease with no success, as the thickener was breaking down due to the caustic water and the ingression of destructive particulates. Due to the contamination issues, they were over-greasing daily to try and push out the contamination. Our company ran a rheology study that established that the best thickener option would be a polyurea-thickened grease. Rheometric analysis enabled a conclusion to be reached without further costly field tests.
We have looked at creep feed grinding fluids with some modified Falex pin and vee testing. We also have evaluated the best EP additives through the same testing. Variations of the step up and run up test were used along with studying different “plateau” regions and wear on the pin. (Example: More wear with better surface wear was actually better in some cases, depending on the metal removal operation.)
A student of mine modeled transmission clutch material testing using a pin-on-disc, making samples from the pin side out of the clutch material (running against a separator disc made of steel).
FZG test modified to test heavy high base oil viscosity on open-gear compounds/greases.
I wanted to solve the compressor gelation problem. I checked oxidation stability, but this property is not a problem. The problem was low-friction property. I now use SRV to check friction property.
Many problems solved: relative wear rates, comparative coefficient of friction, lube studies, material characterizations.
Developing low-friction engine oils with a specifically designed tester that simulates the ring on liner conditions. This was achieved by taking the actual rings and liner components and by replicating the mid-stroke speed and high speed in the tester.
In the process of redesigning a pipe-threading product for environmental reasons, we were stumped going from bench test to actual threading because the new products looked great in the lab but failed in the field. After studying the nuances in the test results of the product that was working in the field, we were able to tweak the test conditions to more accurately replicate the field and successfully redesigned the product.
We used a hard ball sliding against a hard steel flat bench test to try to understand the difference in the performance of two gear oils and different surface roughness of the steel. Load and speed were designed to duplicate known conditions in the hypoid gear set, which was wearing prematurely with a new gear oil. DOE helped sort out whether gear surface roughness or the type of gear oil was the most important cause of high wear. The flat steel surface was of the same metallurgy as the gears and the roughness chosen reflected the extremes of gear roughness. DOE did help eliminate some potential causes of the early wear out condition.
Rolling-elements bearing friction test of lubrication regimes.
In the cases where we solved application issues with bench tests, it has never been with standard tests. Always with tests simulating the application conditions.
Wear of valve train component. We developed our own procedure.
Useful bench top tests are hot plate, patch test and a microscope. I’ve found water ingress, fuel/glycol and abnormal wear caught in filters from them.
We frequently diagnose contamination problems using ASTM methods on our bench top equipment. We most commonly use results from our FT-IR to determine the percentage of water, fuel and coolant contamination in used oil.
In the early and mid-90s wind turbine gearboxes failed regularly despite oil samples showing good element levels. The FZG rig test on used oil checks the load carrying after several years. Oil samples show elements but do not show clearly if the additives are still functional. It was a standard test. Based on the results we tested the oils to FZG 14, which was not at all standard at that time. The FZG >14 is now a standard requirement.
Designed a bespoke piece of test equipment to accurately simulate a very specific tribological problem. This improved the correlation between lab data and field data. Subsequently we used this test method to produce significantly improved lubricants for this system.
We were looking at developing low-friction greases for CV joint applications. We took a CV joint, cut out tracks and mounted them on a reciprocating friction and wear tester, applied grease and ran a ball bearing ball against the track. We monitored the friction coefficient throughout the test and wear on the ball and track at the end of the test. We then tested a series of greases and used the data to develop a low-friction grease additive system.
We solved a journal bearing reliability problem with custom testing for rotating loads in a refrigerant atmosphere. The bench tester allowed control of loads, speeds, viscosities, bearing sizes and duty cycles. Once fully developed, the tester was able to duplicate multiple failure mechanisms.
In my experience, bench-scale and standard testing is used for a variety of purposes—basic research, material development and specific applications problem solving. For the latter, after a detailed tribosystem analysis, including the type of wear/lubrication regime common to the application, a test method was selected or developed to produce that type of wear or friction. Reference samples of current materials were tested in the same way and compared to candidate materials. Multiple repetitions were used to establish confidence in results.
Understanding of interactions and change in coefficient of friction as rotating parts interact with each other over time under given conditions. Testing was accomplished using a milling machine with custom furniture.
Wear/erosion of conduits by nanofluid flow. New ad-hoc test rigs used. First test rig was a multiple-nozzle jet impingement set up; second one was a flow-through system with a pipe-chamber.
Comparing and contrasting surface coating treatments.
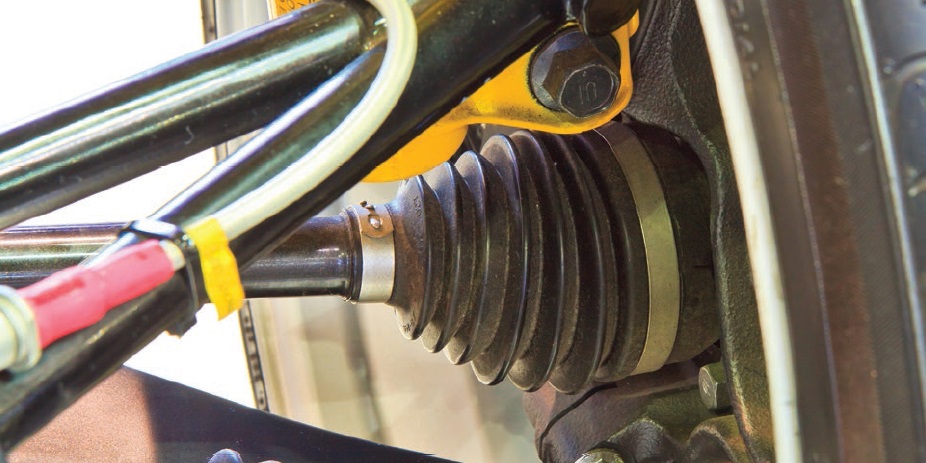
© Can Stock Photo / Reeed
Does tribology testing using bench top rigs save you time?
Yes 89%
No 11%
Based on responses sent to 13,000 TLT readers.
What are the pros and cons of tribology testing using bench top rigs?
Pros outweigh the cons. These tests afford an opportunity to test technology on a smaller, safer and more cost-effective scale instead of having to run risky, potentially expensive field tests that could result in failure.
Difficult to directly replicate field conditions, so you need to make assumptions on what matters—which can be subjective!
Test rigs allow us to validate our seal designs.
Pros: standardized equipment, small sample size for larger series. Results that are comparable but with different studies. Also useful for standards and norms. Con: finding a rig yielding results bearing a meaningful connection to real-life systems. In other words, a representative model.
Availability of rigs either at commercial labs, educational institutions or elsewhere.
They can save money and time, but it’s really hard to calculate load, temperature and Hz (that can simulate real compressor condition). I’m not sure that the condition I calculated is really representative of real condition. So I have to test using real compressor.
Pro: they save time and resources. Con: not enough people realize how beneficial they are.
Tribology testers need to operate with correlation to the actual system in the contact geometry, type of motion and materials and typical conditions for speed, loads, etc. Pros: faster and cheaper testing than field testing. Cons: the further the conditions are removed from the actual operating parameters, the less meaningful are the results up to the point to get a lot of data that has no real use.
If the bench top rig is replicating field conditions, you can go into the field with much more confidence and success. The problem is that if you are not replicating the conditions in the field well, you could be surprised by a pretty bad field test.
It cannot completely duplicate the actual environment in a working mechanical assembly. It does offer a look at specific variables, which may contribute to component wear and life.
Tribology and surface engineering is such a complex matter that bench test rigs can give detailed and accurate information surrounding a phenomenon.
Field (application) testing is expensive and can, in a real production environment, be very disruptive.
Pro: repeated conditions of tests, programmable. Con: expensive, time consuming, sometimes lack of proper connection to very complex real conditions.
It is difficult to trend data using those methods. Lab-in-a-box methods don’t work very well.
Pro: the small scale makes it easy to use in a laboratory setting. Con: it is difficult to replicate real-life problems encountered by full-scale equipment.
Advantages: quick and controlled comparisons can be made, key parameters can be isolated, and some rigs can be adapted to suit a wide variety of tribological conditions. Some service cycles in the field can last >10 years. Accelerated development tests are crucial. Disadvantages: there is a trade-off between tailored accuracy of test parameters to the specific application versus the benefits of generic comparison (e.g., 4-ball wear scar). Most bench top rigs (by definition) aim to remove the human influence from the system to improve accuracy whereas the human/operational influences are often key parameters in industrial environments.
To properly mimic your real-world contact you have to use the same materials, contact loads and stresses, geometries and surface finish. Speeds and temperatures have to be similar to the application but can be adjusted within known parameters to accelerate the testing, provided this does not change the failure mechanism. If you do not take care to mimic the real world properly, the results are often meaningless. Most standard rigs currently bear no relation to reality (4-ball test, for example), and this needs to be recognized when doing screening.
It does not simulate the real-life application.
Although bench testers take time to develop, they allow better control of test conditions. They also allow for larger sample sizes.
This is the subject of a book, but here it is briefly. Pros: variables more controllable, usually lower cost, repeatability obtained with multiple runs, small sample size, standards available for specific cases. Cons: may not simulate all key variables of an application, accelerated tests may result in wear modes that do not occur in the field, simple tests like the pin on disk fail to provide a good simulation of the problem and give misleading rankings. Test selection requires careful comparison with applications, unless the purpose is simply a generic comparison under controlled conditions.
Pros: they allow you to test specific interactions in conditions as close to in situ as possible. Cons: unless great care is taken in setting up the testing, variability will invariably be introduced.
The pros are known—fast, small volume of sample needed, flexibility of hardware to screen fluids and materials. Cons are applicability to transmission and axle level tests and to ASTM tests.
Pros: full control of test variables, easy measurement of wear from simple specimens. Cons: results might not be extrapolated to actual systems.
Pro: quick and easy. Con: doesn’t replicate field component tribology.
These rigs can be used as a quick screening tool to down select material selection or drive research down a particular path.
Real-world applicability.
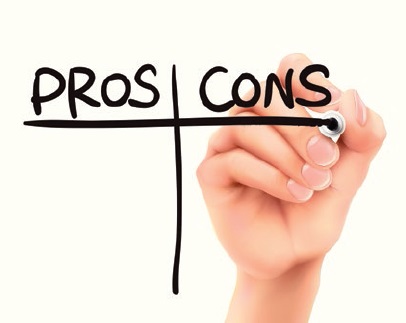
© Can Stock Photo / kchungtw
Does tribology testing using bench top rigs save you money?
Yes 90%
No 10%
Based on responses sent to 13,000 TLT readers.
Editor’s Note: Sounding Board is based on an email survey of 13,000 TLT readers. Views expressed are those of the respondents and do not reflect the opinions of the Society of Tribologists and Lubrication Engineers. STLE does not vouch for the technical accuracy of opinions expressed in Sounding Board, nor does inclusion of a comment represent an endorsement of the technology by STLE.