20 Minutes With Farshid Sadeghi
Rachel Fowler, Managing Editor | TLT 20 Minutes April 2017
This Purdue University professor solves problems for industry and government—and successfully integrates the research into his engineering courses.
DR. FARSHID SADEGHI - The Quick File
Farshid Sadeghi is the Cummins Distinguished professor of the School of Mechanical Engineering at Purdue University in West Lafayette, Ind. His background includes publishing more than 160 archival journal papers. He has given more than 300 presentations at various society meetings and industrial and academic institutions around the world.
Sadeghi also has an illustrious career as an STLE volunteer. He served as the editor-in-chief of Tribology Transactions, STLE’s peer-reviewed journal, from 2009-2016. Previously he was an associate editor for the journal for nine years. In addition, he served on the planning committee for the STLE/ASME International Joint Tribology Conference, chairing the 2000 meeting in Seattle.
Sadeghi received the Burt L. Newkirk Award in 1991 from ASME, the Edmond E. Bisson Award from STLE in 1996, the RCT Creative Research Award from ASME in 2008, the ASME Mayo D. Hersey Award in 2011 and the STLE International Award in 2011. He also has received several best paper awards from ASME and IMechE and teaching awards from Purdue University. He was elected a fellow of STLE and ASME in 2004 and 2006, respectively. At the 2016 STLE Annual Meeting in Las Vegas, Sadeghi received a special award from the society’s board of directors honoring his excellence in journal publishing.
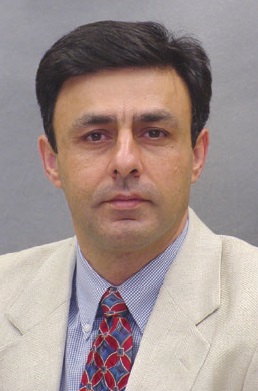
Farshid Sadeghi
TLT: Describe some of the tribology challenges, especially with bearings, that industry/government brought to you. How did you address them?
Sadeghi: I have spent the last 35 years studying tribology-related issues for industry and government. I started my research work in elastohydrodynamic lubrication (EHL) and then moved on to bearing dynamics and rolling contact fatigue (RCF). I also have done significant work in microelectromechanical sensors for tribological applications and wet clutch engagement. I have worked with a multitude of industries and government agencies to solve their tribological problems in these areas.
With EHL we developed numerical solutions for pressure and temperature distribution under rolling sliding contacts. We investigated the effects of surface roughness, debris contamination and material in homogeneity for a variety of applications.
In rolling contact fatigue, we used continuum damage mechanics to develop finite element models to estimate RCF lives of heavily loaded contacts under various operating conditions. We successfully modeled some of the pressing issues that bearing manufacturers are facing these days such as RCF in large bearings, butterfly formations, white etching cracks, etc.
Since bearings are used in a variety of conditions, the understanding of bearing dynamics is always one of the challenges in tribology. We have been developing a model commonly referred to as the dynamic bearing model (DBM) and now are at the cusp of having a virtual simulation tool. The model can be used to investigate various types of rolling element bearings in a fully dynamic and 3D condition. Recently we successfully developed a combined explicit finite element and discrete element model and, therefore, now have extended the capability of DBM by including the effects of shaft and surrounding structures flexibility in the bearing model.
We developed wireless telemetry micro-sensors to monitor the temperature of the cage of a bearing. The sensor was used to determine the temperature of bearing under fully lubricated and starved condition and has demonstrated that the bearing cage is a good indicator of the health of a bearing.
We also are working with the chemistry department at Purdue University to evaluate performance of new lubricant additives. We have performed experiments to measure the friction and wear in mixed and boundary lubrication with this lubricant and have found very promising results in reducing the frictional losses and wear.
TLT: How often does your academic/fundamental research impact industry and STLE?
Sadeghi: As I mentioned earlier, our research work is focused toward solving industry and government problems. Thus, our research is constantly impacting the industry.
My laboratory specializes in building custom test rigs to investigate particular industry problems. Industry players often don’t want to spend resources in building test rigs and experiments. We have performed experiments ranging from characterizing tribological properties of bearing steels, lubricants, etc., to evaluating the performance of entire tribology systems such as axial piston pumps, turbochargers and other components. We are collaborating with leading bearing manufacturers in developing a software to predict the life of a bearing depending on its loading and operating history. The aim of the project is to replace the numerous sensors currently being used to estimate the remaining bearing life based on their current state. We are working very closely with the bearing manufacturer to achieve this vision.
Another bearing manufacturer wanted us to simulate refurbishing. Between 60%-80% of the cost of new bearings can be saved by using refurbished bearings instead of replacing them. However, there were no models, which estimates life of the refurbished bearings or to optimize different parameters of the refurbishing process. The limited research in this area has restricted the widespread implementation of bearing restoration. So we developed a numerical model to simulate the refurbishing process and currently running experiments on refurbished bearing to validate our model.
TLT: What do you think are the upcoming challenges in tribology, especially bearings?
Sadeghi: In industrial countries the cost of energy and material losses due to friction and wear is close to 5% of gross annual product. A major challenge in front of us is reducing the energy consumption and moving toward greener technology. As tribologists, we play a direct role in reducing power losses in machinery while guaranteeing reliability and respecting environmental regulations.
As the automotive industry is adapting hybridization to improve efficiency, the power losses in bearings are becoming even more significant. In electric vehicles, the bearings are going to be the major source of noise. One major issue that is usually neglected is life of the bearing. You might be able to lower frictional losses temporarily, but if this comes at the cost of reduction in bearing life, then you really have not improved efficiency.
We need to develop a more realistic material microstructure model to evaluate the desired properties of materials for bearing applications.
TLT: What has been an ongoing challenge that needs to be worked on?
Sadeghi: The range of applications utilizing bearings have increased tremendously in recent years. Consequentially the range of bearing sizes has drastically increased from nanoscale bearings to wind turbine bearings. Most wind turbine gearbox failures are the result of bearing failures.
As we explore new horizons in space, our technology also needs to keep pace with it. The challenges involved in bearings for space appliances are very different than we have encountered until now. Traditional liquid lubricants can’t be used in space, so there is ongoing research on using solid lubricant coatings to improve wear resistance and reduce friction.
TLT: What advancements in experiments, modeling and knowledge do you think is necessary to solve the challenges?
Sadeghi: Currently there are various models that examine specific aspects of the working of the bearings. Just as there are lubrication models to evaluate pressure distribution, fatigue models estimate the impact of the loading on bearing components and bearing dynamics models. However, these aspects are not independent.
As the material deteriorates, the EHL pressure distribution is affected, which further modifies fatigue damage propagation. Hence, there is a need to develop a holistic model that takes into account all these aspects simultaneously. Recently we developed a finite elements model, which combines EHL and damage mechanics. Further, as we are making advances in controlling the material properties during manufacturing, we need to develop a more realistic material microstructure model to evaluate the desired properties of materials for bearing applications.
TLT: How does your research work enable academic education?
Sadeghi: I try to incorporate my research work into academic education. I teach a course on tribology at Purdue University. The students taking the course must develop a numerical software to calculate pressure distribution and other lubrication parameters for different types of bearings.
In addition, the course involves a project extension where I encourage students to read recent journal articles on tribology. Students have to follow the work in those papers and replicate part of their results. This not only helps in generating awareness about current challenges in tribology among students but also provides them with an opportunity to learn about research and know what is involved in research.
You can reach Farshid Sadeghi at sadeghi@purdue.edu.