Now it’s all about 4.0
Dr. Robert M. Gresham, Contributing Editor | TLT Lubrication Fundamentals March 2017
Welcome to the Industrial Revolution's fourth generation—and a Big Data approach to condition monitoring.
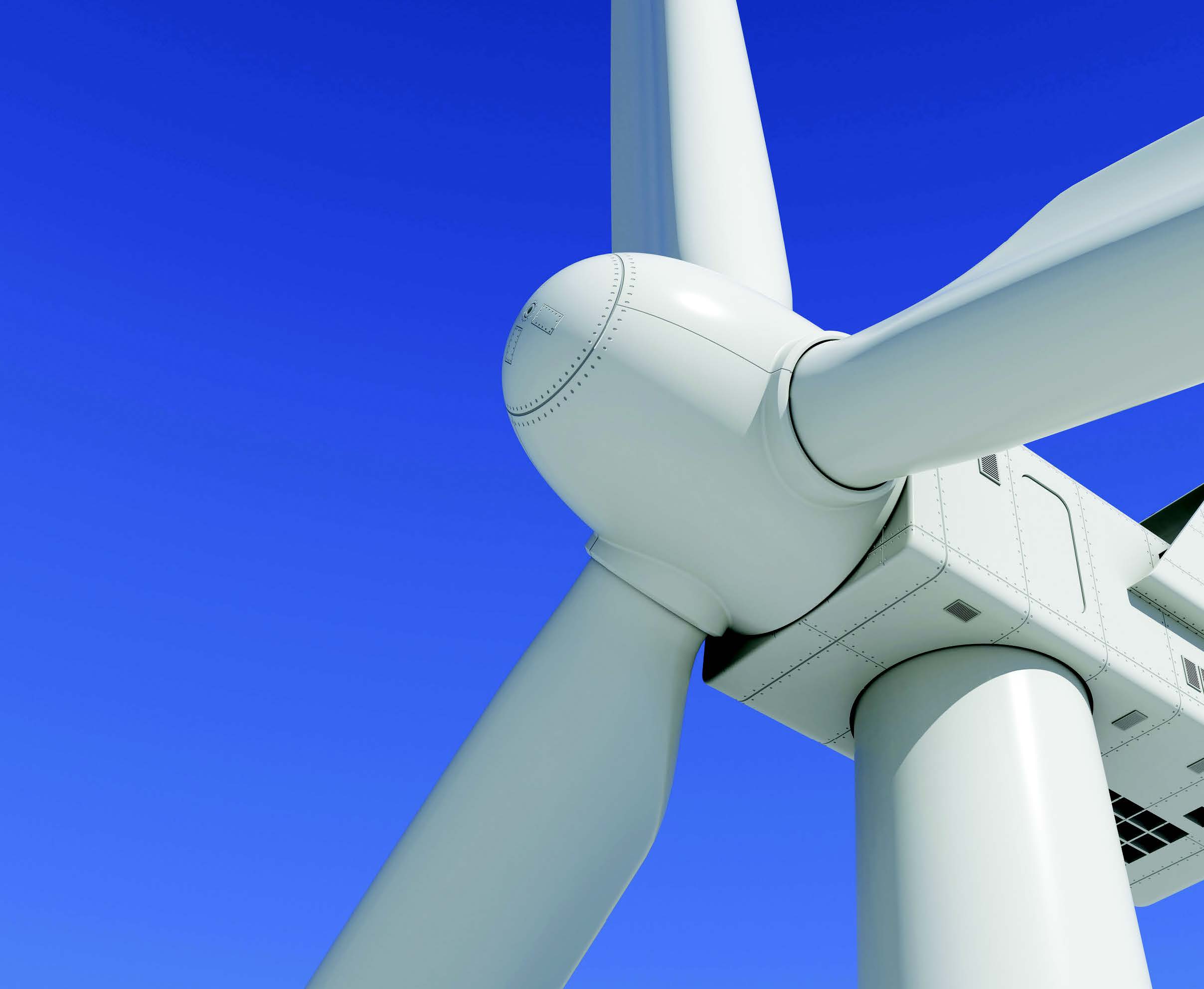
© Can Stock Photo / aleksanderdn
AS YOU MIGHT RECALL, STLE PUBLISHED AN EMERGING TRENDS REPORT in 2014. This report has been a great resource for STLE, providing insight into the major future directions of science and technology, regulatory needs and societal needs as they pertain to our industry. This fall, we initiated a new study with McKinley Advisors to update the previous report as to what trends were valid or not and to identify new trends emerging since 2014. Many of you will get a chance to contribute to this study—for that we thank you.
I covered one such new trend in an article in the August 2016 TLT titled Maintenance 4.0. The source for this article was the LubMat 2016 Conference in Bilbao, Spain, where presentations were made on the subject. Maintenance 4.0 is the new buzzword for this improved level of condition monitoring, maintenance and asset management.
With Maintenance 4.0, the fourth-generation maintenance, the emphasis is on risk management maintenance. Some of the characteristics of risk management maintenance involve an even higher level of condition-based maintenance through the use of sensors on critical equipment and through so-called Big Data analysis that determines more precise trending and the state of the equipment. Of course, determining the level of risk to the overall operation for each piece of equipment if it fails—and the economic impact—is taken to a much higher level. Finally, and this is critical, take proactive steps to eliminate that risk for that equipment or system with the most impact. For example, this could take the form of statistically determining if one brand of bearing lasts longer for a given application and using the longer-lasting bearing regardless of cost. In oil analysis, preferably through use of sensors, we monitor not just the health of the oil per se but, rather, the critical additive systems in the oil as they begin to break down. Thus, the oil can be changed before the machine actually sees degraded oil. More about this later.
When one thinks of the enormous capital investment and the equally enormous repair expense in large wind turbine farms, a Maintenance 4.0 approach would seem the only logical method to manage these assets. Manufacturing robots also can be an expensive investment that is amenable to a Maintenance 4.0 approach. Interestingly, when you think about manufacturing something with complex robots, it seems clear that the operations and maintenance departments begin to merge into one. An operator no longer makes or assembles things; the robot does that. The operator programs the robot to do what is needed, then monitors it through the use of sensors and Big Data analysis of the robot to see that it does what is intended. At the same time, the operator attends to the needs of the robot—its maintenance. Finally, when you consider the risks and costs associated with operation of nuclear power plants, a Maintenance 4.0 program looks pretty good as well.
At the OilDoc Conference this January in Bavaria, Germany, STLE-member Steffen Bots, OELCHECK (a prominent German oil analysis company), presented Handling of Oil Analysis Data – Opportunities and challenges of Big Data and Industry 4.0. Bots, who is CLS™ and OMA™ certified, vice chair of the OMA Certification Committee and serves on the STLE Certification Board, says, “The term Industry 4.0 or Industrial Internet should indicate the starting point of a fourth industrial revolution following modern industry, mass production and digital revolution. It is a synonym for automated production while all information about the production process, or the condition and performance of the production equipment, is continuously monitored. A key aspect of this idea is networking of machines, sensors and humans in order to communicate about the Internet of things.”
According to Bots, these ideas arose from a German government project, Industrie 4.0. The characteristics of Industrie 4.0 include the following: The production process is continuously monitored, all machines or components are linked to each other, Big Data from real-time information allow for optimization of the complete process, the human/worker is controlling everything from the cockpit and it covers the whole life cycle. I’m not aware of a similar initiative in the U.S. Perhaps some of you are; if so, please let me know.
Bots illustrated these concepts as they impact the oil analysis community with Oil Analysis 4.0. He sees that customers are asking for more and more data to be transmitted to them electronically. This, in turn, requires that internally more and more testing, results and interpretation must be monitored with sensors, programming, memory storage and related IT services to allow the data to be sent—and ultimately to conform to Big Data computing and transmission. Having toured his facility, it is already an electronic masterpiece of integration of their operations, yet more investment will be needed in the future. However, oil analysis as a maintenance discipline uniquely fits the model for Big Data analysis for Industrie 4.0.
Some of the bigger challenges are that typical relational databases are not up to the task of managing the volume and statistical requirements. New storage, computing and analysis methods are needed, yet there are no standards for such development. Equally, there are no models for secure access, data interpretation without human intervention to add application knowledge, technique and context. Or, as Bots puts it, “someone sitting in the cockpit.” Thus, there are no models for how to do all this in real time, at least yet.
These problems are not unique to the oil analysis industry. I am certain that each part of the industry has both its own unique problems coupled with the common problems related to how to utilize and implement the concept of Big Data for its particular application. Indeed, we hear similar concerns outside of manufacturing with the concept of automated cars and trucks.
Yet, this is the nature of all transformative science and technology. There are very, very few Eureka! moments. More, it is slogging ahead in the metaphoric mud of the technological trenches: two steps forward, one backward. This is how progress is made; this is how science is made.
As we move to the future, guided by such efforts as STLE’s Emerging Trends II Report, the tribology and lubrication engineering community will necessarily be at the forefront but behind the scenes, enabling many of these innovations to go forward.
Bob Gresham is STLE’s director of professional development. You can reach him at rgresham@stle.org.