20 Minutes With Bruce Morton
Rachel Fowler, Managing Editor | TLT 20 Minutes March 2017
Combine different forms of condition monitoring to draw the correct conclusions, advises this condition intelligence specialist.
BRUCE MORTON - The Quick File
Bruce Morton is currently a condition intelligence specialist for Dingo, a world leader in providing condition management solutions to asset-intensive industries. His primary responsibility includes data analysis for condition monitoring of components to make the best assessment of component health. He also interacts with customers on critical results and helps customers meet maintenance objectives and goals. Morton has 20 years of experience in used oil analysis laboratories, most of that time as laboratory manager. He worked in Caterpillar dealer labs in Utah and Nevada as well as POLARIS Labs in Utah. He has extensive experience in laboratory instrumentation, data analysis and ISO 17025 accreditation.
Morton received his bachelor’s degree in chemistry from the University of Utah. He was on the committee for developing the ISO/TC 108/SC 5/WG 4 standard, Machine Condition Monitoring using Oil Analysis. An STLE member, he holds the society’s CLS™ and OMA I™ certifications. In his spare time, Morton loves to work on cars and restore them.
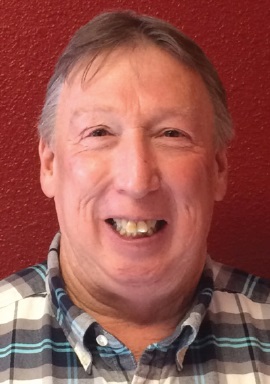
Bruce Morton
TLT: Technology has produced numerous advancements within the fields of condition monitoring (CM) during your career. What are key innovations you have witnessed?
Morton: Thirty years ago when I started in this field, condition monitoring was primarily accomplished by oil analysis. Vibration analysis was used to a limited degree in fixed-plant environments. There also are the time-tested visual inspections such as magnetic plug and filters inspections that give early warning to wear problems or failures.
As time progressed, along came such innovations as vibration analysis, which is used much more not only in plants and mills but also in some mobile-mining applications such as drills and shovels. Oil analysis is still the best bang for the buck. However, there are new applications of technology—such as smartphone apps—that make some of the traditional inspections and observations like magnetic plug inspections extremely easy to acquire the data. Oil analysis for machinery health has been compared to blood testing for human health. It’s an excellent diagnostic tool, but it doesn’t give the doctor—or the mechanic—the complete picture. In many cases, in both medicine and machine health, additional tests such as imaging and physical inspections are needed to identify and fix the root cause of the problem. The power of CM is that it brings all of an operation’s condition data under one roof. By analyzing this seemingly disparate data and looking at the complete picture, we can quickly pinpoint existing and emerging issues and perform the corrective work necessary to keep assets healthy and productive.
TLT: In your opinion, do you see one particular technology or methodology that distinguishes itself apart from another? Are the synergies more effective when applied together?
Morton: Definitely. There is a synergy when you can combine different methods of CM. CM today is when you combine all possible inputs into the analysis to provide a better picture of the health of a component or system. At Dingo we call the various inputs observations rather than data. The reason is that
observations, such as magnetic plug inspections, filters inspections, photos of a problem (such as appearance of the oil), technician inspections and real-time sensors, might be the trigger to take action, where oil analysis might not have exceeded any alert levels.
Despite the emergence of new condition monitoring technologies, traditional oil analysis has survived and is just as important as ever in extending the life of machinery.
© Can Stock Photo / scenery1
TLT: Comparing oil analysis, vibration, thermography and real-time data, do you see one more applicable today compared to when you first entered the field?
Morton: A few years ago it was thought that the brick-and-mortar laboratory was going to be replaced by on-board sensors and on-site labs. However, we still see that traditional oil analysis has survived and is just as important as ever. Over the years vibration analysis has become much easier and routine with hand-held analyzers. Thermography and ultrasound are very valuable in certain applications, but I see oil analysis and vibration as being used the most in fixed-plant, mills and mobile equipment.
TLT: With the various customers and industries you work with (mining, renewable energy, rail, oil and gas) do you see best practices or solutions that can be applied from one field to another that bring about change?
Morton: CM is used in some form or another in all industries. At Dingo, we primarily deal with wind energy, mining, fixed plants and mills, mobile equipment and rail. The more observations that can be included in the analysis of a component, the greater the chance of extending the life of that component. The main problem is that a maintenance program may include oil analysis, vibration analysis, filter inspections and other observations, but often all of these inputs cannot be viewed at the same time. There may be one program that has oil analysis data, another program that has filter inspections and another program that has vibration analysis data.
All of the inputs or observations must be taken into account. Getting all the observations together so that a condition monitoring analyst can make the best recommendation is sometimes a difficult task. Once you begin analyzing multiple observations from a component as one group of data, then it is possible to change out components based on condition rather than on a time-based schedule. At Dingo, we have a software program called Trakka that is able to receive multiple data inputs such as oil analysis, vibration, filter inspection, photos and technician inspections into one program so that the best decisions for a component can be made.
TLT: With as many years in the field and your vast experiences, what are some of the common issues that you see on a day-to-day basis that limits or has increased efficiencies?
Morton: Many of the issues are the same as have always existed. As an oil analyst, I see many samples that appear to have been taken incorrectly. This may be from external contamination of the sample such as improper sampling. Filter inspections may be performed but have no results of the inspection made in the report. Sometimes a problem is identified and no action is taken.
If time and money are being spent on a CM program, no matter what method of analysis might be used, take the time to do it right. Having to chase down results is time consuming and takes away from the end result, extending the life of the component. Dingo makes gathering data easier with a field inspection app (
see Figure 1) for a smartphone or tablet that can capture images and text to be imported into the Trakka software. Real-time data is a powerful CM tool.
Figure 1. Dingo field inspection app.
You can reach Bruce Morton at bmorton@dingo.com.