Positive outlook for wind turbine lubricants
Sushmita Dutta | TLT Market Trends February 2017
This fast-growth, risk-averse industry will remain attractive for suppliers of synthetic lubricants.
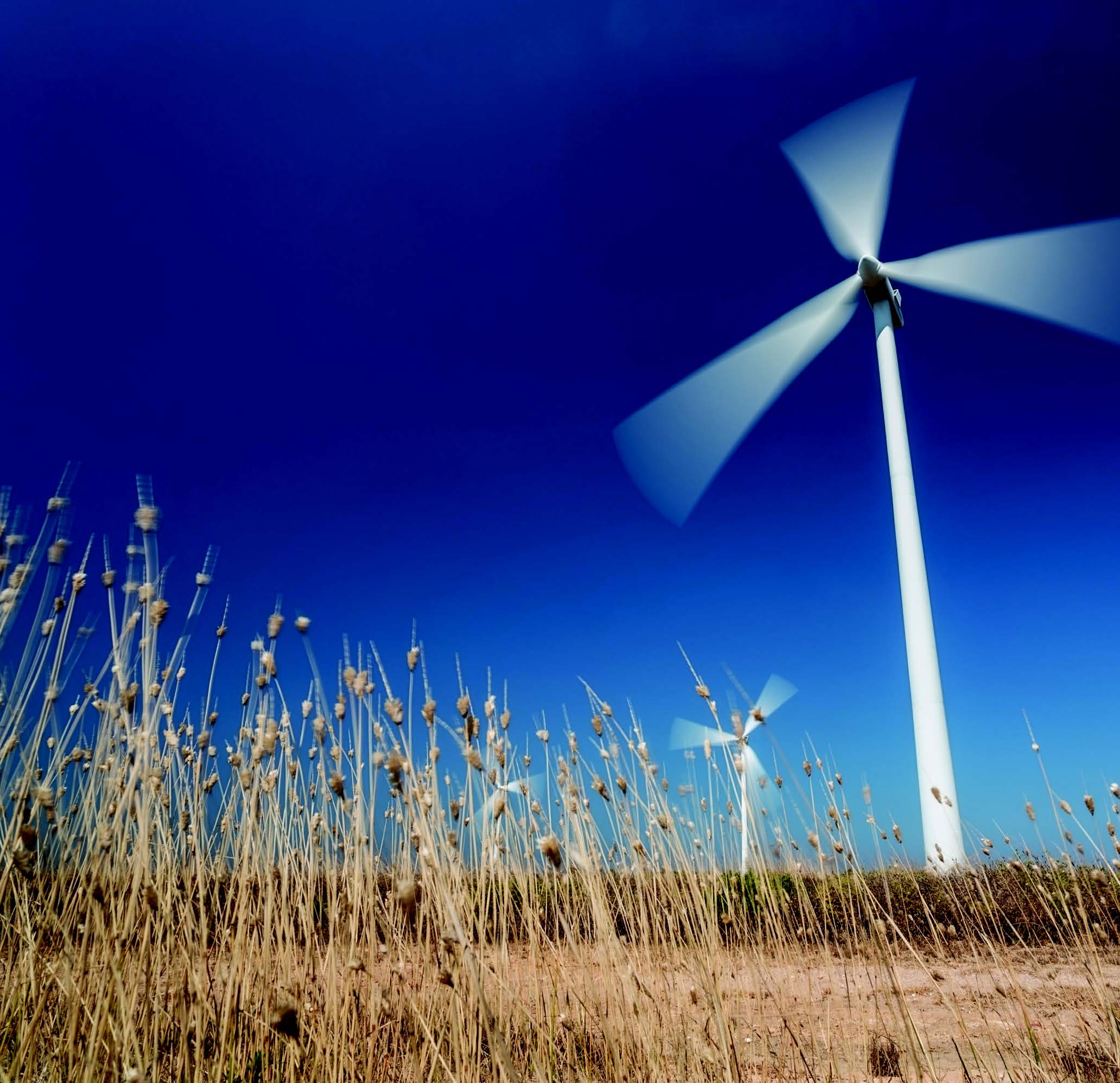
© Can Stock Photo / sergojpg
RENEWABLE SOURCES OF ENERGY, which include wind power, have developed rapidly since the United Nations Framework Convention on Climate Change was introduced in 1992 to address global warming and combat climate change.
With support coming from governments in the form of tax rebates, mandatory minimum purchase price and subsidies, due to its low-carbon footprint, the wind energy industry has witnessed tremendous growth in the past 25 years. Wind power is now the second largest electricity source globally among all the renewable power sources, according to the U.S. Energy Information Agency (EIA). EIA projects the wind power industry’s share in the global net electricity generation from renewable power will grow rapidly from 11% in 2012 to 19% in 2020 and 23% in 2040. These numbers suggest that the industry will grow as a reliable source of energy in the long term.
LUBRICANTS AND WIND POWER
Wind turbine lubricants play a critical role in equipment operation, maintenance and reliability of a wind farm. There are a number of lubrication points in a wind turbine, including gearbox, open gear, pitch gear, pitch bearing, rotor shaft, yaw bearing, yaw gear, hydraulic systems and generator bearings. These points require various lubricants such as gear oils, hydraulic oils and greases. Gear oil is used in lubricating gearboxes; grease is used on the main rotor shaft bearing, yaw bearing, pitch drive gears, blade bearing and generator bearing. Hydraulic fluid is used in hydraulic systems for blade pitch control. Improper or insufficient lubrication can lead to significant maintenance and operations cost or equipment downtime.
Wind turbine lubricant demand volume is a function of a variety of factors such as new installations, operating capacity, oil change frequency and penetration of direct drives. New installations (e.g., a new wind farm) will drive up lubricant consumption for the initial fill of wind turbines for this wind farm. The operating capacity, oil change frequency and penetration of direct drive turbines determine the service fill volume. Technological issues within each of these factors influence lubricant demand. Lubricant consumption per megawatt (MW) capacity of a wind turbine decreases with increasing MW capacity. As a result, increasing usage of higher capacity turbines results in lower lubricant usage. The extension of oil drain intervals also results in lower lubricant usage. The penetration of direct drives further dampens lubricant demand as direct drive installations do not need gear oils.
WIND TURBINE LUBRICANT DEMAND
Global lubricant consumption in the wind energy sector is estimated to be between 35 kilotonnes to 40 kilotonnes in 2015. This consumption has grown in line with the wind power capacity growth, which has increased seven-fold from 59 GW in 2005 to close to 433 GW in 2015 (
see Figure 1).
Figure 1. Global lubricant consumption has grown in line with the wind power capacity growth.
Gear oil, which accounts for 70% of lubricant consumption, is the most important lubricant category (
see Figure 2). A properly formulated gear oil increases the reliability of the gearbox unit and prevents failure. Therefore, usage of gear oils made from high quality synthetic base oils is well established in the wind power sector.
Figure 2. Gear oil is the most important lubricant category.
Synthetic lubricants used in the wind power industry are full synthetics, typically polyalphaolefin-based products. Synthetic lubricants are estimated to account for more than 80% of total lubricant consumption by the industry, and gear oils have the highest penetration of synthetic products (
see Figure 3).
Figure 3. Synthetic lubricants are estimated to account for more than 80% of total lubricant consumption by the industry.
GROWTH FACTORS
As gearbox failure can result in huge downtime costs for wind farm operators, gearless technology, also known as direct drive, has been developed. The technology completely eliminates gearboxes and problems associated with their failure. As direct drive turbines do not consume gear oil, which constitute 70% of the global wind turbine lubricants consumption volume, expansion of direct drive technology will have profound impact on lubricant consumption.
However, in the near term, potential for increasing the share of direct drive is quite small because not all OEMs offer this technology (
see Figure 4). This technology is more expensive as it requires usage of exotic materials to make permanent magnets, which increases the cost of installations. For higher MW capacity turbines, the use of direct drive technology is not preferred because of high capital cost. In addition, gearbox manufacturers have improved equipment reliability and the number of failures has reduced significantly.
Figure 4. Not all OEMs offer direct drive since the potential for increasing the share is small.
Currently oil drain intervals range from up to six years for onshore turbines and up to seven to 10 years for offshore installations. The average drain interval will extend gradually as operators try to optimize lubricant consumption while keeping in mind that the cost associated with downtime is much higher than the cost incurred for lubricants. As the industry is risk averse, farm operators are continuously trying to balance operational cost and performance.
The most significant lubricant demand driver will be growth in wind power capacity. Global wind energy capacity over the next five years will grow at a CAGR of 13% (
see Figure 5). Although the growth rate is lower than in previous years, it is still much faster than global industrial lubricant demand growth or lubricant demand growth in other end-use industries. Factors that could hinder capacity growth include grid connectivity issues, availability of land for onshore installations and withdrawal of government support.
Figure 5. Wind power capacity will be the most significant lubricant demand driver in the coming years.
Wind power farms, due to their remote locations, suffer from poor grid connectivity problems in some countries. Grid expansion is not always able to keep up with the rate at which wind turbines are growing, and this restricts the industry’s growth. For instance, in China about 25% of the capacity is not connected to the grid. This suggests that if grid expansion is not ramped up in the country in the future, wind industry’s growth could be relatively slower than expected. The availability of appropriate locations for wind farms also is becoming a topic of concern for the wind industry as wind turbines have to be away from population centers. However, this has resulted in the development of offshore wind farms. In addition, the industry is exploring the option of developing floating wind farms that will be able to operate in greater water depths and experience more consistent wind speed.
In recent years, the Spanish and U.S. governments have reduced monetary support to the wind power industry, but complete withdrawal has not been seen. Government support in the form of tax rebates, subsides and policy changes have been instrumental in the growth of wind power industry in any country. Therefore, withdrawal of government support could hamper the industry’s growth.
Nonetheless, the capacity addition over the next five years will be comparable to the capacity added in the last 10 years. Despite strong growth in capacity, it is expected that lubricant demand growth will lag installation growth. Gradual drain interval extension, use of higher MW turbines and penetration of direct drives will have a dampening effect on lubricant demand growth.
COMPETITIVE LANDSCAPE
The wind turbine lubricants market is highly consolidated and the top five suppliers account for 85%-90% of the market. The industry is being catered by the leading global lubricant companies such as ExxonMobil, Shell and BP. The advantage these companies have over niche or regional suppliers include OEM-approved products, supply reliability, consistent quality across the globe and capability to produce high-quality synthetic lubricants. The entry barrier for a new lubricant supplier is high due to long product-approval processes. Despite this, in the last five years the industry has witnessed the entry of mid-tier lubricant manufacturers.
CHALLENGES
Growth of offshore and floating turbines will add to the challenges associated with wind turbine lubrication. Moisture is a big problem in a gearbox because it leads to severe corrosion if not expelled from the system. Therefore, lubricant suppliers need to focus on developing more robust lubricants to help minimizing gearbox failure. Mixing and contamination of grease with dirt and water are common problems reported by wind farm operators. However, these problems are not as common with automatic greasing systems as with manual lubrication. Lubricant suppliers should collaborate with farm operators to develop proper training of maintenance professionals to minimize these issues.
CONCLUSION AND OPPORTUNITIES
Wind power is a high-growth industry and its lubrication needs are expected to trend in a similar fashion. The industry will drive demand for high-performance lubricants, and suppliers willing to offer product customization and after-sale services will have higher growth prospects. This fast-growth, risk-averse industry will remain attractive for the suppliers of synthetic lubricants as wind turbine lubricants have a high penetration of synthetics as compared to other industries.
Sushmita Dutta is project lead-energy for Kline. You can reach her at sushmita.dutta@klinegroup.com.
Kline is an international provider of world-class consulting services and high-quality market intelligence for industries including lubricants and chemicals. Learn more at www.klinegroup.com.