Modeling miniature earthquakes
Drs. Wilfred T. Tysoe & Nicholas D. Spencer | TLT Cutting Edge February 2017
Rate-state theory, which describes the time-dependent nature of the contact during friction and is used to describe earthquakes, is tested on a micromachine.
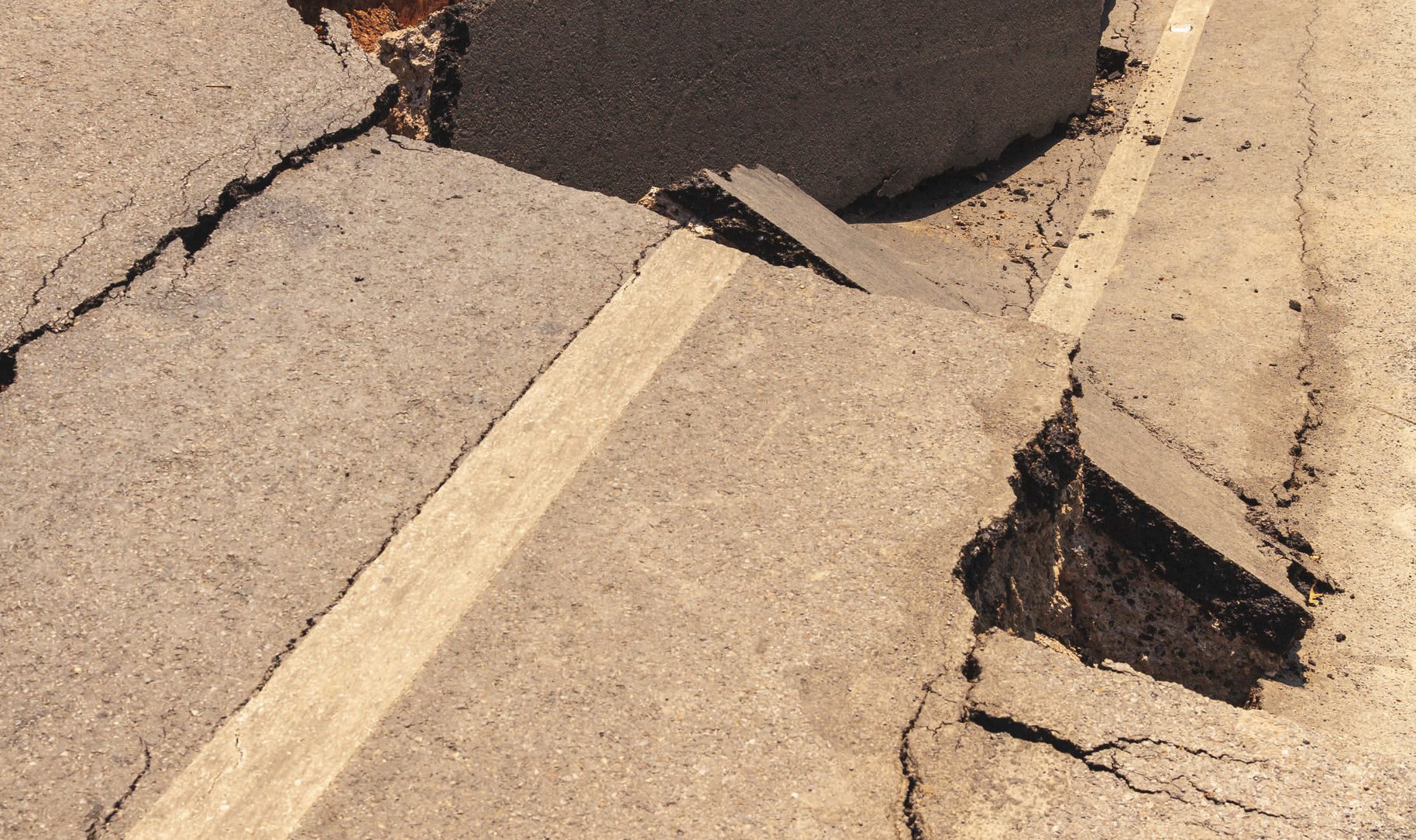
© Can Stock Photo / Naypong
IN MOST FRICTION MODELS, THE CONTACT CONDITIONS are assumed to stabilize almost instantaneously once the two surfaces come into contact. This is implicitly assumed in the atomic scale Prandtl-Tomlinson model for sliding friction. This model assumes the existence of an energy barrier to sliding. The imposition of a lateral force lowers the height of the barrier until, at high lateral forces, the barrier reduces to zero. At intermediate forces, thermal energy causes the atoms in the contact to transit the barrier to allow sliding, thereby giving rise to temperature-dependent friction. The model also predicts that the friction force increases with sliding velocity because, as the velocity increases, the system has to transit the barrier more quickly, thus requiring larger lateral force to overcome the energy barrier.
However, the situation becomes more complicated if the contact evolves with time—so-called
rate-state friction—where the friction force depends on the state of the system. While such an evolution could be due to a number of effects, an obvious one is a time-dependent increase in contact area that causes static friction to be larger than dynamic friction. Such time dependence also implies that friction should decrease with increasing velocity, since the contact has less time to evolve at higher velocities. A key indication of rate-state effects is an initial
decrease in friction with sliding velocity (when rate-state effects dominate) followed by a transition into a regime in which the friction
increases with velocity. These ideas also explain commonly observed stick-slip behavior. At high sliding speeds and low loads, junctions have less time to evolve, tending to result in steady sliding, while higher loads and slower sliding produce stick-slip behavior since the contact has more time to evolve. These are just the conditions that apply as rocks in a fault slide over each other, the slip—in this case—being an earthquake.
A powerful way to explore such time-dependent systems is to perturb the system and follow the response after suddenly changing the sliding velocity. However, it is challenging to build a tribometer with adequate velocity control over a wide range together with the ability to rapidly change the sliding velocity. This was accomplished by professor Maarten de Boer and graduate student Sameer Shroff from Carnegie Mellon University using the micromachine shown in Figure 1. A thermal actuator expands on heating, allowing sliding velocities to be varied between 0.1 and 3,000 micrometers/s. Heat sinks shunt the heat generated in the actuator before it reaches the friction block, which remains at constant temperature.
Figure 1. (a) Optical image of a fabricated and released test platform. Yellow boxes indicate details shown in the corresponding figure parts (b-e). (b) SEM image of the friction block. Cross section α–α′ is labeled and shown in f. (d) SEM image showing two of the six friction feet below the friction block. (e) AFM scan of the counter-surface below the friction feet shown in d. (Published with permission from Ref. 1.)
Importantly, they could adjust the heating time profile to obtain very rapid jumps in sliding velocity. They used this instrument to study the friction of polycrystalline silicon functionalized with a boundary lubricant and were able to measure the expected velocity-dependent friction (
see Figure 2a). They also rapidly increased the sliding velocity from 50-1,000 micrometers/s (
see Figure 2b) and found transient behavior as the system slid at a high speed in a state that had developed at a low speed. While being far from an earthquake, this model system contains all its fundamental physical ingredients. The de Boer group analyzed the results using perturbation theory and the brave reader is invited to explore Ref. 2 to see how they did it.
Figure 2. (a) Dynamic friction coefficient versus pulling velocity in the steady sliding regime. (b) Upper panel: Pulling velocity versus time showing a velocity step at t = 3 ms. Lower panel: Resulting spring elongation versus time. (Published with permission from Ref. 1.)
REFERENCES
1.
Shroff, S.S. and de Boer, M.P. (2016), “Full assessment of micromachine friction within the rate-state framework: experiments,”
Tribology Letters,
63, p. 31.
2.
Shroff, S.S. and de Boer, M.P. (2016), “Full assessment of micromachine friction within the rate-state framework: theory and validation,”
Tribology Letters,
63, p. 39.
Eddy Tysoe (left) is a distinguished professor of physical chemistry at the University of Wisconsin-Milwaukee. You can reach him at wtt@uwm.edu.
Nic Spencer (right) is professor of surface science and technology at the ETH Zurich, Switzerland. You can reach him at nspencer@ethz.ch.
Both serve as editors-in-chief of STLE-affiliated Tribology Letters journal.