Complexity in ISFA (in-service fluid analysis): Part XXX
Jack Poley | TLT On Condition Monitoring January 2017
Holistic condition monitoring in the 21st Century: Part II
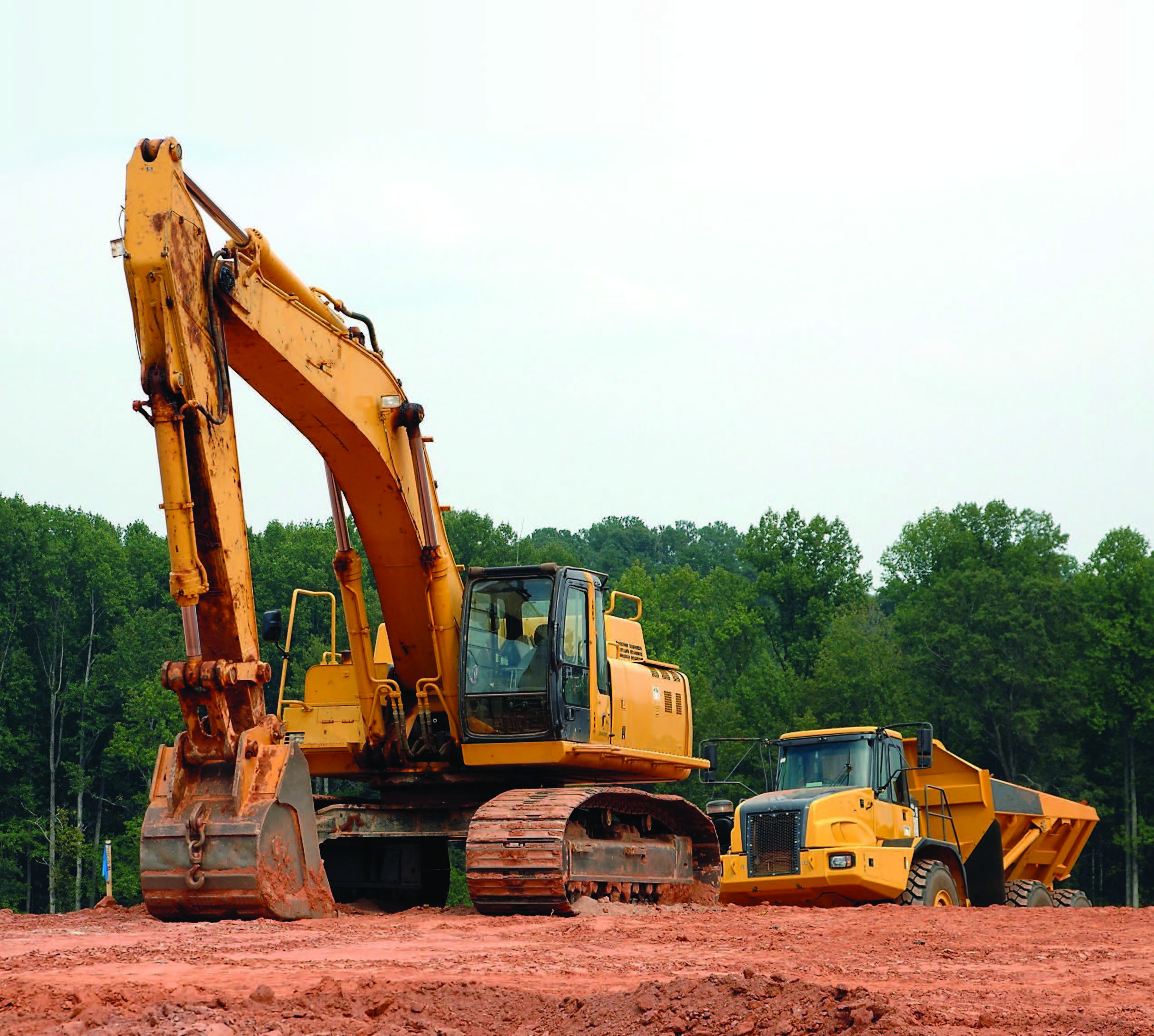
© Can Stock Photo / paulb
LAST INSTALLMENT I RE-INTRODUCED SOME THOUGHTS I advanced a decade ago regarding the eventuality of a holistic approach to condition monitoring (CM). The theoretical aspect is simple and direct: having additional, relevant CM data available significantly increases one’s chances of assessing machinery condition accurately, with all the attendant benefits. Here’s a sample list of CM data types that might be considered in a multi-faceted approach to reviewing and assessing data.
•
The two primary (well-established) CM subtypes over many decades:
1.
Fluid analysis (i.e., in-service fluid analysis, oil analysis)
•
Fluid makeup: true data normalizing
•
Lube sensors (Tier 1 inspection, relatively recent)
2. Vibration analysis
•
Ultrasonics or other acoustics
•
Thermography
•
Temperature
•
Pressure.
HOW MIGHT WE SORT THROUGH THESE DATA TYPES?
•
The concept of holistic CM necessarily involves multiple disciplines/techniques, implying that these disciplines must now be considered in the context of each other. There are
deep-thinking intelligent agents (IAs) in use for vibration (VIB), as there are for ISFA, and expert systems are in play for other CM data, too. Multiple IAs need to be amalgamated for best overall effect.
•
A new consideration when more than one CM discipline is involved will be the relative strengths of each CM approach as to its ability to isolate particular problems accurately in the overall holistic picture. One might disable or subordinate an algorithm in one IA in favor of another IA’s capabilities and logic path, based on a superior aspect of the favored discipline. The idea is to balance the emphasis from each IA so that one is assessing data with increasing focus and confidence, maintaining speculation at a minimum.
•
The best benefit from having the advantage of multiple CM tools is that they can be complementary and, most important, clarifying and validating. For example, suppose one has a significant vibration reading and also abnormal levels of large (>4µ and greater diameter, in particular) ferrous wear particles from ISFA testing. This combination could readily indicate the onset of catastrophic failure, as such a combination may represent fatigue trauma from overload or other cause. While the presence of large ferrous particles is forbidding, it is really the vibration anomaly that adds the most weight to the good possibility of catastrophic wear development. Perhaps with only a few simple diagnostics, a decision would be made to stop the machine and literally inspect it for the suspected problem. Both disciplines provided complementary data that, analyzed contextually, obviated the likely problem.
If we take the ferrous wear debris result alone, there is no justification to conduct a visual inspection unless diagnostics pointed in that direction.
Taking the vibration issue alone, several things are possible and, almost certainly, no teardown would occur without revealing diagnostics.
While the combination of data from those two major CM tools seems to obviate the decision, diagnostics should still be performed, if possible. The difference is that one might choose to inspect even if diagnostics provided no clue to a developed problem because that particular combination of data would seem telling. There’s enough evidence to consider action. Maybe a third technique can be availed as well. The bottom line is that maximized, diverse CM coverage can have huge efficacy.
Maybe you say, “
Well, sure, belt and suspenders are always better, but they’re perhaps cost prohibitive.” This could be the case; however, it doesn’t have to be. I’m aware of numbers of existing maintenance programs that include both vibration and fluid analysis, but the two disciplines are not meshed together, i.e., they are not considered in concert with each other. The respective maintenance teams handling these CM functions hardly ever exchange information, let alone wins or losses. This is a big—and sad—oversight. In such cases the ISFA is used primarily to govern on-condition lube changes instead of adding the value of suggesting action that can often prevent abnormal vibration readings (from wear, most often) occurrences in the first place.
So such companies are not complaining about belt and suspenders cost as they purport to get benefits from both the belt and the suspenders. What does not happen in the way of benefits is the
synergy that’s available with the combined information from two or more different approaches to machine monitoring. This is often the largest chunk of monetary benefit available, and if not availed, it’s, as I like to say, money left on the table. CM is about money, nothing else. Maximized production, maintenance expense, safety—it’s all about money. Take the money and run (productively) to the bank.
IMPLEMENTATION CONSIDERATIONS WITH HOLISTIC CM
•
Several IAs, or the expansion of a sufficiently powerful IA to accommodate the multiple IA equivalent, will be necessary in order to accommodate the variances in the respective disciplines and algorithms, as well as accommodate the added data volume.
•
Sensor information (from VIB and fluid monitoring sensors) will be especially proliferate, necessitating systematic data reduction to look at significant data excursions as to range and dwell time, trends and so forth.
•
Sensor data output contrasts greatly with any testing that is episodic, such as testing lube samples. Samples are taken at intervals involving weeks or months, sometimes longer. A lot can happen in between. Sensors, on the other hand, also are providing readings at intervals, except those intervals are in terms of seconds and fractions of seconds, dependent on the sensor’s programming. This micro-episodic behavior necessitates mathematical crunching and reduction to get these data to manageable, practical levels.
I’ll add some more flesh to the holistic CM concept next article.
Jack Poley is managing partner of Condition Monitoring International (CMI), Miami, consultants in fluid analysis. You can reach him at jpoley@conditionmonitoringintl.com.
For more information about CMI, visit www.conditionmonitoringintl.com.