Minding the fleet from the inside out
Dr. Nancy McGuire, Contributing Editor | TLT Feature Article January 2017
Oil analysis keeps vehicles running smoothly on land, fleet and air.
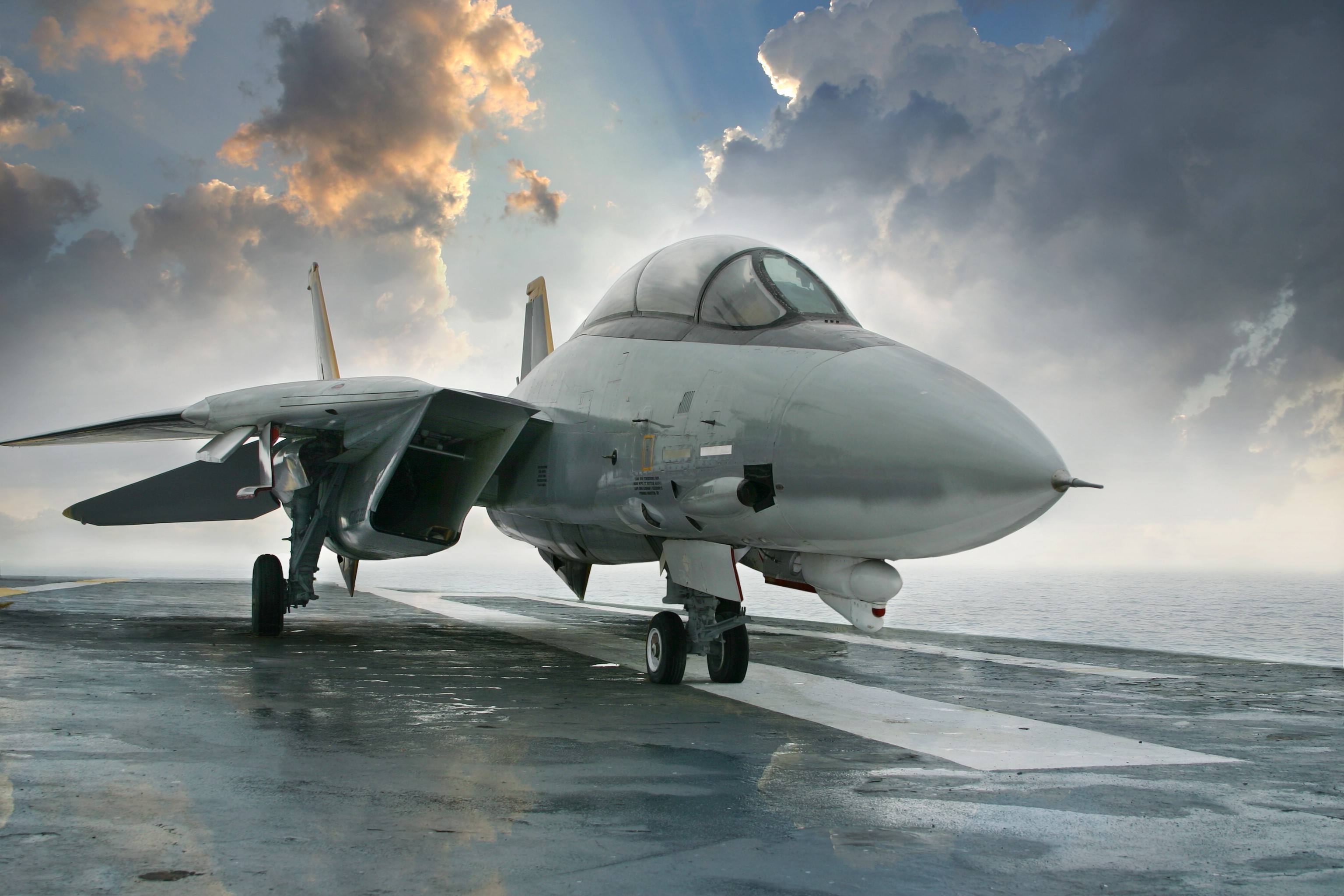
© Can Stock Photo / Willard
KEY CONCEPTS
•
Managers of vehicle and boat fleets of all sizes do regular oil analysis to keep their equipment working longer.
•
Oil analysis helps optimize your operation and alerts you to impending equipment failures.
•
No one test tells the whole story. Interpreting test results takes skill.
IT'S A SUNDAY AFTERNOON AND THE FERRY IS PACKED TO CAPACITY, carrying island residents and weekend tourists across Vineyard Sound to the mainland terminal on Cape Cod. Now would not be a good time for a mechanical breakdown, but you’re not worried. Because your oil analysis lab alerted you to a flurry of metal particles from that gear that was starting to go, you were able to order a new one in plenty of time and install it between scheduled runs. The ferry made its next run right on time and has been running just fine ever since.
WHO DOES THIS AND HOW MUCH?
Bryan Debshaw, CEO of POLARIS Laboratories®, a commercial fluid analysis laboratory in Indianapolis, Ind., says that his oil analysis customers run “the whole gamut” of industries—oil and gas operations, transportation, mining and power generation. “All sizes of vehicle and boat fleets have set up oil testing programs,” he says.
POLARIS Laboratories found that 53% of its customers who have oil analysis programs use management reports to set and adjust standard lifecycles for their equipment. Management reports examine average lifetimes for many units, usually grouped by unit type or manufacturer and model. “Maintenance teams and those in charge of equipment replacement have an estimation of how long a unit will last before a major rebuild or replacement,” Debshaw explains. Oil analysis assists by evaluating whether the equipment is wearing more quickly than normal or showing signs of entering early failure mode; corrective actions can be taken early.
In a recent Webinar (
1), STLE-member David Hilligoss, lubricant segment leader for PerkinElmer, a laboratory instrument manufacturer in Venice, Fla., noted that Caterpillar Inc. runs the largest oil analysis program in the world, followed by the U.S. Military (
2). Western markets for oil analysis are mature and demand is staying more or less level. Asia-Pacific has become the largest market over the past decade because of rapid economic development.
Jamie Antaya, senior fleet mechanic for AAA Northeast in Providence, R.I., oversees a fleet of about 120 service trucks that provide roadside assistance all over Rhode Island. These run from half-ton pickup trucks for small jobs like jump starts to larger medium-duty flatbed trucks for vehicle towing. “Some of the trucks have more than 400,000 miles on them,” he says. He recommends oil analysis for any size of fleet. “It’s best to start the program from Day One, and this is especially important for high-value assets,” he says.
Antaya has been with AAA for about six years and his shop’s oil analysis program is about a year old. AAA tests its trucks every 5,000 miles, which is often just a month’s worth of service. “The program was started because truck engines were failing, but since the oil analysis program has been in place, there have been no total engine failures,” he says. No testing is done in house; all the oil testing is done by an outside lab under their oil vendor’s service contract. Antaya’s educational background is in this area, so he came to the job well equipped to interpret the information coming back from the lab.
Stephen Clifford is the port engineer for The Steamship Authority, which runs ferry boats between Cape Cod, Mass., and the islands of Martha’s Vineyard and Nantucket. He oversees 10 boats that run a regular schedule between Martha’s Vineyard and Woods Hole, and between Nantucket and Hyannis. Clifford started with Steamship Authority in 2007, and his previous jobs were in similar functions. His company’s oil analysis program covers the generators, engines and reduction gears for the ferries. They get lab tests for wear metals, contaminants, additive metals and fuel dilution. All of the people involved in his operation’s oil monitoring program are licensed engineers, but there was some on-the-job training as well.
A ferry from the Steamship Authority. (Photo courtesy of Stephen Clifford.)
Steamship Authority ferry. (Photo courtesy of vincebusam. Available at www.flickr.com/photos/vincebusam/.)
WEAR METALS
What do fleet mechanics and engineers learn from these oil tests? “Like many fleets that run oil analysis programs, AAA Northeast’s main test is for metals (aluminum, iron, copper and zinc),” Antaya says. Metal particles in an in-service lubricant can come from parts that are starting to fail or from various kinds of contamination, and they can act as abrasives and accelerate wear in other parts downstream.
“Wear metal testing is by far the most common oil test requested,” says Debshaw. “Very few vehicle fleet operations are equipped to run wear metal analysis onsite, so POLARIS Laboratories does this on all their lubricant samples.”
The method of choice for wear metal testing is inductively coupled plasma atomic emission spectroscopy (ICP-AES, often referred to as just ICP). This type of analysis typically covers about 24 chemical elements, including wear metals, contaminants and dirt and metals used as lubricant additives.
Hilligoss explains that ASTM D5185 is still used for ICP analysis even though it is an older method. Most labs modify this method for faster sample throughput by making their dilutions on a volume-to-volume basis rather than by weight. Volume-based dilutions are not suitable for determining absolute values for metal content, but they can be used to measure trends over the lifetime of oil from one specific reservoir. “Trend analysis also means that most labs can loosen QC standards to 10% now rather than the 5% specified by this method,” he adds.
ASTM D5185 requires the use of internal standards—reference metals added in known quantities to each lab sample to serve as calibration and quantitation markers. Internal standards must be elements that are not otherwise present in your samples so that the signal comes only from the reference standard. “Cobalt is still the most commonly used internal standard, but other internal standard metals recommended for this method can present issues,” Hilligoss says. Cadmium, one such standard, now shows up as a wear metal in some samples. “Rare Earth elements, including yttrium and scandium, can affect results when they interact with some viscosity improvers,” he adds.
Hilligoss noted that lubricant analysis laboratories must have ICP instruments that are set up to run nonaqueous samples, and samples must be stirred just before they are run to make sure that the wear particles are included in the sample stream instead of settling to the bottom of the sample container. “Newer ICP instruments can achieve the needed precision using smaller samples, which speeds up sample throughput,” he says.
FUEL CONTAMINATION
Gas chromatography (GC) has largely taken over from Fourier transform infrared spectroscopy (FTIR) for fuel contamination testing in lubricant oils, according to Hilligoss. Older types of diesel fuels used high-sulfur base oils, and the FTIR methods used this sulfur as a marker. “Newer low-sulfur fuels cause less pollution, but they rendered FTIR ineffective as a test method,” he says.
“Viscosity measurements are still used as an initial screening for fuel contamination, but a high soot content can keep viscosity high, counteracting the viscosity-reducing effects of fuel dilution,” says Hilligoss. Flash point tests, another indicator of fuel contamination, can be inaccurate and hard to automate.
“GC’s ability to distinguish between gasoline, diesel and biodiesel makes it a more reliable and valuable test,” Hilligoss says. Its linear response allows you to quantify the amount of each component present in the sample. “In addition, GC requires no sample preparation, an important consideration in today’s busy labs,” he adds.
The previous standard GC method for fuel dilution testing takes about 35 minutes per sample because the sample flows through the instrument column at the same speed from start to finish. ASTM D7593, a newer standard now in round-robin testing, uses a backflush configuration to reduce sample run time to about two minutes. “Fuel contaminants, which tend to be more volatile, reach the detector early in the run, and the rest of the sample is backflushed off the column,” says Hilligoss.
COOLANT CONTAMINATION
Coolant contaminants increase the acidity of a lubricant and they promote corrosion. “GC is replacing ICP for detecting coolant contamination,” says Hilligoss. Because sodium, potassium, boron and molybdenum are now used in oil additives as well as coolants, ICP analysis is now less valuable for determining coolant contamination. GC distinguishes lubricants from coolants by identifying the various organic components of each.
FTIR only detects high levels of coolant contamination, and colorimetric methods for coolant contamination testing are expensive, labor intensive and prone to yielding false positives. “GC is more reliable than either of these methods,” Hilligoss adds.
“The ASTM D7922 standard for contamination by ethylene glycol, a common coolant base, is currently in the round-robin testing phase,” he says. In this method, phenylboronic acid is added to the sample to derivatize the ethylene glycol and increase its volatility. The volatile derivative separates from the oil matrix and collects in the headspace at the top of the sealed sample container, where it can be removed for injection into the GC instrument. “This method also works with the new propylene glycol antifreezes,” Hilligoss adds.
AAA tow truck. (Photo courtesy of frankieleon. Available at www.flickr.com/photos/armydre2008/.)
OTHER CONTAMINANTS AND DEGRADATION PRODUCTS
The same ICP run that detects wear metals also can pick up evidence for dirt (including abrasive minerals like silica), inorganic components from coolants (sodium, potassium and boron) and metallic lubricant additives.
FTIR and GC pick up organic contaminants that ICP isn’t designed to detect, and FTIR can check for water and soot. “In addition to wear metal testing, POLARIS Laboratories runs tests for viscosity, oxidation/nitration, water, soot, fuel contamination and particle counts,” says Debshaw.
“Some laboratories that run large numbers of acid number and base number (AN and BN) tests use FTIR as an initial screening method to reduce the number of samples that they need to titrate,” says Hilligoss. Instead of using one marker on the FTIR spectrum, these labs use chemometrics methods that use the whole spectrum for the analysis.
LUBRICANT COMPONENTS
In addition to flagging contaminants, oil analysis also helps to monitor components that are supposed to be present in the lubricant. For instance, it can be used to track additive level trends and alert the end-user when it’s time to top off a particular additive. Oil analysis also is used to check for signs that the lubricant is starting to degrade and is due for replacement (
3).
ICP analysis can track trends in metals commonly used in oil additives (organometallics and EP additives, for instance). The unexpected presence of metals in a new oil shipment may indicate that you’ve received the wrong formulation or that batch shipments have become cross contaminated.
FTIR is used to check in-service oils for the depletion of organic additives, and it also indicates whether the oil you’re using is the type you intended to use for a given application. This can head off problems caused by shipping mixups or by topping off a tank with an incompatible oil. FTIR also will indicate whether an oil is approaching the end of its service life by measuring levels of oxidation and nitration.
Hilligoss describes two approaches to FTIR testing. Reference methods (also called differential methods) measure the spectral difference between a new reference oil and an in-service oil sample. One example of this approach is ASTM E2412, which is a standard practice (a list of recommendations), not a method. For this approach, the new oil must be the same oil as the in-service oil. This can be a problem if you don’t know what type of oil you’re using or you topped off the reservoir with another kind of oil. “Reference methods were popular in the 1980s, but now there are so many different formulations that fewer laboratories use this approach,” Hilligoss says.
The other approach is a non-reference method from the Joint Oil Analysis Program (
4). This method measures trends for in-service oil samples compared to a baseline sample of the same oil. “The results from this method are not directly comparable to those from the reference methods,” says Hilligoss. “The ASTM CS96 committee has been working since 2007 on some new FTIR methods for in-service oils.”
EVOLVING FORMULATIONS
Relatively few oil formulations were available in the 1980s. “Now there are more than 10,000 formulations in use,” Hilligoss says, citing a greater variety of base oils, including synthetics. Oils are blended for specific performance applications. “The variety and complexity of additives factor in as well—some oil products are more than 50% additives,” he says.
Debshaw concurred: “We have to be constantly aware” of new formulations. POLARIS Laboratories works with the major oil companies that give them reference samples. He noted, however, that changes in formulations don’t generally require big changes in testing. “Most of the change is on the analysis side,” he says.
Even though instrument manufacturers and contract laboratories are dealing with an ever-increasing variety of lubricant formulations, end-users tend to limit the number of formulations they use. This not only holds costs down, but it decreases the chances of using the wrong oil or topping off an oil reservoir with an oil that is incompatible with the rest of the oil already in service.
AAA’s fleet uses standard semisynthetic lubricants—“Nothing exotic,” says Antaya, “always from the same manufacturer.” They do use different grades of oils for the trucks included in the oil analysis program.
Clifford explained that the Steamship Authority uses bulk deliveries of lubricants from two vendors because the boat engines in the fleet come from two manufacturers. “Limiting the kinds of lubricants they use helps prevent cross contamination or using the wrong type of oil,” he says. Steamship Authority has a dedicated truck for all their oil deliveries to make sure there is no cross contamination with another customer’s oil.
CONTRACT LAB SERVICES
Fleet managers commonly send samples to a contract laboratory rather than maintaining labs in house. “These types of operations are more cost conscious than power generation or military operations,” Debshaw says (
see In-house Oil Testing). It’s more economical to send samples to an accredited commercial lab that can hire the expertise and maintain the instruments. Most of POLARIS Laboratories’ customers send samples on a routine schedule.
A Ford F150 from AAA in Virginia. (Photo courtesy of DiamondBack Truck Covers. Available at www.flickr.com/photos/diamondbackcovers/.)
IN-HOUSE OIL TESTING
“Military oil analysis programs involving deployments in remote locations, and operations that are mission-critical demand results turnaround in as little as one hour,” says Bryan Debshaw, CEO of POLARIS Laboratories®. In these situations, mobile labs are set up on aircraft, ships or land vehicles and they follow the deployments. For an onsite lab, you not only need the equipment, “but you [also] need the person onsite,” he says, who can operate the equipment and interpret the results.
“Industrial operations, power generation facilities and other operations that run 24/7 do some of their testing onsite,” Debshaw notes. Equipment failures can shut down an entire process in these operations, so early warnings are vital for strategic scheduling of maintenance and repairs.
Antaya sends samples to his oil vendor—who submits the samples to a contract lab through the vendor’s customer service program—while Clifford sends his samples directly to the lab. “Vendors and manufacturers also can submit their own samples as a part of their product development or troubleshooting efforts,” says Debshaw.
Contract labs take the responsibility of owning, maintaining and updating the instruments, and their staff members stay current on changes in testing methods and oil formulations. In addition, contract labs use sample automation and electronic databases to cut the time it takes to receive samples, log them in, run the analysis and get the results back to the customer.
A full-service lab will provide trend monitoring, interpretation of the laboratory results and recommendations as a part of their service. “We’re a technical services firm; we take data and convert it to actionable information,” says Debshaw. “Most of our data analysts are Certified Lubrication Specialists™. These analysts take a holistic view of a customer’s operation.” POLARIS Laboratories also has a field service team that goes to customers’ operational sites to give training or address specific issues.
“A sensor will tell me to shut a piece of equipment down but not why or what I need to change,” says Debshaw. “Sensors help with optimization, but a human expert provides a more complete picture of what is going on in any given situation.”
“Most contract labs promise a 24-hour turnaround once they receive a sample,” says Hilligoss and Debshaw. “Large labs run more than 2,000 samples daily and some labs operate multiple shifts around the clock,” says Hilligoss. Debshaw notes that turnaround times are posted daily on POLARIS Laboratories’ Website to alert customers to situations where the lab is experiencing unusually high demand.
POLARIS Laboratories advises its customers on how to reduce the time between sending a sample and getting the results—and the biggest delay is transportation. Even with a 24-hour turnaround time at the lab, Clifford and Antaya report that they get their results back a week to 10 days from when they send the samples out the door.
“Customers usually send samples by trackable commercial carriers,” says Debshaw. They may pay for overnight shipping for critical analyses, but routine samples typically travel by ground shipment. Clifford sends routine monthly samples by mail, but if there is an issue or they need to re-run a test, they ship it overnight.
More than 40% of POLARIS Laboratories’ customers submit sample information forms electronically, which saves them time because they can save information that doesn’t change from month to month and not have to type it in every time. This sample information includes the manufacturer, model and unit number of the vehicle or other equipment where the oil was taken from, the lubricant type and grade and any significant changes since the last sample, like a filter change (
see Sample Compliance).
SAMPLE COMPLIANCE
Debshaw emphasized the importance of customers setting and adhering to a sampling schedule. “If a customer says the equipment should be sampled every 60 days—but they stretch it to 90 or 120—it is
out of compliance,” he explains. In the same way, if customers set a standard for the number of units they will sample—but they only sample 50% of those units—they are out of compliance.
“Being out of compliance increases the risk to the equipment and makes it harder to observe trends in the data,” Debshaw says. “Compliant samples have been pulled on schedule for the equipment, they are drawn from the equipment in a way that minimizes risks of contamination, the forms are completed accurately and they are sent to the laboratory for analysis promptly.”
Customers also get their results back electronically. Antaya’s lab sends him trend graphs, areas of concern and recommendations. The lab flags issues and indicates which sample results are in the acceptable ranges. AAA gets their results by mail and email—and an inventory coordinator handles the paperwork and passes the results along to Antaya.
Clifford gets his results by email, but the lab will fax results to him in high-severity situations. The lab also has a Website where he can check results. Results come in the form of a severity rating: “0 or 1 is good, 2 to 3 is abnormal and 4 is critical,” he says. The lab sends comments as well as the raw numbers:
This sample’s not significantly abnormal but watch it or
Do something immediately! The results report includes results for the four previous analyses so Clifford can track trends that way as well as by using his in-house records.
If Clifford gets an anomalous result that he suspects isn’t related to equipment or oil failure, he sends another sample to the lab for retesting. He noted that occasionally the way a sample is collected will contaminate it. For example, storing oil in a galvanized bucket might cause high zinc levels. Touching a sample with dirty hands or using a contaminated sample tube also would cause high contaminant readings that have nothing to do with the lubricant in the engine.
“The oil vendor’s rep looks at lab results for samples sent through his office,” Clifford says. The vendor’s rep can recommend changes in the lubricant grade or formulation to improve performance or alert the customer to a bad batch of oil or the wrong oil in a bulk delivery.
PROBLEMS SOLVED
“No one analysis tells you the whole story; interpretation takes skill,” says Hilligoss. Skilled interpretation of the laboratory results can pay off in ways beyond the obvious early warnings for failing parts and oils that are reaching the end of their service life.
Clifford explained that he doesn’t use the Steamship Authority’s oil analysis program to get a longer lifetime out of the oil. In fact, he and his staff sometimes change it more often than the manufacturer’s recommendation if the test results indicate that this is necessary. “It’s more effective to change the oil before it starts building up contaminants and starting to degrade than to save a little money by running it longer,” he says. He added that the tests let them know when they are doing something right so they can keep it up: changing filters or cleaning tanks more often, for example.
Oil analysis also can aid in troubleshooting a problem. Clifford told of a situation in 2015 where an oil sample from a reduction gear on one of the ferries had a high lead count. Lead is a wear metal, probably from a bearing or a gear tooth that was starting to fail. He sent his lab results to the equipment manufacturer, who was able to tell him the specific gear on the specific shaft that was causing the problem. The manufacturer indicated that it was important to act immediately. The early detection gave Clifford and his coworkers time to order the part and schedule a repair session between scheduled trips, so they were able to rectify the problem without losing any operation time. “This was a real cost saver because it takes 12-26 weeks to get a new reduction gear on order,” Clifford says. “If the gear had failed unexpectedly, they could have lost months of operating time.”
Clifford says that if he sees the same problem on three different boats, all using the same oil, it could be a sign of something amiss in one of their oil deliveries. “It’s not likely to see the same mechanical failure in several boats all at once, so it’s probably something in the oil,” he says. He told of an instance when they were getting high zinc readings for one batch of oil, but his operations use zinc-free oil. The vendor took care of replacing the oil in the boats with the proper formulation.
“AAA’s trucks spend a lot of time idling between service calls,” Antaya says. They don’t go back to the garage until the end of the day and drivers often sit inside the cab with the heater or air conditioning running while they wait for the next call. Antaya says that sometimes he can tell who’s driving a truck by the results of the oil tests. If a truck is showing abnormal wear even though it hasn’t made a lot of runs over rough terrain or during severe weather, he can make recommendations on driving practices that reduce wear and tear on the vehicle.
What should an operations manager know before setting up an oil analysis program for the first time? To get the most value from an oil analysis program, Debshaw says, “Make sure that your samples are compliant and act on the critical samples. Find ways to take action earlier and focus your time and attention on improvement.”
In the long run, an oil analysis program not only alerts you to impending crises—it helps you avoid crises in the first place and lets you make a good operation even better.
REFERENCES
1.
Hilligoss, D.R. (Oct. 4, 2016), “Lubricant analysis: The value of oil condition monitoring and PerkinElmer’s continuing commitment.” Webinar available
here.
2.
McGuire, N. (2014), “Oil analysis: Keeping military systems running smoothly,” TLT,
70 (7), pp. 34-43.
3.
Wooton Consulting. “Using oil analysis as a tool in fluid degradation RCA.” Available
here.
4.
PerkinElmer. (2002), “The JOAP method for oil condition monitoring using spectrum oilexpress. Available
here.
Nancy McGuire is a free-lance writer based in Silver Spring, Md. You can contact her at nmcguire@wordchemist.com.