Special Report: Antioxidants: Key additives enable lubricants to operate under more severe conditions
Dr. Neil Canter, Contributing Editor | TLT Tech Beat September 2016
But maximizing their performance depends on formulating the proper lubricant and monitoring it during use.
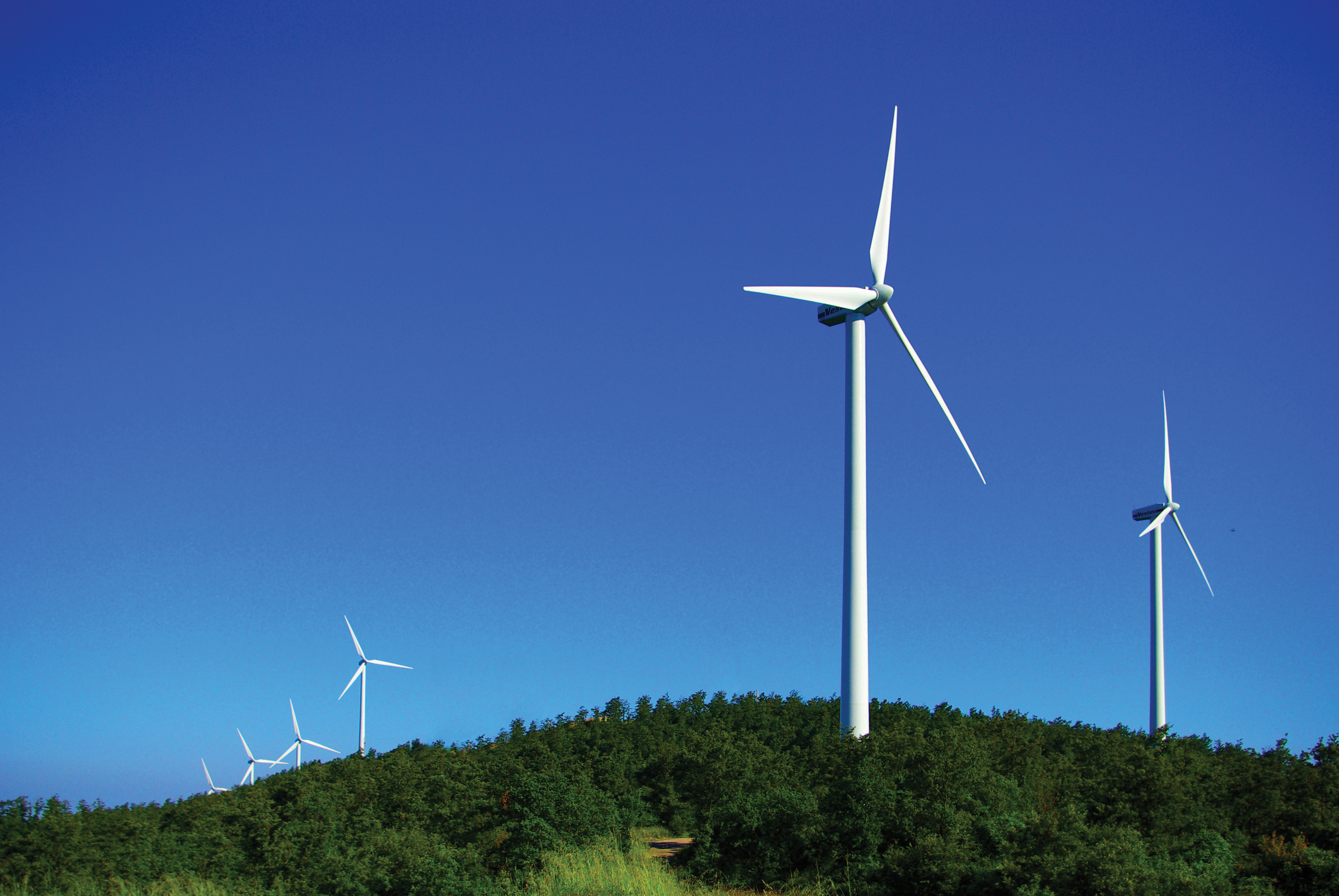
© Can Stock Photo Inc. / pmm
KEY CONCEPTS
•
Three types of antioxidants are used to protect industrial lubricants from external factors that will result in the generation of free radicals.
•
Multiple types of antioxidants are recommended for use in lubricant applications because they complement each other.
•
Evaluating the effectiveness of antioxidants used in a specific lubricant requires a series of laboratory tests followed by an assessment of field performance.
DEMANDS PLACED ON LUBRICANTS TO PROVIDE SUPERIOR PERFORMANCE under more stressful operating environments over longer periods of time are increasing. This means that the function that antioxidants perform to protect lubricants is continuing to increase in importance.
With the implementation of two new engine oil specifications, as was discussed in a previous TLT article (
1), antioxidants will continue to play an important role in automotive lubricants. But antioxidants also are an important additive used in industrial lubricants.
This article furnishes an update on the use of antioxidants in industrial lubricants that includes discussions about critical lubricant applications, how to select antioxidants, assessing antioxidant performance and future trends.
Input on developments with antioxidants has been obtained from representatives at the following companies: BASF, Chemtura, Fluitec Industries, King Industries, Polnox, Rhein Chemie and Vanderbilt Chemical.
FUNCTION OF ANTIOXIDANTS
Oxidation is a multistep process involving a three-step radical process that if left unchecked will eventually lead to the total breakdown of the components in the lubricant. In the first step of the radical process, known as initiation, an external factor such as heat, severe pressure or the presence of a metal will trigger the formation of a free radical (or unpaired electron) that is derived from one of the organic components found in the lubricant. Either a bond inside the organic species between two atoms is broken to form the radical or an electron is subtracted from a molecule by an oxidized metal.
The free radical formed is a highly reactive species that can react with oxygen to form a hydroperoxide radical in the second step of the radical process. This is known as propagation because the additional radicals formed accelerate the decomposition of the lubricant. The hydroperoxide radicals formed engage in a third step, known as the multiplying step, leading to the formation of additional radicals.
Dr. Michael König, senior manager application for Rhein Chemie Rheinau GmbH in Mannheim, Germany, says, “A second aspect of propagation is that the peroxides formed can further react to form additional radicals in a branching and multiplying process. By continuous breaking of bonds, smaller or even volatile molecules are generated.” A schematic showing initiation, propagation and multiplying is illustrated in Figure 1.
Figure 1. The three-step process describing oxidation involves the initiation, propagation and multiplication of free radicals. (Figure courtesy of Rhein Chemie Rheinau GmbH.)
The only termination step of the radical process is the recombination step where two of the free radicals will combine to form a stable compound in a reaction that essentially removes free radicals from the lubricant as shown in Figure 2.
The termination step is only effective in stopping the process if no more free radicals are formed during initiation. For this to occur, the external stresses that are causing the lubricant to oxidize must stop.
Ultimately, König points out that the final products of oxidation are carbon dioxide and water, as shown in Figure 2.
Figure 2. Termination of oxidation takes place through recombination of two free radicals as shown in the top reaction. The ultimate oxidation products as shown in the bottom reaction are carbon dioxide and water. (Figure courtesy of Rhein Chemie Rheinau GmbH.)
Antioxidants interfere with oxidation through reacting with free radicals to form stable species. STLE-member Vince Gatto, research director for Vanderbilt Chemicals LLC in Norwalk, Conn., says, “The two major classes of antioxidants used in industrial lubricant applications are aromatic amines and hindered phenols. They are classified as primary antioxidants because they function to scavenge peroxy radicals in the oil, converting the peroxy radicals into more stable hydroperoxides. Quite frequently the combination of these two classes are used due to the known stabilization synergy that results (basically aromatic amines antioxidants at high temperatures while hindered phenolics are more effective at lower temperatures).”
STLE-member Cyril Migdal, R&D director for Chemtura Corp. in Naugatuck, Conn., provides specific examples of aromatic amines and hindered phenolics. He says, “The most widely used aromatic amine are the alkylated diphenylamines (ADPAs). Another radical scavenger aromatic amine type used is phenyl-alpha-naphthyl amine (PANA) or its alkylated version, alkyl phenyl-alpha-naphthyl amine (APANA). The most widely used hindered phenolic is 2,6-di-t-butyl-p-cresol, commonly known as BHT. Other examples of hindered phenolics with the benefit of lower volatility than BHT are 3,5-di-t-butyl-4-hydroxy-hydrocinnamic acid, C7-C9 branched alkyl ester and 4,4’-methylenebis (2,6-di-tertiary-butylphenol).”
Secondary antioxidants are a second class that decompose less stable hydroperoxide radicals to more stable alcohols. Migdal says, “Examples of secondary antioxidants are zinc dialkyldithiophosphates (ZDDPs), phosphites, sulfides and thiocarbamates.”
Gatto believes that ashless dithiocarbamates provide some additional benefits. He says, “Ashless dithiocarbamates are an example of a supplemental antioxidant that are used in addition to aromatic amine and hindered phenolics to enhance certain specific properties of the finished industrial fluid. They are synergistic with the aromatic amine antioxidants and can enhance general oxidation control but in addition also can deliver some antiwear benefits.”
A third type of antioxidant is tertiary antioxidants. König says, “Tertiary antioxidants inhibit the formation of catalysts used in the initiation reaction (
see Figure 1). They typically have the function of acting as ferrous and non-ferrous metal inhibitors.”
An example of a tertiary antioxidant is an alkylated diphenylamine derivative of tolutriazole. Gatto says, “Alkylated diphenylamine derivatives of tolutriazole function as both primary antioxidants (scavenging peroxy radicals) and corrosion inhibitors (passivating metal surfaces). They also are synergistic with ashless dithiocarbamates.”
CRITICAL LUBRICANT APPLICATIONS
STLE Past President Robert Baker, technical sales & marketing advisor for King Industries in Norwalk, Conn., says, “Very few applications (such as lost lubricants and once through) do not benefit from the ability of antioxidants to extend the functional life of the lubricant and prevent premature failures. There is economic incentive in most cases with critical applications being those where the cost of downtime to change out the lubricant is significantly greater than the cost of the lubricant itself. Perhaps the most current example may be the wind turbine.”
Galen Greene, technical service manager for BASF Corp. in Tarrytown, N.Y., agrees and says, “Almost every lubricant needs antioxidants! They are used across the spectrum of industrial lubricants, from relatively low-temperature applications such as hydraulic oils to more demanding applications where the lubricant is exposed to higher temperatures such as gas turbine oils and compressor oils.”
STLE-member Jo Ameye, general manager Europe for Fluitec International in Antwerp, Belgium, says, “Antioxidants are needed in any application where the fluid’s primary mode of failure is oxidation. Examples include turbine, compressor and rotating equipment (rust and oxidation formulations) and the new generation of synthetic gear oils.”
STLE-member Ashok Cholli, president and chief technology officer of Polnox Corp. in Lowell, Mass., says, “Lubricant products essentially comprise approximately 85%-95% base stock oil that basically consists of organic hydrocarbon molecules derived from petroleum, synthetic or biobased raw materials. Antioxidants are an essential additive for all applications, and their use depends upon the nature and quality of oil and the stability requirements of the end-use application. Lubricants containing more stable oils (such as synthetic base stocks) may need only a very low level of antioxidant, while less oxidatively stable vegetable oils may require higher treat levels.”
König says, “All industrial lubricants formulated for long lifetime operations and exposed to heat and/or air require antioxidants.”
Migdal lists criteria involving the application, lubricant type and application where antioxidants are needed. He says, “The most critical antioxidant needs are applications where the sustained operating temperature is > 40 C, the base stock is of poor quality (high in aromatics and unsaturates), metal contamination in the lubricant is possible and applications that are intended to be ‘filled for life.’”
Gatto discusses operating conditions that place a large demand on antioxidants. He says, “The stress applied to antioxidants is most severe in applications such as high temperature turbines and compressors, where the lubricant is exposed to severe environments involving high temperatures, cold spots and metal contamination and where water places a large demand on antioxidants. Even more severe conditions are encountered when temperatures in a specific application are highly variable. This is due to the potential for water buildup at low temperatures that can lead to acid buildup and corrosion which both accelerate oxidation.”
ANTIOXIDANT SELECTION
In selection of antioxidants, it is important to use a mixture of aromatic amines and hindered phenolics to afford the broadest temperature coverage. Migdal says, “At temperatures less than 120 C, hindered phenolic antioxidants perform very well and are predominately used, however at temperatures greater than 120 C, aromatic amines such as alkylated diphenylamines are more effective than hindered phenolics.”
The need for multiple antioxidants is demonstrated in Figure 3 that shows the evaluation of turbine oils in the Turbine Oil Oxidation Stability Test (TOST—ASTM D943) and in Figure 4 that shows the same samples examined using the Rotating Pressure Vessel Oxidation Test (RPVOT—ASTM D2272). These studies demonstrate how combining an alkylated diphenylamine with a hindered phenolic leads to better oxidation protection than either of the two antioxidants used by themselves.
Figure 3. Better results in delaying the onset of oxidation are achieved with multiple antioxidants such as the combination of an alkylated diphenylamine (ADPA) and hindered phenolic (HP) in the TOST. (Figure courtesy of Chemtura Corp.)
Figure 4. The ADPA, HP antioxidant combination also shows better results in the RPVOT. (Figure courtesy of Chemtura Corp.)
Gatto indicates that combinations of antioxidants represent the best approach for lubricant formulators to use in order to ensure that the lubricant will perform up to its capability in a particular application. He says, “The formulator should use a combination of hindered phenolics and aromatic amines plus one or more supplemental antioxidants. This strategy takes advantage of the performance synergy between antioxidant classes and generally allows for the lowest cost formulation. Formulators should use hindered phenolics in combination with aromatic amines plus supplemental ashless dithiocarbamates and supplemental alkylated diphenylamine derivatives of tolutriazole. The ratio among antioxidants is important and needs to be worked out for each application.”
Gatto also gives guidelines for how hindered phenolics and aromatic amines should be used. He adds, “In applications where sludge or deposits is a problem, hindered phenolics are favored. In high temperature applications where sludge and deposits are less of an issue, aromatic amines are favored.”
Baker is in agreement that multiple antioxidants should be used. He says, “Even in applications not considered severe, a mix of chemistries may be more cost effective.” Figure 5 shows an example of data compiled by formulating an ISO VG 46 Group I base oil with antioxidants. Better performance results are achieved when the RPVOT and TOST are run using formulations with two antioxidants, as well as two metal catalyst passivators.”
Figure 5. Formulating with two antioxidants and two metal catalyst passivators leads to superior RPVOT and TOST performance results. (Figure courtesy of King Industries.)
Baker also points out an important factor regarding the heat/temperature of the application. He says, “Oxidation is a typical reaction for which the rate doubles approximately every 10 C. Antioxidants are sacrificial and are consumed as they perform their function, so there will be a half-life decrease for every 10 C increase in the average operating temperature of the lubricant.”
Greene feels that antioxidant selection needs to be done by developing a test program that correlates well with a specific application. He says, “Once a field-correlated test program has been selected and validated, antioxidants can be selected and validated based on base fluid solubility, regulatory requirements and performance.”
Making a careful selection of antioxidants when formulating can lead to beneficial results as shown in the TOST study in Figure 6. Greene says, “In this case a hydraulic fluid formulated with an ashless additive package can be supplemented with a mixture of specific aromatic amine antioxidants. Since the right antioxidant system is in place, a lubricant formulator can dial in the desired TOST performance up to very high levels without compromising the fluid’s sludging tendency while keeping a very low additive treat rate.”
Figure 6. Supplementing a hydraulic fluid with a mixture of specific aromatic amines enables the antioxidation performance to be tailored to meet particular operating conditions. (Figure courtesy of BASF Corp.)
Cholli lists three key considerations that the lubricant formulator must consider in selecting an antioxidant for a specific lubricant application. He says, “The formulator must know the nature of the base stock and whether it is derived from petroleum, synthetic or a biobased raw material. Operating temperature that the lubricant will be subjected to must be evaluated as there are different antioxidants optimized for low-temperature or high-temperature performance, and cost-performance requirements must be considered based on the price of the antioxidant and its treat rate.”
König feels that one other factor that a formulator must be aware of is whether the specific antioxidant meets the regulator requirements of the specific country or region. Migdal points out that there is an additional step the formulator must take if the antioxidant is needed for a food-grade lubricant. He says, “The formulator must select an antioxidant for a food-grade application that is registered under a certification such as USDA’s HX-1 category.”
BIOLUBRICANTS
One specific class of base stocks that is particularly troublesome from the oxidation standpoint are biolubricants. Cholli explains, “In contrast to petroleum-based lubricants, biolubricants consist of esters of mixed fatty acids (i.e., saturated, monosaturated and polyunsaturated) that contain significant levels of unsaturated components particularly those that are polyunsaturated. The level of unsaturated components is known to correlate with increasing oxidative instability.”
Cholli maintains that the performance of conventional antioxidants is relatively ineffective when used with biolubricants. He says, “The most serious issues in using conventional antioxidants are the lack of sufficient reactivity to efficiently scavenge the highly reactive free radical intermediates that propagate oxidation chains in polyunsaturated oils and the sacrificial nature of conventional existing antioxidants that makes them incapable of functioning as antioxidants once they scavenge a free radical.”
An alternative antioxidant technology known as DT-mPM has been found to be a better option for lubricant formulators. Cholli says, “This technology exploits a unique regenerative mechanism to improve the antioxidant performance by multiple times to provide a significant improvement in efficacy over conventional products.”
Performance data showing the effectiveness of DT-mPM versus a commercial antioxidant are shown in Figure 7. The two antioxidants are each added separately at a 2% treat rate to canola oil and metal catalysts (iron and copper) and their effectiveness compared using the Pressure Differential Scanning Calorimetry (PDSC) test procedure, ASTM D6186. Both samples are heated at 135 C for seven days and the oxidation induction time (OIT) determined on a daily basis and charted in Figure 7.
Cholli says, “Subjecting the canola oil containing DT-mPM to pro-oxidant metal catalysts and a temperature of 135 C for four days leads to an identical OIT compared to the canola oil sample after it is just blended with 2% of a commercial antioxidant (
see arrow in Figure 7). The DT-mPM antioxidant provides strong performance under severe conditions compared to a commercial antioxidant that has not even been subjected to the harsh experimental conditions.”
Figure 7 also reveals that even after seven days of exposure of heat and metal catalysts to the oil, the DT-mPM antioxidant outperforms and maintains its superior efficacy compared to the commercial antioxidant, according to Cholli.
Figure 7. A PDSC study shows that an alternative antioxidant technology known as DT-mPM exhibits superior performance in canola oil versus a commercial antioxidant. (Figure courtesy of Polnox Corp.)
Baker points out that the type of base stock used in the biolubricant is critical in determining whether an antioxidant will be effective. He says, “Natural oils simply cannot be inhibited to withstand any significant heat and are restricted to more or less ambient applications. The life of formulated conventional and many synthetic fluids can be compared using the TOST in the thousands of hours; however, inhibited natural oils are at best in the hundreds of hours and biodegradable synthetics can only be compared without the addition of water.”
Figure 8 compares the performance of petroleum, natural oil and synthetic ester base stocks with an appropriate treat rate of the same antioxidant blend in the TOST and the RPVOT. The natural oils display inferior oxidation characteristics compared to the petroleum base oils and the saturated biodegradable, synthetic ester.
Figure 8. The challenge in protecting natural oil-based lubricants from oxidizing as compared to other base stocks is shown in this RPVOT and TOST study. (Figure courtesy of King Industries.)
Baker adds, “For more demanding applications that require or desire biolubricants, it is necessary to move toward synthetic esters and utilize the benefit of antioxidant blends similar to those that have been demonstrated in petroleum base stocks.”
König believes that hydrolysis of biolubricants is as important as oxidation. He says, “Hydrolysis products of esters promote the radical formation and aging of esters. This means that esters need as much protection from hydrolysis as from oxidation and aging of esters by radical reactions must be distinguished from aging by hydrolysis. One challenge faced by lubricant formulators is the main types of antioxidants are not readily biodegradable, so care must be taken by lubricant formulators in developing biolubricants that only contain antioxidants that are non-bioaccumulative and exhibit low aquatic toxicity.”
Greene is in agreement and states that formulating biolubricants is constrained by regional specifications. He says, “Specifications for biolubricants in specific global regions (e.g., the European Eco-Label) often limit which antioxidants can be used and the treat rate that may be used.”
Migdal offers suggestions for what antioxidants to use in formulating unsaturated biolubricants. He says, “In general, higher doses of antioxidant are required and even then biolubricants will not be as oxidatively stable as low unsaturated counterparts. Antioxidants such as PANA and APANA generally work well in vegetable oils and other ester base stocks whether bio-derived or not.”
Gatto also feels that combinations of aromatic amine-based antioxidants are useful in working with biolubricants. He says, “Alkylated diphenylamines should be used with alkylated phenyl-alpha-naphthylamines and a supplemental antioxidant such as the ashless dithiocarbamates.”
DIFFERENTIATE ANTIOXIDANT PERFORMANCE
The best approach to differentiate antioxidant performance is through running a series of laboratory tests (recognizing that no bench test simulates all the possible operating conditions to be encountered). Details on the available tests can be found in the ASTM Fuels and Lubricants Handbook (
2). Baker says, “Four of the most common fluid lubricant oxidation tests are the TOST, RPVOT, PDSC and the Cincinnati Milacron ‘thermal stability’ test” (
see Table 1). It should be noted that automotive engine oils are typically confronted with conditions not common to most industrial applications and industrial bench tests are generally not considered predictive of engine performance.”
Table 1. Table courtesy of King Industries.
Gatto offers his thoughts for evaluating antioxidants. He says, “My preference is to use one bulk oil oxidation test (dry TOST or Indiana Stirring Oxidation Test (ISOT)), one thin film oxidation test (PDSC) a varnish or sludge test (Cincinnati Milacron Thermal Stability Test or 1,000 hour TOST) and a deposit test (Panel Coker). The RPVOT is used by the lubricants industry as an antioxidant screener for turbine and compressor oils, although the test was not designed for that purpose.”
Besides the PDSC, Ameye offers other tests for evaluation of antioxidants in order to differentiate their performance. He says, “Linear Sweep Voltammetry (LSV) is used to measure the content of aromatic amines and hindered phenolics in turbine oils through the ASTM D6971 and D6810 test methods, respectively. FT-IR measures the concentration of hindered phenolics in lubricants and high-pressure liquid chromatography/gas chromatography are two methods that also can be used to measure the concentration of antioxidants in lubricants.”
Migdal feels that a series of tests can be used to properly differentiate antioxidant performance. He says, “The PDSC can be tailored for use under different pressures, temperatures, atmospheres and catalysts. The RPVOT is used to simulate an environment of 150 C in applications where water may be present. The TOST is used in steam turbines, where water is present and is run at a temperature (95 C) that simulates the low temperature of this application. For gas turbines, a relatively new test method known as the Determination of the Oxidation Stability and Insolubles Formation of Inhibited Turbine Oils at 120 C was developed and is known as ASTM D7873.”
Migdal continues by stressing that statistical experimental design (SED) methodology should be used to maximize the information obtained from a series of environmental stress tests used to evaluate antioxidant performance. He says, “SED is the best technique to identify synergistic or antagonistic effects between additives. Variables to consider when setting up an SED to evaluate antioxidants include: additive concentration, end-use temperature range, presence/type of metal ions, oxidation in bulk or thin-film and whether to include water.”
Greene indicates that field performance will drive customer perception about the value of the lubricant and counsels that test programs should be tailored to evaluate the performance parameters that matter. He says, “Combinations of parameters such as viscosity control, acid number control, sludge and deposit control must be prioritized with regard to the specific application. Many well-understood, industry-standard bench-and-rig tests are available for industrial lubricants and OEM specifications can offer a guide to which tests are appropriate for which applications.”
Cholli prefers to use the PDSC to assess antioxidant performance. He says, “The PDSC is a direct method that detects the heat generated as a result of exothermic processes that are occurring due to the reaction of heat and oxygen with the lubricant oil molecules in auto-oxidation reactions. It is simple to correlate the role of antioxidants to retard such exothermic reactions by measuring the time required to go to the auto-oxidation stage under the isothermal conditions of the test. The PDSC also is highly accurate and reproducible, requires only a small amount of sample and more importantly does not take a long time to run.”
König cautions that evaluation of antioxidants may actually take a long period of time. He says, “Sometimes, it is necessary to run long-term tests to cover all aspects of complex antioxidant mechanisms.”
ADDITIVES THAT COMPLEMENT ANTIOXIDANTS
Secondary and tertiary antioxidants work to supplement the performance of primary antioxidants. Greene says, “Most machines are made of metals that can play a role in accelerating oxidation by catalyzing the hemolysis of O-O bonds in the peroxides that inevitably form in a lubricant. Minimizing the catalytic activity of metals through the use of a robust corrosion inhibitor and metal deactivator system is an important element in formulation of an industrial lubricant with a long service life.”
Migdal points out that there is a second class of metal deactivators besides the triazoles that are effective in preventing metal ions (i.e., Fe
+2, Cu
+2) from catalyzing oxidation of the lubricant. He says, “The second class is the chelating type that can attach themselves to metal ions in solution keeping them from catalyzing the oxidation process. An example of a chelator is N,N-disalicylidene-1,2-propanediamine.”
Gatto feels that sulfur- and phosphorus-free molybdate esters act synergistically with antioxidants. He explains, “Both of these additive types are not very effective antioxidants, but they synergize alkylated diphenylamines and sulfurized compounds. This approach has been used in engine oils but has not been tried as much in industrial lubricants. One reason for their use in engine oils is that molybdate ester also are synergistic with zinc dialkyldithiophosphates.”
EXTEND OPERATING LIFE OF AN OXIDIZED LUBRICANT
All of the respondents caution that once oxidation of a lubricant starts, it will continue to accelerate, in many cases exponentially, making it difficult to stop and leading eventually to the need to replace the lubricant. A few suggestions are offered below.
Greene says, “One approach is to top treat the lubricant with an antioxidant, but this can lead to unpredictable results and is generally unadvisable. This is because the antioxidant system is carefully balanced, and it is highly possible an end-user would upset this balance leading to worse performance.”
König agrees that addition of antioxidants may be helpful if the lubricant system has not reached a critical situation. He says, “Radical scavengers and/or peroxide decomposers can be added in an attempt to slow down the oxidation process.”
Ameye says, “Two steps to take are to remove oxidation and degradation products by chemical filtration to prevent further base-oil degradation and to replenish with fresh antioxidants.”
Cholli says, “Where oil contamination is limited, it may be possible to consider replenishing the lubricant system with fresh oil at regular intervals to maintain performance.”
Baker suggests the use of another additive type to minimize the presence of insoluble species if the lubricant system has not reached the point of no return. He says, “Addition of a dispersant may be helpful in reducing the presence of sludge or varnish formation that can result from oxidation.”
Gatto claims that use of a highly refined base oil gives the lubricant end-user more of a chance to stabilize the situation. He says, “If a lubricant based on a Group I base oil has started degrading, then not much can be done. But lubricants formulated with Group II, III and IV base stocks have a very high oxidation stability and usually do not degrade to a large extent in the presence of antioxidants. Monitoring antioxidant depletion in the system can be used to find the optimum point where antioxidant replenishment is feasible. This is usually at a stage where between 50% and 75% of the antioxidant is depleted.”
Ultimately, Gatto considers all of these approaches to extend the operating life of the oxidized lubricant to be operationally challenging and technically complex. “Some are only temporary measures requiring the lubricant to eventually be changed to avoid equipment failure,” he says.
Gatto also indicates that a new antioxidant shows good performance in initial testing and can be used in a broad range of base stocks including Group IV oils and PAG-based fluids. He says, “This antioxidant has a key benefit of boosting fluid resistance to oxidation without compromising sludge control. Normally this is very difficult to do.”
Figure 9 shows RPVOT and sludge control data prepared from a turbine oil formulated with a Group II base oil and 0.8% of a turbine oil package containing antioxidant, corrosion inhibitor, rust inhibitor and diluent oil in the listed percentages. Introduction of 0.2% of the new antioxidant as a top treat boosts the RPVOT while lowering the milligrams of sludge to an acceptable level as evaluated using ASTM D2070, a method that is done to evaluate thermal stability of industrial lubricants.
Figure 9. Addition of the proper top treat can boost antioxidant performance as shown in the evaluation of a turbine oil using the TOST and a thermal stability test. (Figure courtesy of Vanderbilt Chemicals LLC.)
Gatto adds, “This work demonstrates that a top treat can work if the correct formulation approach is used.”
ASSESSMENT OF CURRENT ANTIOXIDANTS
The increasingly stressful operating conditions for lubricants means that there is need to assess the performance characteristics of the currently available antioxidants. Ameye says, “A better synergy needs to be achieved between different types of aromatic amines and hindered phenolics. Better antioxidant solutions are needed on the newer generation of steam and gas turbines and radial/centrifugal compressors because they tend to use smaller oil reservoir volumes that have less dwell time leading to additional oxidative stress.”
One other area where improvement is needed is in hydraulic fluids. Ameye says, “More hydraulic oils need to be enhanced with primary antioxidants such as aromatic amines and hindered phenolics instead of relying on secondary antioxidants.”
Baker points out that a big challenge for the lubricants industry is the lack of new antioxidants to work with in new and existing products. He says, “Registrations of new antioxidant candidates have become more difficult and expensive, which is virtually precluding the development of new chemistries. The continuing challenge is to seek cost-effective synergies of existing chemistries.”
FUTURE TRENDS
Future trends revolve around the continuing use of more highly refined petroleum oil base stocks, synthetic base stocks and the need to find ways to keep lubricants based on these materials operating effectively over longer lifetimes. “Higher refined and modern base oils promise a longer lifetime,” says König, “while end-user requirements for oxidative stability of lubricants increase. The required stabilities—even in higher refined and modern base oils—can only be achieved by use of optimized antioxidant and/or industrial oil packages.”
Cholli emphasizes that biobased lubricant use will continue to grow as will the challenges associated in using them. He says, “Increased environmental awareness in society to minimize the consequences of pollution coupled with increased regulatory requirements are expected to drive the development of lubricant additives that are non-toxic and environmentally friendly. The trend also may include using raw materials from renewable resources (biobased) in manufacturing of additives in order to lessen dependence on the petroleum-based chemicals that dominate the world today.”
Migdal points out that the lubricants industry trend away from Group I base oils will leave a need for integrating a specific antioxidant type into future formulations prepared with more highly refined base oils. He says, “Blending of hydrocarbon synthetic-based lubricants may require an additional antioxidant because the ‘natural’ antioxidant present in Group I base oils is removed in processing more highly refined base oils. The antioxidant that lubricant formulators may need to add is generally the secondary type or hydroperoxide decomposers.”
Baker sees that maximizing lubricant performance in the future will only be part of an overall strategy by the end-user to maximize the performance of the system. He says, “Increasing attention is being paid to a system approach to equipment operation and maintenance, such that the benefit of prolonging the functional life of the lubricant to the system as a whole is recognized (versus the cost of the lubricant alone).”
Greene focuses on the greater demands that end-users are facing, which puts more pressure on antioxidants to effectively perform. He says, “Customers continue to expect lower cost of ownership including longer service intervals and higher energy efficiency. This means longer lubricant life at higher operating temperatures. More and higher performing antioxidants will be needed to meet these expectations.”
Gatto specifically discusses the opportunity to conduct proper condition monitoring of compressor and turbine oils to extend lubricant performance. He says, “An enormous opportunity exists for extending the useful life of certain compressor and turbine oils via antioxidant replenishment. The technology already exists to do this with the key being proper condition monitoring of the service lubricant and having the right systems in place for removing contaminants that build up over time. Using the right combination of antioxidants that can be easily monitored in the turbine oil and easily replenished at the appropriate time is essential. This can potentially provide enormous cost savings to the power generation industry if developed properly.”
Gatto continues, “Another opportunity exists for higher temperature, more thermally stable antioxidants providing superior deposit control. Such technology already exists for aviation lubricants but is exceedingly expensive. Cost reduction for this technology becomes a challenge because it may require the development of a new molecule that is costly and can take many years.”
Ameye points out that longer lubricant life will lead to reduced maintenance costs and improved reliability in lubricant applications. He says, “Higher use of antioxidants in insulating/transformer fluids is needed as the lubricants industry has switched from naphthenic to paraffinic base oils.”
It is clear that antioxidants will continue to be an important additive type that is required to protect lubricants from the more demanding operating conditions they face on a daily basis. Finding better ways to use antioxidants in specific combinations for particular applications and working to better monitor lubricant systems are two ways that the industry will be able to maximize their value in the future.
REFERENCES
1.
Canter, N. (2015), “GF-6, PC-11 and dexos1™: New engine oil specifications mean new additive challenges,” TLT,
71 (9), pp. 10-24.
2.
Totten, G., Ed. (2003), “Fuels and lubricants handbook: Technology, properties, performance and testing,”
ASTM International.
Neil Canter heads his own consulting company, Chemical Solutions, in Willow Grove, Pa. Ideas for Tech Beat items can be sent to him at neilcanter@comcast.net.