Complexity in ISFA (in-service fluid analysis): Part XXVIII
Jack Poley | TLT On Condition Monitoring September 2016
Mining for dollars Part IV—making it easier on the intelligent agent.
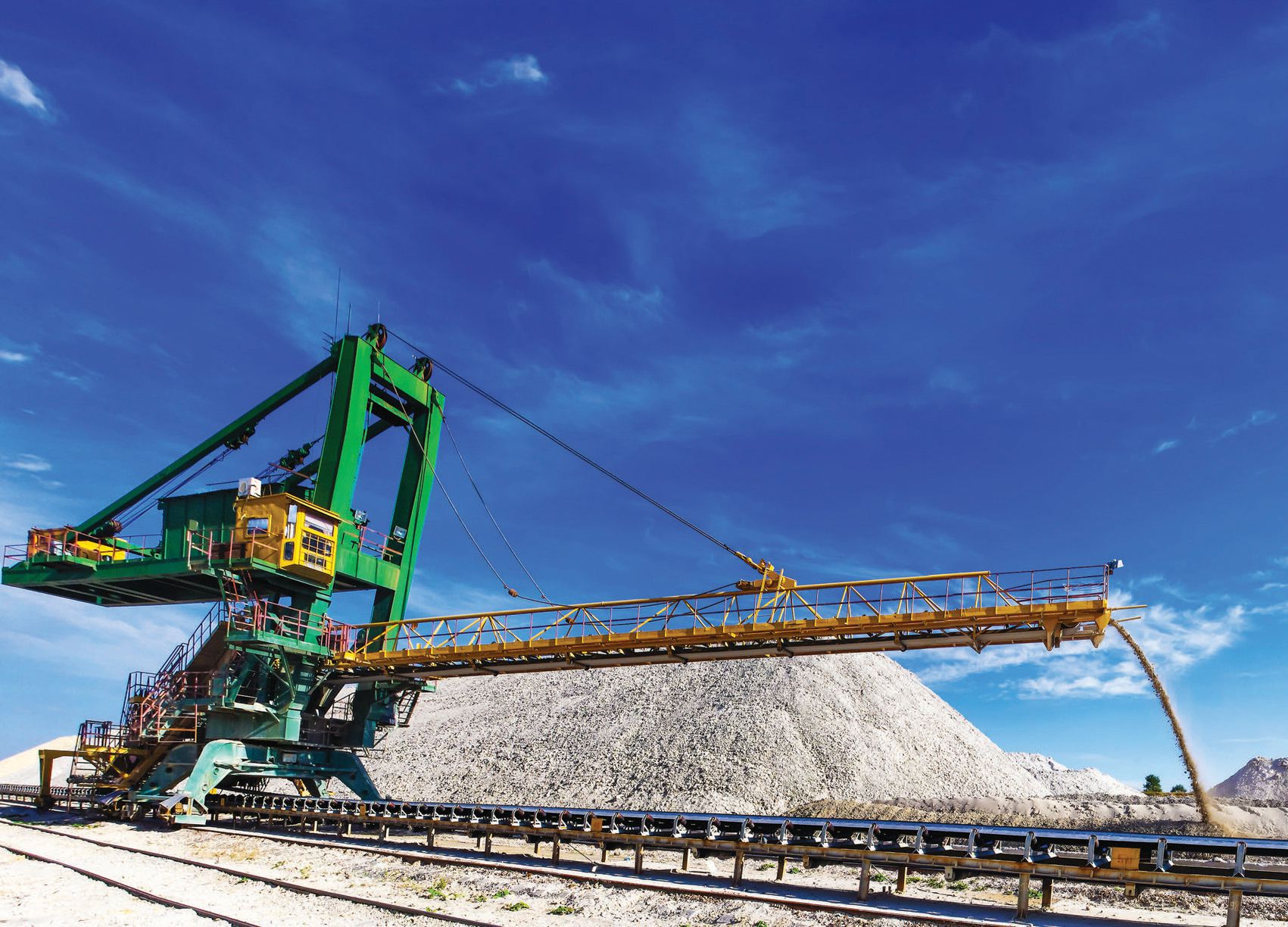
© Can Stock Photo Inc. / Wingedbull
IF YOU'VE BEEN FOLLOWING THE THREE PREVIOUS COLUMNS, here are some takeaways:
Swallow the database pill.
•
If you are beginning an ISFA program for the first time (at your current company), this is your first and best chance to get the database properly sanitized and prepped to make your program the best it can be. If you’re going to use an intelligent agent (IA) in the process, it’s essential.
•
Corollary: If you’ve been into your program for a number of months or years, you can still improve things going forward.
Be a part of the solution—participate in all respects.
•
As I’ve admonished before, ISFA programs do not run themselves. Neither is it your “tester’s responsibility” to make it run for you. The tester (lab) is responsible for furnishing accurate data and, if also supplying commentary, a highly competent, appropriate advisory. Nevertheless the tester is leading you to the water. You have to decide to drink it.
•
You are likely—despite good intentions—not supplying useful, accurate
feedback to the evaluator, so that he or she can reinforce what’s right and fix what’s wrong with the commentary supplied in specific instances. This is gold, otherwise known as
money on the table. Pick it up. Communicate with the evaluator. Again, if an IA is in use, this is where the added benefits begin.
•
Read the previous two bullets regularly. Apply them for best results.
Let’s say you have good intentions and understand the necessity of cleaning up your database to set the table for maximum uptime (ROI). Then let’s discuss the
solution aspect more thoroughly. It really is the last rivet in maximizing ROI from your program.
I’ve been at oil analysis for more than 50 years. Everyone seems to know what
oil analysis is all about, once mentioned, but I wonder if it’s
really understood, in terms of priorities.
Many first-time ISFA users are attracted to the notion of safely extended lube and filter changes. Good idea, but that would be reason No. 2 to investigate the lube. In recent times, more ISFA users have come to understand that it is the machine, not the lube, which needs to be protected. Accordingly the major metals—Fe, Al, Cu, Pb + Si (dirt indicator)—are the most important indicators of wear and frequent cause (e.g., dirt). When liquid-cooled reciprocating engines, some reciprocating compressors and automatic transmissions are being monitored, coolant becomes another factor that frequently causes major wear problems, and there are telltale metals, particularly potassium (K)* from many coolant additive packages, that indicate coolant seepage at sensitive levels well in time to avert a catastrophe. Further with diesels, fuel dilution is yet another contaminant, indicative of pump, fuel line or injector issues. All these types of problems leave clues in the lube that are much more important as signals (root cause) for machinery maintenance, as opposed to simply triggering changing the lube to remove the contaminants. They’ll continue to return until the root cause is removed. If the cycle is not broken, short-term failure is a likely result.
Revisiting an earlier anecdote, I was interviewed and misquoted in Popular Science magazine in the 1960s as indicating that
oil analysis was like blood testing, when in fact it was the interviewer’s own analogy gleaned from our conversation. My contribution, not printed, was to state that, on the surface, medicinal blood analysis represented a parallel but also that the state of oil analysis wasn’t nearly sophisticated enough to warrant direct comparison. It still isn’t, but it can exist in the same conversation these days, perhaps.
The only reason I want to include oil analysis in the same conversation as a medical blood test is to point out the major difference between the two sciences. In the medical setting, the doctor is the focal point of the diagnosis. His opinion is essential. In the oil analysis setting the report is the focal point and the commentary (diagnosis) is thrown in, inclusive with the test. To my knowledge, an ISFA laboratory—supplying a comment inclusive with test data—has never charged a fee for that opinion. While the fee is built-in, the tests determine the service price. Often report recipients have no idea who evaluated the test data and provided an opinion. When one thinks about it, that’s rather amazing, because the evaluation is the ultimate deliverable of ISFA, isn’t it? The test data and any available information about the machine’s operating conditions are stepping stones to reaching a conclusion.
Secondly, irrespective of the quality or accuracy of maintenance advisories, it is often the case that no feedback is offered from the maintenance team as to the efficacy of the advisories rendered. This is partly due to inherent devaluation of the commentary, based on the culture in which ISFA has been steeped, in that most evaluation is not paid activity from the user’s viewpoint. As a result, valuable information never makes it to the computerized maintenance management system so that it can be used to vet both the comment and the maintenance effort. As such, the ISFA program’s value is never called into question because it’s never been questioned.
Prior to computerization of the ISFA process—sample log-in, testing, evaluation and reporting—there was no easy means to track feedback. Now there’s no excuse not to,
yet feedback remains an elusive piece of vital information. Actually, it’s neglected. Companies willing to track this information have significantly larger savings and uptime. They’ll know where soft spots (opportunity fixes) reside in their operations.
In 1981 I used a simple spreadsheet technique to establish and verify that a large trucking company had high instances of fuel leaks in the case of one diesel engine MFR/model and seemingly excessive coolant leaks with a different MFR/model. I based this strictly on what the test data seemed to indicate—sample by sample, engine model by engine model. My lab had an IA that I had designed, and we were able to sift through and cull out problem types based on the IA’s evaluations, as there was no feedback with which to correlate. It was found that about half of the reports with these two types of trauma were acted upon and the correlation was virtually 100%. What is sad is that half of the problems weren’t investigated, and numbers of failures did, in fact, occur upon further investigation, likely from inattention to the indicated problem (fuel or coolant).
In the case of the frequent fuel leaks, the MFR was spurred into some R&D and was able to pinpoint the problem and correct it for that model going forward. Both MFR and the user benefited. Seeing oil analysis exact change in a manufacturing process is one of the most exciting technical events I’d ever experienced in my career.
The very best improvement an IA can bring to the ISFA party
is a vetting process that’s thorough and doesn’t let problem test results get through the cracks. But it still requires that the user (1.) acts on advisories in timely fashion then (2.) reports findings with sufficient accuracy so that the IA can validate and correct itself, with judicious domain expertise in the mix for final vetting. Then the advisory will take its proper place as the deliverable it should always be.
Ultimately, given accurate feedback, IAs will be able to make diagnostic and prognostic statements with a confidence level stated in percentages. When this routinely happens we can talk about blood testing and machinery fluids analysis in the same paragraph.
*K is particularly dependable for detecting coolant leaks at onset because, unlike sodium (Na) and boron (B), e.g., K rarely has an alternate chemistry that might possibly be in play. Na and B are frequently found in various lube additive chemistries. That is, they’re not confined at all to coolants. It’s not always a slam-dunk to bang on these metals in the name of coolant.
Jack Poley is managing partner of Condition Monitoring International (CMI), Miami, consultants in fluid analysis. You can reach him at jpoley@conditionmonitoringintl.com.
For more information about CMI, visit www.conditionmonitoringintl.com.