Considerations for thin section bearings
Jeanna Van Rensselar, Senior Feature Writer | TLT Webinars August 2016
A technical examination of these unique components, their applications and advantages.
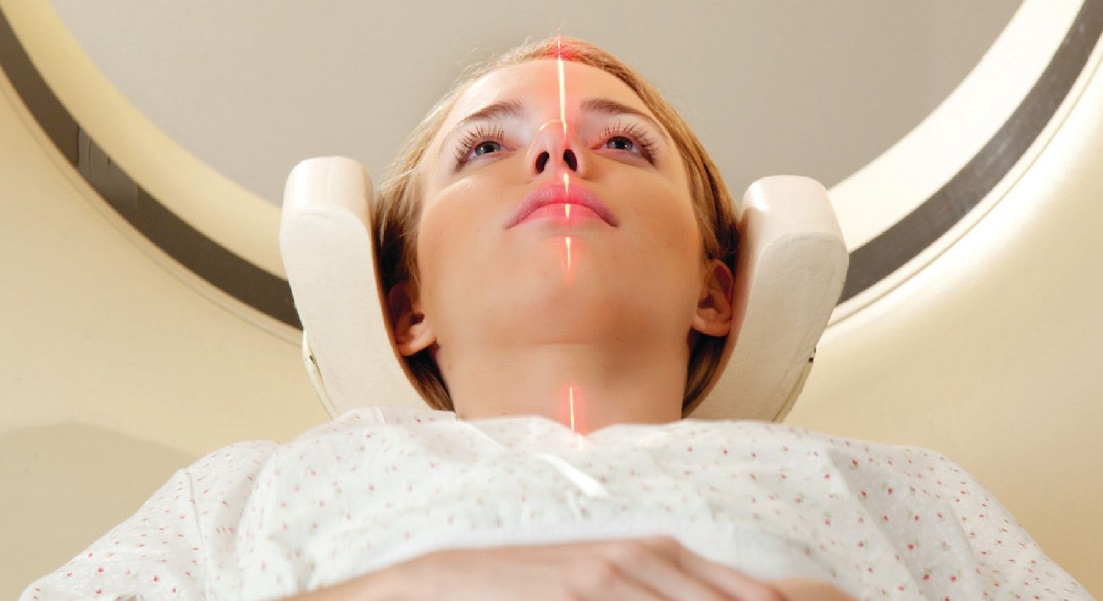
© Can Stock Photo Inc. / Leaf
KEY CONCEPTS
•
Thin section bearings have a cross section that is constant regardless of bore size.
•
They are used in specialty applications such as robotics that require smooth movements and an accurate, stable axis of rotation.
•
They are very similar to conventional ball bearings but thinner—creating many advantages and a few disadvantages.
MEET THE PRESENTER
This article is based on a Webinar originally presented by STLE University on Nov. 11, 2014. “Considerations for Thin Section Bearings and Their Applications” is available at
www.stle.org: $39 to STLE members, $59 for all others.
Long-time STLE-member Les Miller is vice president of engineering at Kaydon Bearings where he is responsible for product design, development and application. He received his bachelor’s degree in mechanical engineering from Tri-State College and has been active in the bearing industry for 39 years. He also has been active in the ABMA Engineering Education Committee and Bearing Technical Committee for the past 20 years and is a member of the ASME Tribology Division. His work history includes 26 years with NSK and a total of 13 years with SKF/Kaydon in ever-increasing levels of responsibility for product design and application engineering. You can reach Miller at
lmiller@kaydon.com.
Les Miller
THE FOCUS OF THIS ARTICLE IS THIN SECTION BALL BEARINGS. The difference between the inside and outside diameter of the rings is much less than standard bearings, but the cross section remains constant as the bore diameter changes. Generally a bearing is considered a thin section when the bore diameter is greater than four times the radial cross section. The considerable advantage of the compact design is slightly offset by a diminished load-carrying capacity and temperature limitations in some cases. The standard material is high-chrome bearing steel, but they are available in other materials such as stainless steel.
Thin section bearings save weight, create space, reduce friction, increase design flexibility and provide excellent running accuracy. These bearings are available in a variety of materials, corrosion-resistance options, separator options, cross sections, internal fit-up choices, contact angles and precision levels. They solve a variety of design problems that cannot be addressed with conventional ball bearings.
Advantages of thin section bearings include:
•
Light weight
•
Multiload capabilities
•
High stiffness
•
A small cross section (with a variety of possible cross sections and sizes).
Thin section bearings were originally developed for applications with tight space limitations. They continue to be most advantageous where space limitations and combined loading and/or weight restrictions necessitate unique designs. They contribute to downsizing, weight reduction and reduced friction loss. The high accuracy of the bearings also enables excellent, quiet performance at high speeds (perfect for CT scanners that require a large hollow rotating area).
Not surprisingly, one of many promising applications is robots. Other applications include medical, aerospace, defense and a range of industrial and commercial applications that require precision. Many of these applications also require special lubricants and extreme cleanliness.
Thin section bearings are available as deep groove ball bearings, four-point contact ball bearings and angular contact ball bearings. Each of these designs is available in a range of sizes and materials.
An array of Kaydon’s thin section bearings. (Courtesy of Kaydon Bearings.)
THE BASICS
A simple bearing is defined as a device that supports and facilitates motion between fixed and moving machine parts (
see Bearing Definitions and Terms). It may have internal rolling elements, and those rolling elements may consist of balls, cylindrical rollers, tapered rollers or spherical rollers. A thin section bearing, per ANSI/ABMA standard 26.2,
Thin Section Ball Bearings Inch Design, is a bearing with a fixed cross section so that “...within a given series, the bearing cross section remains constant irrespective of the bore diameter.” This includes ball bearings of (1.) single-row, radial contact; (2.) single-row, angular contact; and (3.) single-row, four-point angular contact.
BEARING DEFINITIONS AND TERMS (1)
Axial clearance. This is the total amount of free axial movement between the inner and outer race of a bearing. Bearings with internal clearance contain both axial and radial clearance.
Axial load. This is the load applied to the bearing parallel with the bearing axis of rotation, also known as thrust load.
Capacity. Dynamic capacity is the basic C rating, which represents a load that the bearing can theoretically endure for a million revolutions.
Static capacity is the approximate load the bearing can endure before permanent deformation occurs on the ball or raceway.
Deflection. This is the amount of movement associated with compression or stretching of bearing components when placed under load.
Diameter tolerance. This is the range in which the average diameter of a bore may fall.
Diametral clearance. This is the total free movement of the inner race relative to the outer race in a radial plane, also referred to as
radial clearance.
L10 life. This is theoretical lifespan of a bearing under a specific set of dynamic operating conditions associated with 90% reliability.
Moment load. This is the load that, when applied to a bearing system, tends to overturn or bend the axis of rotation in an angular direction.
Pitch diameter. This is the theoretical median diameter of a bearing, which passes through the center of the rolling elements.
Preload. This is the amount of load placed on the rolling elements before the application of any external loads.
Radial load. This is the load applied perpendicular to the bearing axis of rotation.
Runout. This is the maximum axial or radial race wall thickness variation of an inner or outer bearing race.
•
Single-row radial contact ball bearings
o
Handle radial loads
o
Have a zero-degree contact angle
o
Have a single ball path
o
Include a snap-over separator
o
Have a preload or clearance set at the factory.
•
Single-row angular contact ball bearings
o
Are used in pairs
o
Handle radial, axial or moment loads
o
Have a 30-degree contact angle
o
Have a single-ball path
o
Include a circular pocket separator
o
Have a fit-up that can be adjusted at installation.
•
Four-point contact ball bearings
o
Handle radial, axial or moment loads
o
Are used alone
o
Have 30-degree contact angles
o
Include a snap-over separator
o
Have a clearance set at the factory.
Common separator materials include:
•
Brass. Usually the standard option for Kaydon catalog bearings.
•
300 series stainless steel/precipitation hardened SST wire. Advantages include low outgassing, high-temperature and harsh-environment tolerance. Disadvantages include higher friction than brass, more particle generation and poor wear properties.
•
Phenolic laminate (resin-coated linen weave). Advantages include light weight, low wear, porosity and quiet operation. They are appropriate for the low-friction and high-speed applications found in many legacy applications. Disadvantages include poor dimensional stability, especially in larger diameter bearings. They cannot be manufactured in sizes greater than 20 inches.
•
Molded nylon. Advantages include lightweight, low wear, quiet operation and very low cost. Disadvantages include porosity (they readily outgas), limited tooling and inability to withstand high temperatures.
•
Molded PEEK (polyether ether ketone). Advantages include light weight, low wear, quiet operation, low cost and low outgassing. Disadvantages include limited tooling and high-temperature intolerance.
•
Nylon strip. Advantages include light weight, low wear, quiet operation, low cost and the flexibility to be cut to any length. Disadvantages include porosity, high-temperature intolerance, open ends and a snapover style that may unzip and eject.
APPLICATIONS
Thin section bearings make the most sense in applications that involve tight spaces, low weight requirements, compact designs and precision. Primary applications are semiconductor mechanisms such as:
•
Atmospheric and vacuum robots
•
Wafer probers
•
Ion implantation
•
Sputtering equipment
•
Test heads/manipulators
•
Rapid thermal processing (RTP)
•
Megasonic cleaning systems
•
Photolithography lens and counterbalance
•
Chemical mechanical polishers (CMP)
•
Die bonders
•
Lappers
•
Wafer steppers
•
Transfer systems (SMIF).
These semiconductors typically require a vacuum environment, low-particle generation and high accuracy.
Medical applications include:
•
Oncology treatment
•
Robotic surgery
•
Security scanners
•
Diagnostic equipment
•
CT scanners and baggage scanners used for airport security.
Bearings for CT scanners in particular require quiet operation, long life and low friction (
see Figure 1). They require a large opening for scanning (people or baggage) for which a large diameter thin section bearing system is key. The long service life can be achieved with the addition of lithium or polyurea grease.
Figure 1. CT scanner assembly single four-point contact bearing. (Courtesy of Kaydon Bearings.)
BEARING SELECTION CONSIDERATIONS
There are four basic bearing selection considerations: available space, the degree of precision that is required, stiffness and the internal and external operating environments. Additional considerations include the applied load, the degree of misalignment, operating speed, noise level, axial displacement, mounting/dismounting factors, sealing and lubrication (
see Kaydon’s Lubrication Recommendations for Thin Section Bearings).
KAYDON’S LUBRICATION RECOMMENDATIONS FOR THIN SECTION BEARINGS (2)
Kaydon recommends that the selection of the proper lubricant be based on an evaluation by the system design engineer of the operating conditions, including at a minimum: rotational speed, type and magnitude of loads and ambient temperature. The three types of lubricants commonly used are oil, grease and dry film/surface treatment.
•
Oil usually provides more complete lubrication. Because of its liquid state, oil provides better coverage of the critical surfaces and assists in dissipating heat more readily. This is especially true when circulation and cooling are provided. In high-speed applications where the heating effect is more pronounced, oil is specified. Where minimum torque is a requirement, oil will usually provide lower friction values.
•
Grease offers certain advantages of its own. Because it is more easily retained, the design of bearing housings and seals is simplified. In many applications, the lubricant itself serves to exclude contaminants when used in conjunction with labyrinths or close clearances between the rotating and stationary structures. For higher speeds within the range suitable for grease lubrication, a channeling type of grease is often selected.
•
Dry films and surface treatments have been used as bearing lubricants in applications subject to environmental extremes, particularly where conventional lubricants cannot be tolerated or will not survive. A wide variety of types are available for selection; options include tungsten disulfide, graphite and molybdenum disulfide.
As far as the bearing size, considerations include shaft outer diameter, housing inner diameter, width and cross section. Then there is the required bearing configuration: radial, axial or combined; the dynamics—will the bearing rotate relative to the load or will the load rotate relative to the bearing; and static—will static load be present while the bearing is stationary or at very low rpm; will it be constant and how much shock load will be present (
see Figure 2)?
Figure 2. Custom bearing configuration four-point contact type: mammography scanner—operates with axis vertical. Lower shield also serves as belt guide and is only needed on lower side. (Courtesy of Kaydon Bearings.)
BEARING DESIGN CONSIDERATIONS
Given the environments where thin section bearings perform best, bearing design considerations should factor in low torque, low particle generation, high accuracy, high-duty cycles, high temperatures and corrosion resistance (
see Figure 3).
Figure 3. Kaydon’s precision measurement of a thin section bearing. (Courtesy of Kaydon Bearings.)
•
Low-friction torque. Lubricant selection oil vs. grease; cage selection-non-metallic vs. metallic; internal fit-up; clearance vs. preload; external fit-up/loose fit-up vs. press fit-up.
•
Low-particle generation. Separator selection-performance plastics and nylon vs. steel/brass/Teflon/PEEK; race and ball material-hybrid bearings (ceramic balls and steel races); grease selection-hybrid bearings and oil vs. grease and dry films; packaging cleanliness–clean room packaging.
•
High accuracy. Precision class; internal fit-up-preload vs. clearance; equipment design—higher-level assemblies vs. individual bearings/ integral bearing designs vs. higher level assemblies.
•
High-duty cycles. Bearing selection—higher capacity vs. minimum capacity; separator selection—performance plastics vs. steel/Teflon; lubricant selection—synthetic hydrocarbon greases vs. PFPE vs. organic; maintenance schedule.
•
High temperatures. Race and ball material—special steels as required; separator material-steel ring and balls vs. plastics/Teflon/PEEK; lubrication selection—PFPE greases and dry films vs. synthetic vs. organic; external fit-up—steel shaft and housings vs. aluminum.
•
Corrosive environment. Race and balls—ceramic balls and races/17-4PH steel races and ceramic balls/440 C steel races and ceramic balls; separator material—engineered plastic (refer to compatibility charts); lubrication—consult lubrication expert; platings—Endurakote and titanium nitride vs. none.
Depending on the application requirements, thin section bearings can be lubricated in many ways (
see What Can Go Wrong?). Options include lubricants designed specifically for high speed, high temperature, low torque, water resistance and/or oscillation. Specialty lubricants such as dry film can be used in vacuum environments. The optimal grease depends on the application and environment.
WHAT CAN GO WRONG?
Mechanisms containing thin section bearings can lose their usefulness for reasons that include:
•
Motor lock-up-high torque
•
Positioning errors—erratic torque
•
Excessive noise
•
Contamination.
o
Wear particles from balls
o
Wear particles from ball paths in the races
o
Fretting between interfaces in housings, shafts and bearing faces and pilots
o
Sliding friction from separators or spacers
o
Lubricant breakdown
o
Lubricant expulsion.
Much of this can be avoided by incorporating bearings with the optimal size and material for the application.
REFERENCES
1.
Excerpt from Kaydon Catalog, p.127.
2.
From
Lubrication and Maintenance of Reali-Slim Thin Section Bearings, Reali-Slim Bearings Catalog 300 Kaydon Bearings. Available
here.
Jeanna Van Rensselar heads her own communication/public relations firm, Smart PR Communications, in Naperville, Ill. You can reach her at jeanna@smartprcommunications.com.