Fretting about friction
Evan Zabawski | TLT From the Editor August 2016
Less wear yields fresher and clearer notes.
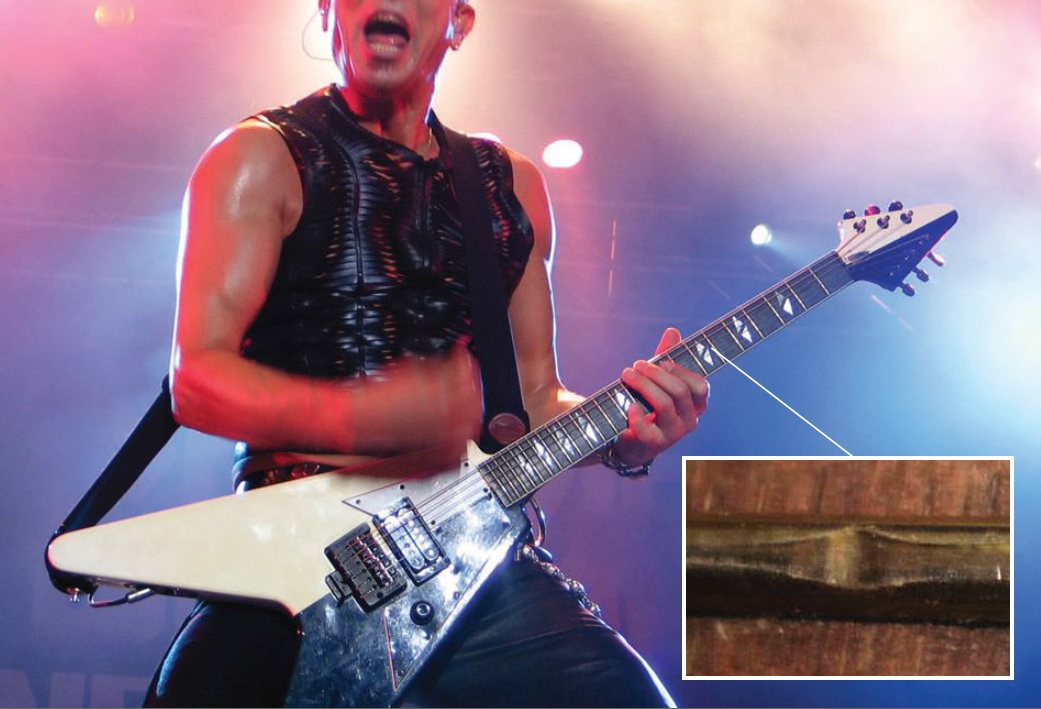
One who tends to press hard or perform a lot of pitch bending will find themselves with more fret wear than others.
© Can Stock Photo Inc. / nao
WHY DO SOME STRINGED INSTRUMENTS HAVE FRETS? Those of us who do not play assume they are there to mark where your fingers are supposed to go, but that is not entirely true. Nor are frets present solely to ensure intonation. Frets serve multiple purposes, and the foremost is allowing the player to fully pinch the string and produce a clear tone.
Frets divide the neck of an instrument into semitones or half steps, with each octave being divided into twelve semitones. Classical guitars will typically have 19 frets, but electric guitars can have as many as 24 frets. The spacing of the frets never changes, but varying heights of neighboring frets can cause fret buzz.
Fret buzz occurs when the vibrating portion of the string contacts a fret other than the fretted note. Fret buzz can be caused by changes in the relief of the guitar neck from natural warping, incorrectly installed frets, loose strings or wear of the fret itself.
Fret wear is bound to happen over time, but material choice of both the frets and strings can hinder or accelerate wear. For many years frets were made from German silver, a 3:1:1 copper, nickel and zinc alloy. Originally from China where it was called bai tong or paktong, meaning
white copper, the alloy was imitated by the Germans in the early 19th Century to such success that the original name has been all but forgotten.
For classical guitars, treble strings were made with animal intestine and bass strings with silk wrapped in animal intestine until WWII rationing led to the invention of nylon strings. Treble strings are now nylon, and the bass strings are nylon wrapped with silver-plated bronze or copper wire. Electric guitars have commonly used nickel-plated steel strings, but new alloys and coatings are continually entering the market.
One alternative is stainless steel strings, which produces a brighter tone but leads to more fret wear. This fret wear can be pronounced enough to change the profile of an individual fret and cause fret buzz. The common solution is to redress the frets, entailing a lot of manual labor: sanding (to remove grooves and level the frets with each other) and then recrowning (to produce a rounded profile) and polishing each fret. After a few redressings the only course is to re-fret the guitar, presenting the guitar owner with the option of selecting a new material.
For increased durability, some players may choose stainless steel frets, but when paired with strings of a softer material, they will cause string wear. Worn strings will not sound as fresh, producing a dead sound. When the frets and strings are both stainless steel, fret wear is significantly slower, and the strings tend to last two to three times longer.
Saying that, all this is dependent on how the player actually plays the guitar. One who tends to press hard or perform a lot of pitch bending will find themselves with more fret wear than others. The worst offender, however, is the use of a capo—a device that clamps down on all the strings to reduce the playable length of the strings. Guitar techs are quick to note that a capo exerts more pressure that a finger, which causes more damage and leads to more business for them.
Of course, with any metal-to-metal contact, one of the best solutions is application of a lubricant. Commonly referred to as
fast fret, it is usually just a form of mineral oil used on both strings and frets. Some players rely on the lemon oil they employ as fretboard conditioner for their lubrication needs, but due to variations in additional ingredients that may be absorbed into the nitrocellulose finishes, many manufacturers will not endorse lemon oil.
With proper usage and care, a guitar player need not fret about fretting their frets excessively.
Evan Zabawski, CLS, is a reliability specialist based in Calgary, Alberta, Canada. You can reach him at evan.zabawski@gmail.com.