Maintenance 4.0
Dr. Robert M. Gresham, Contributing Editor | TLT Feature Article August 2016
Condition monitoring moves into its fourth decade with increased emphasis on risk management maintenance.
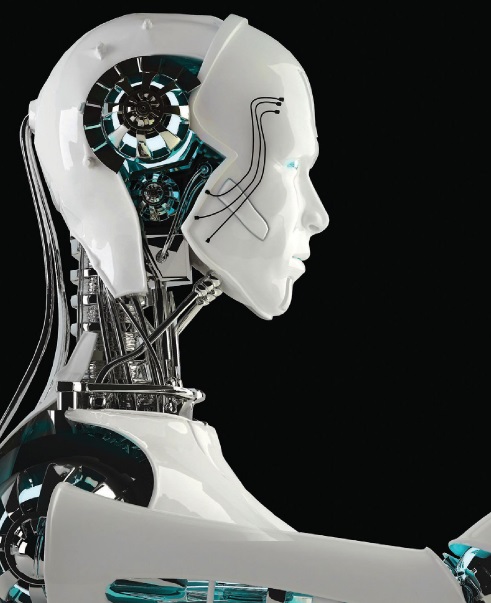
© Can Stock Photo Inc. / abida
KEY CONCEPTS
•
Asset management was a dominant theme at the LubMat 2016 conference in Spain.
•
Risk management maintenance involves an even higher use of sensors on critical equipment and big data analysis.
•
In the future robots will do more manufacturing while humans maintain the robots.
I RECENTLY ATTENDED THE LUBMAT 2016 CONFERENCE IN BILBAO, SPAIN. This conference is more industry focused than many conferences in our field and has a broad international attendance—primarily greater Europe, the U.S., Central America and South America. At the last conference, LubMat 2014, I made a presentation on STLE’s Emerging Trends report which had come out that year. It was well received and elicited good questions and commentary in the halls. Interestingly, at this LubMat many of the plenary speakers talked about and expanded on emerging trends from their various perspectives.
Wind turbines and robots used in manufacturing are technologies that would benefit from a Maintenance 4.0 approach.
© Can Stock Photo Inc. / welcomia
There were several common themes in the presentations and technical talks. Predominant were the ideas of a much improved condition monitoring, maintenance and asset management program. In addition, there were overlapping subjects such as wind turbines (where the Europeans have more operating experience) and increased use of robotics in manufacturing, which also overlaps as it is very important to keep the robot properly maintained to not only eliminate downtime but also to ensure that its manufacturing tasks stay within specifications.
Maintenance 4.0 is the new buzzword for this improved level of condition monitoring, maintenance and asset management. Twenty years ago oil analysis was just getting going. STLE had begun work on two new certifications in oil analysis, and everyone was preaching about the ills of reactive maintenance—which basically boils down to you wait until it breaks, run out and see how fast you can fix it to eliminate downtime and reduce costs. Of course, this approach results in downtime or even loss of critical equipment, potential exposure of employees to toxic materials, poor housekeeping or unsafe conditions such as fires and explosions, not to mention delays in supplying those all-important customers, who make it possible to pay the bills. Further these kinds of problems can result in regulatory fines and similar sanctions.
More recently, we began to talk of predictive maintenance. This is the idea that through condition monitoring techniques, such as oil analysis, vibration analysis, thermal, etc., we can determine when a machine or machine component is beginning to wear or break down. This then buys a little time to order in replacement parts and to schedule down time to make the needed repairs.
More recently still, we explored the concepts of proactive maintenance. Here we introduced the ideas of asset management along with more improved condition-based maintenance techniques. Some of the new ideas were to identify and rate each piece of equipment or component according to the criticality of it to the overall plant operation and assign a dollar amount as a measure of its importance. This provided financial justification for increased condition monitoring of critical equipment, inventorying critical repair or replacement parts and, most important, scheduling maintenance cycles well in advance so key system components receive periodic maintenance to ensure no downtime between cycles.
Now with Maintenance 4.0, the emphasis is on risk management maintenance. Some of the characteristics of risk management maintenance involve an even higher level of condition-based maintenance through the use of sensors on critical equipment and through big data analysis to more precisely determine trends and the state of the equipment. Of course, determining the level of risk to the overall operation for each piece of equipment if it fails, and the economic impact if it fails, is taken to a much higher level.
When you consider the risks and costs associated with operating nuclear power plants, a Maintenance 4.0 program looks pretty good.
© Can Stock Photo Inc. / MartinLisner
Finally, and this is critical, take proactive steps to eliminate that risk for that equipment or system with the most impact. This could take the form of statistically determining if one brand of bearing lasts longer for a given application and using the longer-lasting bearing regardless of cost. In oil analysis, preferably through use of sensors, monitor not the health of the oil per se but the critical additive system in the oil as it begins to break down. Then the oil can be changed before the machine actually sees degraded oil.
An important part of Maintenance 4.0, implied above, is enhanced asset management. In fact, there is a relatively new standard, ISO 55000, which is an international standard covering management of physical assets. Initially a publicly available specification (PAS 55) published by the British Standards Institution in 2004, the ISO 55000 series of asset management standards was launched in January 2014. In a recent article, in Noria’s Machinery Lubrication, Jim Fitch characterized the standard: “Asset management involves the balancing of costs, opportunities and risks against the desired performance of assets, to achieve the organizational objectives. An asset management system provides a
structured approach for the development, coordination and control of activities undertaken on assets by the organization over different life cycle stages and for
aligning these activities with its organizational objectives.”
When one thinks of the enormous capital investment and the equally enormous repair expense in large wind turbine farms, a Maintenance 4.0 approach would seem the only logical method to manage these assets. Manufacturing robots also can be an expensive investment which is amenable to a Maintenance 4.0 approach. Interestingly, when you think about manufacturing something with complex robots, it seems clear that the operations and maintenance departments begin to merge into one. An operator no longer makes or assembles things; the robot does that. The operator programs the robot to do what is needed then monitors the robot to see if it does what is intended and at the same time attends to the needs of the robot—its maintenance.
Finally, when you consider the risks and costs associated with operating nuclear power plants, a Maintenance 4.0 program looks pretty good as well.
This year’s LubMat conference was informative. Normally, LubMat stands for lubricants and materials. This year it was more about lubricants and Maintenance 4.0.
Bob Gresham is STLE’s director of professional development. You can reach him at rgresham@stle.org.