20 Minutes With Paul A. Bessette
Rachel Fowler, Associate Editor | TLT 20 Minutes August 2016
This self-described ‘chemical tribologist’ discusses industry consolidation, education, economics—and his favorite testing machine.
PAUL A. BESSETTE - The Quick File
Paul A. Bessette is the president of Triboscience & Engineering, Inc. (TS&E), and lead tribologist for Tecsia Lubricants. He has been involved with synthetic lubricants for more than 39 years, including 25 years at Nye Lubricants and three years at Ciba-Geigy.
TS&E was established in 2000 and initially provided consulting services. Since 2005 TS&E has gravitated toward manufacturing lubricants for both domestic and foreign customers with an emphasis on perfluorinated polyethers.
Paul was vice chairman of the NLGI Grease Education Course for 10 years and was honored with the NLGI Fellows Award, Meritorious Service Award, Achievement Award, Clarence E. Earle Memorial Award and Author’s Award. He also was an associate editor for Tribology Transactions, Journal of Synthetic Lubricants and a peer reviewer for NLGI. He is a member of STLE and ASTM.
Paul earned a bachelor’s of science degree in chemistry from Lowell Technological Institute. His graduate work included polymer chemistry at Brooklyn Polytechnic Institute. He also has a master’s of business administration from University of Massachusetts Dartmouth.
Clients have included Engineered Custom Lubricants, DuPont, BP Castrol, Lubrication Technologies, Kyodo Yushi, Honeywell, Hewlett-Packard and NASA.
Research interests include improving methods of grease filtration, vapor pressure of synthetic lubricants, thermo-oxidative stability, low-temperature rheology of oils and greases and advanced rolling element bearings greases.
Paul has authored or co-authored chapters in Space Vehicle Mechanisms: Elements of Successful Design, John Wiley & Sons, Inc.; Handbook of Lubrication and Tribology, CRC Press; and Synthetic Lubricants and High-Performance Functional Fluids, Marcel Dekker.
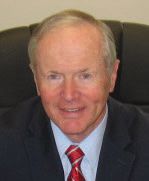
Paul A. Bessette
TLT: Why did you become a tribologist?
Bessette: Tribology is a very inclusive discipline, and my background in polymer chemistry was a tremendous asset to understanding the chemical and physical nature of ingredients used in formulating synthetic oils and greases. Since my work has focused mainly on the development of lubricants, I consider myself a chemical tribologist.
TLT: How did you become interested in grease?
Bessette: In 1976 I left Ciba-Geigy and joined the William F. Nye Co. in Fairhaven, Mass. Nye was originally a whale oil company, and when I joined we were still selling residual inventory of various marine mammal oils. However, management was sufficiently perspicuous to realize that new products, especially synthetics, were necessary for the firm’s future success. Grease became a necessary compliment to the company’s product line, and I was tasked with making things happen. When Nye was given the opportunity to manufacture a sodium-thickened synthetic ester grease being discontinued by Texaco, we installed the necessary equipment and successfully manufactured a rheologically challenging grease to the delight and satisfaction of customers producing rolling element bearings. That initial success was the impetus to develop other greases.
TLT: Do you have a favorite grease?
Bessette: No! Forty years of study, hard work and research has taught me that there are no panaceas in the world of lubrication. Some greases may be characterized as general purpose, but for high-speed bearing applications, computer disk drives, sintered metal components and jet engine actuators, we must be mindful that these diverse tribological challenges require individual solutions.
For example, perfluoropolyether (PFPE) greases possess unsurpassed thermo-oxidative stability. In an atmosphere of pure, dry oxygen maintained at 3500 kPa and 210 C, no exotherm is observed after two hours. At first blush, one would assume that such a grease is the Almighty’s gift to tribology! However, due to the discrete nature of the polytetrafluoroethylene (PTFE) used to form the grease, PFPE greases are problematical for bearing application where Dn values exceed 200,000. These greases produce too much vibration and runout.
Paul Bessette preparing to run a weight loss determination using the thermogravimetric analysis.
TLT: What are some of the most important challenges in the lubricating industry today?
Bessette: I divide the challenges into three categories: industry consolidation, education and economics.
When one firm acquires another, product lines are rationalized to the chagrin of distributors and OEMs. If a small distributor has established a business around certain product types, the discontinuation of the product or new minimum order requirements are often too burdensome. Moreover, alternative recommendations are difficult to justify due to the cost and time constrains of new product requalification.
From an education standpoint, the word grease is far too generic. Lubricants used in the mining industry or those used in spacecraft control moment gyroscopes are referred to as grease. However, a molybdenum disulfide-fortified calcium sulfonate grease is very different from an ultra-filtered lithium-thickened synthetic fluid prepared under clean room conditions. All too frequently the choice of lubricant is made at the completion of the design cycle. This is done at great peril to the timely launching of new products.
Some greases sell for less than $2 per pound while others cost more than $1,000. It’s the application and technology that dictates grease economics. Consider a conductive plastic potentiometer where the lubricant must function from -40-100 C, be resistant to fuel vapors and possess a viscosity index sufficiently high that contact hydroplaning does not occur. A linear perfluoroether grease costing approximately $500 per pound is a viable candidate for this application, but the cost of grease per potentiometer is marginal since only milligrams of grease are used per unit. Even expensive greases usually have a minor impact on the overall economics of a component.
TLT: Do you have a favorite tribotest or tribology test machine?
Bessette: I abashedly say yes! In our laboratory at TS&E, we have a four-ball wear machine and a four-ball EP tribometer, pressure differential scanning calorimeter and a control stress rheometer. However, my preferred tribochemical research tool is our spiral orbit tribometer (SOT). Its acquisition was purely serendipitous. The short version of a long story is that I had invited Bob Price to join me in Fall River, Mass., since both he and I were working alone in two different labs. Price and STLE-member Ed Kingsbury were colleagues at Draper Labs, and Kingsbury decided to visit Price’s new workplace. I had known Kingsbury for a number of years, and I think he was sufficiently impressed with the sophistication of our lab that he offered to give us the SOT along with a microbalance. Approximately 16 years earlier Kingsbury tried to sell me the same SOT, but I was compelled to refuse since I had recently acquired another tribometer.
In my opinion, the SOT is a unique research tool in that it faithfully simulates bearing behavior. Essentially it is a thrust bearing comprised of a single ball where friction force, electrical resistance, temperature and coefficient of friction are monitored in real time. It is an elegant tool to study the tribochemical behavior of greases and additives. Since micrograms of grease are used and lubricant life is a function of the number of ball orbits, the number of lubricant molecules degraded per orbit can be determined. I’m currently using the SOT to investigate if specific solid additives can reduce the catalytic activity of 52100 steel in contact with linear PFPE-based greases.
Although PFPE greases possess excellent thermo-oxidative stability, they are vulnerable depolymerization in contact with metal surfaces producing what the aerospace community refers to as brown sugar. Since we can calculate the number of moles of lubricant that are on the ball, it’s possible to calculate the number of molecules degraded per ball orbit. The numbers recorded thus far are in the billions. I call it tribomortality.
A close second instrument would be the pressure differential scanning calorimeter (PDSC). With this research tool, we can quickly study the efficacy of antioxidants and other additives on the thermo-oxidative stability of various lubricants. Moreover, since the instrument is used to measure heat flow—both positive and negative— the PDSC is an effective means of determining the amount of thickener in a used grease provided the thickener melts. Since only milligrams of sample are required, the technique is superior to Soxhlet extractions.
TLT: What was the most challenging technical project you worked on?
Bessette: During my career I’ve worked on numerous daunting technical challenges from commercial and military aircraft disasters, grain elevator explosions, polyurea grease reformulated with the improper stoichiometry and a silicone grease use in writing instruments to prevent ink from back leaking onto everyone’s high-priced clothing.
In retrospect, the tribological Gordian Knot for me was finding an alternate route to the manufacture of PFPE greases. Prior to the ozone hole controversy, PFPE greases were made using DuPont’s™ Vydax 1000. Vydax 1000 was a 7.5% dispersion of low-molecular weight PTFE in trichlorotrifluorethane. PFPE fluid would be added to grease vessel and the Vydax added incrementally as the solvent was removed by heat and slight vacuum.
At Nye, we recovered 80%-95% solvent using the appropriate heat exchangers. The grease was usually made on the firm side since adding additional fluid was easier than adding more PTFE dispersion. The Montreal Protocol ended chlorofluorocarbons (CFCs) and new technology was urgently needed since PFPE greases had made significant inroads into a host of industries.
The initial attempt was to replace the CFC solvent carrier with isopropyl alcohol (IPA). Unlike the CFC, IPA is flammable, and a great deal of time was spent trying to produce an azeotrope that would be less hazardous than distilling IPA in an environment surrounded with electric motors that were not explosion proof. The government did not want us to put CFC in the stratosphere; I was determined not to put our employees there as well! Successful PFPE grease was made with the IPA-based dispersion, but a major problem ensued. Trace amounts of IPA remained in the grease that oxidized to form a foul smelling carboxylic acid. The resultant odor of the grease was a showstopper and a new approach was needed.
That approach came with the realization that perhaps a solvent dispersion of the PTFE was unnecessary. After a few days of trial and error, it was discovered that a “dry approach” was a viable alternative to the traditional methods for producing PFPE grease. Both Gerry Madden and Richard Morgan at DuPont were instrumental in bringing what become known a Vydax GT to market. That collaboration surely had a profound impact on a number of key industries including aerospace, military and automotive. As a footnote, the recovered CFC was used to prepare lubricant dispersions used to simultaneously coat thousands of small components. CFCs were more economical and better solvents than their replacements.
Paul Bessette checking the coefficient of friction of a PFPE grease being tested with the spiral orbit tribometer.
TLT: If you could have the freedom to choose an exploratory R&D project, what would you choose?
Bessette: There is a great deal of responsibility owning your own company. However, this also is a great deal of autonomy. My current work with the SOT satisfies my current research interest.
TLT: What inspired you to start your own company?
Bessette: After approximately 25 years at Nye, I opted to hang out my own shingle and become a consultant. I was hired by Engineered Custom Lubricants, DuPont, Castrol and was offered minor assignments with Kyodo Yushi, Honeywell, Hewlett-Packard, NASA and a few others.
After six years of living out of a suitcase and constant traveling to Michigan, Delaware and Illinois, I decided to open my own laboratory in an incubator facility in Fall River, Mass. I could continue to provide technical guidance to clients but with the added luxury of having dinner and a glass of wine with my wife, Jean. As the company has expanded— we now have seven employees—TS&E has gravitated toward manufacturing our own line of specialty synthetic oils and greases. Although our forte is PFPE- based products, we do a great deal with PAOs, esters, silicones and PAGs including development work with the new Dow OSP products. In retrospect, the inspiration emerged from a deep-seated entrepreneurial bent.
TLT: What is the focus of your company?
Bessette: To provide customers with lubricants that are designed for the application, provide extended life under the most demanding tribological conditions and be economical. Our philosophy is to be bona fide partners not only with customers but suppliers as well. Economic success is a joint effort!
In terms of research and testing, we issue comprehensive reports that provide clients with problem-solving information.
TLT: What is most satisfying about owning and managing your own company?
Bessette: There are numerous benefits to being at the helm of your own company. I enjoy the autonomy, the financial independence and the personal satisfaction of moving the organization to new heights. However, from a personal standpoint, the greatest satisfaction for me is being able to employ intelligent and ambitious young people and give them the opportunity to excel in a stimulating environment.
TLT: What is most challenging about owning and managing your own company?
Bessette: Based on my experience, the most challenging aspects of operating a successful small business are financial and regulatory. We now exist in a global economy with goods moving throughout North America, Europe and Asia. When a firm attains a certain sales volume it must adopt accrual-based accounting. Specifically, raw materials cannot be expensed until sold. However, raw material suppliers expect payment in 30 days. If a finished good is shipped to Asia by sea, it’s approximately a six-week journey, and customers demand 30 days after the good arrives.
Several years ago we purchased our own million-dollar facility. After the transaction our accountant informed me that the building would be fully depreciated in 39 years. I’ve told family, friends and colleagues that I’m planning to keep at it for another 10 years. Why retire when I’m terrible at golf? But our facility will not be completely written off until I’m 105 years old! If our S-Corp can keep more of its hard-earned income, we can hire more scientists, engineers and acquire additional capital equipment to maintain our current growth trajectory.
To some extent we are all being regulated back to the Stone Age. I personally take great umbrage at some of the new GHS labeling requirements. To stipulate that low-viscosity PAO is hazardous due to the possibility that it could be aspirated into the lungs during ingestion, it diminishes the real hazards that should be minimized in any work environment.
Finally, small firms struggle with recognition. It’s challenging trying to inform the world that you are open for business.
Paul Bessette measuring wear scars.
TLT: What characteristics or behaviors are important for successful entrepreneurs?
Bessette: Necessary traits for success in business include resilience, not being too risk averse, a sound business model, potential clients and personal or available financial resources. In the arena of specialty synthetic lubricants, the gestation period from forwarding a trial sample to receiving a purchase order can be as long as three years.
TLT: Was there a particular accomplishment or event where you realized that your company would have legs and grow over the long term?
Bessette: I can think of no singular accomplishment that assured the success of the company. However, I’m sanguine about TS&E’s long-term viability due to the quality of people on staff! I’m a believer in technological incrementalism. Numerous small accomplishments eventually lead to big things!
TLT: What are your plans and goals for your company?
Bessette: The motto of TS&E is
Excellence in Synthetic Lubricants. I would be immensely gratified if that motto endured well beyond my tenure at the helm.
You can reach Paul A. Bessette at pabessette@tselubes.com.